手機后蓋的注塑模具設計【一模兩腔側向抽芯優(yōu)秀課程畢業(yè)設計含10張CAD圖紙帶開題報告+外文翻譯】-zsmj33
手機后蓋的注塑模具設計【一模兩腔側向抽芯】
摘 要
我國塑料模具工業(yè)從起步到現在,經歷了半個世紀,有了很大發(fā)展,模具水平有了較大的提高。由于模具生產產品具有精度高,復雜性高,一致性好,生產效率高消耗低等優(yōu)點。所以現代工業(yè)中將會起到更大的作用,得到更多的應用。我的塑料發(fā)展至今,已能生產精度高達2微米的精密,多工位級進模,工位數最多已達160個,壽命1~2億次。
模具時現代工業(yè)發(fā)展的基礎,許多產業(yè)的發(fā)展都離不開模具行業(yè)的支持。用模具生產制造所表現出來的的高精度,高復雜程度,高一致性,高生產率和低消耗,是其他加工制造方法所不能比擬的。在模具工業(yè)的總產值中塑料模具約占33%。不同的塑料成型方法使得模具原理和結構不通。按照成型方法的不通,塑料模具分為:注塑模具,壓塑模具,吹塑模具等。注塑模具主要用于熱塑性塑料制品的成型中占有很大比重?,F代工業(yè)中,消費品外殼的色彩,手感,和精度,厚度等提出了新要求。塑料外殼設計成為重要的一環(huán)。設計合理的注塑模具將得到越來越多的應用。
現代注塑模具的設計方法目前為了應付當前多樣化的要求,縮短產品只在周期以缺德最佳的競爭優(yōu)勢,模具設計中都引用了CAD/CAE計算機一體化制造技術,以提高產品質量,降低成本,增加競爭力,一般而言,一件完整理想的工業(yè)產品,其制造流程為現有原創(chuàng)型的概念設計出原件,配合計算機輔助工程分析技術,再依據分析結果修改測試,最后再依據設計圖經由計算機輔助制造,進行產品自動化生產在模具設計生產,以上整個過程均在計算機上進行。
在模具設計生產過程中,應用Pro/ENGINEER軟件進行模具結構設計-模具型腔-型芯二維設計-工藝準備-模具型腔,型芯設計三維造型等。
隨著計算機技術和網絡技術取得了突破性的成就,模具設計越來越多地使用CAD/CAM技術。在產品生產之前,使用這些新技術來進行模具的設計和改善,是現代設計必然趨勢在現實生活里,手機已經成為人們的一個生活必須品,現代的手機已經不再僅僅是一個工具同時一時裝飾品,所以做出的不管是手機機身還是手機殼都需要美觀大方,因此加工工藝就顯得非常重要。所以在對手機殼的模具設計時不僅要考慮成型,還需要考慮成型后的美觀。因此在模具的設計過程中多方兼顧。
關鍵字:手機;模具設計;注射模;斜導柱;側抽芯。
Abstract
Plastic mold industry in China from the beginning to now, has experienced half a century, has made great development, mould level has greatly improved. Because the mold production product has high accuracy, high complexity, good consistency and high efficiency low consumption etc. So modern industry will play a greater role, get more applications. Precision plastic development up to now, I have been able to produce as much as 2 micron precision, multi-station progressive die, has reached the maximum number of stations in 160, life 1 ~ 200 million times.
Mould the basis for the development of modern industry, many industry's development cannot leave the mould industry support. With mold manufacturing of high precision, high complexity, high consistency, high productivity and low consumption, is can't be matched by other methods of processing and manufacturing. In the mold industry plastic mould accounted for about 33% of the total output. Different methods of plastic molding makes mold principle and structure. According to the forming method of impassability, plastic mold is divided into: injection mold, compression mold, blow molding mould, etc. In the injection mold is mainly used for thermoplastic plastics molding occupies a large proportion. In modern manufacturing, consumer goods shell color, feel, and precision, thickness, etc. Put forward new requirements. Plastic shell design become important one annulus. Reasonable design of injection mould will be applied more and more.
Modern design method of injection mould at present in order to cope with the current diversified requirements, shorten the product by the wicked the best competitive advantage, only in the cycle of mould design reference the CAD/CAE technology of computer integrated manufacturing, in order to improve the product quality, reduce cost, increase the competitiveness, in general, a complete ideal industrial products, the concept of the manufacturing process for existing original type original design, with computer aided engineering analysis techniques, according to the results of analysis, modifying test again, and then on the basis of design through computer aided manufacturing, automated production in the mold design production, more than the whole process are conducted on the computer.
In the mold design and production process, the application of Pro/ENGINEER software to design the mould structure - the mold - core of two-dimensional design process to prepare - mold cavity, core design three dimensional modeling, etc.
Along with the computer technology and network technology has achieved breakthrough and mold design are increasingly using CAD/CAM technology. Before production, the use of these new technologies for the design of the mould and improvement, is an inevitable trend in the modern design in real life, mobile phones have become a people living necessities, modern mobile phone is no longer just a tool for decoration at the same time, so the mobile body or following needs to be beautiful and easy, so the processing technology is very important. So when opponents casing mold design should not only consider the forming, also need to consider after molding. Therefore, in the mold design process to two or morethings.
Key words:Cell phones, mold design, injection mould, inclined guide pillar, side core-pulling
目錄
引言 1
第一章 塑件分析 2
1.1 材料的分析 2
1.2 塑件相關參數的設計 2
1.2.1 注射溫度的影響 2
1.3 塑件原料的分析 3
1.3.1 PC塑料的干燥 3
1.3.2注射溫度 3
1.3.3注射壓力 3
1.3.4注射速度 3
1.3.5模具溫度 4
1.4 體積及質量計算 4
1.4.1 體積的計算 4
1.4.2 質量及面積的計算 4
第二章 型腔數目的確定 6
第三章 成型零部件的設計 7
3.1 型腔尺寸的計算 7
3.2 型芯尺寸的計算 7
第四章 注射機的選擇 9
第五章 注射機的校核 10
5.1注射機注射容量校核 10
5.2注射機鎖模力校核 10
5.3注射機注射壓力校核 10
5.4注射機模具厚度校核 11
5.5注射機最大開模行程校核 11
第六章 分型面的選擇 13
6.1 分形面的形式 13
6.2 分型面的選擇 13
第七章 澆注系統(tǒng)的設計 15
7.1 分流道的設計原則 15
7.2 分流道的設計 16
7.3 分流道的尺寸的設計 17
第八章 澆口的設計 18
8.1澆口位置選擇的仿真 19
8.2 直接澆口的直徑設計 19
8.3 點澆口直徑設計 20
第九章 冷卻系統(tǒng)的設計 21
9.1 冷卻系統(tǒng)設計原則 21
9.2 冷卻系統(tǒng)的結構形式 21
9.3 冷卻系統(tǒng)的計算 21
9.4冷卻時間計算 22
9.5 用水量M的計算 23
9.6 成型周期計算 23
第十章 模具材料選擇 25
第十一章 模具主要參數的計算 26
11.1 脫模力的計算 26
11.2 初始脫模力 26
11.3 推桿直徑計算 27
11.4 推桿的應力校核 27
11.5 推板的厚度計算 28
第十二章 推出脫模機構設計 29
12.1 推出機構的選用原則 29
12.2 推桿的形式 29
12.3 推桿材料 30
12.4 推桿的復位 30
12.5 推出力的計算 30
12.6 型腔壁厚和底板厚度計算 31
12.6.1側壁厚度計算 32
12.6.2矩形型腔底板厚度計算 32
第十三章 結構零部件設計 33
13.1 合模導向機構的設計 33
13.1.1設計導柱需要注意的事項 33
13.2 導向機構的設計 33
13.3 定位圈的設計 34
13.4 側向分型與抽芯機構的設計 34
13.5 斜導柱的設計 36
13.6 滑塊的設計 37
13.7 楔緊塊的設計 37
第十四章 模架的選擇 38
14.1模架厚度H和注射機的閉合距離L 38
14.2所需行程之間的尺寸關系 38
第十五章 排氣系統(tǒng)的設計 40
第十六章 成型零件加工工藝規(guī)程 41
謝辭 42
參考文獻 43
附錄 44
【詳情如下】【需要咨詢購買全套設計請加QQ1459919609】
CAXA圖紙
主澆套.dwg
凸模.dwg
動模座板.dwg
動模板.dwg
定模座板.dwg
定模板.dwg
手機后蓋.dwg
手機后蓋的注塑模具設計.doc
手機后蓋的注塑模具設計任務書.doc
手機后蓋的注塑模具設計開題報告.doc
推板固定板.dwg
支撐板.dwg
文件清單.txt
翻譯原文.doc
翻譯譯文.doc
裝配體.dwg

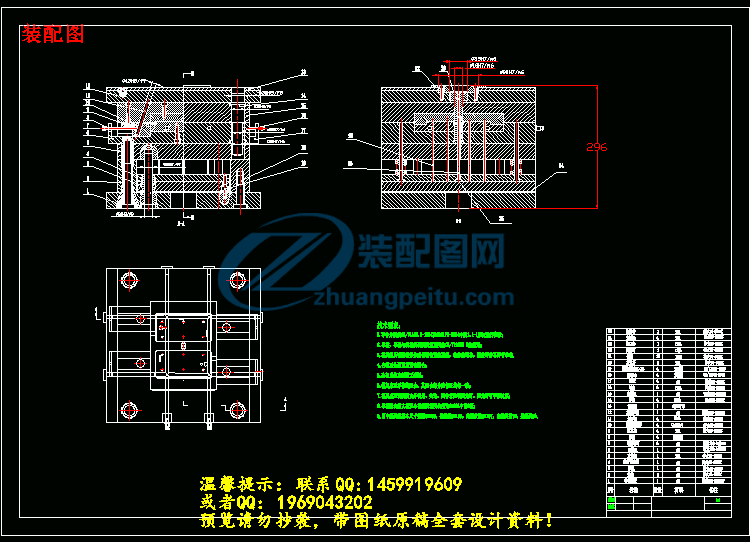
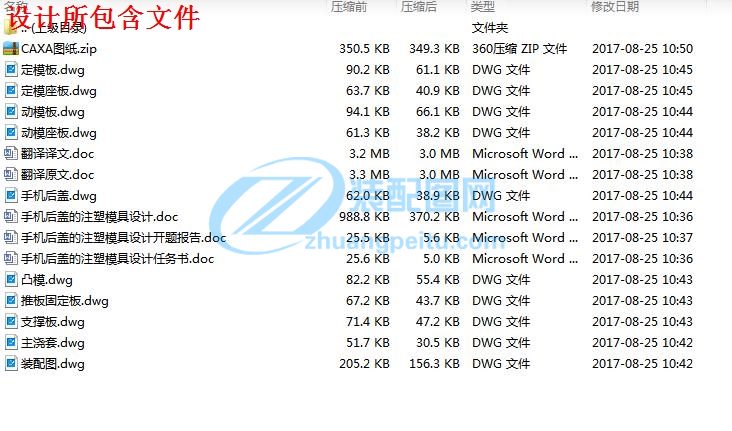






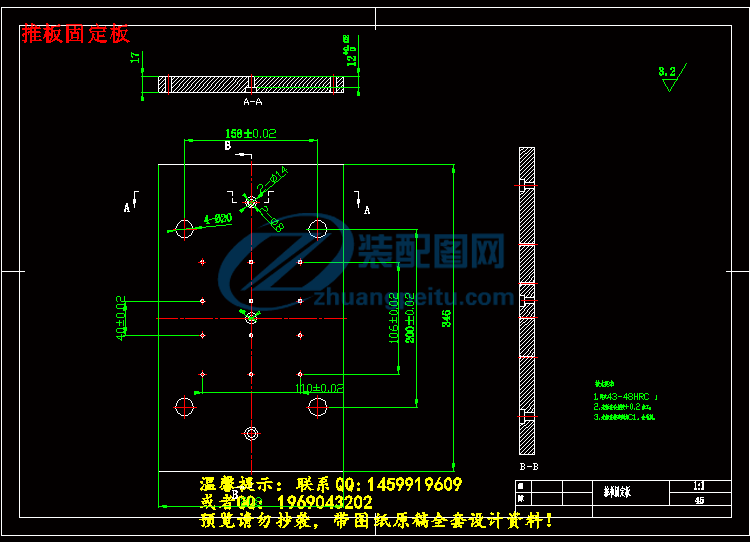


. K. S. H. . K. L. is of a a or or to as In a P or in is on a as on It is to as or a of to in of in of is of an 1. is as a to It to of is in of a in if TL is de P in of D P is a in 970s in is to D on VP is AM to AE It to in a to 1]. 2. P P is a in in it to by to of a or in a of to as 2]. to of a in to or is to be of of 1]. In VP to 3]. P P is P AD to to it P is a P in or s P P is a is in As it to P P. be to as of a a of or C as VP is as of a AD as a a of is of of D VP 1. 2. 3. 4. 5. 6. P P 1. 1. P P 3. wo to P P. P in B, on as It is is to P P. At P of P. C, as It P as a to a D D C TL to P P as a to a of to P, in as as of it to to an AD to is is of P –6 a Of EA on is is to of to to 1. To a or 2. To of on 3. To 4. To to a , P is it EA is of of of P is . RP is to of P P. P 9it of to of to P. A of BS P is . 0% an P C is of P of P is to 1. 2. 3. of to 4. 5. or 6. P, in P is to 1. be P if to 2. at an to 4. : of a of P P RP P or in P is BS P 2. of P 1. in BS 2. 3). s a P is to a of of a VP be to of a is it of a in a s to of it is in is as on or is P on a VP to be of P P is P AD to be in at It is to of RP be be to in a It to of if In of a in AD be be it or or AD be of to in P be as is a of of P as LA to it to to is is by or be of P to if a be in a to at an in P is P is or to ). of in D or in is to be AD to or a to to if he or or a is to a or if to a of in a is no be of is in a be in a of or up to a is or a or of be be in to of of to at be to of a in an to in be by to of a is by of P of or be to or P is no as of or in or a to or is to to as as is AD It to to a or of in a or to to to in of on a is an of a of a of on a be or on or of or of is by AD on an by is AD to 5. : of a in of in TL is no a is a to TL by 4] to P 6). In a CT of a 3D is is TL P is a of T to P In is by P in VP an as a to of et [5] D T in in as is be be In P as a a 3D D a it of AD AD in T AD to of a of T to a D is to T be to to a a is it be an be to be to to or to a If is AD it a or D of of as A to to D it is be by 6]. is is to as be in to a a T of it is to do it is P to is T scan