【溫馨提示】壓縮包內(nèi)含CAD圖有下方大圖片預覽,下拉即可直觀呈現(xiàn)眼前查看、盡收眼底縱觀。打包內(nèi)容里dwg后綴的文件為CAD圖,可編輯,無水印,高清圖,壓縮包內(nèi)文檔可直接點開預覽,需要原稿請自助充值下載,所見才能所得,請見壓縮包內(nèi)的文件及下方預覽,請細心查看有疑問可以咨詢QQ:11970985或197216396
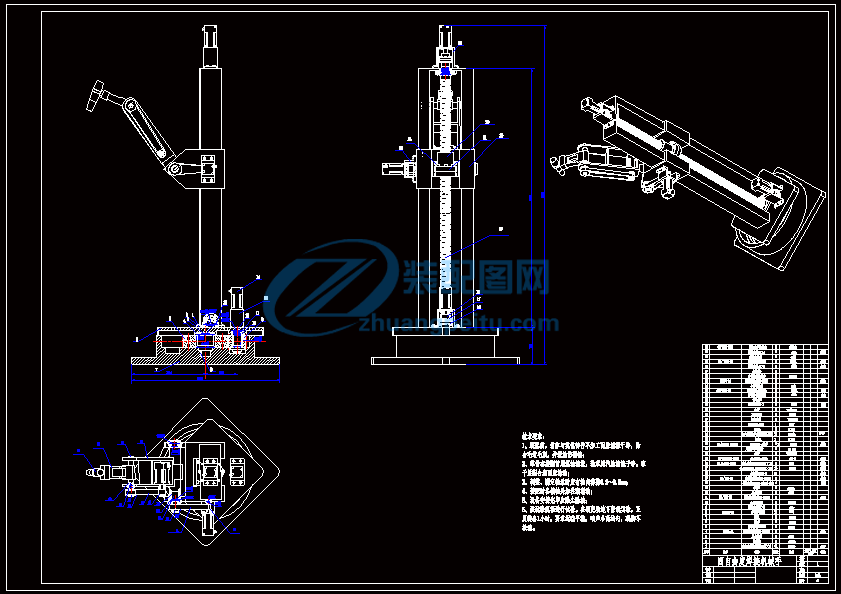
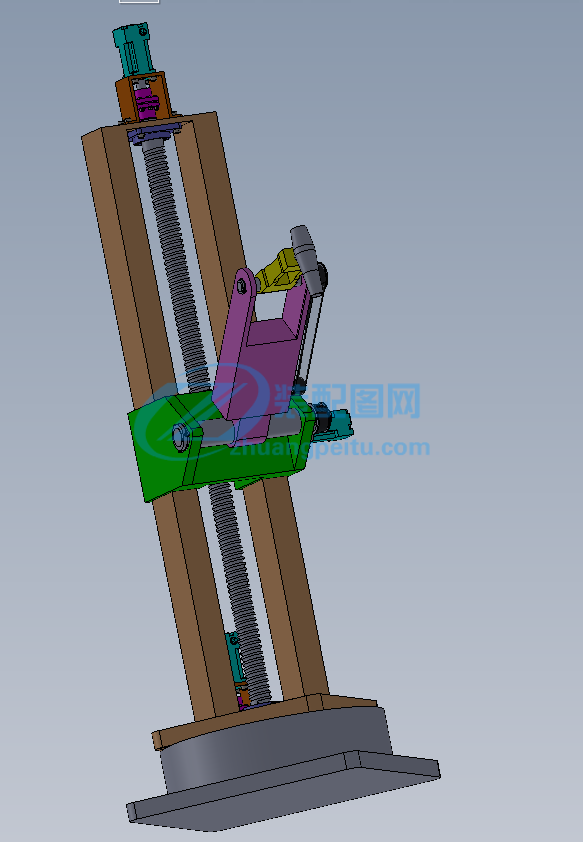
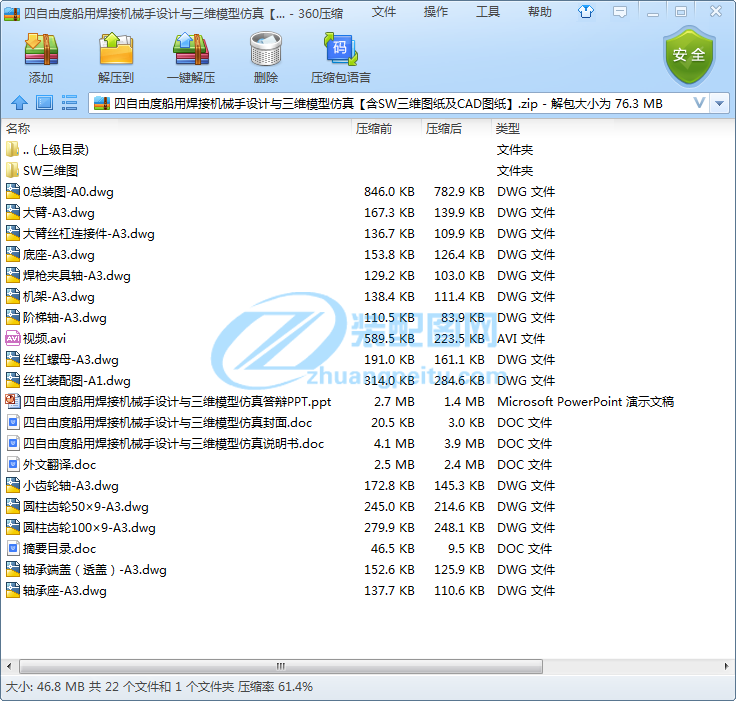
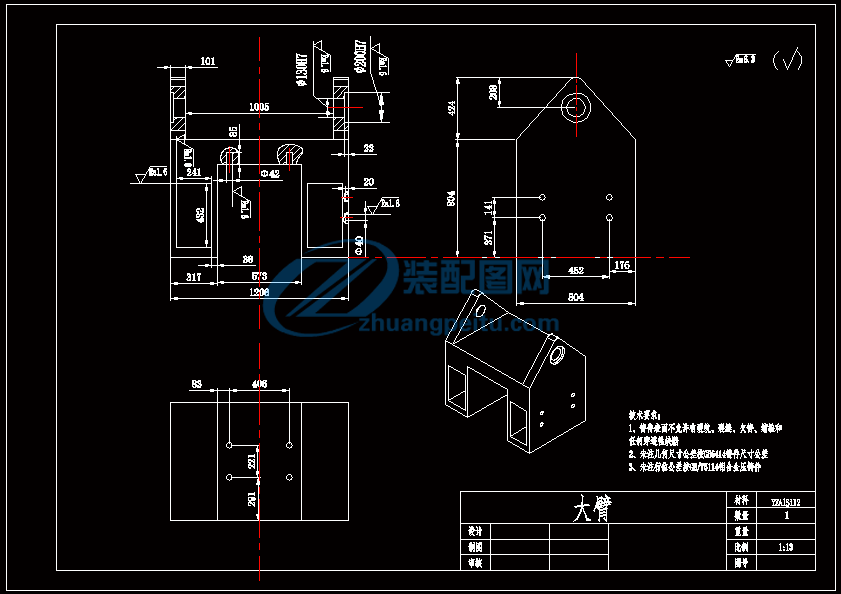
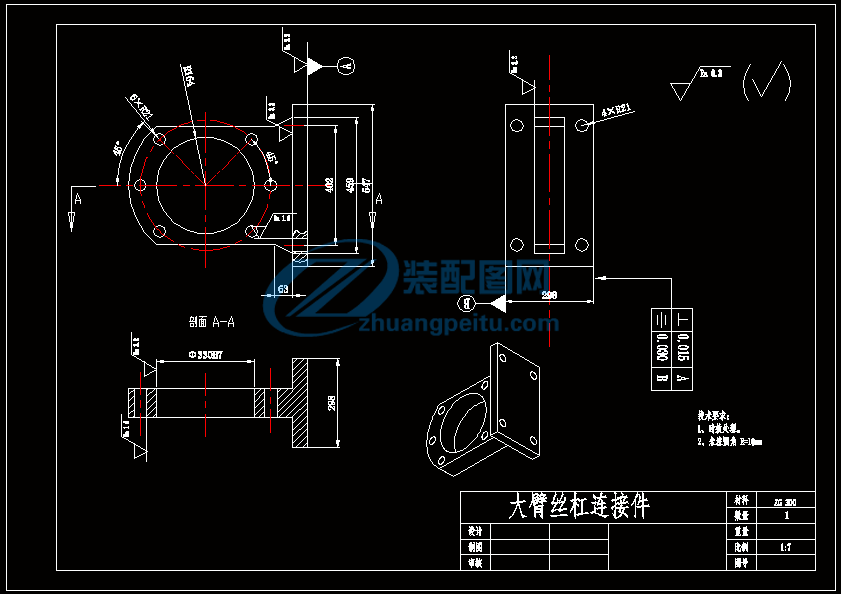

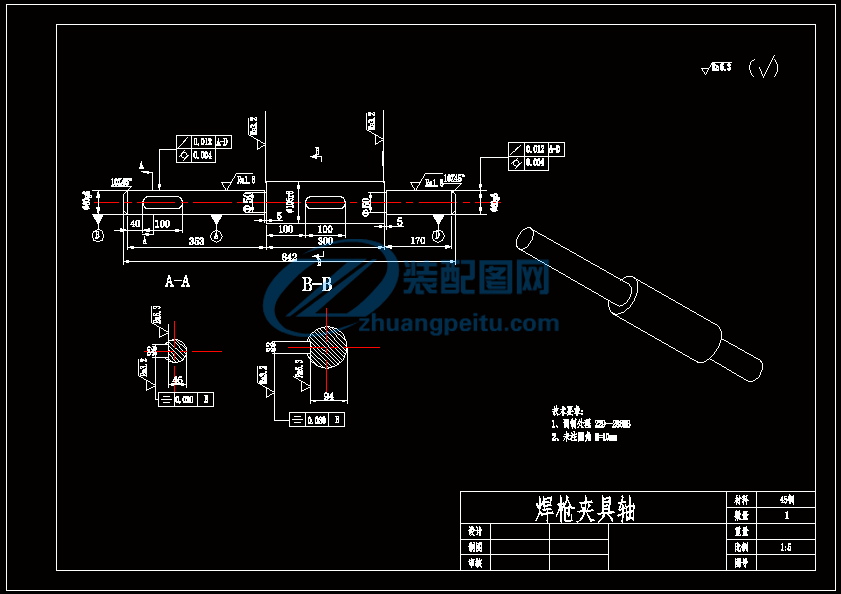
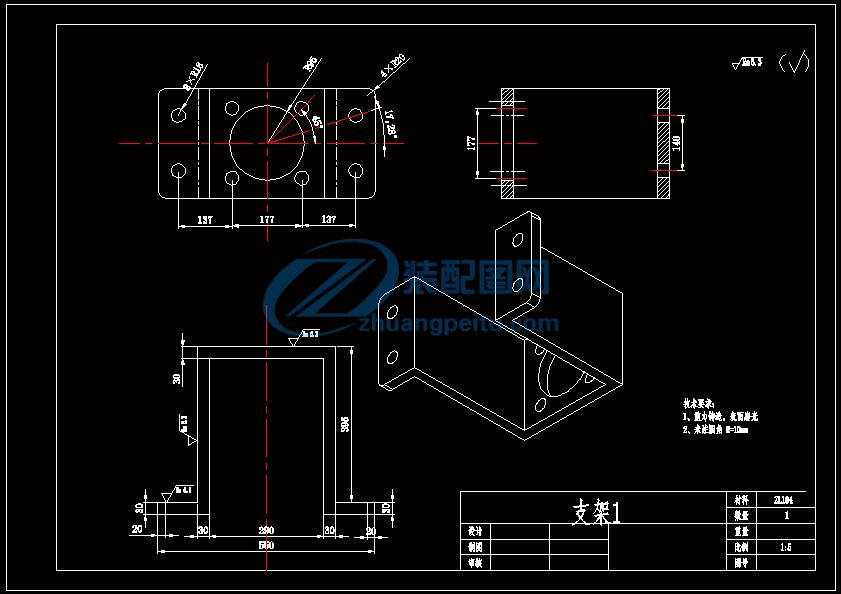
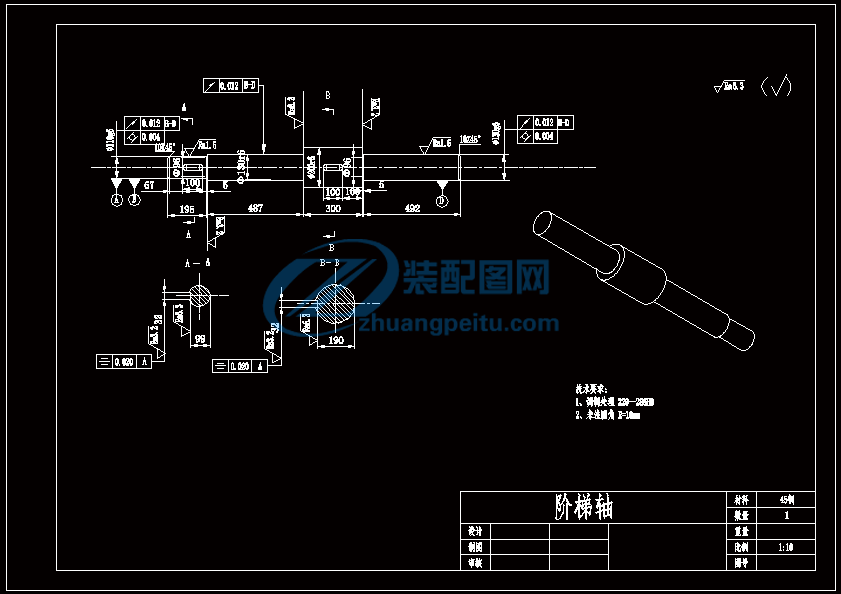
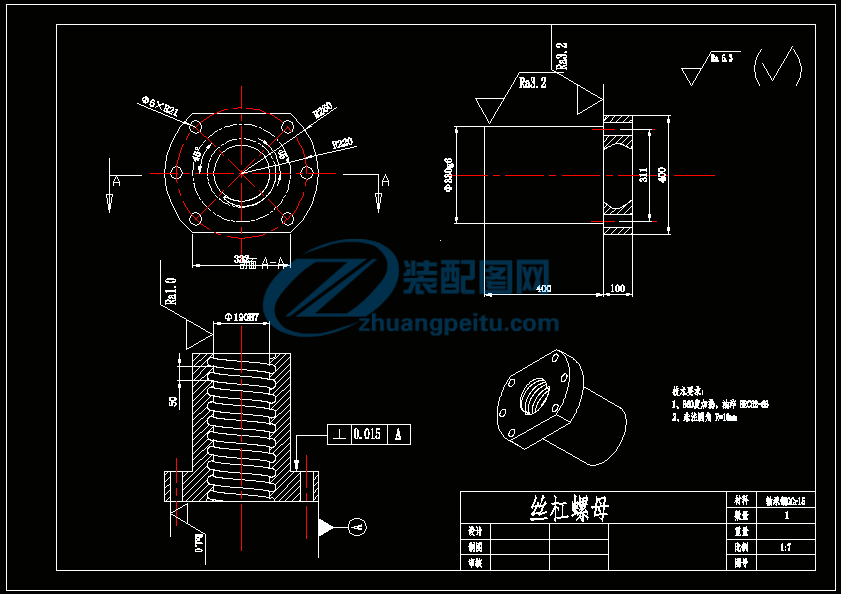
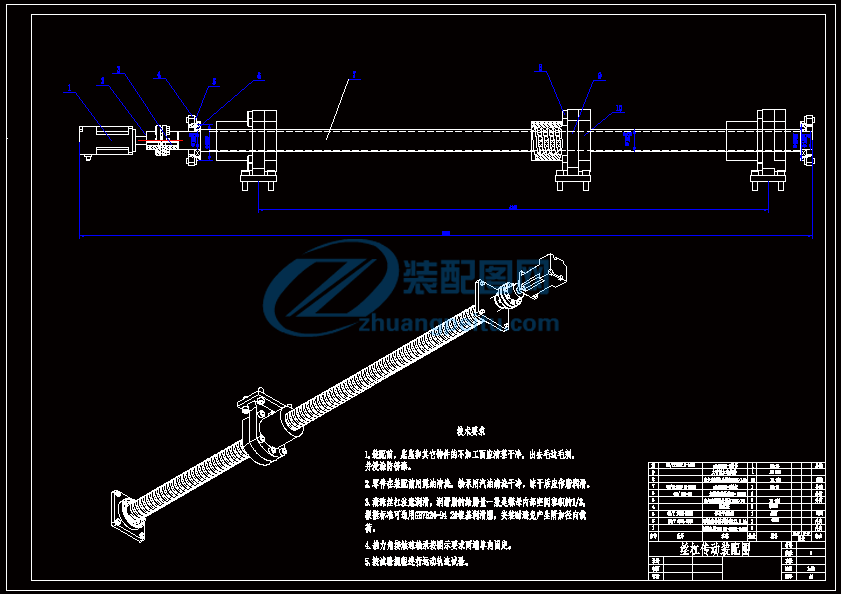
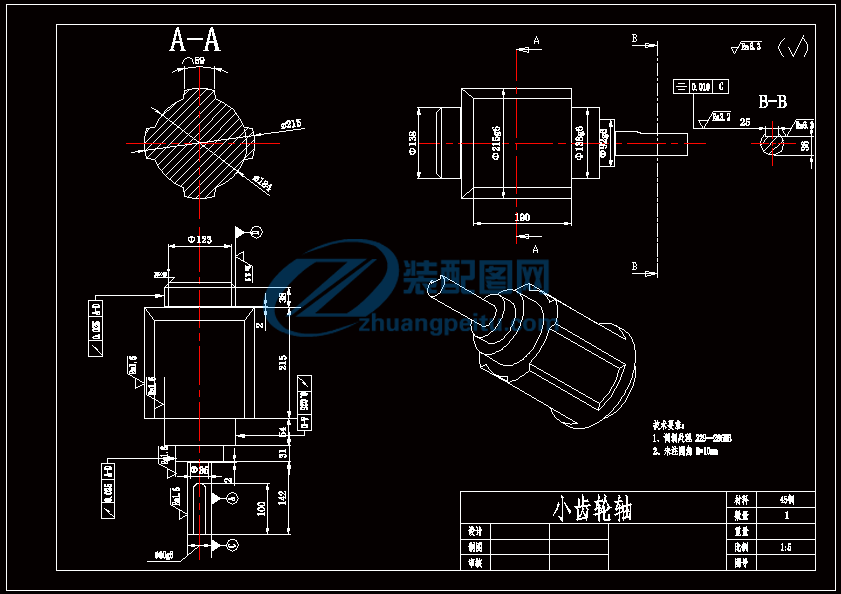
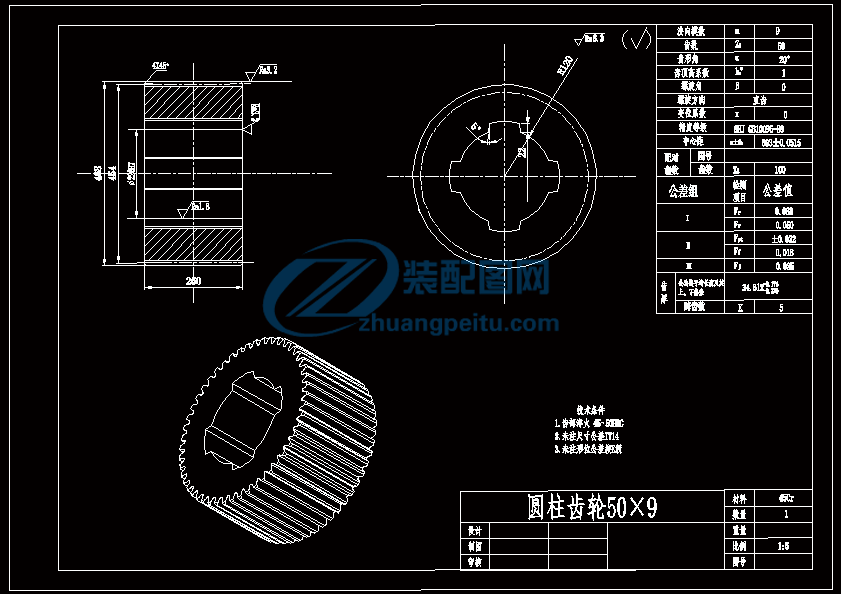

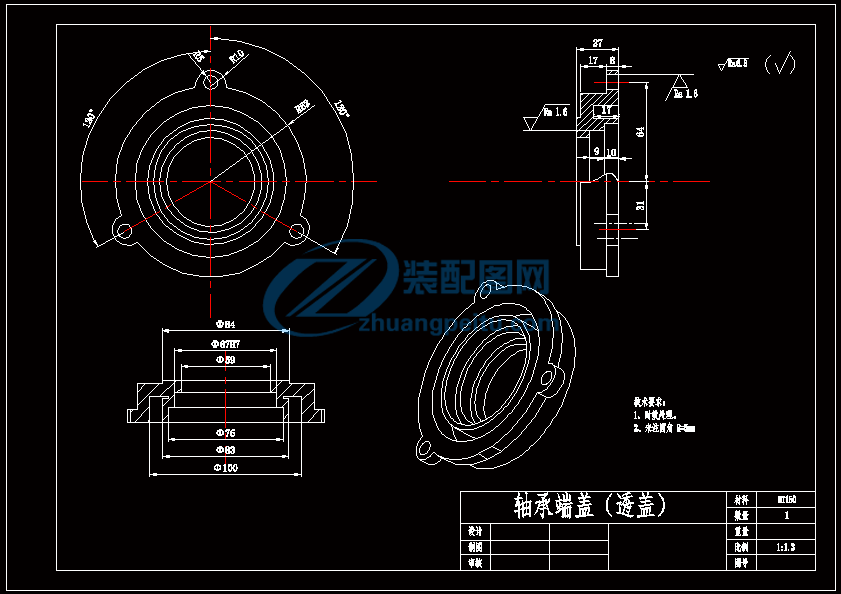
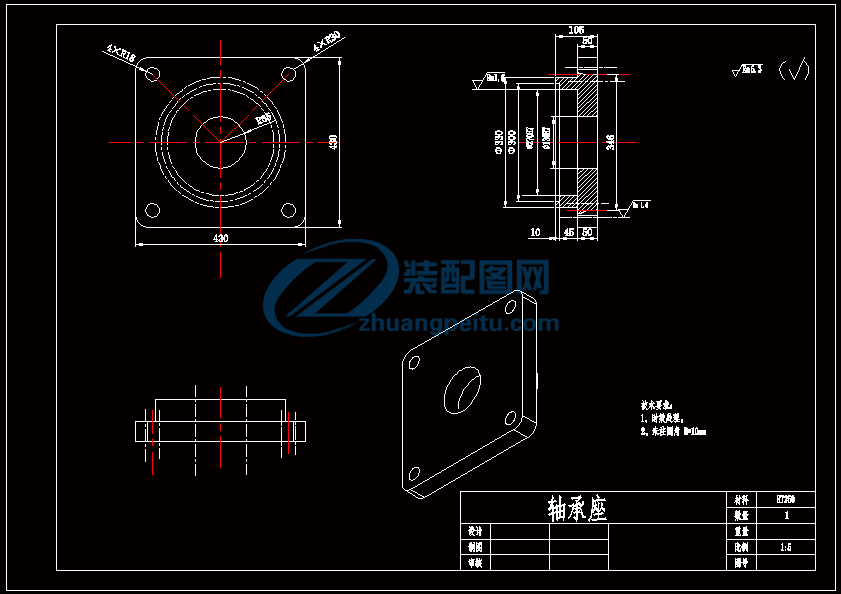
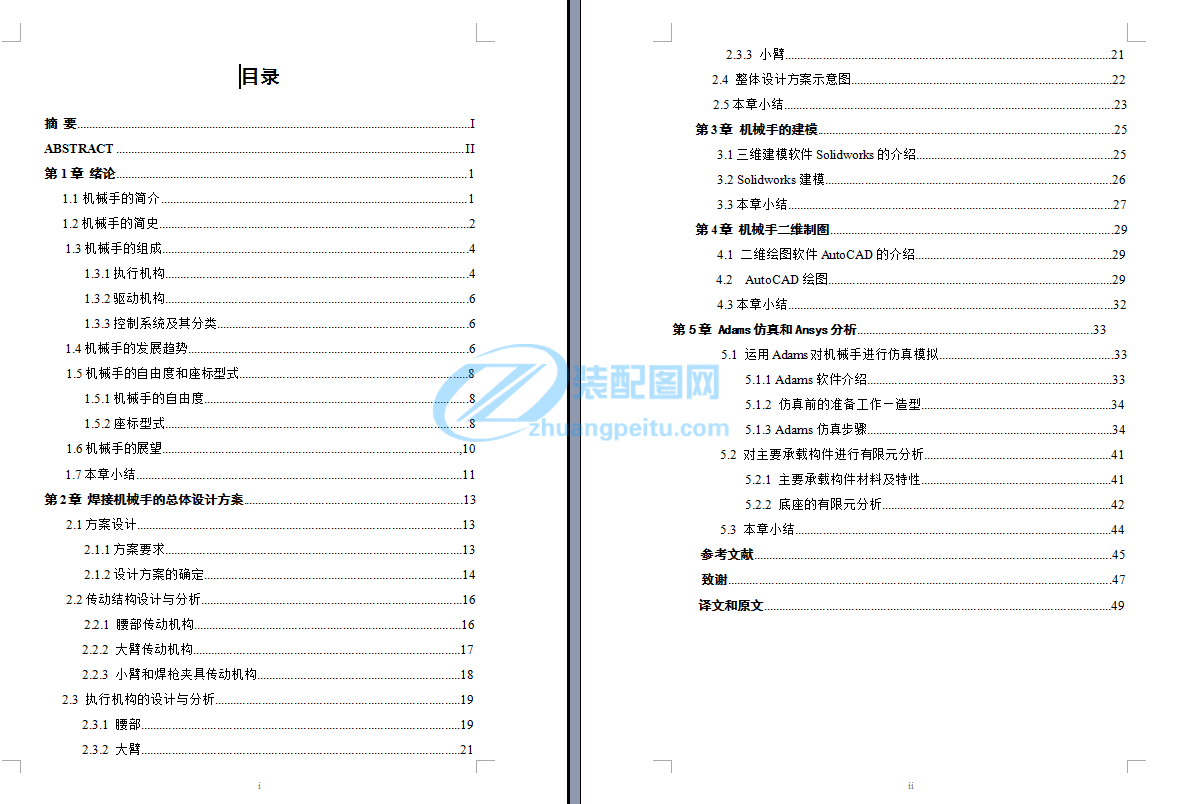
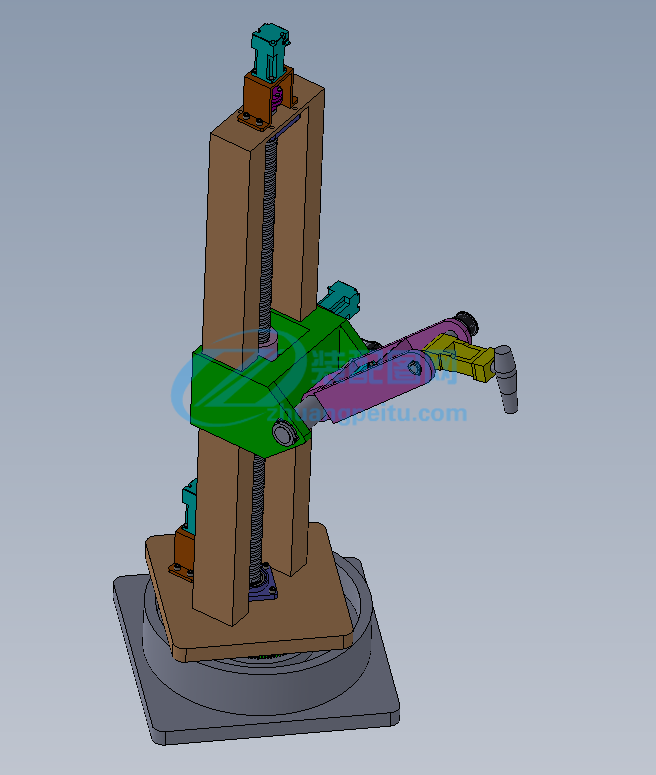
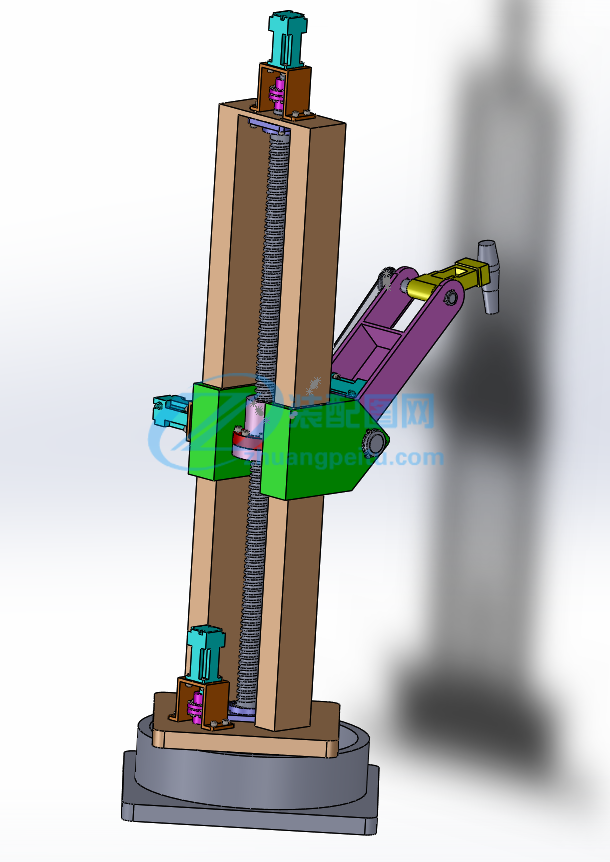
譯文和原文
P3R3串行機械手移動焊接機器人優(yōu)化設計和工作空間分析
摘要
本文介紹了基于工作空間分析的移動焊接機器人的優(yōu)化設計。一個焊接機器人已經(jīng)被開發(fā)用于船舶的雙層船身結構,而且展現(xiàn)了良好的焊接性能。但是優(yōu)化運動變量來保證在船舶里的焊接性能令人滿意是很有必要的。面向任務的工作區(qū),是工作區(qū)啟用特定的旋轉,被定義驗證機器人的焊接能力,并合并所需的旋轉功能。計算工作空間,一個同時考慮投球和偏航角度的幾何方法被采用。基于工作空間分析,一個方案是編譯考慮質量減少,和一個帶有工作空間邊緣約束的在設計參數(shù)和工作區(qū)之間的一個比率。擬議的優(yōu)化過程是由粗細搜索兩個步驟組成。在粗搜索步驟中,一個滿足幾何設計約束的可行的參數(shù)區(qū)域(定期用量法)被定義,和獲得無任何考慮的目標函數(shù)。在細搜索步驟,在整個的定期用量法中,使用優(yōu)化技術的共軛梯度法確定設計變量。這種建議的方法來計算面向任務的工作區(qū)和程序優(yōu)化設計,將適用于一般工業(yè)機器人。
關鍵詞:工作區(qū)優(yōu)化;移動焊接機器人;串行機械手;面向任務的工作區(qū)
1. 介紹
1.1在船舶建造工業(yè)中的焊接機器人
在過去的幾十年里,已經(jīng)有一大批試圖在造船過程中實現(xiàn)自動化焊接。在這里,我們想介紹先進的焊接機器人系統(tǒng)。表1-A展示了智能移動焊接結構,這些結構是由2個(表1-A(a),[1]或者3個(表1-A(b),[2])棱柱和2個轉動關節(jié)組成。他們使用差動驅動輪定位在橫向方向。因此,如果一個特定的魯棒算法高定位精度并不存在,差動驅動由于滑動不能保證在重復的多道焊中的平直度。
在一個開放的區(qū),用開銷龍門起重機可以將一個多軸鉸鏈機器人放置于此。DANDY [3],顯示在表1-B,已開發(fā)和成功地用于大宇造船的船廠和韓國的海洋工程有限公司。當機器人完成單一焊接任務,機器人通過使用安裝在船的天花板上的開銷龍門起重機移動到第二焊接位置。因為開銷起重機不能到達封閉區(qū)的內(nèi)部,所以適用于區(qū)域的機器人只能被限制在開放區(qū)。此外,控制器位于開放區(qū)的外面,因此需要大量的電纜從外面進來。這就在封閉結構中處理幾個電纜過程中產(chǎn)生了困難。還有更多由多軸機器人系統(tǒng)與一個高架起重機組成的當前可用的系統(tǒng),,在[7,8]有相關描述。
在這一點上,我們想強調(diào)的是船舶建造環(huán)境中嵌入式控制器的重要性。在焊接中,一個電流用于在基本材質和自耗電擊棒之間觸發(fā)電弧。在那一刻,眾所周知,電子的隨機運動攜帶電流發(fā)生,影響了連接在機器人和控制器之間的信號電纜。此外,很多機器人同時在同一個區(qū)域焊接。因此,可以認為模塊化控制器有助于避免多種噪音對整個系統(tǒng)的消極影響?;诘侥壳盀橹挂呀?jīng)澄清了的事實可以知道,一個便攜式只焊接機器人的集成系統(tǒng)設計,需要一個模塊化控制器和輔助運輸設備,作為在封閉結構中工作的移動機器人的最終選擇,被大力提倡。
表1-C(a)顯示的是已在日本的日立Zosen船廠被開發(fā)的數(shù)控(NC)噴漆機器人[4]。一個6軸噴漆機器人,連同一個自動駕駛裝置,用一個可擴展的放置器放在了封閉區(qū)。然而,這種機器人系統(tǒng)需要一個800×1600平方毫米的出入孔。因為出入孔的尺寸與船舶的設計安全條例密切相關,任何擴大措施都必需得到船的主人的許可,這幾乎是不可能實現(xiàn)的。這個機器人噴漆系統(tǒng)的另一個嚴重的問題是,在封閉區(qū)域的內(nèi)部,它不能在橫向方向上自由移動。在西班牙的工業(yè)自動化研究所(IAI)開發(fā)了一個機器人系統(tǒng)稱為槳手1,可以用在一個封閉的區(qū)域[5];這個機器人像一個蜘蛛一樣移動,有四條腿可以擴展和收縮。它可以自主移動,因此可以克服很多在封閉區(qū)域中遇到的焊接障礙,,但它必須分解成七個模塊才可以放入一個封閉的區(qū)域,然后重新組裝起來。重組大約需要15分鐘,這是漫長的足以嚴重影響系統(tǒng)的生產(chǎn)效率[9]。
最近被建立的SNU的RRX平臺[6],克服了以前機器人的所有缺點,在超過一年的實地測試中,它的焊機和移動性能得到驗證。然而,值得一提的是這個系統(tǒng)在500×700平方毫米洞的出入仍然是相對困難的,盡管它滿足空間約束。主要的原因是它的尺寸相對工人來說還是很大的。
1.2 機械手的優(yōu)化
運動設計已在機器人的機械手臂設計中占有重要的地位,因為工作空間、速度和精度等系統(tǒng)的性能由它的幾何參數(shù)確定。特別的,確定維度的機械手的幾何參數(shù)主要受制于優(yōu)化非線性成本函數(shù),受到一組適當?shù)募s束。作為評判機械手臂質量的標準,人們越來越感興趣的是機械手的運動學特性,如工作區(qū)特性,調(diào)節(jié)指數(shù),靈巧的標準。
1.2.1 工作空間
已經(jīng)有很多的研究來優(yōu)化機械手的工作空間[10,11]。Kumar 和 Waldron提出[12]了一個在可及的和靈巧的工作區(qū)上的優(yōu)化設計和分析,用于幾何優(yōu)化[13]。一個可達的工作空間是末端可以不考慮取向而達到的位置,一個靈巧的工作空間是末端可以擁有完整的旋轉能力而達到的位置。Haug等人提出了一個復合的工作區(qū),這個工作區(qū)在所有的部分的關節(jié)區(qū)都具有指定的工作能力[14,15],和一個依據(jù)等級缺陷決定工作空間邊界的雅克比方法。Pond和Carretero還提出依據(jù)雅克比矩陣的條件數(shù)決定工作空間的雅克比方法[16]。Bonev和Ryu提出了一個定向工作區(qū):一個末端所有可達到的取向都在一個固定點上[17]。
1.2.2. 調(diào)節(jié)和靈巧
另一方面,各種評估工作空間運動性能的有關性能指標的研究在很長一段時間被發(fā)表。Salibury和Craig[18]用雅克比矩陣的條件數(shù)作為評估工作空間性能的優(yōu)化標準。Yoshikawa [19]提出了將雅克比矩陣的行列式作為可操縱性的測量(MOM), 而Stoughton and Kokkinis [20] 用最低奇異值和條件數(shù)。
值得特別注意的一點是,先前有關工作空間的概念是任務獨立的:他們對于特定的任務不能保證最好的機械手。因此,任務特異性直接考慮在規(guī)定的轉動能力,采用代表效果好確定工作空間邊界需要在特定的任務。并且MOM可以作為數(shù)學工具來驗證到奇異點的距離,而條件數(shù)可以被用作一個實際測量的生病調(diào)節(jié)[21]的工作區(qū)和運動精度[22]的機械手在它整個工作區(qū)。因此,可操縱性測量的需要將從避免的可能性奇點在縮放操作臂的尺寸的角度在本文出現(xiàn)。
1.3 研究目的
在這項研究中,任務導向的工作區(qū)和它的部分工作區(qū)是至關重要的在有效地獲得最優(yōu)設計。因為我們只需要35°的轉動能力,使一個Ushaped焊接任務,一個面向任務的工作區(qū)(TOW)可以得到排除無用的方向的末端。在這里,拖可以被定義為一組機器人末端位置這樣可以達到末端用一個預定義的轉動能力。即使我們只考慮規(guī)定的發(fā)展方向采用空間,工作空間搜索仍然是一個耗時程序。因此,為了減少計算成本,部分工作區(qū)(PW),它可以被視為一個橫截面積的牽引,提出了計算theTOWand之間距離的u形焊接部分沒有詳盡的搜索可能的職位候選人在完整的范圍的面向任務的工作區(qū)。一些研究提出的幾何處理機械手工作空間被發(fā)現(xiàn)在文學;但是,這個話題似乎是值得的受調(diào)查,應該是一個偉大的幫助在最優(yōu)設計。
利用提出的幾何治療在機械手工作區(qū),我們同時考慮結構質量和設計效率作為目標函數(shù)對最大化質量降低和減少損失的設計效率。設計包括兩個步驟:粗和細搜索。在粗搜索步驟,我們找到可行的參數(shù)區(qū)域(存取)在預定義的約束是滿意的。在找到搜索一步,我們分析目標函數(shù)在存取獲得最終的最優(yōu)參數(shù)集,提出兩步過程簡化通過將最優(yōu)設計問題的復雜約束條件和目標函數(shù)。
一個更重要的方面是可操縱性優(yōu)化設計措施,詳見1.2節(jié)。實際上,可操縱性僅用于避免奇點在優(yōu)化設計程序。然而,由于可操縱性是非常重要的決定焊接過程的質量,我們獨立分析可操作度在本文的末尾。確定最優(yōu)聯(lián)合的價值觀,例如由Zacharias et al.。[23],是還剩下一個問題需要解決。
2. 問題描述
本節(jié)描述了RRX移動焊接機器人和運動學分析是計算中使用的工作區(qū)。這個實驗結果的u形線焊接操作還描述了定義所需的旋轉。
2.1移動焊接機器人:RRX
2.1.1 RXX系統(tǒng)描述
圖2(一個)顯示的成分RRX焊接機器人,這是由三個子系統(tǒng)組成的移動平臺,一個連續(xù)式焊接機械手,嵌入式控制器。移動平臺使機器人的移動橫向和縱向方向就確信雙層船身內(nèi)部塊,和詳細過程的運動一直解釋說之前的出版物[6]。在搬到前面的u型焊接線,移動平臺是停在一個固定的位置,和焊接機械手操作。焊接機械手包括三個柱狀節(jié)理和三個轉動關節(jié)使6自由度(自由度)空間運動。
第四版的RRX組裝焊接機器人,或RRX4因為它被稱為,是顯示在圖2(b),它具有一些優(yōu)勢在前面的模型在其嵌入式控制器,減少噪聲級,它的更好的密封特點,也可在危險環(huán)境中使用。然而,最優(yōu)設計運動參數(shù)仍然是一個尚未解決的問題,成功的焊接性能就確信雙層船身結構內(nèi)的船只。
2.1.2 焊接機械手的運動學分析
圖3顯示了運動學模型的焊接部分的RRX機器人系統(tǒng),它包括一個3 p3r機械手組成一個PPRPRR串行鏈,P,R表示棱鏡和轉動關節(jié)分別?;顒雨P節(jié)的棱鏡來標示d1、d2和d4,參加革命活動關節(jié),θ5θ3來標示,和θ6。
被定義為一個問題的正運動學問題確定末端效應的姿勢時關節(jié)值給定的,所以可以串行機器人正運動學輕松解決使用齊次變換矩陣(HTM),定義如下[24]:
Rii哪里?1和有價證券?1代表方向和位置(我)th框架,分別對(我?1)th幀。RRX效應器的姿勢可以按順序計算乘HTM從基本幀(幀零)框架采用(第七框架),如情商。(2)。組件產(chǎn)生的矩陣如表2所示,在ci,si,cα,sα表示cos(θi),罪(θi),因為(α),和贖罪(α),分別。見[6]的詳細推導。
逆運動學問題的問題是找到共同價值觀的姿勢時,采用了。一般來說,逆運動學問題的系列機器人是一個非線性聯(lián)立方程,所以一些數(shù)值方法可以采用計算解決方案。然而,逆運動學的RRX平臺可以解決分析從HTM在情商。(2),聯(lián)合采用計算值HTM的組件,如情商。(3)。結果的逆運動學分析將被應用于計算工作空間在第三節(jié)。
2.2定義任務的焊接,u形邊界
焊接任務的機器人,和工作環(huán)境,圖4所示。動的RRX縱向加勁肋形式、和方法,u形焊接線。移動平臺的RRX停止其運動在一個預定義的固定距離,焊接機械手開始焊接,u形焊接線。焊接后段,RRX移動到前面下一個u型線和簡歷焊接。
的尺寸u形焊接線的不同就確信雙層船身類型的塊。尺寸的范圍是顯示在右邊的圖4。從給定的尺寸,所需的平行六面體形狀的位置工作空間定義焊接一個900×800×10毫米的體積,這是馬克斯(西城)××max(HL)馬克斯(WT),重量的寬度焊接珠,從橫向網(wǎng)絡地板。
在焊接過程中沿焊縫,焊接火炬,供給熱量、氣體和物質的對象被焊接,應該對焊點連續(xù)旋轉因此,一個更可靠的附加質量,達到了焊接過程。一般來說,不同的旋轉角度在連續(xù)焊接過程,所以測量的旋轉角是必要的焊接塊沿著u形焊接線。因為一個滾動的運動不會影響焊接性能,必需的角度對俯仰和偏航運動對于基地框架應該被定義。
一般來說,所需的偏航和節(jié)距角焊接由技術人員的經(jīng)驗,所以它是嗎很難定義精確的角度觀察人工處理操作。因此,RRX用于本研究獲得要求偏航和節(jié)距角,以便RRX操作執(zhí)行一個成功的焊接沿著u形線,旋轉角度的測量記錄的焊槍通過遠期運動學關節(jié)角的。焊接結果是密切檢查經(jīng)驗豐富的技術人員。自需要有一個比較大的利潤率的角度,一個合適的解決辦法就是所需的火炬角通過使用向前運動關系從聯(lián)合角度來衡量這個編碼器。焊接的質量,還會檢查的經(jīng)驗豐富的技術人員。
圖5(一個)顯示了運動的焊槍沿u形焊接線,框{ B }表示基礎構架,和幀{ T }表示工具框架。最初的工具框架焊接過程{ T0 }定義為旋轉(90°,0°、114°)就幀{ B },為了有對稱偏航螺距角。測量偏航螺距角焊炬、與尊重到幀{ T0 },表示為長度從原點的投影到y(tǒng)z平面,見圖5(b)。所需的yawpitch角度是確定為35°關于Z { T0 }在整個焊接過程。
執(zhí)行焊接工藝成功地,35°的偏航螺距轉動能力應該得到保證。因此,客觀的紙可以定義為優(yōu)化運動參數(shù)為了提高設計效率,同時滿足35°的轉動能力。在優(yōu)化過程中,一種新的方法確定提出了面向任務的工作區(qū)第三節(jié)。
3.確定任務導向的工作區(qū)
3.1幾何方法考慮結合偏航螺距角
本節(jié)提出了一種新的方法來考慮方向計算一個面向任務的工作區(qū)對匯率操縱國。通常,一個機械手的方向被定義為一個旋轉矩陣,由空間定向矢量和這個旋轉矩陣變換乘法。然而,表示的工具框架{ T },通過使用通常的慣例,不直觀的確定組方向的嗎指定范圍從規(guī)定的任務。這是因為,約定利用旋轉矩陣受到一系列的三個通過正常的歐拉角旋轉。
在這種方法中,一個指定范圍的方向的工具幀{ T },就基本框架{ B },是產(chǎn)生的簡單的向量的計算。該方法考慮了在一個固定方向的末端位置作為一組計算方向向量。這種方法更簡單,更直觀比傳統(tǒng)的方法,它也有優(yōu)點的考慮兩個偏航和節(jié)距角在同一時間。
圖6顯示了程序計算了定向向量,采用一個固定的位置周圍的末端。首先,旋轉z軸方向向量的初始工具框架{ T0 },需要35°偏航螺距角在這個研究。然后,讓一組M×新西蘭軸方向向量的向量計算顯示在底部圖6。滾動運動也被認為是在每個方向向量的z軸嗎防止發(fā)生沖突和焊接機械手結構。由此產(chǎn)生的方向向量代表一組需要旋轉在一個固定的位置,采用,所以只有位置用于確定面向任務的工作區(qū)。
3.2 計算的面向任務的工作區(qū)
面向任務的工作區(qū)可以由使用幾何的方法,提出了在前面的部分中。首先, 一組位置,采用的taskoriented作為候選人工作區(qū)是定義。為每一個位置,一個錐形的集所需的能力被定義為過程提出了在3.1節(jié)。在計算所需的活動關節(jié)值通過逆運動學為每個位置,限制活動關節(jié)中風是用來作為判據(jù)來確定位置在面向任務的工作區(qū)或不是。詳細的流程圖計算任務導向工作區(qū)顯示在圖7。
圖5。測量偏航螺距角焊在u形線通過使用組裝RRX4及其表示的長度在XY{ T0 }平面的投影。(一)焊接過程的一個標準塊模擬測量所需的旋轉角度。(b)測量的旋轉角度沿{ T0 }幀被表示為一個長度從原點通過余弦函數(shù)。
圖6。錐形幾何表示包括旋轉角度和計算過程;α和β表示增量的迭代循環(huán)。
計算任務導向的工作區(qū),幾個旋轉角度,顯示在圖8,其中每個圖形在平面上表示預測計算的面向任務的工作區(qū)。隨著需要旋轉能力增加,體積的面向任務的工作區(qū)卻降低了。面向任務的工作區(qū)35°的轉動能力,表示為紅色線。計算任務型工作空間相對大保證金與所需的900×800×工作區(qū)10毫米,因此有必要找出最佳的運動設計成本和重量參數(shù)效率。
4.結論
本文介紹了最優(yōu)設計的移動焊接機器人,RRX,通過任務型工作空間。所需的轉動角度探討了實驗研究沿著u型線的焊接。幾何方法使用一個錐形的單位來確定任務型工作空間提出基于運動分析的機器人,這樣可以執(zhí)行所需的旋轉。運動學變量,這樣會減少一個多目標函數(shù)組成的質量機及其設計的效率,取決于一個二級優(yōu)化程序。因此,大規(guī)模減少優(yōu)化設計是13%,和損失的設計效率是4.9%。從這個預計的重量RRX可以會減少。重新設計RRX4后,機器人可以應用在組裝線的船舶建造過程。擬議的優(yōu)化設計方法是將采用串行和并行機制的機器人。
參考文獻
[1] B.-O.金,Y.-B.全度妍,S.-B.金,運動控制兩輪焊接移動機器人焊縫跟蹤傳感器:PROC國際研討會工業(yè)工程,釜山,韓國,2001年,851-856.
[2] J.-H.李,J.-J.金,J.-K.金,J.-R.園區(qū)發(fā)展的馬車式焊接雙船體裝配生產(chǎn)線在造船,機器人:PROC:第17屆世界杯國際自動控制聯(lián)合會,首爾,韓國國會,2008年,4310-4311.
[3] J.H.李等人,機器人焊接系統(tǒng)用于面板塊組件玉浦船舶船體,技術46(2)(1998)32-40.
[4] T.宮崎造船,數(shù)控噴涂機器人,PROC化學研究所99,波士頓,美國,1999年,第1-14頁.
[5] M.無敵艦隊,P.岡薩雷斯·桑托斯,登山和步行機器人歐洲艦船設計短期課程,布雷斯特,法國海運業(yè),2002年,8-12.
[6] D.李某,李選,C.林,古北路,K.-Y.金,李,T. J.金,開發(fā)的移動工作中的雙殼結構的船舶,機器人的機器人系統(tǒng)計算機集成制造26(1)(2010年)13-23.
[7] NJ雅各布森,歐登塞鋼造船廠的焊接機器人,三代:PROC:中國科學院化學研究所,韓國釜山,2005年,289-300.
[8] R. Bostelman,A. Jacoff,束河,先進的雙體船交付焊接系統(tǒng)采用機器人,起重機,PROC:第三屆國際公務員制度委員會座談會智能工業(yè)自動化和軟計算,1999年,意大利熱那亞.
[9] J.阿蘭達,馬無敵艦隊,JM德拉克魯茲海事自動化工業(yè)ISBN:84-609-3315-6,2004年,143.
[10] X.-J.劉,王J.,H.-J.鄭,優(yōu)化設計5R對稱并聯(lián)用包圍和良好的條件的工作空間,機器人和機械手自治系統(tǒng)54(3)(2006)221-233.
[11] C.B.范,S.H.楊榮文,G.楊I.-M.陳完全內(nèi)斂,工作空間分析電纜驅動機器人,機器人和自主系統(tǒng)57(9)(2009)901-912.
[12] R.V.庫馬爾,K.J.沃爾德倫,工作區(qū)的機械手,期刊機械設計,ASME103(3)(1980)665-672.
[13] R.V.庫馬爾,K.J.沃爾德倫,MJ仔,幾何優(yōu)化的串行鏈操縱結構,工作容積和空調(diào),國際機器人研究5(2)(1986)91-103.
[14] F.-C.楊,E.J.豪格運動的工作能力,數(shù)值分析機制,機械設計雜志,ASME116(1994)111-118.
[15] E.J.豪格,C.-M.祿,F(xiàn).A.阿德金斯,J.-Y.次王,數(shù)值算法映射邊界的機械臂工作區(qū),機械設計雜志,ASME118(1996)228-234.
[16] ?G.T.池塘,J.A.卡雷特羅,定量比較靈活工作空間并聯(lián)機器人,機械工程學報42(2007)1388-1400.
[17] I.A。BONEV,J.劉某,六自由度方向工作區(qū)分析的新方法并聯(lián)機器人,機械工程學報36(2001)15-28.
[18] J.K.索爾茲伯里,J.J. Graig,鉸接式的手:力控制和運動學問題,國際機器人研究1(1)(1982年)4-17.
[19] T.吉川機器人機制的可操作性,國際期刊機器人研究4(1985)3-9.
[20] 斯托頓,T.的Kokkinis,一個新的運動結構的一些性質機器人:PROC:第13屆的ASME設計自動化會議,馬薩諸塞州的波士頓,1987年,73-79.
[21] G·E·福賽斯,馬馬爾科姆,CB莫勒,計算機數(shù)學方法計算,普倫蒂斯 - 霍爾,新澤西州Englewood Cliffs,1977年.
[22] Y.村,先進機器人:冗余和優(yōu)化,艾迪韋斯利,1991.
[23] F.撒迦利亞,C.博斯特,G.?Hitzinger,捕捉機器人工作區(qū)結構:代表機器人的能力:PROC:IEEE/RSJ國際機密。在英特爾。羅布。和系統(tǒng),美國加利福尼亞州圣迭戈,2007年,第3229-3236頁.
[24] ?R.M.穆雷,李正東,SS沙斯特里,機器人的數(shù)學簡介操縱,CRC出版社,1994.
[25] M.切卡萊利,工作區(qū)開鏈機械手,在分析和設計:PROC:AIP會議,蓋瑟斯堡,MD,USA,1998年,388-405.
[26] Z. Michalewicz M.舍瑙爾,用于約束的進化算法參數(shù)優(yōu)化問題,進化計算14(1)(1996)1-32.
[27] J.S.阿羅拉,優(yōu)化設計,愛思唯爾學術出版社,2004.
[28] Nocedal,S.J.賴特,數(shù)值優(yōu)化,1999年,斯普林格.
[29] 弗萊徹,C.M.的里夫斯,功能最小化共軛梯度,計算機雜志7(1)(1964)149-154.
[30] M.鮑威爾,重新啟動程序,共軛梯度法,數(shù)學編程12(1)(1977)241-254.
Optimal design and workspace analysis of a mobile welding robot with a 3P3R
serial manipulator
abstract
This paper presents the design optimization of a mobile welding robot based on the analysis of its workspace. A welding robot has been developed to be used inside the double-hull structure of ships, and it shows good welding functionality. But there is a need to optimize the kinematic variables ensuring that the required welding functions inside the ships are satisfied. The task-oriented workspace, which is the workspace enabling specific rotations, has been defined in order to validate the welding ability of the robot, and incorporating the required rotational capabilities. To calculate the workspace, a geometric approach is adopted which considers the pitching and yawing angles simultaneously. Based on the workspace analysis, a scenario is compiled for considering a mass reduction, and a ratio between the design parameters and the workspace, with constraints on the workspace margins. The proposed optimization procedure is composed of two steps of coarse and fine searching. In the coarse searching step, a feasible parameter region (FPR) is defined, which satisfies the geometrical design constraints, and can be obtained without any considerations of the objective functions. In the fine searching step, the design parameters are determined by using the optimization technique of the conjugate gradient method in the overall FPRs. The suggested approach to calculating the task-oriented workspace, and the procedure of optimal design, are expected to be applied to general industrial robots.
1. Introduction
1.1. Welding robots in ship-building industries
Over the last few decades, there have been a large number of attempts to automate welding in the shipbuilding process.Here, we would like to introduce the state of the art in welding robot systems. Table 1-A shows the intelligent mobile welding carriages. These carriages are composed of two (Table 1-A(a), [1]) or three (Table 1-A(b), [2]) prismatic (P) and two revolute (R) joints. They use differential driving wheels for positioning in the transverse direction. Thus, if a certain robust algorithm for high positioning accuracy does not exist, the differential driving cannot guarantee the straightness in repetitive multi-pass welding because of slippage. In the case of an open block, a multi-axis articulated robot can be placed into the open block by using overhead gantry cranes. DANDY [3], shown in Table 1-B, has been developed and
successfully used in the shipyard of Daewoo Shipbuilding and Marine Engineering Co. Ltd., Korea. After the robot finishes a single welding task, the robot is moved to the next welding location by using the overhead gantry crane installed in the ceiling of the shipyard. Since the overhead crane cannot approach the inside of the closed block, as shown in Fig. 1, the applicable area of the robot is limited to open blocks. Moreover, controllers are located at the outside of the open blocks, thus requiring a number of cables from the outside. This gives rise to difficulties in handling the several cables in the enclosed structures. There are also more examples of the currently available systems, which are a combination of a multi-axis robotic system with an overhead crane, as described in [7,8].
At this point, we would like to emphasize the importance of the embedded controller in the shipbuilding environment. During welding, an electric current is used to strike an arc between the base material and the consumable electrode rod. At that moment, it is known that, as the parts are welded, random movement of the electrons carrying the current occurs, and this affects the signal cables connecting the robots and the controllers. Moreover, there are a number of robots welding simultaneously in the same block. Thus, it can be thought that modularized controllers help to
Table 1 Several types of autonomous welding system.
prevent negative influences on the entire system from the various noises. Based on these facts that have been clarified so far, the design of an integrated system of a portable welding-only robot, having a modularized controller and auxiliary transportation devices, as a final alternative to a mobile robot working inside of
the enclosed structures has been encouraged.
Table 1-C(a) shows the numerically controlled (NC) painting robot, which has been developed by the Hitachi Zosen shipyard in Japan [4]. A 6-axis painting robot, together with a self-driving carriage, is placed inside the closed block using an expandable placer. However, this robotic system requires a large access hole of size 800 × 1600 mm2. Since the size of the access hole is related to ship-design safety regulations, any enlargement requires the permission of the ship’s owner, and is almost impossible to achieve. Another serious problem of this robotic painting system is that it cannot move freely in the transverse direction inside an enclosed block. The Industrial Automation Institute (IAI) in Spain has developed a robotic system called ROWER 1, that can be used in a closed block [5]; the robot moves like a spider, and has four legs capable of extending and contracting. It can move autonomously and can thus overcome many of the welding obstacles encountered in a closed block, but it has to be disassembled into seven modules before it can be placed into a closed block, and then reassembled in situ. Reassembly takes approximately 15 min, which is long
enough to seriously affect the productivity of the system [9].
The RRX platform of SNU [6], which overcomes all the disadvantages of the previous robots, has recently been established, and its performances of welding and mobile functions have been verified through field testing over a period of one year. However, points of note are that this system is still relatively hard to handle for placing in, and withdrawing from, the 500×700mm2 access hole, even though it satisfies the dimensional constraints. The main reason for this is its relatively large size compared to the size of human workers.
1.2. Manipulator optimization
Kinematic design has occupied an important position in robotic manipulator design because the performance of a system in terms of workspace, velocity, and accuracy is dominated by its geometrical characteristics. In particular, determination of the dimensions of the geometric parameters of a manipulator is primarily concerned by optimizing a nonlinear cost function, subject to a set of appropriate constraints. As criteria for judging a manipulator’s quality, there has been an increasing interest in the kinematic properties of a manipulator, such as workspace feature, conditioning index, and dexterity criteria.
1.2.1. Workspace
There has been much research to optimize the workspace of manipulators [10,11]. Kumar and Waldron [12] proposed
Fig. 1. Double-hulled ship wall.
an optimal design and analysis on reachable and dexterous workspaces, which was used for geometric optimization by Kumar et al. [13]. A reachable workspace is a position set of end-effectors in which an end-effector can reach without considering orientation, and a dexterous workspace is a position set of end-effectors in which an end-effector can reach with a full rotational capability. Haug et al. proposed a composite workspace that requires a specified working capability in joint space for all sets of points [14,15], and a Jacobian approach that determines the workspace boundary in terms of rank deficiency. Pond and Carretero also proposed a Jacobian approach that determines the workspace in terms of the condition number of the Jacobian matrix [16]. Bonev and Ryu proposed the orientation workspace: the set of all attainable orientations of an end-effector about a fixed point [17].
1.2.2. Conditioning and dexterity
On the other hand, various research on performance indices for evaluating the kinematic quality of the workspace has also been published over a long period. Salibury and Craig [18] used the condition number of the Jacobian matrix as an optimization criterion to evaluate the workspace quality. Yoshikawa [19] proposed the determinant of the Jacobian matrix as a measure of manipulability (MOM), whereas Stoughton and Kokkinis [20] used the minimum singular value and the condition number.
A point where special attention should be paid is that the previous concepts of the workspace are task independent: they do not guarantee the best manipulator for a specific task. Thus, task specificity of a direct consideration on the prescribed rotational capability of the end-effector represents good performance in determining the workspace boundary required in the specific tasks. And the MOM can be used as a mathematical tool to verify the distance from singularities, whereas the condition number can be used as a practical measure of the ill-conditioning [21] of the workspace and kinematic accuracy [22] of a manipulator over its whole workspace. Hence, the need for a manipulability measure will arise in this paper in terms of avoiding the likelihood of the singularity under a scaling of the manipulator dimensions.
1.3. Objective of the research
In this study, the task-oriented workspace and its partial workspace are crucial in efficiently obtaining the optimal design. Since we need only 35° of rotational capability to enable a U-shaped welding task, a task-oriented workspace (TOW) can be obtained by excluding useless orientations of the end-effector. Here, the TOW can be defined as a position set of the end-effector such that the end-effector can reach with a predefined rotational capability. Even if we only consider prescribed orientations in the end-effector space, workspace searching is still a time-consuming procedure. Thus, in order to reduce the computational cost, a partial workspace (PW), which can be considered as across-sectional area of the TOW, is proposed to calculate the distance between the TOW and the U-shaped welding part without exhaustively searching the possible position candidates in the full range of task-oriented workspace. Few studies on the proposed geometric treatments for the manipulator workspace were found in the literature; however, this topic seems to be a worthwhile subject to investigate, and should be a great help in the optimal design.
Using the proposed geometric treatments on the manipulator workspace, we simultaneously considered structural mass and design efficiency as objective functions with respect to maximizing the mass reduction and minimizing the loss of design efficiency. The design involves two steps: coarse and fine searches. In the coarse search step, we find feasible parameter regions (FPRs) where the predefined constraints are satisfied. In the find search step, we analyze the objective function in the FPRs to obtain the final optimal parameter set. The proposed two-step procedure simplifies the optimal design problem by separating the complicated constraints and the objective function.
A further important aspect of the optimal design is the manipulability measure, as discussed in Section 1.2. Actually, manipulability is only used to avoid singularity during the optimal design procedure. However, since manipulability is very important for determining the quality of a welding process, we independently analyze the manipulability at the end of this paper. Determining the optimal joint values, such as performed by Zacharias et al. [23], is also a remaining p