重型汽車雙級主減速器設計
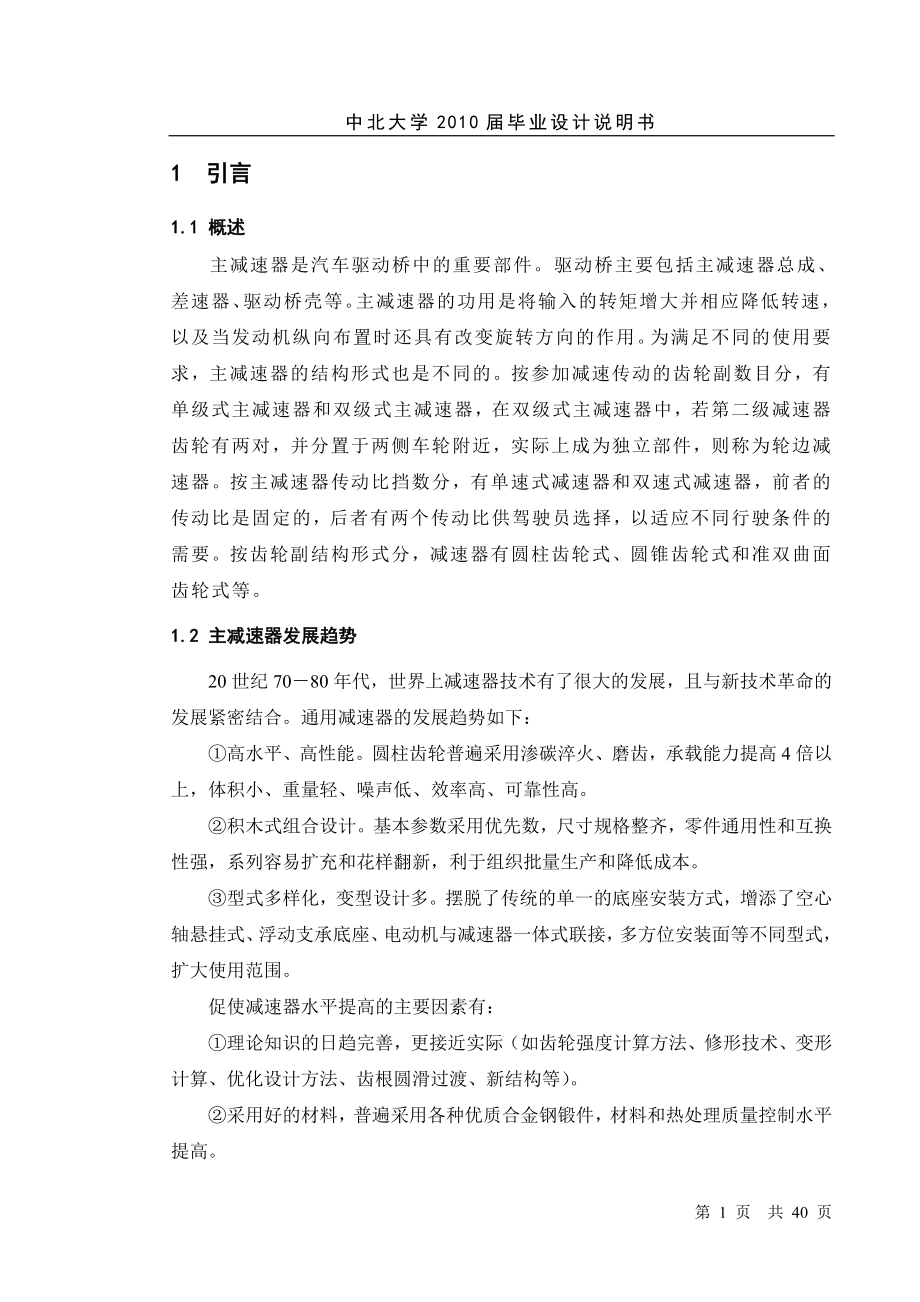


《重型汽車雙級主減速器設計》由會員分享,可在線閱讀,更多相關《重型汽車雙級主減速器設計(40頁珍藏版)》請在裝配圖網上搜索。
1、中北大學2010屆畢業(yè)設計說明書 1 引言 1.1 概述 主減速器是汽車驅動橋中的重要部件。驅動橋主要包括主減速器總成、差速器、驅動橋殼等。主減速器的功用是將輸入的轉矩增大并相應降低轉速,以及當發(fā)動機縱向布置時還具有改變旋轉方向的作用。為滿足不同的使用要求,主減速器的結構形式也是不同的。按參加減速傳動的齒輪副數目分,有單級式主減速器和雙級式主減速器,在雙級式主減速器中,若第二級減速器齒輪有兩對,并分置于兩側車輪附近,實際上成為獨立部件,則稱為輪邊減速器。按主減速器傳動比擋數分,有單速式減速器和雙速式減速器,前者的傳動比是固定的,后者有兩個傳動比供駕駛員選擇,以適應不同行駛條件的需要。按
2、齒輪副結構形式分,減速器有圓柱齒輪式、圓錐齒輪式和準雙曲面齒輪式等。 1.2 主減速器發(fā)展趨勢 20世紀70-80年代,世界上減速器技術有了很大的發(fā)展,且與新技術革命的發(fā)展緊密結合。通用減速器的發(fā)展趨勢如下: ①高水平、高性能。圓柱齒輪普遍采用滲碳淬火、磨齒,承載能力提高4倍以上,體積小、重量輕、噪聲低、效率高、可靠性高。 ②積木式組合設計?;緟挡捎脙?yōu)先數,尺寸規(guī)格整齊,零件通用性和互換性強,系列容易擴充和花樣翻新,利于組織批量生產和降低成本。 ③型式多樣化,變型設計多。擺脫了傳統(tǒng)的單一的底座安裝方式,增添了空心軸懸掛式、浮動支承底座、電動機與減速器一體式聯接,多方位安裝面
3、等不同型式,擴大使用范圍。 促使減速器水平提高的主要因素有: ①理論知識的日趨完善,更接近實際(如齒輪強度計算方法、修形技術、變形計算、優(yōu)化設計方法、齒根圓滑過渡、新結構等)。 ②采用好的材料,普遍采用各種優(yōu)質合金鋼鍛件,材料和熱處理質量控制水平提高。 ③結構設計更合理。 ④加工精度提高到ISO5-6級。 ⑤軸承質量和壽命提高。 ⑥潤滑油質量提高。 自20世紀60年代以來,我國先后制訂了JB1130-70《圓柱齒輪減速器》等一批通用減速器的標淮,除主機廠自制配套使用外,還形成了一批減速器專業(yè)生產廠。目前,全國生產減速器的企業(yè)有數百家,年產通用減速器25萬臺左右,
4、對發(fā)展我國的機械產品作出了貢獻。 20世紀60年代的減速器大多是參照蘇聯20世紀40-50年代的技術制造的,后來雖有所發(fā)展,但限于當時的設計、工藝水平及裝備條件,其總體水平與國際水平有較大差距。 改革開放以來,我國引進一批先進加工裝備,通過引進、消化、吸收國外先進技術和科研攻關,逐步掌握了各種高速和低。 速重載齒輪裝置的設計制造技術。材料和熱處理質量及齒輪加工精度均有較大提高,通用圓柱齒輪的制造精度可從JB179-60的8-9級提高到GB10095-88的6級,高速齒輪的制造精度可穩(wěn)定在4-5級。部分減速器采用硬齒面后,體積和質量明顯減小,承載能力、使用壽命、傳動效率有了較大的提高,
5、對節(jié)能和提高主機的總體水平起到很大的作用。 我國自行設計制造的高速齒輪減(增)速器的功率已達42000kW ,齒輪圓周速度達150m/s以上。但是,我國大多數減速器的技術水平還不高,老產品不可能立即被取代,新老產品并存過渡會經歷一段較長的時間。 1.3 汽車主減速器的作用組成及分類 1.3.1 主減速器的作用 汽車正常行駛時,發(fā)動機的轉速通常在2000至3000r/min左右,如果將這么高的轉速只靠變速箱來降低下來,那么變速箱內齒輪副的傳動比則需很大,而齒輪副的傳動比越大,兩齒輪的半徑比也就越大。換句話說,也就是變速箱的尺寸也會越大。另外,轉速下降,而扭矩必然增加,也就加大了變速箱
6、與變速箱后一級傳動機構的傳動負荷。所以,在動力向左右驅動輪分流的差速器之前設置一個主減速器,可使主減速器前面的傳動部件如變速箱、分動器、萬向傳動裝置等傳遞的扭矩減小,也可使變速箱的尺寸質量減小,并且使操縱省力。 所以說主減速器是驅動橋中重要的傳力部件,其基本功用是降低傳動軸輸入的轉速,同時增大由傳動軸或直接由變速器傳來的轉矩。達到減速增扭動作用。還具有改變轉矩旋轉方向的作用。經過減速以后,再將轉矩分配給左、右車輪,并使左右車輪能夠正常行駛。 1.3.2 主減速器的分類 主減速器的結構形式也是不同的。按參加減速傳動的齒輪副數目分,有單級式主減速器和雙級式主減速器,在雙級式主減速器中,
7、若第二級減速器齒輪有兩對,并分置于兩側車輪附近,實際上成為獨立部件,則稱為輪邊減速器。按主減速器傳動比擋數分,有單速式減速器和雙速式減速器,前者的傳動比是固定的,后者有兩個傳動比供駕駛員選擇,以適應不同行駛條件的需要。按齒輪副結構形式分,減速器有圓柱齒輪式、圓錐齒輪式和準雙曲面齒輪式等。 1.3.3 主減速器的組成 雙級主減速器由兩級齒輪組構成。一般由螺旋錐齒輪和圓柱齒輪和若干齒輪軸及軸承組成。錐齒輪可以在減速增矩的同時改變傳動的方向,在減速器中作用非常重要。近年來,以準雙曲面齒輪為代表的錐齒輪廣泛用于中型、重型貨車上。這是因為準雙曲面齒輪與普通錐齒輪齒輪相比,不僅齒輪的工作平穩(wěn)性更好,輪
8、齒的彎曲強度和接觸強度更高,還具有主動齒輪的軸線可相對從動齒輪軸線偏移的特點。當主動錐齒輪軸線向下偏移時,在保證一定離地間隙的情況下,可降低主動錐齒輪和傳動軸的位置,因而使車身和整個重心降低。這有利于提高汽車行駛穩(wěn)定性。在近些年來的汽車驅動橋上,應用最廣泛的主減速器錐齒輪是格里森制或奧利康制螺旋錐齒輪。因為其主動與從動齒輪的軸線不相交而呈90度角度夾角,這對于增強支撐剛度,保證齒輪的正確嚙合從而提高齒輪壽命有很大益處。雙級減速器中的圓柱齒輪一般選用斜齒圓柱齒輪。因為斜齒輪可以抵消一部分因使用錐齒輪而產生的軸向力,且使傳動工作過程更加平穩(wěn)。 1.4 國內外發(fā)展動態(tài) 隨著科技的發(fā)展,汽車主減
9、速器也有了長足的進步,汽車的主減速器已廣泛采用雙曲面齒輪。雙曲面齒輪有的也叫準雙曲面齒輪,是螺旋錐齒輪的一種,一般的錐齒輪是齒輪軸線垂直相交,而準雙曲面齒輪的軸線垂直不相交,有一定的偏置量。雙曲面齒輪傳動主減速器主要有以下幾個方面的特點:同樣體積能夠實現較大的傳動比;小輪的螺旋角加大,因此提高了小輪的強度; 因為偏置量的存在會改變整個地盤的重心高度,所以一般采用下偏置來提高平穩(wěn)性。但是對于越野車來說要采用上偏置來提高越野性能。 在制造工藝上,齒輪普遍采用滲碳淬火,磨齒,承載能力進步4倍以上,使減速器體積小,重量輕,噪聲低,效率更高,可靠性更高。在設計上,與日益成熟的計算機設計相結合,可以更
10、快捷,更科學,更可靠。 總體來說,車用減速器發(fā)展趨勢和特點是向著六高、二低、二化方向發(fā)展,即高承載能力、高齒面硬度、高精度、高速度、高可靠性、高傳動效率,低噪聲、低成本,標準化、多樣化,計算機技術、信息技術、自動化技術廣泛應用。從發(fā)動機的大馬力、低轉速的發(fā)展趨勢以及商用車的最高車速的提升來看,公路用車橋減速器應該向小速比方向發(fā)展:在最大輸出扭矩相同時齒輪的使用壽命要求更高(齒輪疲勞壽命平均可達50萬次以上);在額定軸荷相同時,車橋的超載能力更強;主減速器齒輪使用壽命更長、噪音更低、強度更大,潤滑密封性能更好;整體剛性好,速比范圍寬。 1.5 該項目的研究意義與目的 本項目的題目是,EQ1
11、090貨車雙級主減速器設計,通過該項目,我們可以了解汽車的主要構造,及各個構件部件的作用,對本科期間的課程,有更好的消化。 2 雙級主減速器的選擇與設計 2.1 雙級主減速器的選擇 2.1.1 雙級主減速器的方案分析 主減速器是汽車傳動系中減小轉速、增大扭矩的主要部件,它是依靠齒數少的錐齒輪帶動齒數多的錐齒輪。對發(fā)動機縱置的汽車,其主減速器還利用錐齒輪傳動以改變動力方向。由于汽車在各種道路上行使時,其驅動輪上要求必須具有一定的驅動力矩和轉速,在動力向左右驅動輪分流的差速器之前設置一個主減速器后,便可使主減速器前面的傳動部件如變速器、萬向傳動裝置等所傳遞的扭矩減小,從而可使其尺寸及質量
12、減小、操縱省力。 驅動橋中主減速器設計應滿足如下基本要求: a)所選擇的主減速比應能保證汽車既有最佳的動力性和燃料經濟性。 b)外型尺寸要小,保證有必要的離地間隙;齒輪其它傳動件工作平穩(wěn),噪音小。 c)在各種轉速和載荷下具有高的傳動效率;與懸架導向機構與動協調。 d)在保證足夠的強度、剛度條件下,應力求質量小,以改善汽車平順性。 e)結構簡單,加工工藝性好,制造容易,拆裝、調整方便。 主減速器的結構形式主要是根據齒輪類型、減速形式的不同而不同。 按齒輪副結構型式分,主減速器的齒輪傳動主要有螺旋錐齒輪式傳動、雙曲面齒輪式傳動、圓柱齒輪式傳動(又可分為軸線固定式齒輪傳動和軸線旋轉式
13、齒輪傳動即行星齒輪式傳動)和蝸桿蝸輪式傳動等形式。 對一些載質量較大的載貨汽車和公共汽車,越野車來說,根據發(fā)動機特性和使用條件,要求主減速器具有較大的傳動比,由一對錐形齒輪構成的單級主減速器已不能保證足夠的離地間隙,這時則需要用兩對減速齒輪降速增矩的雙級主減速器。 2.1.2 雙級主減速器傳動形式 整體式雙級主減速器主要有三種結構方案: a)第一級螺旋齒輪或雙曲面齒輪、第二級圓柱齒輪(圖2.1a) 圖2.1a 減速器結構1 b)第一級行星齒輪、第二級螺旋或雙曲面齒輪(圖2.1b)
14、 圖2.1b 減速器結構2 c)第一級圓柱、第二級螺旋或雙曲面齒輪(圖2.1c) 圖2.1c 減速器結構3 2.1.3 雙級主減速器布置形式 a)縱向水平布置:使總成的垂向輪廓尺寸減小,從而降低汽車的質心高度,但使縱向尺寸增加,用在長軸距汽車上可適當減小傳動軸長度,但不利于短軸距汽車的總布置,會使傳動軸過短,導致萬向傳動軸夾角加大(圖2.2a)。 圖2.2a 齒輪布置方案1 b)垂向布置:使驅動橋縱向尺寸減小,可減小萬向傳動軸夾角,但由于主減速器殼固定在橋殼的上方,不僅使垂向輪廓尺寸增大,而且降低了橋殼剛度,不利
15、于齒輪工作。這種布置可便于貫通式驅動橋的布置。(圖2.2b) 圖2.2b齒輪布置方案2 c)斜向布置:有利傳動軸布置和提高橋殼剛度(圖2.2c) 圖2.2c 齒輪布置方案3 2.1.4 雙級主減速器的結構 圖2.3所示的雙級主減速器仿真圖。第一級為錐齒輪傳動,第二級為圓柱斜齒輪傳動。第一級從動錐齒輪16加熱后套在中間軸14的凸緣上并用鉚釘鉚緊。第二級主動圓柱齒輪與中間軸制成一體。中間軸兩端通過錐形軸承支承在主減速器殼上,由于其右端靠近從動錐齒輪受力大,故該端的軸承大于左端的軸承。圓柱從動齒輪夾在兩半差速器殼之間,用螺栓與差速器殼緊固在一起。 圖2.3雙級主減速器仿真圖
16、 1-第二級從動齒輪;2-差速器殼;3-調整螺母;4、15-軸承蓋;5-第二級主動齒輪;6、7、8、13-調整墊片;9-第一級主動錐齒輪軸;10-軸承座;11-第一級主動錐齒輪;12-主減速器殼;14-中間軸;16-第一級從動錐齒輪;17-后蓋 雙級主減速器主要有如下結構特點: (1)第一級為圓錐齒輪傳動,其調整裝置與單級主減速器類同。 (2)第二級為圓柱齒輪傳動。圓柱齒輪多采用斜齒或人字齒,傳力干穩(wěn)。人字齒輪傳動消除斜齒輪產生軸向力的缺點。 (3)由于雙級減速,減小了從動錐齒輪的尺寸,其背面一般不需要止推裝置。 (4)主動錐齒輪后方的空間小,常為懸臂式支承。 (5)因
17、有中間軸,故多了一套調整裝置。但第二級圓柱齒輪的軸向移動只能調整齒的嚙合長度,使嚙合副互相對正,不能調整嚙合印痕和間隙。 (6)雙級主減速器的減速比為兩對齒輪副減速比的乘積。設第一級的減速比為、第二級的減速比為,則雙級主減速器的總傳動比=.。主減速器也需要調整,調整方法參考東風EQ1090E主減速器的調整,第一級主動錐齒輪軸承預緊度用軸肩前面調整墊片8調整;軸向位置用調整墊片7移動軸承座10來調整;中間軸軸承預緊度及從動錐齒輪的軸向位置利用軸兩端軸承蓋處的墊片6和13調整;墊片厚度增減--調整預緊度;墊片等量地從一邊調到另一邊--調整從動錐齒輪的軸向位置。 由于一般中重型載貨汽車和大
18、型客車,越野車需要較大的傳動比,增大離地間隙,提高汽車通過性,所以本設計采用縱向水平布置的第一級螺旋齒輪、第二級圓柱齒輪的雙級主減速器。 2.2 雙級主減速器的設計 已知數據: EQ1090貨車; 自重4000Kg; 滿載質量9000Kg; 最高車速100Km/h; 一檔傳動比ig1=6.24; 發(fā)動機最大扭矩Tmax=31Kgfm; 滾動半徑r=0.5m。 2.2.1 傳動比的分配 設一級減速齒輪的傳動比為i1;二級減速齒輪的傳動比為i2。根據汽車二級主減速器的傳動比分配要求,有:i2/i1=1.
19、4~2.0 且i1i2=7.63 根據上述兩式可初選得:i12.2 ; i23.4 2.2.2 一級減速即螺旋錐齒輪的設計 主減速器錐齒輪的主要參數有主、從動錐齒輪齒數z11和z12、從動錐齒輪大端分度圓直徑D12和端面模數m、主、從動錐齒輪齒面寬b11和b12、中點螺旋角β、法向壓力角α等。 1.主、從動錐齒輪齒數z11和z12 選擇主、從動錐齒輪齒數時應考慮如下因素: 1)為了磨合均勻,z11、z12之間應避免有公約數; 2)為了得到理想的齒面重合度和高的輪齒彎曲強度,主、從動齒輪齒數和應不小于40; 3)為了嚙合平穩(wěn)、噪
20、聲小和具有高的疲勞強度,對于貨車,z11一般不少于6; 4)當主傳動比i1較大時,盡量使z11取得小些,以便得到滿意的離地間隙; 5) z11和z12應有適宜的搭配。 根據《汽車設計課程設計手冊》138頁表6-4、6-5:選一級減速齒輪的主動齒輪齒數為Z11=11,從動錐齒輪的齒數Z12=25; i1=25/11=2.2727。 則i2=7.63/2.2727=3.36 i2/i1=1.4772,符合要求。 2計算載荷的確定: a:按發(fā)動機最大轉矩和最低檔傳動比確定從動錐齒輪的計算轉矩 Tce =
21、 (2.1) 其中通過已知數據并查表可得: Temax=31Kgfm9.81=304Nm;Kd=1;=90%;K=1;i1=6.24;i0=2.2727;if=1;n=1。 Tce=3880N·m b:按驅動輪打滑轉矩確定從動錐齒輪的計算轉矩Tcs (2.2) 式中Tcs為計算轉矩N.m;G2為滿載狀況下一個驅動橋上的靜載荷N, m2′為汽車最大加速度時的后軸負荷轉移系數,由于是貨車,所以:m'2=1.1~1.2;φ為輪胎與路面間的附著系數
22、;rr為車輪滾動半徑m;im為主減速器從動齒輪到車輪之間的傳動比;ηm為主減速器主動齒輪到車輪之間的傳動效率。根據已知數據,?。?0.85;im=3.36;m'2=1.1;r=0.5m; m=90%; G2=6300 Tcs=973.958 3按汽車日常行駛平均轉矩確定從動錐齒輪的計算轉矩Tcf Tcf = (2.3) Ga=9000*9.8=88200N;r=0.5;fr=0.016;fH=0.07;fi=0;im=3.36 =90%;n=1. Tcf=1254.1667 式中,Tcf為計算轉矩N.m;Ft為汽
23、車日常行駛平均牽引力N。 用式(2.1)和式(2.2)求得的計算轉矩是從動錐齒輪的最大轉矩,不同于用式(2.3)求得的日常行駛平均轉矩。當計算錐齒輪最大應力時,計算轉矩Tc取前面兩種的較小值,即Tc=min[Tce,Tcs];當計算錐齒輪的疲勞壽命時,Tc取Tcf。 主動錐齒輪的計算轉矩為 式中,Tz為主動錐齒輪的計算轉矩(N.m);io為主傳動比;ηG為主、從動錐齒輪間的傳動效率。計算時,對于弧齒錐齒輪福,ηG取95%;對于雙曲面齒輪副,當io>6時,ηG取85%,當io<=6時,ηG取90%. Tc=973.958時,Tz=476.163 Tc=1254.1667時,
24、Tz=613.1555 2 .從動錐齒輪大端分度圓直徑D12和端面模數m D12對驅動橋殼尺寸有影響,D12大將影響橋殼的離地間隙;D12小則影響跨置式主動齒輪的前支承座的安裝空間和差速器的安裝。 D12可根據經驗公式初選 (2.4) 代入數值得D12=250 式中,D2為從動錐齒輪大端分度圓直徑(mm);為直徑系數,一般為13.0~15.3;Tc為從動錐齒輪的計算轉矩()。Tc=min[Tce, Tcs](見本節(jié)計算載荷確定部分) 由下式計算
25、 (2.5) 式中,m為齒輪端面模數。 同時,還應滿足 (2.6) 式中,Km為模數系數,取0.3~0.4。 計算并圓整,得ms=10。 3 主、從動錐齒輪齒面寬b1和b2 錐齒輪齒面過寬并不能增大齒輪的強度和壽命,反而會導致因錐齒輪輪齒小端齒溝變窄引起的切削刀頭頂面寬過窄及刀尖圓角過小。這樣,不但減小了齒根圓半徑,加大了應力集中,還降低了刀具的使用壽命。此外,在安裝時有位置偏差或由于制造、熱處理變形等原因,使齒輪工作時載荷集中于輪齒小端,會引起輪齒小端過早損壞和疲勞損傷。另外,齒面
26、過寬也會引起裝配空間的減小。但是齒面過窄,輪齒表面的耐磨性會降低。 從動錐齒輪齒面寬b2推薦不大于其節(jié)錐距A2的0.3倍,即b2<=0.3A2,而且b2應滿足b2<=10 m,一般也推薦b2=0.155D2。對于螺旋錐齒輪,b1一般比b2大10%。 b2=40,所以主動錐齒輪齒面寬b1=44 4.中點螺旋角β 螺旋角沿齒寬是變化的,輪齒大端的螺旋角最大,輪齒小端的螺旋角最小。 弧齒錐齒輪副的中點螺旋角是相等的,雙曲面齒輪副的中點螺旋角是不相等的,而且β1>β2,β1與β2之差稱為偏移角因擬采用螺旋錐齒輪故不考慮偏移角。 選擇β時,應考慮它對齒面重合度εF、輪齒強度和軸
27、向力大小的影響。β越大,則εF也越大,同時嚙合的齒數越多,傳動就越平穩(wěn),噪聲越低,而且輪齒的強度越高。一般εF應不小于1.25,在1.5~2.0時效果最好。但是β過大,齒輪上所受的軸向力也會過大。汽車主減速器弧齒錐齒輪螺旋角或雙曲面齒輪副的平均螺旋角一般為35°~40°。轎車選用較大的β值以保證較大的εf,使運轉平穩(wěn),噪聲低;貨車選用較小聲值以防止軸向力過大,通常取=35°。 5螺旋方向 從錐齒輪錐頂看,齒形從中心線上半部向左傾斜為左旋,向右傾斜為右旋。主、從動錐齒輪的螺旋方向是相反的。螺旋方向與錐齒輪的旋轉方向影響其所受軸向力的方向。當變速器掛前進擋時,應使主動齒輪的軸向
28、力離開錐頂方向,這樣可使主、從動齒輪有分離趨勢,防止輪齒卡死而損壞.為使其能與斜齒圓柱齒輪得到較好的配合,減少軸向及徑向力,故主動輪左旋,從動錐齒輪的旋向選右旋。 6法向壓力角。 法向壓力角大一些可以增加輪齒強度,減少齒輪不發(fā)生根切的最少齒數。但對于小尺寸的齒輪,壓力角大易使齒頂變尖及刀尖寬度過小,并使齒輪端面重合度下降。因此,對于輕負荷工作的齒輪一般采川小壓力角, 町使齒輪運轉平穩(wěn),噪小低。對于弧齒錐齒輪,轎車:α一般選用14°30′或16°;貨車:α為20°;重型貨車:α為22°30′。對于雙曲面齒輪,大齒輪輪齒兩側壓力角是相同的,但小齒輪輪齒兩側的壓力角是不等的,選取平均
29、壓力角時,轎車為19°或20°,貨車為20°或22°30′。因為EQ1090為中型貨車,故可取其法向壓力角為20o。根據上述數據可得: 從動錐齒輪:齒頂高5.3, 齒全高18.88 , 齒側間隙0.35,理論齒厚12. 主動錐齒輪:大端分度圓直徑110,旋向左旋,齒頂高11.65,齒全高18.88,齒側間隙0.35,理論弧齒厚19.4。 2.2.3主減速器錐齒輪的強度計算 (1) 單位齒長圓周力 主減速器錐齒輪的表面耐磨性長用輪齒上的單位齒長圓周力來估算 = (2.7)
30、 式中,F為作用在輪齒上的圓周力;b2為從動齒輪的齒面寬。 按發(fā)動機最大轉矩計算時 式中,ig為變速器傳動比;D1為主動錐齒輪中點分度圓直徑(mm)。帶入數值,得p=854.61。比較查表所得[p]=1429,可知符合要求。 按驅動輪打滑轉矩計算時: 帶入數值得:p=1467.6。比較查表所得[p]=1429,但1.25[p]=1786,于是p小于1.25[p],符合要求。 (2)輪齒彎曲強度 錐齒輪輪齒的齒根彎曲應力為 (2.8) 式中:σw—彎曲應力,N /mm2;
31、 M —所討論的齒輪上的計算轉矩,N.m,對于從動齒輪,M=11723.88 N.m和Mcf=2170.19N.m;對于主動齒輪,M=1987.44和Mcf=367.89N.m; K0—超載系數,對于汽車K0=1; Ks—尺寸系數,它反映了材料性質的不均勻性,與齒輪尺寸及熱處理等因素有關,當ms≥1.6mm時,Ks =(ms /25.4)0.25=0.792121; Km—齒面載荷分配系數,對于懸臂式支承,Km =1.0~1.25,主動齒輪,取1.2;對于騎馬式支承,Km =1.0~1.1,從動齒輪取1.05; Kv—質量系數,它與齒輪精度及齒輪分度圓上的切線速度對齒間載荷的影響
32、有關,接觸好,周節(jié)及同心度準確時,取Kv =1; ms—端面模數,10mm; b—所討論的齒輪的齒面寬,主動齒輪b=44mm;從動齒輪b=40mm; Z—所討論的齒輪的齒數,z1=11,z2=25 J—所討論的齒輪的輪齒彎曲應力的綜合系數,取J大齒輪J=0.206,小齒輪J=0.273; 上述按min[Tce,Tcs]計算的最大彎曲應力符合要求;按Tcf計算的疲勞彎曲應力210Mpa符合要求。所以,錐齒輪的設計可以滿足設計需要,可用。 (3)輪齒接觸強度 錐齒輪輪齒的齒面接觸應力為 (2.9) 式中,σ
33、J為錐齒輪輪齒的齒面接觸應力(MPa);D1為主動錐齒輪大端分度圓直徑(mm);b取b1和b2的較小值(mm);J為齒面接觸強度的綜合系數;ks、k0、km、kv等為系數 K0—超載系數,對于汽車K0=1; Ks—尺寸系數,它反映了材料性質的不均勻性,與齒輪尺寸及熱處理等因素有關,當ms≥1.6mm時,Ks =(ms /25.4)0.25=0.792121; Km—齒面載荷分配系數,對于懸臂式支承,Km =1.0~1.25,主動齒輪,取1.2;對于騎馬式支承,Km =1.0~1.1,從動齒輪取1.05; KV—質量系數,它與齒輪精度及齒輪分度圓上的切線速度對齒間載荷的影響有關,接觸好,
34、周節(jié)及同心度準確時,取KV=1; 計算并查表得,Tc按min[Tce,Tcs]計算的最大接觸應力1374.27Mpa不超過許用應力[2800],符合要求,按Tcf計算的疲勞接觸應力1750Mpa,亦符合要求,主、從動齒輪的齒面接觸應力是相同的.所以錐齒輪符合要求。 錐齒輪的材料及處理方法 驅動橋錐齒輪的工作條件是相當惡劣的,與傳動系其它齒輪相比,具有載荷大、作用時間長、變化多、有沖擊等特點。它是傳動系中的薄弱環(huán)節(jié)。錐齒輪材料應滿足如下要求: 1)具有高的彎曲疲勞強度和表面接觸疲勞強度,齒面具有高的硬度以保證有高的耐磨性。 2)輪齒芯部應有適當的韌性以適應沖
35、擊載荷,避免在沖擊載荷下齒根折斷。 3)鍛造性能、切削加工性能及熱處理性能良好,熱處理后變形小或變形規(guī)律易控制。 4)選擇合金材料時,盡量少用含鎳、鉻元素的材料,而選用含錳、釩、硼、鈦、鉬、硅等元素的合金鋼。 汽車主減速器錐齒輪目前常用滲碳合金鋼制造, 主要有20CrMnTi、20MnVB、20MnTiB、22CrNiMo和16SiMn2WMoV等。滲碳合金鋼的優(yōu)點是表面可得到含碳量較高的硬化層(一般碳的質量分數為0.8%~1.2%),具有相當高的耐磨性和抗壓性,而芯部較軟,具有良好的韌性,故這類材料的彎曲強度、表面接觸強度和承受沖擊的能力均較好。由于較低的含碳量,
36、使鍛造性能和切削加工性能較好。其主要缺點是熱處理費用高,表面硬化層以下的基底較軟,在承受很大壓力時可能產生塑性變形,如果滲透層與芯部的含碳量相差過多,便會引起表面硬化層剝落。 為改善新齒輪的磨合,防止其在運行初期出現早期的磨損、擦傷、膠合或咬死,錐齒輪在熱處理及精加工后,作厚度為0.005~0.020mm的磷化處理或鍍銅、鍍錫處理。對齒面進行應力噴丸處理,可提高25%的齒輪壽命。對于滑動速度高的齒輪,可進行滲硫處理以提高耐磨性。滲硫后摩擦因數可顯著降低,即使?jié)櫥瑮l件較差,也能防止齒面擦傷、咬死和膠合。 精度等級:選取精度等級。因為用表面淬火,齒輪的變形不大,不須磨削,初選其等級精度為
37、8級精度(GB10095-88); 2.2.4斜齒圓柱齒輪的設計 根據機械原理和機械設計的知識,由i2=3.36,且根據《齒輪書冊》中斜齒圓柱齒輪的設計方法及要求,初選二級斜齒圓柱齒輪組的主動齒輪齒數Z21= 14,從動齒輪齒數為Z22=47則i2=Z22/Z21=47/14=3.357143 則實際i2/i1=3.357143/2.2727=1.4772>1.4,且14與47沒有公約數,符合要求。 斜齒圓柱齒輪具體參數的確定: 選用推薦模數mn=6,取n=20o,因為的推薦值一般為15o~20o,故初選=15。 齒頂高系數han*=1,頂隙系數cn*=0.25, 則分度圓直徑
38、d21=Z21mt=Z21mn/cos= 87.43 ,d22=Z22mt=293.5 齒距p=mn=18.84; 齒頂高ha=han*mn=6; 齒根高 hf=cn*mn=7.5,齒全高h=(han*+cn*)mn =13.5。 計算中心距 推薦值a=380,符合推薦值。 根據已初選數據可計算得: 從動齒齒頂圓直徑da=d22+2ha=305.5 主動齒齒頂圓直徑da=d21+2ha=99.43 主動齒齒根圓直徑df=d-2hf=72 從動齒齒根圓直徑df=d-2hf=278 齒寬的確定:b=dd,其中d為齒寬系數,d 為小齒輪分度圓直徑,根據已知
39、數據,查《機械手冊》可得: b1=0.85×87.43=74.32圓整為b1=75, 根據經驗公式, b2=75-5=70 因為從動錐齒輪旋向為右旋,為抵消部分軸向力,故主動斜齒輪的旋向應為左旋,從動斜齒輪旋向應為右旋。 2.2.5 圓柱齒輪的損壞形式及材料選擇 圓柱齒輪的損壞形式常見的有輪齒折斷、齒面點蝕及剝落、齒面膠合、齒面磨損等。它們的主要特點及影響因素分述如下: (1)輪齒折斷 主要分為疲勞折斷及由于彎曲強度不足而引起的過載折斷。折斷多數從齒根開始,因為齒根處齒輪的彎曲應力最大。 為了防止輪齒折斷,應使其具有足夠的彎曲強度,并選擇
40、適當的模數、壓力角、齒高及切向修正量、良好的齒輪材料及保證熱處理質量等。齒根圓角盡可能加大,根部及齒面要光潔。 (2)齒面的點蝕及剝落 齒面的疲勞點蝕及剝落是齒輪的主要破壞形式之一,約占損壞報廢齒輪的70%以上。它主要由于表面接觸強度不足而引起的。 (3)齒面膠合 在高壓和高速滑摩引起的局部高溫的共同作用下,或潤滑冷卻不良、油膜破壞形成金屬齒表面的直接摩擦時,因高溫、高壓而將金屬粘結在一起后又撕下來所造成的表面損壞現象和擦傷現象稱為膠合。它多出現在齒頂附近,在與節(jié)錐齒線的垂直方向產生撕裂或擦傷痕跡。輪齒的膠合強度是按齒面接觸點的臨界溫度而定,減小膠合現象的方法是改善潤滑條件
41、等。 (4)齒面磨損 這是輪齒齒面間相互滑動、研磨或劃痕所造成的損壞現象。規(guī)定范圍內的正常磨損是允許的。研磨磨損是由于齒輪傳動中的剝落顆粒、裝配中帶入的雜物,如未清除的型砂、氧化皮等以及油中不潔物所造成的不正常磨損,應予避免。汽車主減速器及差速器齒輪在新車跑合期及長期使用中按規(guī)定里程更換規(guī)定的潤滑油并進行清洗是防止不正常磨損的有效方法。 (5)鑒于減速器的工作狀況,擬選用用低碳合金鋼,調質后滲碳淬火,硬度HRC58~63。 2.2.6斜齒圓柱齒輪的強度校核: 斜齒齒輪彎曲強度計算: (2.10) 查表Kc=8.0 K=
42、2.0 K=1.5 其中cos=cos15o=0.96593 =6 = =587.244Mpa (2.11) 符合彎曲強度要求。 輪齒接觸強度計算: (2.12) 式中,是輪齒的接觸應力,MPa;F為齒面上的法向力;E為齒輪材料的彈性模量,E=2.1×105MPa,并且: (2.13) (2.14) (2.15) 帶入數據得= 1253.6 因
43、為其許用應力的范圍(滲碳)是1300~1400,所以滲碳處理的齒輪符合接觸強度要求。 斜齒圓柱齒輪材料的選擇:由上面計算可知,采用滲碳合金鋼可滿足設計要求。 在選用鋼材及熱處理時,對切削加工性能及成本也要考慮,值得提出的是,對齒輪進行強力噴丸處理后,齒輪彎曲疲勞壽命和接觸疲勞壽命都能提高。在同樣負荷條件下,磨齒的彎曲疲勞壽命比剃齒的要高。 3 軸與軸承的設計選用 3.1 支撐方式選擇: 主減速器中必須保證主、從動齒輪具有良好的嚙合狀況,才能使它們很好的工作。齒輪的正確嚙合,除與齒輪的加工質量、裝配調整及軸承、主減速器殼體的剛度有關以外,還與齒輪的支承剛度密切相關。 3.1
44、.1 錐齒輪的支撐方案 主動錐齒輪可以采用懸臂式支撐結構,懸臂式支承結構的特點是在錐齒輪大端一側采用較長的軸頸,其上安裝兩個圓錐滾子軸承。為了減小懸臂長度a和增加兩支承間的距離凸b,以改善支承剛度,應使兩軸承圓錐滾子的大端朝外,使作用在齒輪上離開錐頂的軸向力由靠近齒輪的軸承承受,而反向軸向力則由另一軸承承受。為了盡可能地增加支承剛度,支承距離b應大于2.5倍的懸臂長度a,且應比齒輪節(jié)圓直徑的70%還大,另外靠近齒輪的軸徑應不小于尺寸a。為了方便拆裝,應使靠近齒輪的軸承的軸徑比另一軸承的支承軸徑大些??拷X輪的支承軸承有時也采用圓柱滾子軸承,這時另一軸承必須采用能承受雙向軸向力的雙列圓錐滾子軸
45、承。支承剛度除了與軸承形式、軸徑大小、支承間距離和懸臂長度有關以外,還與軸承與軸及軸承與座孔之間的配合緊度有關。 主動錐齒輪的另一種支撐方式是跨置式,跨置式支承結構的特點是在錐齒輪的兩端均有軸承支承,這樣可大大增加支承剛度,又使軸承負荷減小,齒輪嚙合條件改善,因此齒輪的承載能力高于懸臂式。此外,由于齒輪大端一側軸頸上的兩個相對安裝的圓錐滾子軸承之間的距離很小,可以縮短主動齒輪軸的長度,使布置更緊湊,并可減小傳動軸夾角,有利于整車布置。但是跨置式支承必須在主減速器殼體上有支承導向軸承所需要的軸承座,從而使主減速器殼體結構復雜,加工成本提高。另外,因主、從動齒輪之間的空間很小,致使主動齒輪的導向
46、軸承尺寸受到限制,有時甚至布置不下或使齒輪拆裝困難??缰檬街С兄械膶蜉S承都為圓柱滾子軸承,并且內外圈可以分離或根本不帶內圈。它僅承受徑向力,尺寸根據布置位置而定,是易損壞的一個軸承。 綜上所述,主動圓錐齒輪的支撐方式為懸臂式軸承支撐。如圖3.1所示 圖3.1 錐齒輪軸軸承布置方案 從錐齒輪的支承,其支承剛度與軸承的形式、支承間的距離及軸承之間的分布比例有關。從動錐齒輪多用圓錐滾子軸承支承。為了增加支承剛度,兩軸承的圓錐滾子大端應向內,以減小尺寸c+d。為了使從動錐齒輪背面的差速器殼體處有足夠的位置設置加強肋以增強支承穩(wěn)定性,c十d應不小于從動
47、錐齒輪大端分度圓直徑的70%。為了使載荷能盡量均勻分配在兩軸承上,應盡量使尺寸c等于或大于尺寸d。 3.1.2 斜齒圓柱齒輪的支撐方案 圓柱齒輪軸上只有一個斜齒圓柱齒輪,且齒輪位置居中,故可采用一對軸承對稱布置于齒輪兩側的方案。 圖3.2:圓柱齒輪軸的軸承布置方案 3.2 軸的設計與校核 軸是組成機器的主要零件之一,一切作回轉運動的零件都必須安裝在軸上才能進行運動及動力的傳遞。因此軸的作用是支撐回轉件及傳遞運動和動力。軸的結構設計是根據軸上零件的安裝、定位及軸的制造工藝等方面的要求,合理確定軸的結構形式和尺寸。軸的結構
48、設計不合理,會影響軸的工作能力和軸上零件工作的可靠性。 3.2.1 主動錐齒輪軸的設計與校核 1.最小直徑的確定 此軸為花鍵軸,初選為 (3.1) K取4.0,Tm 變速器輸出的最大轉矩。則d=39, 因為一軸是花鍵軸,即花鍵的內徑應為39,于是花鍵軸外徑為D=47。 2.各軸段直徑的確定 軸段Ⅰ是安裝聯軸法蘭的,經分析可知其是最小軸頸處,其與軸的聯接為花鍵連接,可取其直徑為D1=47;軸段Ⅱ是安裝圓錐滾子軸承的軸段,選擇軸承內徑為d=50,軸徑就和軸承內徑相等;軸段Ⅲ是過渡軸段,取為D3=45mm;軸Ⅳ是安裝安裝圓錐滾子軸承的軸
49、段,由于其承受的載荷較前一軸承大,所以選取軸承的內徑為D=65mm。 3.初步選擇滾動軸承 因軸承同時受有徑向力和軸向力的作用,故選用單列圓錐滾子軸承??紤]到各種因素,從軸承手冊上初步選擇軸承A為0基本游隙組、標準精度級的單列圓錐滾子軸承,其軸承代號為32310,其尺寸為50*110*42.25;軸承B為2基本游隙組、標準精度級的單列圓錐滾子軸承,其代號為32313,其尺寸為65*140*51,這個軸承采用軸肩定位。 4.軸上零件的周向定位 軸Ⅰ和萬向節(jié)的聯接采用法蘭凸緣聯接,法蘭與軸的鏈接采用花鍵聯接。首先計算花鍵的有效鏈接長度,根據花鍵的校核公式 ,可得
50、 (3.2) 其中查得,,,,,。將數據代人上式可得 考慮到安裝等因素,取有效長度為。 所以軸段Ⅰ的長度取為。 5.確定軸上的圓角和倒角的尺寸: 取軸端倒角為。 6.作出彎扭合成圖并判斷危險截面 1).求支反力 根據軸的結構,根據軸的計算簡圖及前面計算的到的齒輪載荷求出軸承的支反力有: 對于H面有: 由力的平衡和力矩平衡(對A點取矩)可得: 其中的值見表3-2,于是可求得:,;同理可得V面得支反力為:,,圖中的軸向反力為。 2).根據支反力作出軸的彎矩圖和扭矩圖 支點
51、B處的彎矩最大為 ,,合成彎矩為 ,該軸的扭矩為,C點只受扭矩其值為。 作出軸的彎矩圖和扭矩圖,如圖3.1所示。 由圖可看出危險截面為截面B和C。 按彎扭合成應力校核軸的強度.: 截面B的校核: 根據第三強度理論有 (3.3) 其中折合系數,抗彎截面模量,則 截面C的校核: 截面C只受扭矩作用,因此只校核其剪切應力由第一強度理論有 (3.4) 7.軸的許用應力計算 軸的材料是20CrMnTi,其抗拉強度為,屈服極限為,根據
52、彎曲疲勞極限的計算公式可得: 合成彎矩為: 圖3.1 軸Ⅰ的彎扭圖 取安全系數為,則,則剪切許用應力為。由此可看出軸的校核通過,該軸安全。 3.2.2 從動錐齒輪軸的設計校核 1.初步確定軸的最小直徑 由經驗公式可得 (3.5) 其中取,則有 取,由于主動斜齒輪分度圓直徑為,由軸承手冊查到相應軸的直徑最小為,因此軸Ⅱ應當做成齒輪軸。軸的材料和主動斜齒輪材料相同為42CrMo。 2.各軸段直徑的確定: 軸段Ⅰ、Ⅴ是安裝圓錐滾子軸承的軸段,可取
53、其直徑為。軸段Ⅱ左邊是定位圓錐滾子軸承的軸肩,查軸承手冊可知其,可?。惠S段Ⅳ取為;軸Ⅲ定位從動錐齒輪的軸肩,其直徑取為。 3.初步選擇滾動軸承 因軸承同時受有徑向力和軸向力的作用,故選用單列圓錐滾子軸承。其中軸承C左邊采用套筒定位??紤]到各種因素,從軸承手冊上初步選擇軸承C、D為0基本游隙組、標準精度級的單列圓錐滾子軸承,其軸承代號為32310,其尺寸為。 4.各個軸段的長度確定 各個軸段的長度確定除了考慮各自的要求外,還要考慮箱體的對稱性。 軸段Ⅰ是安裝圓錐滾子軸承的軸段,其長度取決軸承的寬度,查表可知軸承的內襯寬度為B=42.5mm,所以取其長度略比軸承內襯寬度小為40mm。軸段
54、Ⅱ是齒輪軸,為了差速器殼有安裝的空間齒輪左邊軸的長度取為;取軸Ⅰ的中心線到圓錐滾子軸承D右邊的距離為,則齒輪右邊到軸Ⅰ的中心線的距離為;齒輪右邊要留出足夠的退刀曹,其長度取為,所以軸段Ⅱ的長度是;軸段Ⅲ是定位軸肩其寬度應為20mm。段軸Ⅳ段是安裝定位套筒和從動錐齒輪的軸段,取為20mm。 5.確定軸上的圓角和倒角的尺寸: 取軸端倒角為2*45°,各個軸肩處圓角半徑r=2。 6.作出彎扭合成圖并判斷危險截面 1).求支反力 根據軸的結構,在確定支點位置時在軸承手冊中查取。因此作為簡支梁的支承跨距如圖3.2所示為240,根據軸的計算簡圖及前面計算的到的齒輪載荷求出軸承的支反力有: 對于
55、H面有: 由力的平衡和力矩平衡(對D點取矩)可得 (3.6) 其中的值見表3-2,于是可求得:,;同理可得V面得支反力為:,,圖中的軸向反力為。 2.)根據支反力作出軸的彎矩圖和扭矩圖 齒輪2、3處的彎矩最大分別為: ,; ,。 合成彎矩圖為: 圖3.2 合成彎矩圖 由圖上可知齒輪2、3所在截面是危險截面 7.截面A的校核 根據第三強度理論有
56、 (3.7) 其中折合系數,抗彎截面模量, 則 8.截面B的校核 根據第三強度理論有: (3.8) 其中折合系數,抗彎截面模量,則 9.軸的許用應力計算 軸的材料是42CrMo,其抗拉強度為,屈服極限為 ,根據彎曲疲勞極限的計算公式可得 取安全系數為,則,則剪切許用應力為。由此可看出軸的校核通過,該軸安全。 3.3 軸承的選擇 滾動軸承可以概括的分為向心軸承、推力軸承、向心推力軸承三類。因為齒輪采用了螺旋錐齒輪和斜齒圓柱齒輪,故需采用向心推力軸承。由于主減速器的沖
57、擊載荷較大,且轉速較高,所以擬采用圓錐滾子軸承。參考《機械手冊》和 《汽車軸承手冊》,并結合上面計算出的軸的數據,采用以下軸承: 內徑 外徑 寬度 型號 主動圓錐齒輪前軸承 50 110 42.25 32310 主動圓錐齒輪后軸承 65 140 48 32313 從動圓錐齒輪軸承 50 110 42.25 32310 3.3.1主減速器軸承的壽命計算 1 軸承的載荷計算 1).主減速器當量載荷 當量
58、載荷的求解: 實踐表明,軸承的主要損壞形式是疲勞損壞,所以應按輸入的當量轉矩進行 計算。作用在主減速器主動齒輪上的當量轉矩可按下式求得 (3.9) 式中—發(fā)動機最大轉矩, —變速器1、2、3、···、倒檔使用率其值可參考表 —變速器1、2、3、···、倒檔的傳動比 —變速器處于1、2、3、···、倒檔時的發(fā)動機轉矩利用率 查表可得,,,,, ,,,,, 分配變速器格擋的傳動比,去五檔傳動比為,則 ,,,其中已知一檔傳動比為,所以各檔的傳動比取為,,,將數據代入上式可得 求齒輪上的力 a 錐齒輪副 主動錐齒輪的周向力為 查表4
59、-1可得錐齒輪的軸向力、徑向力的計算公式為 b.斜齒圓柱齒輪副 主動齒輪所傳遞的當量轉矩為 則可得其周向力為 軸向力為 徑向力為 表4.1主減速器齒輪上承受的當量載荷 F 齒輪 齒輪1 齒輪2 齒輪3 齒輪4 8829.97 8829.97 16025.4 16025.4 7426.6 1044.5 5198.6 5198.6 1044.5 7426.6 6132.9 6132.9 c.軸承的軸向附加載荷 圖4.1 軸承A、B載荷計算圖 軸Ⅰ的軸向附加載為 軸Ⅱ的軸向附加載荷為
60、 2.軸承的軸向力和徑向力 軸承A、B的軸向力和徑向力 軸承的受力簡圖如右圖所示,其中 ,, 軸承A的徑向力力可由下式算得 , (3.10) 代入數據可得 軸承B的徑向力可由下式算得, (3.11) 代入數據可得 查軸承手冊可知,。故軸承A、B的派生軸向力為 ,,其方向如圖所示,由于 圖4.2 軸承C、D的計算簡圖 所以軸承B被壓緊,即, 軸承C、D的軸向力和徑向力 軸承的受力簡圖如右圖所示,其中 ,, , 軸承C的徑向力力可由下式算得 , (3.12) 代入數據可得
61、軸承D的徑向力力可由下式算得: , (3.13) 代入數據可得 查軸承手冊可知,。故軸承C、D的派生軸向力為 ,, 由于。所以軸承D被壓緊,即,。 3)軸承E、F的軸向力和徑向力 軸承的受力簡圖如右圖所示,其,,。 軸承E的徑向力力可由式4.2算得,代入數據可得: 軸承F的徑向力可由上式算得,代入數據可得: 查軸承手冊可知,。故軸承E、F的派生軸向力為 , 其方向如圖4.3示: 圖4.3 E、F軸承受力圖 所以軸承B被壓緊,即,。 .3.3.2 軸承的壽命計算 1.軸承的當量動載荷 軸承的當量動載荷由下式
62、算得 其中是載荷系數,取為,根據軸承型號查軸承手冊可得 A:代號30216,,,;B:代號32218,,,;C、D:代號30217,,,。于是可得軸承的當量動載荷為: 2.軸承的壽命 軸承的壽命可由下式算得: , (3.16) 式中是軸承轉速;是指數,對于滾子軸承。由于半軸正常的轉速可由下式求得 ,式中是汽車行駛的平均速度,對于中型貨車,取中間值為37.5km/h;是車輪的滾動半徑,這里取車輪半徑為。則有: 軸承A、B的轉速為,軸承C、D的轉速為,則其壽命為 ; ; ; 。 4 其它零件及工藝
63、的設計 4.1 齒輪結構形式的確定 主動錐齒輪的小端分度圓直徑為d=55,所以該齒輪應選用軸齒輪。軸的材料和主動錐齒輪材料相同為20CrMnTi。 由于從動圓柱斜齒輪中有差速器在其中,所以必須做成兩部分,組裝時由螺釘連接在一起,可參看裝配圖及從動斜齒輪零件圖。 從動錐齒輪的分度圓直徑為250mm,齒輪的厚度為38mm,若采用整體式齒輪,則會給鑄造帶來不便,且會影響齒輪的結構性能。故采用聯接式齒輪,如零件圖從動錐齒輪圖所示。 主動斜齒圓柱齒輪,其分度圓直徑為87.43mm, 基圓直徑為72.43,計算得此軸的最小直徑為50mm,所以此齒輪做成軸齒輪形式。如零件圖主動斜齒圓柱齒輪圖所示。
64、 4.2主動錐齒輪花鍵的設計 設計選用圓柱直齒30o漸開線花鍵,參考《實用機械設計手冊》,選取花鍵的長度L=70,初選模數m=3,z=14;根據《機械設計》P109,假設載荷在鍵的工作面上均勻分布,各齒面上壓力的合力N作用在平均直徑dm處,即轉遞的轉矩T=ZN.dm/2.并引入系數φ來考慮實際載荷在各花鍵齒上分配的影響,則花鍵連接的強度條件為靜連接: σP=≤[σ]P (4.1) 式中 φ—載荷分配不均勻系數,取0.8; z—花鍵齒數,14; L—齒的工作長度70m; h—花鍵齒側面的工作高度,漸開線花鍵,a=30°
65、,h=m=3mm; dm—花鍵的平均直徑,漸開線花鍵dm=mz=42mm; [σ]P—許用擠壓應力,由P106表6-2查的[σ]P=45MPa; T—花鍵承受的轉矩,按驅動輪打滑時主動錐齒輪的計算轉矩, T=Tz=1987.44N.m η為差速器傳遞效率,0.95 代入數據算得 σP=19.1 MPa. 所以,花鍵滿足連接強度要求。 4.3雙級主減速器的潤滑 軸承的潤滑 1.軸承的值計算 1)計算軸承的轉速 汽車車輪的最大角速度,則各軸的轉速為: 。 式中:—軸的轉速;—第i軸
66、到車輪間的傳動比。 , , 。 2)軸承的值計算 由以上所算得的數據可得: 軸承A:; 軸承B:; 軸承C、D:; 軸承E、F:。 2.軸承潤滑設計 1)潤滑方式的選擇 軸承A、B選用油浴潤滑的方式,軸承C、D也選用油浴潤滑,潤滑油的牌號為:GB 443——1989 L-AN15;軸承E、F選用脂潤滑,潤滑脂牌號為:GB 7324——1994 ZL-3。 2)潤滑方法 在主減速器中,潤滑油不能直接對軸承A、B、C、D進行潤滑,因此本文通過導油槽和集油槽來時相對上述齒輪的潤滑,然后通過圓錐滾子軸承的泵油作用把油排到油池中。潤滑路線是:錐齒輪旋轉時甩油→集油槽→導油槽→軸承A、B之間→回油孔→軸承C、D→箱體。 齒輪的潤滑: 雙級主減速器的潤滑一般是通過油浴潤滑,油池在橋殼內。潤滑油的型號選為:GB 443——1989 L-AN15。由于從動錐齒輪的分度圓直徑為,油浸沒齒寬的3/4,即;而從動圓柱齒輪的分度圓直徑為,按要求潤滑油的浸沒深度不得超過齒輪半徑徑的1/3,即。因此,可以算的油面的高度為(從從動斜圓柱齒輪低處計): ,遠遠超出要求值。 因
- 溫馨提示:
1: 本站所有資源如無特殊說明,都需要本地電腦安裝OFFICE2007和PDF閱讀器。圖紙軟件為CAD,CAXA,PROE,UG,SolidWorks等.壓縮文件請下載最新的WinRAR軟件解壓。
2: 本站的文檔不包含任何第三方提供的附件圖紙等,如果需要附件,請聯系上傳者。文件的所有權益歸上傳用戶所有。
3.本站RAR壓縮包中若帶圖紙,網頁內容里面會有圖紙預覽,若沒有圖紙預覽就沒有圖紙。
4. 未經權益所有人同意不得將文件中的內容挪作商業(yè)或盈利用途。
5. 裝配圖網僅提供信息存儲空間,僅對用戶上傳內容的表現方式做保護處理,對用戶上傳分享的文檔內容本身不做任何修改或編輯,并不能對任何下載內容負責。
6. 下載文件中如有侵權或不適當內容,請與我們聯系,我們立即糾正。
7. 本站不保證下載資源的準確性、安全性和完整性, 同時也不承擔用戶因使用這些下載資源對自己和他人造成任何形式的傷害或損失。
最新文檔
- 2025年防凍教育安全教育班會全文PPT
- 2025年寒假安全教育班會全文PPT
- 初中2025年冬季防溺水安全教育全文PPT
- 初中臘八節(jié)2024年專題PPT
- 主播直播培訓提升人氣的方法正確的直播方式如何留住游客
- XX地區(qū)機關工委2024年度年終黨建工作總結述職匯報
- 心肺復蘇培訓(心臟驟停的臨床表現與診斷)
- 我的大學生活介紹
- XX單位2024年終專題組織生活會理論學習理論學習強黨性凝心聚力建新功
- 2024年XX單位個人述職述廉報告
- 一文解讀2025中央經濟工作會議精神(使社會信心有效提振經濟明顯回升)
- 2025職業(yè)生涯規(guī)劃報告自我評估職業(yè)探索目標設定發(fā)展策略
- 2024年度XX縣縣委書記個人述職報告及2025年工作計劃
- 寒假計劃中學生寒假計劃安排表(規(guī)劃好寒假的每個階段)
- 中央經濟工作會議九大看點學思想強黨性重實踐建新功