二級齒輪減速器外文翻譯
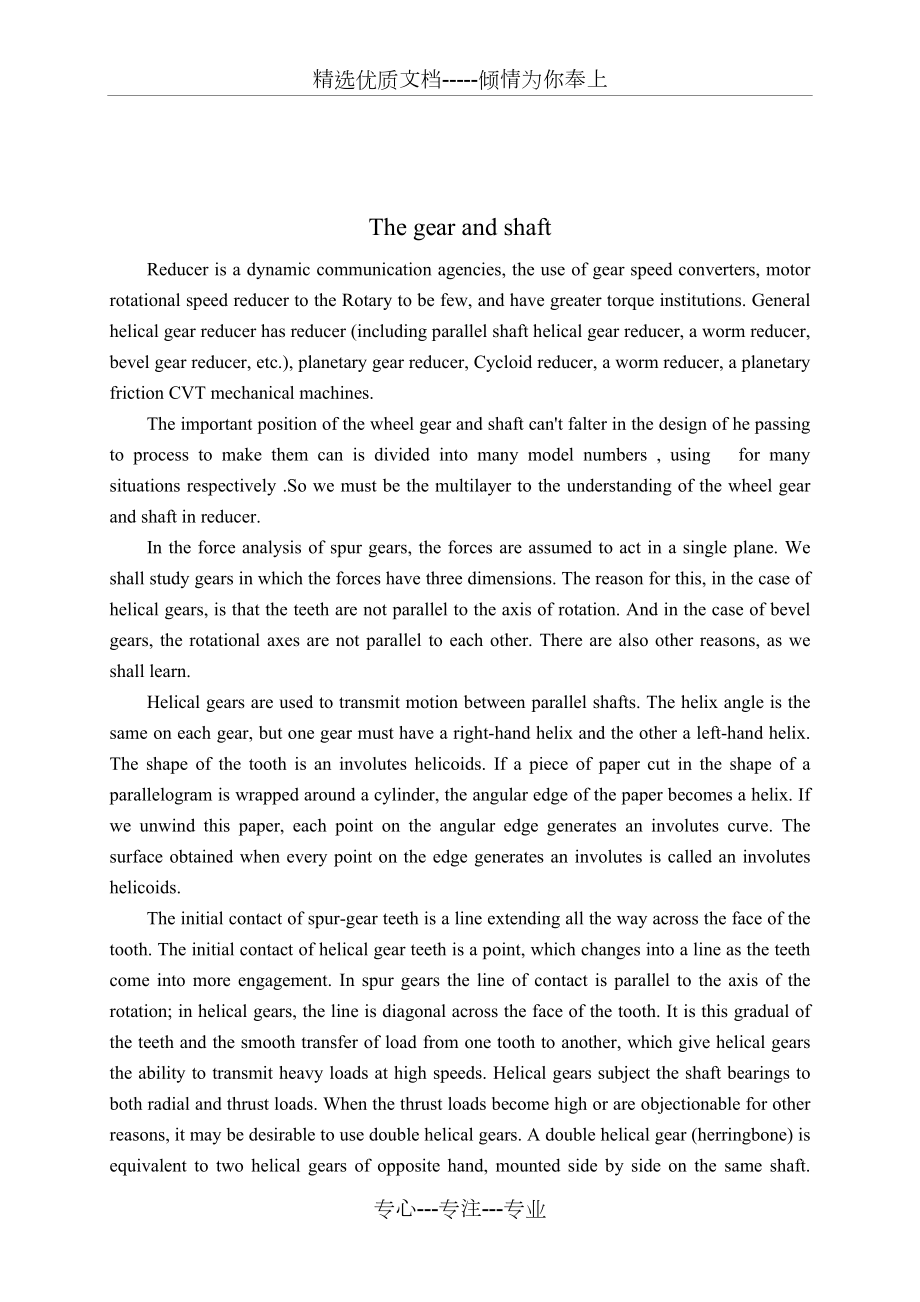


《二級齒輪減速器外文翻譯》由會員分享,可在線閱讀,更多相關(guān)《二級齒輪減速器外文翻譯(9頁珍藏版)》請在裝配圖網(wǎng)上搜索。
1、精選優(yōu)質(zhì)文檔-----傾情為你奉上 The gear and shaft Reducer is a dynamic communication agencies, the use of gear speed converters, motor rotational speed reducer to the Rotary to be few, and have greater torque institutions. General helical gear reducer has reducer (including parallel shaft helical gear reduce
2、r, a worm reducer, bevel gear reducer, etc.), planetary gear reducer, Cycloid reducer, a worm reducer, a planetary friction CVT mechanical machines. The important position of the wheel gear and shaft can't falter in the design of he passing to process to make them can is divided into many model num
3、bers , using for many situations respectively .So we must be the multilayer to the understanding of the wheel gear and shaft in reducer. In the force analysis of spur gears, the forces are assumed to act in a single plane. We shall study gears in which the forces have three dimensions. The reason
4、for this, in the case of helical gears, is that the teeth are not parallel to the axis of rotation. And in the case of bevel gears, the rotational axes are not parallel to each other. There are also other reasons, as we shall learn. Helical gears are used to transmit motion between parallel shafts.
5、 The helix angle is the same on each gear, but one gear must have a right-hand helix and the other a left-hand helix. The shape of the tooth is an involutes helicoids. If a piece of paper cut in the shape of a parallelogram is wrapped around a cylinder, the angular edge of the paper becomes a helix.
6、 If we unwind this paper, each point on the angular edge generates an involutes curve. The surface obtained when every point on the edge generates an involutes is called an involutes helicoids. The initial contact of spur-gear teeth is a line extending all the way across the face of the tooth. The
7、initial contact of helical gear teeth is a point, which changes into a line as the teeth come into more engagement. In spur gears the line of contact is parallel to the axis of the rotation; in helical gears, the line is diagonal across the face of the tooth. It is this gradual of the teeth and the
8、smooth transfer of load from one tooth to another, which give helical gears the ability to transmit heavy loads at high speeds. Helical gears subject the shaft bearings to both radial and thrust loads. When the thrust loads become high or are objectionable for other reasons, it may be desirable to u
9、se double helical gears. A double helical gear (herringbone) is equivalent to two helical gears of opposite hand, mounted side by side on the same shaft. They develop opposite thrust reactions and thus cancel out the thrust load. When two or more single helical gears are mounted on the same shaft, t
10、he hand of the gears should be selected so as to produce the minimum thrust load. Crossed-helical, or spiral, gears are those in which the shaft centerlines are neither parallel nor intersecting. The teeth of crossed-helical fears have point contact with each other, which changes to line contact as
11、 the gears wear in. For this reason they will carry out very small loads and are mainly for instrumental applications, and are definitely not recommended for use in the transmission of power. There is on difference between a crossed helical. Gear and helical gear until they are mounted in mesh with
12、each other. They are manufactured in the same way. A pair of meshed crossed helical gears usually have the same hand; that is a right-hand driver goes with a right-hand driven. In the design of crossed-helical gears, the minimum sliding velocity is obtained when the helix angle are equal. However, w
13、hen the helix angle are not equal, the gear with the helix angle should be used as the driver if both gears have the same hand. Worm gears are similar to crossed helical gears. The pinion or worm has a small number of teeth, usually one to four, and since they completely wrap around the pitch cylin
14、der they are called threads. Its mating gear is called a worm gear, which is not a true helical gear. A worm and worm gear are used to provide a high angular-velocity reduction between nonintersecting shafts which are usually at right angle. The worm gear is not a helical gear because its face is ma
15、de concave to fit the curvature of the worm in order to provide line contact instead of point contact. However, a disadvantage of worm gearing is the high sliding velocities across the teeth, the same as with crossed helical gears. Worm gearing are either single or double enveloping. A single-envel
16、oping gearing is one in which the gear wraps around or partially encloses the worm. A gearing in which each element partially encloses the other is, of course, a double-enveloping worm gearing. The important difference between the two is that area contact exists between the teeth of double-envelopin
17、g gears while only line contact between those of single-enveloping gears. The worm and worm gear of a set have the same hand of helix as for crossed helical gears, but the helix angles are usually quite different. The helix angle on the worm is generally quite large, and that on the gear very small.
18、 Because of this, it is usual to specify the lead angle on the worm, which is the complement of the worm helix angle, and the helix angle on the gear; the two angles are equal for a 90-deg. Shaft angle. When gears are to be used to transmit motion between intersecting shaft, some of bevel gear is r
19、equired. Although bevel gear are usually made for a shaft angle of 90 deg. They may be produced for almost any shaft angle. The teeth may be cast, milled, or generated. Only the generated teeth may be classed as accurate. In a typical bevel gear mounting, one of the gear is often mounted outboard of
20、 the bearing. This means that shaft deflection can be more pronounced and have a greater effect on the contact of teeth. Another difficulty, which occurs in predicting the stress in bevel-gear teeth, is the fact the teeth are tapered. Straight bevel gears are easy to design and simple to manufactur
21、e and give very good results in service if they are mounted accurately and positively. As in the case of spur gears, however, they become noisy at higher values of the pitch-line velocity. In these cases it is often good design practice to go to the spiral bevel gear, which is the bevel counterpart
22、of the helical gear. As in the case of helical gears, spiral bevel gears give a much smoother tooth action than straight bevel gears, and hence are useful where high speed are encountered. It is frequently desirable, as in the case of automotive differential applications, to have gearing similar to
23、bevel gears but with the shaft offset. Such gears are called hypoid gears because their pitch surfaces are hyperboloids of revolution. The tooth action between such gears is a combination of rolling and sliding along a straight line and has much in common with that of worm gears. A shaft is a rotat
24、ing or stationary member, usually of circular cross section, having mounted upon it such elements as gears, pulleys, flywheels, cranks, sprockets, and other power-transmission elements. Shaft may be subjected to bending, tension, compression, or tensional loads, acting singly or in combination with
25、one another. When they are combined, one may expect to find both static and fatigue strength to be important design considerations, since a single shaft may be subjected to static stresses, completely reversed, and repeated stresses, all acting at the same time. The word “shaft” covers numerous var
26、iations, such as axles and spindles. An axle is a shaft, wither stationary or rotating, nor subjected to torsion load. A shirt rotating shaft is often called a spindle. When either the lateral or the tensional deflection of a shaft must be held to close limits, the shaft must be sized on the basis
27、of deflection before analyzing the stresses. The reason for this is that, if the shaft is made stiff enough so that the deflection is not too large, it is probable that the resulting stresses will be safe. But by no means should the designer assume that they are safe,it is almost always necessary to
28、 calculate them so that he knows they are within acceptable limits. Whenever possible, the power-transmission elements,such as gears or pullets, should be located close to the supporting bearings, This reduces the bending moment, and hence the deflection and bending stress. Although the von Mises-H
29、encky-Goodman method is difficult to use in design of shaft, it probably comes closest to predicting actual failure. Thus it is a good way of checking a shaft that has already been designed or of discovering why a particular shaft has failed in service. Furthermore, there are a considerable number o
30、f shaft-design problems in which the dimension are pretty well limited by other considerations, such as rigidity, and it is only necessary for the designer to discover something about the fillet sizes, heat-treatment, and surface finish and whether or not shot preening is necessary in order to achie
31、ve the required life and reliability. Because of the similarity of their functions, clutches and brakes are treated together. In a simplified dynamic representation of a friction clutch, or brake, two inertias I1 and I2 traveling at the respective angular velocities W1 and W2, one of which may be z
32、ero in the case of brake, are to be brought to the same speed by engaging the clutch or brake. Slippage occurs because the two elements are running at different speeds and energy is dissipated during actuation, resulting in a temperature rise. In analyzing the performance of these devices we shall b
33、e interested in the actuating force, the torque transmitted, the energy loss and the temperature rise. The torque transmitted is related to the actuating force, the coefficient of friction, and the geometry of the clutch or brake. This is problem in static, which will have to be studied separately f
34、or earth geometric configuration. However, temperature rise is related to energy loss and can be studied without regard to the type of brake or clutch because the geometry of interest is the heat-dissipating surfaces. The various types of clutches and brakes may be classified as fellows. 1. Rim typ
35、e with internally expanding shoes 2. Rim type with externally contracting shoes 3. Band type 4. Disk or axial type 5. Cone type 6. Miscellaneous type The analysis of all type of friction clutches and brakes use the same general procedure. The following step are necessar
36、y: 1. Assume or determine the distribution of pressure on the frictional surfaces. 2. Find a relation between the maximum pressure and the pressure at any point. 3. Apply the condition of statically equilibrium to find (a) the actuating force, (b) the torque, and (c) the support reactions. Misce
37、llaneous clutches include several types, such as the positive-contact clutches, overload-release clutches, overrunning clutches, magnetic fluid clutches, and others. A positive-contact clutch consists of a shift lever and two jaws. The greatest differences between the various types of positive clutc
38、hes are concerned with the design of the jaws. To provide a longer period of time for shift action during engagement, the jaws may be ratchet-shaped, or gear-tooth-shaped. Sometimes a great many teeth or jaws are used, and they may be cut either circumferentially, so that they engage by cylindrical
39、mating, or on the faces of the mating elements. Although positive clutches are not used to the extent of the frictional-contact type, they do have important applications where synchronous operation is required. Devices such as linear drives or motor-operated screw drivers must run
40、to definite limit and then come to a stop. An overload-release type of clutch is required for these applications. These clutches are usually spring-loaded so as to release at a predetermined toque. The clicking sound which is heard when the overload point is reached is considered to be a desirable s
41、ignal. An overrunning clutch or coupling permits the driven member of a machine to “freewheel” or “overrun” because the driver is stopped or because another source of power increase the speed of the driven. This type of clutch usually uses rollers or balls mounted between an outer sieve and an inne
42、r member having flats machined around the periphery. Driving action is obtained by wedging the rollers between the sleeve and the flats. The clutch is obtained by wedging the rollers between the sleeve and the flats. The clutch is therefore equivalent to a pawl and ratchet with an infinite number of
43、 teeth. Magnetic fluid clutch or brake is a relatively new development which has two parallel magnetic plates. Between these plates is a lubricated magnetic powder mixture. An electromagnetic coil is inserted somewhere in the magnetic circuit. By varying the excitation to this coil, the shearing st
44、rength of the magnetic fluid mixture may be accurately controlled. Thus any condition from a full slip to a frozen lockup may be obtained . 齒輪和軸的介紹 減速器是一種動力傳達機構(gòu),利用齒輪的速度轉(zhuǎn)換器,將馬達的回轉(zhuǎn)數(shù)減速到所要的回轉(zhuǎn)數(shù),并得到較大轉(zhuǎn)矩的機構(gòu)。一般的減速器有斜齒輪減速器(包括平行軸斜齒輪減速器、蝸輪減速器、錐齒輪減速器等等)、行星齒輪減速器、擺線針輪減速器、蝸輪蝸桿減速器、行星摩擦式機械無級變速機等等
45、。 在減速器設(shè)計中齒輪和軸的重要地位是不可動搖的。齒輪和軸主要安裝在主軸箱來傳遞力的方向。通過加工制造它們可以分為許多的型號,分別用于許多的場合。所以我們對齒輪和軸的了解和認識必須是多層次多方位的。 在直齒圓柱齒輪的受力分析中,是假定各力作用在單一平面的。我們將研究作用力具有三維坐標的齒輪。因此,在斜齒輪的情況下,其齒向是不平行于回轉(zhuǎn)軸線的。而在錐齒輪的情況中各回轉(zhuǎn)軸線互相不平行。這還有其他道理值得我們學習就像我們討論的那樣。 斜齒輪用于傳遞平行軸之間的運動。傾斜角度每個齒輪都一樣,但一個必須是右旋斜齒,而另一個必須是左旋斜齒。齒的形狀是一漸開線螺旋面。如果一張被剪成平行四邊形(矩形)的
46、紙張包圍在齒輪圓柱體上,紙上印出齒的角刃邊就變成斜線。如果我展開這張紙,在血角刃邊上的每一個點就發(fā)生一漸開線曲線。 直齒圓柱齒輪輪齒的初始接觸處是跨過整個齒面而伸展開來的線。斜齒輪輪齒的初始接觸是一點,當齒進入更多的嚙合時,它就變成線。在直齒圓柱齒輪中,接觸線是平行于回轉(zhuǎn)軸線的。在斜齒輪中,該線是跨過齒面的對角線。它是齒輪逐漸進行嚙合并平穩(wěn)的從一個齒到另一個齒傳遞運動,那樣就使斜齒輪具有高速重載下平穩(wěn)傳遞運動的能力。斜齒輪使軸的軸承承受徑向和軸向力。當軸向推力變得大了或由于別的原因而產(chǎn)生某些影響時,那就可以使用人字齒輪。雙斜齒輪(人字齒輪)是與反向并排地裝在同一軸上的兩個斜齒輪等效。他們產(chǎn)生
47、相反的軸向推力作用,這樣就消除了軸向推力。當兩個或更多個單向齒斜齒輪被安裝在同一軸上時,齒輪的齒向應作選擇,以便產(chǎn)生最小的軸向推力。 交錯軸斜齒輪或螺旋齒輪,他們是軸中心線既不相交也不平行。交錯軸斜齒輪的齒彼此之間發(fā)生點接觸,它隨著齒輪的磨合而變成線接觸。因此他們只能傳遞小的載荷和主要用于儀器設(shè)備中,而且肯定不能推薦在動力傳動中使用。交錯軸斜齒輪與斜齒輪之間在被安裝后互相嚙合之前是沒有任何區(qū)別的。它們是以同樣的方法進行制造。一對相嚙合的交錯軸斜齒輪通常具有同樣的齒向,即右旋主動齒輪跟右旋從動齒輪相嚙合。在交錯軸斜齒設(shè)計中,當該齒的斜角相等時所產(chǎn)生滑移速度最小。然而當該齒的斜角不相等時,如果兩
48、個齒輪具有相同齒向的話,大斜角齒輪應用作主動齒輪。 蝸輪與交錯軸斜齒輪相似,小齒輪即蝸桿具有較小的齒數(shù),通常是一到四齒,由于它們完全纏繞在節(jié)圓柱上,因此它們被稱為螺紋齒。與其相配的齒輪叫做蝸輪,蝸輪不是真正的斜齒輪。蝸桿和蝸輪通常是用于向垂直相交軸之間的傳動提供大的角速度減速比。蝸輪不是斜齒輪,因為其齒頂面做成中凹形狀以適配蝸桿曲率,目的是要形成線接觸而不是點接觸。然而就像交錯軸斜齒輪那樣,蝸桿蝸輪傳動機構(gòu)中存在齒間有較大滑移速度的缺點。 蝸桿蝸輪機構(gòu)有單包圍和雙包圍機構(gòu)。單包圍機構(gòu)就是蝸輪包裹或部分包裹著蝸桿的一種機構(gòu)。當然,如果每個構(gòu)件各自局部地包圍著對方的蝸輪機構(gòu)就是雙包圍蝸輪蝸桿機
49、構(gòu)。這兩者之間的重要區(qū)別是,在雙包圍蝸輪組的輪齒間有面接觸,而在單包圍的蝸輪組的輪齒間有線接觸。一個裝置中的蝸桿和蝸輪正像交錯軸斜齒輪那樣具有相同的齒向,但是其斜齒齒角的角度是不相同的。蝸桿上的齒斜角度通常很大,而蝸輪上的則極小,因此習慣常規(guī)定蝸桿的導角就是蝸桿齒輪斜角的余角;也規(guī)定了蝸輪上的齒斜角,該兩角之和就等于90度的軸線交角。 當齒輪是用來傳遞相交軸之間的運動時,就需要某種形式的錐齒輪。雖然錐齒輪通常制造成能構(gòu)成90度軸交角,但它們也可產(chǎn)生任何角度的軸交角。輪齒可以鑄出、銑制或滾切加工。僅就滾齒而言就可達一級精度。在典型的錐齒輪安裝中,其中一個錐齒輪常常裝于支承的外側(cè)。這意味著軸的撓
50、曲情況更加明顯而使在輪齒接觸上具有更大的影響。另外一個難題,發(fā)生在難于預示錐齒輪輪齒上的應力,實際上是由于齒輪被加工成錐狀造成的。 直齒錐齒輪易于設(shè)計且制造簡單,如果他們安裝的精密確定,在運轉(zhuǎn)中會產(chǎn)生良好的效果。然而在直齒圓柱齒輪情況下,在節(jié)線速度較高時,他們將發(fā)出噪音。在這些情況下,螺旋錐齒輪比直齒輪能產(chǎn)生平穩(wěn)的多的嚙合作用,因此碰到高速運轉(zhuǎn)的場合那是很有用的。當在汽車的各種不同用途中,有一個帶偏心軸的類似錐齒輪的機構(gòu),那是常常所希望的。這樣的齒輪機構(gòu)叫做準雙曲面齒輪機構(gòu),因為它們的節(jié)面是雙曲回轉(zhuǎn)面。這種齒輪之間的輪齒作用是沿著一根直線上產(chǎn)生滾動與滑動相結(jié)合的運動并和蝸輪蝸桿的輪齒作用有著
51、更多的共同之處。 軸是一種轉(zhuǎn)動或靜止的桿件,通常有圓形橫截面。在軸上安裝像齒輪、皮帶輪、飛輪、曲柄、鏈輪和其他動力傳遞零件。軸能夠承受彎曲、拉伸、壓縮或扭轉(zhuǎn)載荷,這些力相結(jié)合時,人們期望找到靜強度和疲勞強度作為設(shè)計的重要依據(jù)。因為單根軸可以承受靜壓力、變應力和交變應力,所有的應力作用都是同時發(fā)生的。 “軸”這個詞包含著多種含義,例如心軸和主軸。心軸也是軸,既可以旋轉(zhuǎn)也可以靜止的軸,但不承受扭轉(zhuǎn)載荷。短的轉(zhuǎn)動軸常常被稱為主軸。 當軸的彎曲或扭轉(zhuǎn)變形必需被限制于很小的范圍內(nèi)時,其尺寸應根據(jù)變形來進行應力分析而確定。因此,如若軸要做得有足夠的剛度以致?lián)锨惶?,那么合應力符合安全要求那是完全?/p>
52、能的。但決不意味著設(shè)計者要保證它們是安全的,軸幾乎總是要進行計算的,知道它們是處在可以接受的允許的極限以內(nèi)。如齒輪或皮帶輪都應該設(shè)置在靠近配套軸承附近,這就降低了彎矩,從而減小變形和彎曲應力。 雖然來自M.H.G的方法在設(shè)計軸中難于應用,但它可能用來準確預示實際的失效。因此,它是一個檢驗已經(jīng)設(shè)計好了的軸的或者發(fā)現(xiàn)具體軸在運轉(zhuǎn)中發(fā)生損壞原因的好方法。進而有著大量的關(guān)于設(shè)計的問題,如剛度,設(shè)計者去查找關(guān)于圓角尺寸、熱處理、表面光潔度和是否要進行噴丸處理等資料,那真正的唯一的需要是實現(xiàn)所要求的壽命和可靠性。 由于他們的功能相似,將離合器和制動器一起處理。在簡化摩擦離合器或制動器的動力學表達式中,
53、各自以角速度w1和w2運動的兩個轉(zhuǎn)動慣量I1和I2,由于接上離合器或制動器而最終要導致同樣的速度,在制動器情況下其中之一可能是零。因為兩個構(gòu)件開始以不同速度運轉(zhuǎn)而產(chǎn)生打滑現(xiàn)象,并且在作用過程中能量散失,結(jié)果導致溫升。在分析這些裝置的性能時,我們應注意到作用力,傳遞的扭矩,散失的能量和溫升。所傳遞的扭矩關(guān)系到作用力,摩擦系數(shù)和離合器或制動器的幾何狀況,這是一個靜力學問題。這個問題將必須對每個幾何機構(gòu)形狀分別進行研究。然而溫升與能量損失有關(guān),研究溫升可能與制動器或離合器的類型無關(guān)。因為幾何形狀的重要性是散熱表面。各種各樣的離合器和制動器可作如下分類: 1.輪緣式內(nèi)膨脹制動塊 2.輪緣式外接觸制
54、動塊 3.條帶式 4.盤型或軸向式 5.圓錐型 6.混合式 分析摩擦離合器和制動器的各種形式都應用同樣的一般程序,下面的步驟是必需的: 1. 假定或確定摩擦表面上壓力分布 2. 找出最大壓力和任一點處壓力之間的關(guān)系 3. 應用靜平衡條件去找尋(a)作用力;(b)扭矩;(c)支反力 混合式離合器包括幾個類型,例如強制接觸離合器、超載釋放保護離合器、超越離合器、磁液離合器等等。 強制接觸離合器由一個變位桿和兩個夾爪組成。各種強制接觸離合器之間最大的區(qū)別與夾爪的設(shè)計有關(guān)。為了在結(jié)合過程中給變換作用提供較長的時間周期,夾爪可以是棘輪式的,螺旋型或齒型的。有時使用許多齒或夾爪。他們可
55、能在圓周面上加工齒,以便它們以圓柱軸向配合來結(jié)合或者在配合元件的端面上加工齒來結(jié)合。 雖然強制離合器不像摩擦接觸離合器用的那么廣泛,但它們確實有很重要的運用。離合器需要同步操作。 有些裝置例如線性驅(qū)動裝置或電機操作螺桿驅(qū)動器必須運行到一定的限度然后停頓下來。這些應用程序就需要超載釋放保護離合器。這些離合器通常用彈簧加載,以使得在達到預定的力矩時釋放。當?shù)竭_超載點時聽到的“喀嚓”聲就被認定為是所希望的信號聲。 超越離合器或連軸器允許機器的被動構(gòu)件“空轉(zhuǎn)”或“超越”,因為主動驅(qū)動件停頓了或者因為另一個動力源使被動構(gòu)件增加了速度。這種離合器通常使用在外套筒和內(nèi)軸件之間的滾子或滾珠之間。驅(qū)動作用是靠在套筒和平面之間契入的滾子來獲得。因此該離合器與具有一定數(shù)量齒的棘輪棘爪機構(gòu)等效。 磁液離合器或制動器相對來說是一個新的發(fā)展,它們具有兩個平行的磁極板。這些磁極板之間有磁粉混合物潤滑。電磁線圈被裝入磁路中的某處,過激勵該線圈,磁液混合的剪切強度可被精確的控制。因此可以獲得從充分滑移到完全鎖住的任何狀態(tài)。 專心---專注---專業(yè)
- 溫馨提示:
1: 本站所有資源如無特殊說明,都需要本地電腦安裝OFFICE2007和PDF閱讀器。圖紙軟件為CAD,CAXA,PROE,UG,SolidWorks等.壓縮文件請下載最新的WinRAR軟件解壓。
2: 本站的文檔不包含任何第三方提供的附件圖紙等,如果需要附件,請聯(lián)系上傳者。文件的所有權(quán)益歸上傳用戶所有。
3.本站RAR壓縮包中若帶圖紙,網(wǎng)頁內(nèi)容里面會有圖紙預覽,若沒有圖紙預覽就沒有圖紙。
4. 未經(jīng)權(quán)益所有人同意不得將文件中的內(nèi)容挪作商業(yè)或盈利用途。
5. 裝配圖網(wǎng)僅提供信息存儲空間,僅對用戶上傳內(nèi)容的表現(xiàn)方式做保護處理,對用戶上傳分享的文檔內(nèi)容本身不做任何修改或編輯,并不能對任何下載內(nèi)容負責。
6. 下載文件中如有侵權(quán)或不適當內(nèi)容,請與我們聯(lián)系,我們立即糾正。
7. 本站不保證下載資源的準確性、安全性和完整性, 同時也不承擔用戶因使用這些下載資源對自己和他人造成任何形式的傷害或損失。
最新文檔
- 建筑施工重大危險源安全管理制度
- 安全培訓資料:典型建筑火災的防治基本原則與救援技術(shù)
- 企業(yè)雙重預防體系應知應會知識問答
- 8 各種煤礦安全考試試題
- 9 危險化學品經(jīng)營單位安全生產(chǎn)管理人員模擬考試題庫試卷附答案
- 加壓過濾機司機技術(shù)操作規(guī)程
- 樹脂砂混砂工藝知識總結(jié)
- XXXXX現(xiàn)場安全應急處置預案
- 某公司消防安全檢查制度總結(jié)
- 1 煤礦安全檢查工(中級)職業(yè)技能理論知識考核試題含答案
- 4.燃氣安全生產(chǎn)企業(yè)主要負責人模擬考試題庫試卷含答案
- 工段(班組)級安全檢查表
- D 氯化工藝作業(yè)模擬考試題庫試卷含答案-4
- 建筑起重司索信號工安全操作要點
- 實驗室計量常見的30個問問答題含解析