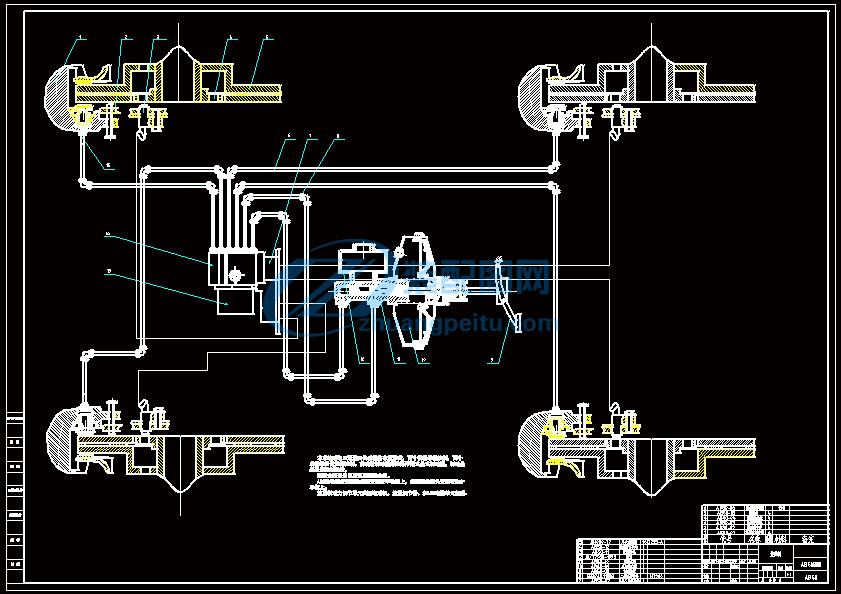
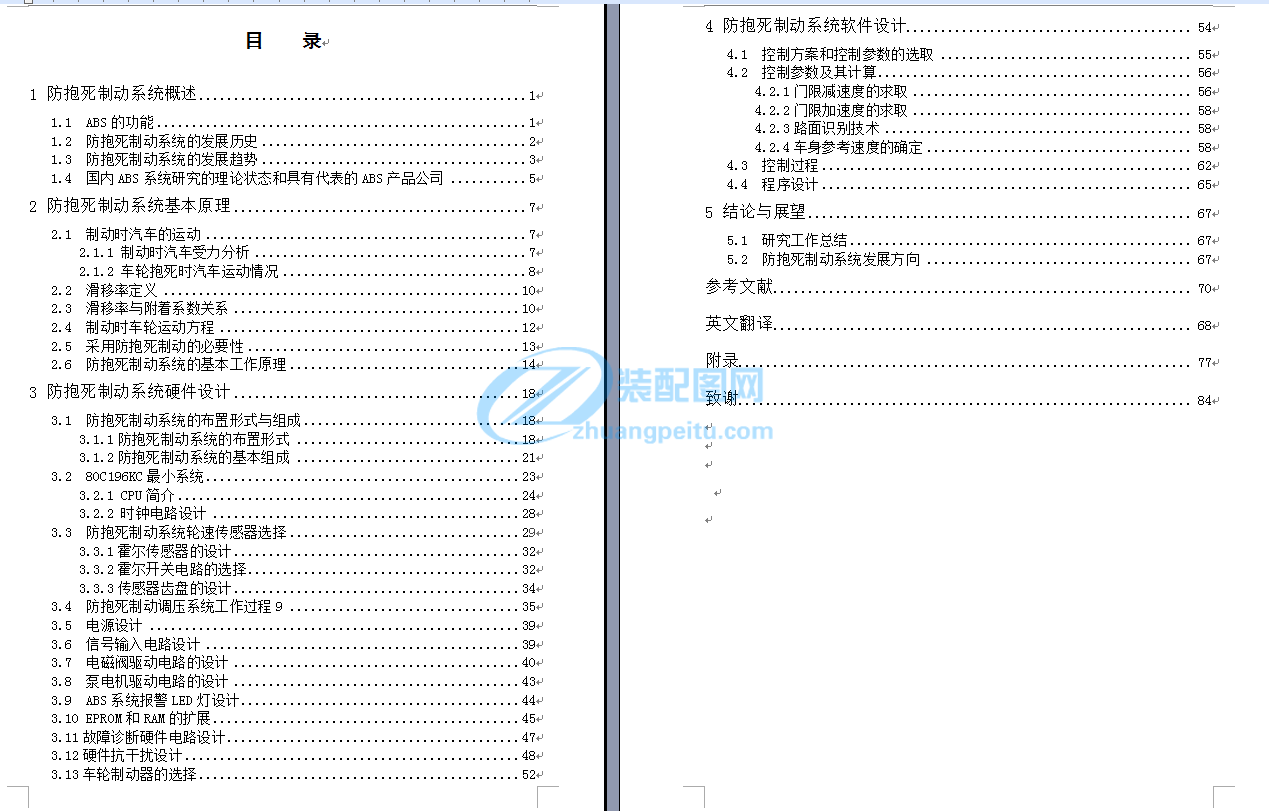
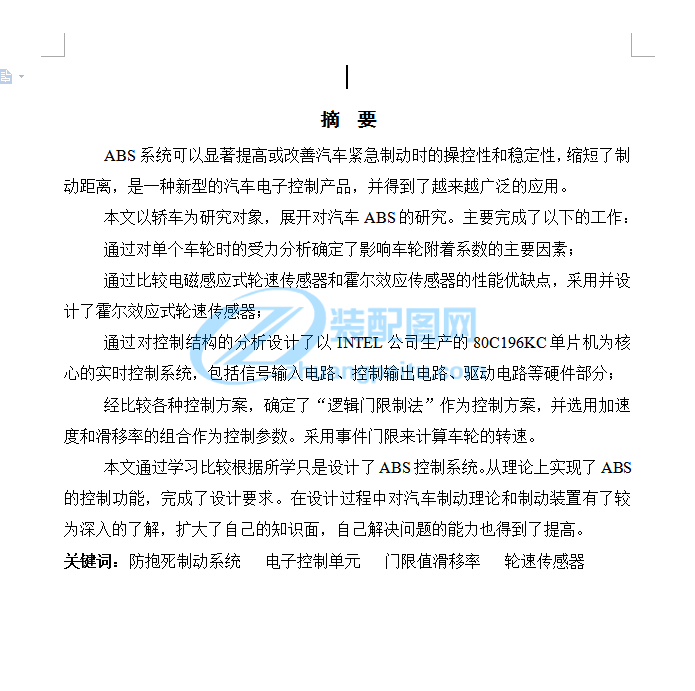
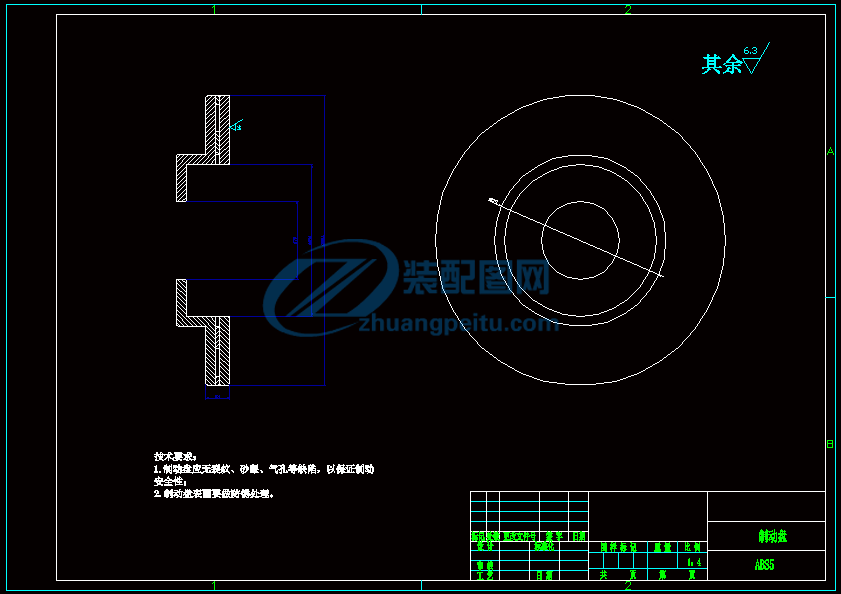
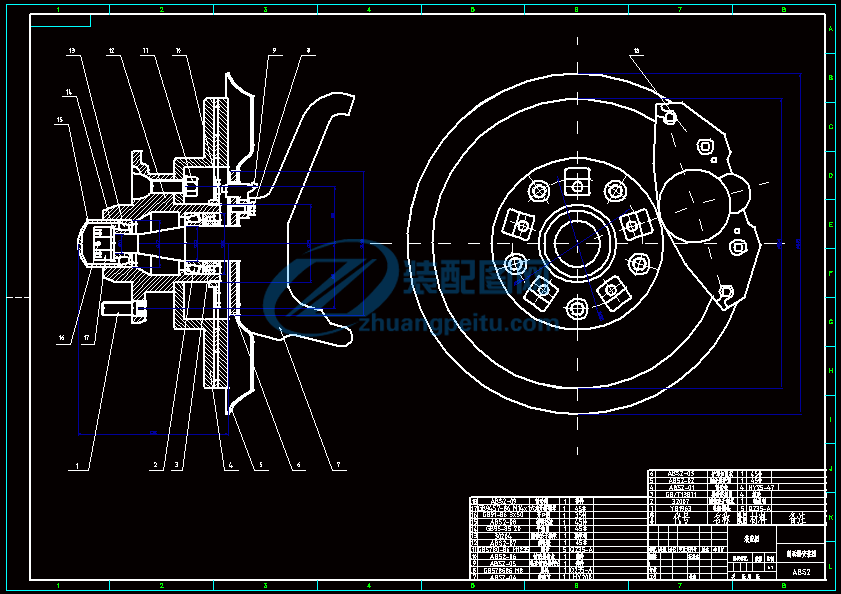
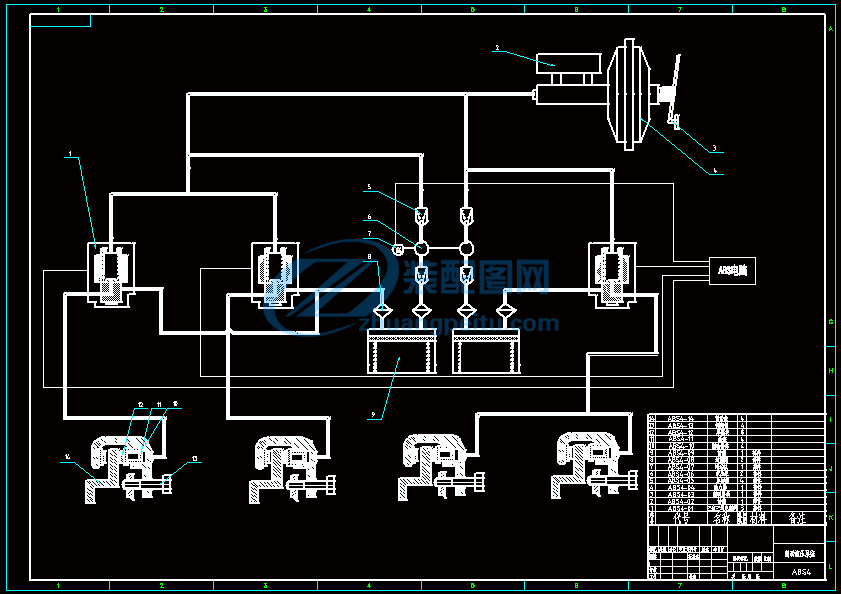
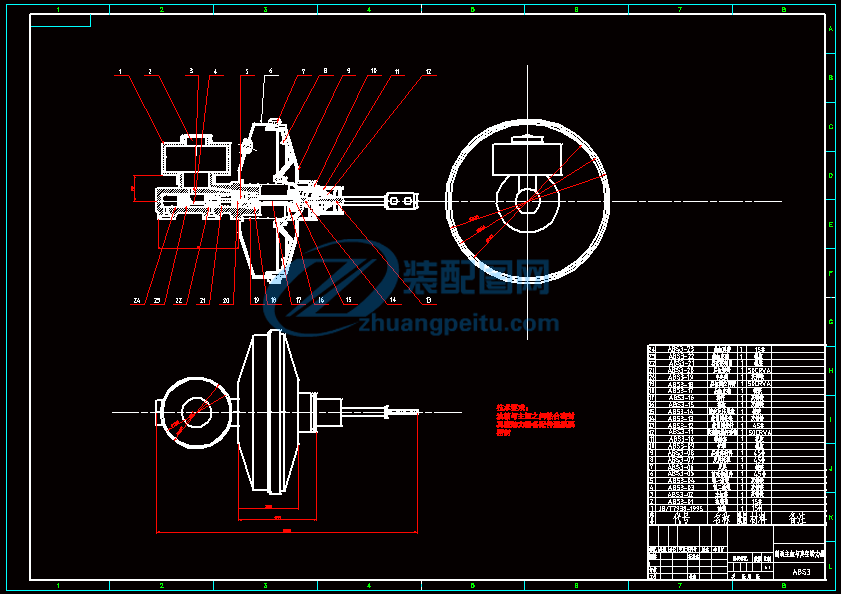
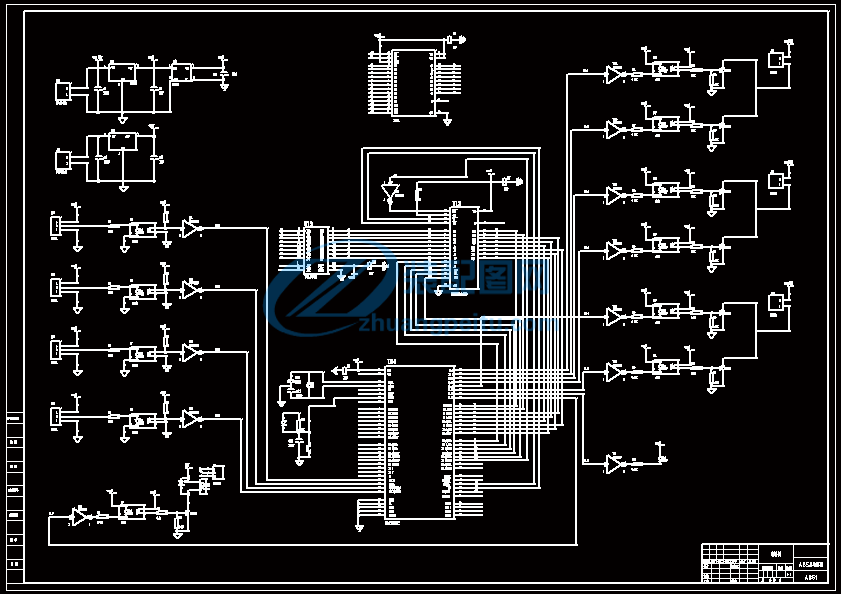
附 錄附錄 A.Car ABS Technology and Development TrendIn the car before the emergence of abs, used car is the open loop brake system. Its characteristic is the brake torque only and drivers of the size of the manipulation of the force, braking force distribution regulation and the size of the brakes on and type. With no wheel the motion of feedback signal measurement, can't know during wheel brake speed and holding in death, car you may adjust accordingly wheel cylinder or the gas chamber of the size of the brake pressure. So in an emergency brake, inevitably appear wheel on the ground, holding in death dragged the phenomenon of sliding. When the wheel lock, the ground of the performance was poor, the lateral attached can provide the lateral adhesion is small, car by external force in any minute under the action of will appear direction, easily happened instability problems of traffic accidents. In the wet pavement or snow and ice on the road, the direction of brake the instability of the phenomenon can more serious. towing It is through the basic function of sensors' wheel each transient state of motion, and according to the motion correspondingly adjust the size of the brake torque in to avoid the wheels holding in death, it is a phenomenon of closed-loop brake system.It is the electronic control technology in cars of the most successful application project, one of auto brake antilock brake systems can make the car in the braking maintain stability and shorten the direction braking distance, effectively improve the driving safety. Car ABS can say is the most important car safety history of the three great inventions (the other two are airbag with seat belt), ABS is also other safety device (such as ESP driving dynamic stability system and EBD braking forces based distribution system) Because money spent too big, ABS the practical use of the early railway vehicle or aircraft. 70 s, digital electronic technology and large scale integrated circuit, for the rapid development of ABS system lays a foundation to practical application. Bosch company in 1978 first launched the digital electronic control unit of the brake system, and ABS2 Bosch holding device in the Mercedes Benz, which opened on the modern ABS system development sequence Although the Bosch ABS2 of electronic control device is a separation of the components, but due to the digital electronic control device and analog electronic control device, the reaction speed, compared to the control accuracy and reliability are significantly improved, therefore, Bosch ABS2 control effect already is quite good. From then on, Europe, America and Japan, many professional company and brake car companies have developed a variety of ABS system. According to statistics, the whole world has more than 60% of new cars equipped with ABS device. When the car brake wheel speed and the differences between body speed, can lead to the wheel and the road, when the wheel slippage between produce pure rolling way and the pavement at contact, the slip rate is zero, and wheel lock the slip rate is 100%. When the slip rate between 10% ~ 30%, the largest transfer of power. The basic principle of braking antilock brake system (2, 3] is based on the above research, through the control regulation system in power, braking process, to the wheel in the slip rate control, within the scope of the right to obtain the best braking effect. ABS system hardware mainly by the wheel sensor, electronic control devices, brake pressure regulator three major components, constitute a to the slip rate is the control of the target of the closed-loop control system. The wheel speed sensor and the data transfer to the electronic control device. Control device is a microprocessor, according to the wheel speed sensor signal to calculate the speed of the car. In the braking process, reducing speed and control device of programmed ideal reducing the speed of characteristic curve in comparison. If control device judge the wheel reducing speed too large and the wheel will embrace died, signal to hydraulic regulator, hydraulic regulator is according to the control device of the signal to the brake wheel cylinder of hydraulic control (the boost, the pressure or blood pressure). Brake pressure to adjust the frequency of the cycle up to 6 ~ 20 H z. ABS technology at the core of theproblem is the control algorithm of research. The control car ABS is a complex, essential nonlinear control problem. In recent years, domestic and foreign scholars in the control of ABS calculate Method on the many theoretical research, mainly in the following several control methods. Now automotive ABS system most of the products are the addition, subtraction speed control, and additional threshold some auxiliary threshold, not involve specific mathematical model. Threshold control for nonlinear systems is an effective control method. In the braking process, can be a primary angular velocity threshold, when actual angular velocity over the threshold, the controller order to release, the wheel brake pressure to rotate faster; A Angle acceleration, when the threshold of angular velocity to reach this threshold, controller and issue commands to control moment, increased, and the wheel as slow movement. Can use a wheel angular velocity sensor as a single wheel signal, and electronic controller in set reasonable add, subtract speed threshold method, can come true to the embrace of the brake cycle. Logic threshold control the fault is that control system of the various threshold and the holding time is from repeated test that experience, and no sufficient data the theoretical basis of the stability of the system and the quality is difficult to evaluation. The optimal control method is based on state space method of modern control theory method. The optimal control method and threshold control method is different, it is a kind of based on the analysis of the model control method. The idea is based on the abs all the control requirements, according to the principle of optimization for brake antilock brake system optimal control goals. This control method is considered the control process of state changes course and make the control process smoothly; Defect is the control effect of quality mainly depends on the mathematical model of the system, quality control is difficult to accurately. The classic of PID control parameters setting is set up on the basis of gather together in try, as long as the scene setting PID parameters, you can get right better control effect. In the ABS in a definition of the expected sliding rate S and actual sliding rate for the input of the difference of the PID, the PID control algorithm is calculate control air pressure value feedback to brake system, a typical feedback control. Its defect is control effect quality depends on the accuracy of the parameter setting. Fuzzy control is based on experience of the rules of the control, and have not rely on the mathematical model of the object, easy to use the experience, knowledge is robust and simple practical. Control rules to the law of thinking. Defect is no effective general calculation method, can only rely on industrial automation instrument and a plan of the device experience and repeated test. By automobile braking antilock brake the basic principle of the braking process, it is known that the nature of the problem is to the wheel the slip rate control adhesion coefficient in the peaks of the Sk, the sliding mode variable structure according to the system of the state, and deviation and at that time, in different derivative value area, in order to control the ideal switch mode switch control the amount of and symbols, in order to ensure that the system in sliding area is small, within the scope of the state trajectory S sliding in the pitch curve sliding into a control target tsinghua university song jian and other car braking process according to the physical nature of international proposed first to brake dissipation power as the target of the control method. Considering the car of the deceleration process, in fact, is the average kinetic energy of the car into other forms of energy dissipation process. Accordingly, if you take the reasoning brake friction power (or says dissipation power) maximum control targets of ABS, have the potential to give consideration to the braking stability and brake performance. This method than the threshold method has good stability, high efficiency of braking, strong adaptability and control of road surface features obvious etc. Characteristics. Research shows that the control method can have a good application prospect. Drive torque system (hereinafter referred to the ASR) is perfect and added. ABS ASR system can improve the car is in the most slippery road stability and acceleration of the electronic device. Its role is mainly through the control engine torque and a car braking system means to control the driving force, to prevent the wheels idling sliding, maintain the best driving force. ABS guarantee The car braking process, the stability of the direction is guaranteed the car ASR process (beginning, the direction of the acceleration) stability and handling. Many of the cars, the modern electronic control device equipped with ABS ASR electronic control signal devices to exchange interface. And ASR and a major part of the ABS (such as electronic controller, wheel sensor, brake pressure regulators) can be used with or Shared with the car with the ABS ASR system, just the premise, differential control valves and engine control cylinder engine can. This shows, ABS and ASR combination, can make full use of the relevant parts of the car, and active safety will be more assured. Vehicle stability control device (hereinafter referred to as VSC) use two sensors were sensor car yaw-rate and lateral acceleration, and car will shift to Angle and the actual direction are compared. When it found the car is not according to the intention of motorists road, immediately sent to the ASR and ABS correction signal, indicating they take measures to make the car to the correct direction. These system although functions and the structure is different, but the work is similar to the process is sensor signal, she is calculated, the execution processing ECU institutions take corresponding actions. In the system composition, pick the accuracy of the sensor signal directly influence the results of ECU, additional, wheel sensor most is installed in the bad environment, especially near to heat resistant, vibrationresistant sex, the magnetic, corrosion resistance has high request, to the improvement of the performance of the sensor is very important. ABS and electronic throttle control system, electronic all control type (or half controlled) suspension, electronic control four-wheel steering, electronic control hydraulic turn To the electronic control, automatic transmission, cruise control system, global positioning system, etc. Various kinds of electronic control system, can make the combined use of car movement remains in the best state. Along with the electronic control units in car has more and more application, vehicle electronic equipment of the data communication between becomes more and more important, the distributed control system for infrastructure automobile vehicle electronic network system is very necessary. Large amounts of data exchange, high reliability and rapid sex is cheap to automobile electronic network system requirements. The network system, the processor independent operation, the control to improve the performance of the car on something, and in the other processors need to provide according to service. When The structure of the network inside the car relies mainly on the bus transmission technology. Car through a kind of communication is bus transfers of agreement will car electronic control units (engine, ABS, automatic transmission, etc.), intelligent sensor, intelligent instrument, and link up a car interior network. Its advantages are: reduced the number of cable and wire harness in volume, improve the electronic system reliability and maintainability; The general sensors, achieve the purpose of sharing data; Improve the flexibility of the system, that is, through the system software can realize the change of system function. Car ABS technology has been acknowledged as the world, ABS change Good the car brake performance, and the shorter the braking distance. Avoid the wheel lock so as to avoid the loss of car to ability, lose the direction stability of the phenomenon. It would be expected that the recent all kinds of vehicles will be equipped with the technology. Of course, ABS technology is still have defects, such as the stability of system still need to improve, control algorithm of further research and improvement. Through the simulation shows, in the design of fuzzy controller, through the adjustment of the fuzzy controller membership functions, the error in the basic fuzzy subsets of domain non-uniform distribution and ZO interval of the retreat to small enough, without any increase in the control strategy of the case, make the steady-state error of the fuzzy controller is greatly reduced, has the good control effect, short setting time, no overshoot, the improved fuzzy controller in steady precision at the same time, continued to parameter time-variance and fuzzy controller of interference has strong adaptability. All in all, this method improves the fuzzy control the system steady control precision, to improve the system dynamic and static quality. Due to the adjustment of the fuzzy controller membership function is very convenient, and therefore, this method is simple and useful for the fuzzy controller is widely used, provide an easy method.附錄 B.汽 車 ABS 技 術 及 其 發(fā) 展 趨 勢在汽車防抱死制動系統出現之前, 汽車所用的都是開環(huán)制動系統。其特點[ 1, 2] 是制動器制動力矩的大小僅與駕駛員的操縱力、制動力的分配調節(jié)以及制動器的尺寸和型式有關。由于沒有車輪運動狀態(tài)的反饋信號, 無法測知制動過程中車輪的速度和抱死情況, 汽車就不可能據此調節(jié)輪缸或氣室制動壓力的大小。因此在緊急制動時, 不可避免地出現車輪在地面上抱死拖滑的現象。當車輪抱死時, 地面的側向附著性能很差, 所能提供的側向附著力很小, 汽車在受到任何微小外力的作用下就會出現方向失穩(wěn)問題, 極易發(fā)生交通事故。在潮濕路面或冰雪路面上制動時, 這種方向失穩(wěn)的現象會更加嚴重。汽車防抱死制動系統( Anti?lock Braking System 簡稱 ABS)的出現從根本上解決了汽車在制動過程中的車輪抱死問題。它基本功能就是通過傳感器感知車輪每一瞬時的運動狀態(tài), 并根據其運動狀態(tài)相應地調節(jié)制動器制動力矩的大小以避免出現車輪的抱死現象, 因而是一個閉環(huán)制動系統。它是電子控制技術在汽車上最有成就的應用項目之一, 汽車制動防抱死系統可使汽車在制動時維持方向穩(wěn)定性和縮短制動距離, 有效提高行車的安全性。汽車 ABS 可以說是汽車安全歷史上最重要的三大發(fā)明之一(另外兩個是安全氣囊與安全帶),ABS 也是其他安全裝置(如 ESP 行車動態(tài)穩(wěn)定系統與 EBD 剎車力分配系統)的基礎。精于汽車電子技術的德國博世( Bosch)公司研發(fā) ABS 系統的起源要追溯到1936 年, 當年博世申請了機動車輛防止剎車抱死裝置 ?的專利。1964 年(集成電路誕生)博世公司再度開始 ABS 的研發(fā), 最后有了? 通過電子裝工業(yè)儀表與自動化裝置置控制來防止車輪抱死是可行的? 結論, 這是 ABS 名詞在歷史上第一次出現。世界上第一具 ABS 原型機于 1966 年出現, 向世人證明? 縮短剎車距離 ?并非不可能。因為投入的資金過于龐大, ABS 初期的應用僅限于鐵路車輛或航空器。70 年代后期, 數字式電子技術和大規(guī)模集成電路的迅速發(fā)展, 為 ABS 系統向實用化發(fā)展奠定了基礎。博世公司在 1978 年首先推出了采用數字式電子控制裝置的制動防抱系統博世 ABS2, 并且裝置在奔馳轎車上, 由此揭開了現代 ABS 系統發(fā)展的序幕。盡管博世 ABS2 的電子控制裝置是由分離元件組成的, 但由于數字式電子控制裝置與模擬式電子控制裝置相比, 其反應速度、控制精度和可靠性都顯著提高, 因此, 博世 ABS2 的控制效果已相當理想。從此以后, 歐、美、日的許多制動器專業(yè)公司和汽車公司相繼研制了形式多樣的 ABS 系統。據統計, 目前全世界已有超過 60%的新車裝有 ABS 裝置。汽車制動時由于車輪速度與車身速度之間存在著差異, 會導致車輪與路面之間產生滑移, 當車輪以純滾動方式與路面接觸時 , 滑移率為零 , 而車輪抱死時其滑移率為100% 。當滑移率在 10% ~ 30% 之間時, 傳遞最大的制動力。制動防抱死系統的基本原理[ 2, 3] 就是依據上述研究成果, 通過控制調節(jié)制動力, 在制動過程中, 把車輪滑移率控制在合適的范圍內, 取得最佳的制動效果。ABS 系統硬件構成主要由輪速傳感器、電子控制裝置、制動壓力調節(jié)器 3 大部分組成, 構成一個以滑移率為控制目標的閉環(huán)控制系統。傳感器測量車輪轉速并這一數據傳送至電子控制裝置上??刂蒲b置是一個微處理器, 根據車輪轉速傳感器信號來計算車速。在制動過程中,減速度與控制裝置中預先編制的理想減速度的特性曲線相比較。如果控制裝置判斷出車輪減速度太大和車輪即將抱死時, 就發(fā)出信號給液壓調節(jié)器, 液壓調節(jié)器就根據控制裝置的信號對制動輪缸的油壓進行控制(升壓、保壓或降壓)。制動壓力調節(jié)循環(huán)的頻率可達 6~ 20H z。ABS 技術的一個核心問題就是控制算法的研究。汽車 ABS 的控制是一個復雜的、本質非線性的控制問題。近年來, 國內外學者對 ABS 的控制算法進行了很多理論研究, 主要有以下幾種控制方法。目前汽車 ABS 系統絕大多數產品都是采用加、減速度門限值控制, 并附加一些輔助的門限值, 并不涉及具體的數學模型。門限控制是對非線性系統的一種有效控制方法。在制動過程中, 可以預選一個角速度門限值, 當實際的角速度超過此門限值時, 控制器發(fā)出指令, 開始釋放制動壓力使車輪得以加速旋轉; 一個角加速度門限值 , 當車輪的角速度達到此門限值時, 控制器又發(fā)出指令, 使控制力矩增大, 車輪作減速運動。可以采用一個車輪角速度傳感器作為單輪信號, 同時在電子控制器中設置合理的加、減速度門限值, 就可以實現防抱制動的循環(huán)。邏輯門限控制的缺點在于控制系統中的各種門限及保壓時間都是從反復試驗中得出的經驗數據, 而無充分的理論依據, 系統的穩(wěn)定性等品質難以評價。最優(yōu)控制方法是基于狀態(tài)空間法的現代控制理論方法。它可以根據車輛? 地面系統的數學模型,采用狀態(tài)空間的概念, 在時間域內研究汽車防抱死制動系統。最優(yōu)控制方法和門限值控制方法不同,它是一種基于模型分析的控制方法。其思路是根據防抱死制動系統的各項控制要求, 按照最優(yōu)化的原理來求得制動防抱死系統的最優(yōu)控制目標。這種控制方法的優(yōu)點是考慮了控制過程中狀態(tài)變化的歷程而使控制過程平穩(wěn); 缺點是控制效果的優(yōu)劣主要依賴于系統的數學模型, 控制質量難以準確把握。經典 PID 控制的參數整定是建立在試湊基礎上的, 只要現場整定 PID 參數合適, 就會得到較好的控制效果。在 ABS 中定義期望的滑移率 S 與實際滑移率之差為 PID 的輸入, 由 PID 控制算法算出控制氣壓值反饋給制動系統, 構成典型的反饋控制。其缺點是控制效果的好壞依賴于參數整定的準確度。模糊控制是基于經驗規(guī)則的控制, 具有不依賴對象的數學模型, 便于利用人的經驗知識, 具有魯棒性強和簡單實用等優(yōu)點??刂埔?guī)則符合人的思維規(guī)律。缺點是沒有有效通用的計算方法, 只能依靠設工業(yè)儀表與自動化裝置計者的經驗和反復調試。由汽車防抱死制動的基本原理可知, 其制動過程的本質問題是把車輪的滑移率控制在附著系數的峰值點 Sk, 則滑動模態(tài)變結構根據系統當時的狀態(tài)、偏差及其導數值, 在不同的控制區(qū)域, 以理想開關的方式切換控制量的大小和符號, 以保證系統在滑動區(qū)域很小的范圍內, 狀態(tài)軌跡 S 沿滑動換節(jié)曲線滑向控制目標清華大學宋健等根據汽車制動過程的物理本質在國際上首次提出了一種以制動器耗散功率最大為目標的控制方法。考慮到汽車減速制動的過程, 實際上是將汽車的平均動能轉化為其他形式能量的耗散過程。據此推理, 如果取制動器的摩擦功率(或稱耗散功率)最大為 ABS 的控制目標, 則有可能兼顧制動穩(wěn)定性和制動效能。該方法較之門限值方法具有制動穩(wěn)定性好、效能高、對路面適應性強和控制特征明顯等特點。研究表明, 這種控制方法會有良好的應用前景。驅動防滑系統(簡稱 ASR)是對 ABS 的完善和補充。ASR 系統是能提高汽車在易滑路面上的穩(wěn)定性和加速性的電子裝置。其作用主要是通過控制發(fā)動機扭矩和汽車的制動系統等手段來控制驅動力, 防止車輪空轉打滑, 保持最佳驅動力。ABS 保證了汽車制動過程中方向的穩(wěn)定性, ASR 則保證了汽車行駛過程中(起步、加速時)的方向穩(wěn)定性和操縱性?,F代的很多轎車中, ABS 電子控制裝置設有與 ASR 電子控制裝置交換信號的接口。并且 ASR 和 ABS 的主要部件(如電子控制器、輪速傳感器、制動壓力調節(jié)器) 可以通用或共用, 裝有 ABS 的汽車在裝用 ASR 系統時, 只需加裝差速制動閥、發(fā)動機控制閥和發(fā)動機控制缸即可。由此可見, ABS 與 ASR 結合使用, 可以充分利用有關部件, 并且汽車的主動安全性將更有保證。車輛穩(wěn)定性控制裝置(簡稱VSC ) 利用兩個傳感器分別感測汽車橫擺角速度和汽車側向加速度,并將轉向角與實際方向進行比較。當它發(fā)現汽車并不按駕車人的意圖行駛時, 就立即向 ASR 和 ABS發(fā)出修正信號, 指示它們采取措施使汽車駛向正確的方向。這些系統盡管功能和結構各異, 但工作過程很相似, 都是傳感器拾取信號, ECU 進行計算處理,執(zhí)行機構采取相應動作。在這些系統組成中, 傳感器拾取信號的準確程度直接影響 ECU 的計算結果,另外, 輪速傳感器大多數是安裝在車輪附近 , 環(huán)境惡劣 , 特別是對耐熱性、耐振性、防磁性、耐腐蝕性有很高的要求, 對傳感器這些方面性能的改進十分重要。ABS 與電子油門控制系統、電子全控式(或半控式) 懸掛、電子控制四輪轉向、電子控制液壓轉向、電子控制自動變速器、巡航控制系統、全球定位系統等各種電子控制系統的組合使用, 可以使汽車的運動始終保持在最佳狀態(tài)。隨著電控單元在汽車中的應用越來越多, 車載電子設備間的數據通信變得越來越重要, 以分布式控制系統為基礎構造汽車車載電子網絡系統是很有必要的。大量數據的快速交換、高可靠性及廉價性是對汽車電子網絡系統的要求。網絡系統中,各處理機獨立運行, 控制改善汽車某一方面的性能,同時在其他處理機需要時提供據服務。汽車內部網絡的構成主要依靠總線傳輸技術。汽車總線傳輸是通過某種通訊協議將汽車中各種電控單元(發(fā)動機、ABS、自動變速器等)、智能傳感器、智能儀表等聯接起來, 而構成的汽車內部網絡。其優(yōu)點有: 減少了線束的數量和線束的容積, 提高了電子系統的可靠性和可維護性; 采用通用傳感器, 達到數據共享的目的; 改善了系統的靈活性 , 即通過系統的軟件可以實現系統功能的變化。汽車 ABS 技術已經得到了全球的公認, ABS 改善了汽車的制動效能, 縮短了制動距離。避免了車輪抱死, 從而避免了汽車喪失轉向能力、失去方向穩(wěn)定性的現象發(fā)生??梢灶A計, 近期各種車輛都必將裝備這種技術。當然, ABS 技術仍有缺陷, 比如系統的穩(wěn)定性還需提高, 控制算法還需進一步的研究和改善。通過仿真可見, 在設計模糊控制器時, 通過調整模糊控制器的隸屬度函數, 使誤差的基本模糊子集在論域上不均勻分布且 ZO 的區(qū)間縮到足夠小 , 在不增加控制策略的情況下, 使得模糊控制器的穩(wěn)態(tài)誤差大大減小, 具有良好的控制效果 , 調節(jié)時間短、無超調 , 在提高模糊控制器的穩(wěn)態(tài)精度的同時, 仍保持著模糊控制器對參數時變和對干擾具有較強的適應能力??傊? 該方法提高了模糊控制系統的穩(wěn)態(tài)控制精度, 改善了系統的動、靜態(tài)品質。由于調整模糊控制器的隸屬度函數非常方便, 因此, 該方法簡便實用 , 為模糊控制器廣泛應用, 提供了一種簡便方法。