畢業(yè)設計論文變速箱殼體組合機床夾具設計含全套CAD圖紙
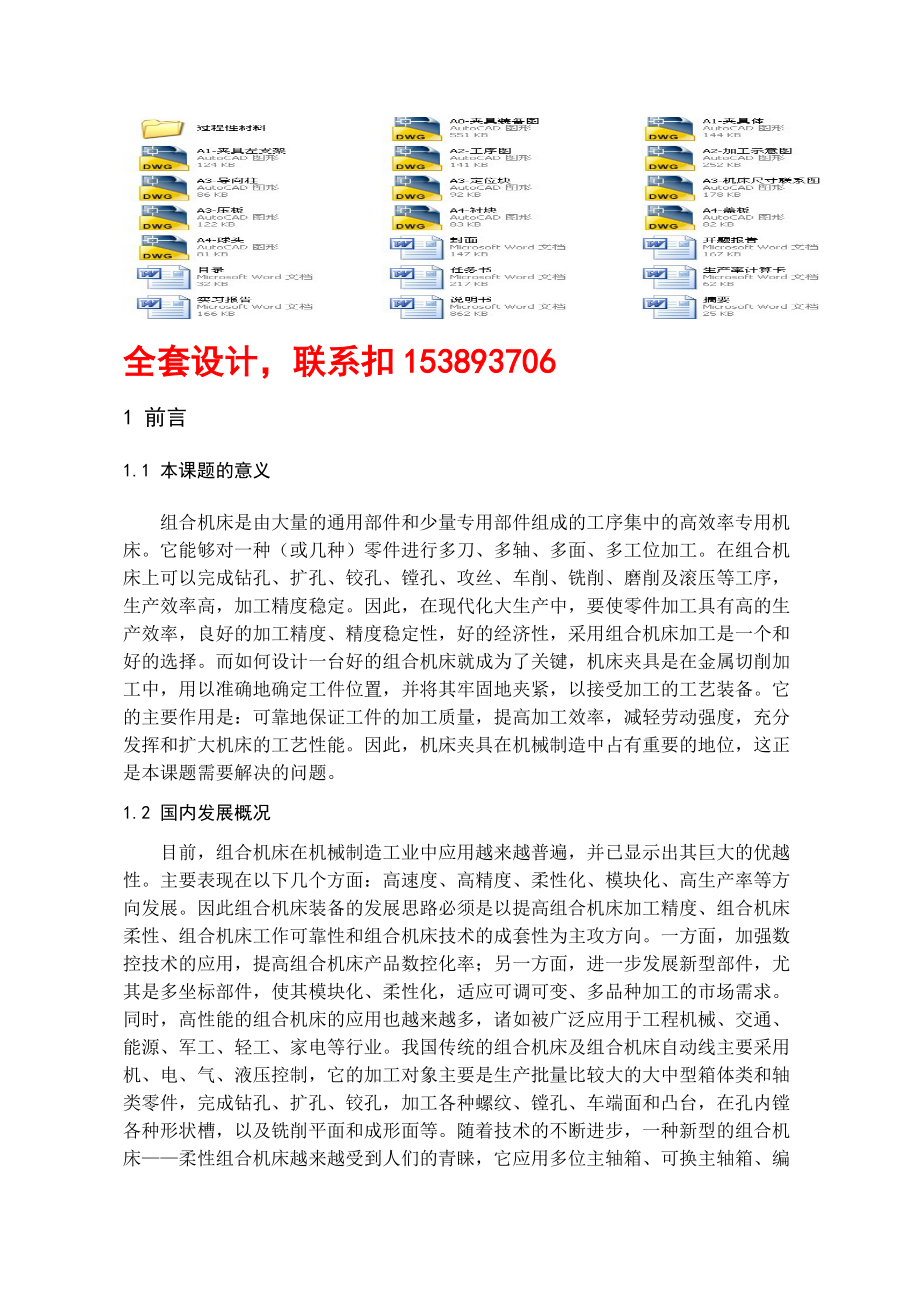


《畢業(yè)設計論文變速箱殼體組合機床夾具設計含全套CAD圖紙》由會員分享,可在線閱讀,更多相關《畢業(yè)設計論文變速箱殼體組合機床夾具設計含全套CAD圖紙(28頁珍藏版)》請在裝配圖網(wǎng)上搜索。
1、 全套設計,聯(lián)系扣153893706 1 前言 1.1 本課題的意義 組合機床是由大量的通用部件和少量專用部件組成的工序集中的高效率專用機床。它能夠?qū)σ环N(或幾種)零件進行多刀、多軸、多面、多工位加工。在組合機床上可以完成鉆孔、擴孔、鉸孔、鏜孔、攻絲、車削、銑削、磨削及滾壓等工序,生產(chǎn)效率高,加工精度穩(wěn)定。因此,在現(xiàn)代化大生產(chǎn)中,要使零件加工具有高的生產(chǎn)效率,良好的加工精度、精度穩(wěn)定性,好的經(jīng)濟性,采用組合機床加工是一個和好的選擇。而如何設計一臺好的組合機床就成為了關鍵,機床夾具是在金屬切削加工中,用以準確地確定工件位置,并將其牢固地夾緊,以接受加工的工藝裝備。它的主要作用是:
2、可靠地保證工件的加工質(zhì)量,提高加工效率,減輕勞動強度,充分發(fā)揮和擴大機床的工藝性能。因此,機床夾具在機械制造中占有重要的地位,這正是本課題需要解決的問題。 1.2 國內(nèi)發(fā)展概況 目前,組合機床在機械制造工業(yè)中應用越來越普遍,并已顯示出其巨大的優(yōu)越性。主要表現(xiàn)在以下幾個方面:高速度、高精度、柔性化、模塊化、高生產(chǎn)率等方向發(fā)展。因此組合機床裝備的發(fā)展思路必須是以提高組合機床加工精度、組合機床柔性、組合機床工作可靠性和組合機床技術的成套性為主攻方向。一方面,加強數(shù)控技術的應用,提高組合機床產(chǎn)品數(shù)控化率;另一方面,進一步發(fā)展新型部件,尤其是多坐標部件,使其模塊化、柔性化,適應可調(diào)可變、多品種加工的
3、市場需求。同時,高性能的組合機床的應用也越來越多,諸如被廣泛應用于工程機械、交通、能源、軍工、輕工、家電等行業(yè)。我國傳統(tǒng)的組合機床及組合機床自動線主要采用機、電、氣、液壓控制,它的加工對象主要是生產(chǎn)批量比較大的大中型箱體類和軸類零件,完成鉆孔、擴孔、鉸孔,加工各種螺紋、鏜孔、車端面和凸臺,在孔內(nèi)鏜各種形狀槽,以及銑削平面和成形面等。隨著技術的不斷進步,一種新型的組合機床——柔性組合機床越來越受到人們的青睞,它應用多位主軸箱、可換主軸箱、編碼隨行夾具和刀具的自動更換,配以可編程序控制器(PLC)、數(shù)字控制(NC)等,能任意改變工作循環(huán)控制和驅(qū)動系統(tǒng),并能靈活適應多品種加工的可調(diào)可變的組合機床。另
4、外,近年來組合機床加工中心、數(shù)控組合機床、機床輔機(清洗機、裝配機、綜合測量機、試驗機、輸送線)等在組合機床行業(yè)中所占份額也越來越大。 夾具方面,隨著科學技術的進步和市場需求的變化,現(xiàn)代機械制造業(yè)得到了較快的發(fā)展。多品種、小批量生產(chǎn)方式將成為今后的主要生產(chǎn)形式,制造系統(tǒng)正向著柔性化、集成化、智能化方向發(fā)展,機床愈來愈多地采用先進的技術,加工效率不斷地提高。機械產(chǎn)品的加工精度日益提高,高精度的機床大量出現(xiàn) 。為了適應生產(chǎn)發(fā)展的需要 ,機床夾具正在向柔性化、高效化、自動化、精密化、標準化方向發(fā)展。 1.3 課題由來及基本條件 a)設計內(nèi)容 設計一臺變速箱殼體雙面組合機床; 總體設計:制定
5、工藝方案,確定機床配置型式及結(jié)構(gòu)方案,“三圖一卡”設計; 部件設計:組合機床夾具設計 b)設計依據(jù) 被加工零件:變速箱殼體(附零件圖) 工件材料:HT150 加工內(nèi)容:一側(cè)鉆削8φ8.5深24的孔,φ11.9深25的孔;另一側(cè)6φ8.5深24的孔,2φ9.8深18.5的孔。 生產(chǎn)綱領:大批大量 2組合機床總體設計 2.1 總體方案論證 本設計的加工對象為變速箱殼體,材料是HT150,硬度HBS170-241,重量21Kg,屬于箱體零件,結(jié)構(gòu)復雜。 2.1.1 加工內(nèi)容及要
6、求 根據(jù)先粗后精、先基準面后其它表面、先主要表面后次要表面的機械加工工序安排的設計原則,對變速箱殼體的工藝路線作如下設計: a)粗銑底面; b)粗銑左、右端面; c)粗銑前、后端面; d)半精銑底面; e)半精銑左、右端面; f)半精銑前、后端面; g)粗鏜孔; h)精鏜孔; i)鉆左、右面的孔; j)攻絲。 本道工序為第9道工序,主要加工左右二面上的17個孔。具體加工內(nèi)容是:左側(cè)面9個孔,鉆削8φ8.5深24的孔,1φ11.9深25的孔;鉆右側(cè)面上8個孔,鉆削6φ8.5深24的孔,2φ9.8深18.5的孔 2.1.2 機床配置型式選擇 根據(jù)任務書的
7、要求:設計的組合機床要滿足加工要求、保證加工精度;盡可能用通用件、以降低成本;各動力部件用電氣控制。因此根據(jù)任務書要求和變速箱殼體的特點初定兩種設計方案: a)臥式組合機床 特點:臥式組合機床重心低、振動小運作平穩(wěn)、加工精度高、占地面積大。 b)立式組合機床 特點:立式組合機床重心高、振動大、加工精度低、占地面積小。 通過以上的比較,考慮到臥式床身振動小,裝夾方便等優(yōu)點,選用臥式組合機床。 2.1.3 定位基準的選擇 組合機床是針對某種零件或零件某道工序設計的。正確選擇定位基準,是確保加工精度的重要條件,同時也有利于實現(xiàn)最大限度的集中工序。本機床加工時采用的定位方式是以
8、底面為定位基準面,限制三個自由度;用兩個擋鐵限制兩個自由度;在左側(cè)有一個支承針,限制剩下的一個自由度。 2.1.4滑臺型式的選擇 本組合機床采用的是液壓滑臺。與機械滑臺相比較,液壓滑臺具有如下優(yōu)點:在相當大的范圍內(nèi)進給量可以無級調(diào)速;可以獲得較大的進給力;由于液壓驅(qū)動,零件磨損小,使用壽命長;工藝上要求多次進給時,通過液壓換向閥,很容易實現(xiàn);過載保護簡單可靠;由行程調(diào)速閥來控制滑臺的快進轉(zhuǎn)工進,轉(zhuǎn)換精度高,工作可靠。但采用液壓滑臺也有其弊端,如:進給量由于載荷的變化和溫度的影響而不夠穩(wěn)定;液壓系統(tǒng)漏油影響工作環(huán)境,浪費能源;調(diào)整維修比較麻煩。本課題的加工對象是變速箱殼體左、右兩個面
9、上的17個孔,位置精度和尺寸精度要求較高,因此采用液壓滑臺。 由此,根據(jù)已定的工藝方案和機床配置形式并結(jié)合使用及修理等因素,確定機床為臥式兩面單工位液壓傳動組合機床,液壓滑臺實現(xiàn)工作進給運動,選用配套的動力箱驅(qū)動主軸箱鉆孔、鏜孔主軸。 . 2.2 確定切削用量及選擇刀具 2.2.1 切削用量的選擇 對于17個被加工孔,采用查表法選擇切削用量,從[1]P130表6-11中選取。由于鉆孔、鏜孔的切削用量還與孔深度有關,隨孔深的增加而逐漸遞減,其遞減值按[1]P131表6-12選取。降低進給量的目的是為了減小軸向切削力,以避免鉆頭、鏜頭折斷??咨疃容^大時,由于冷卻排屑條件都較差,是刀具壽命
10、有所降低。降低切削速度主要是為了提高刀具壽命,并使加工較深孔時鉆頭、鏜頭的壽命與加工其他淺孔時鉆頭、鏜頭的壽命比較接近。 A. 對左面上9個孔的切削用量的選擇 a)鉆孔1~孔8 8Φ8.5,盲孔, l=24mm 由d>6~12,硬度大于170~241HBS,選擇v=10~18m/min ,f>0.1~0.18mm/r,又d=8.5mm,取定v=13.2m/min , f=0.122mm/r,則由 (2-1) 得:n=100013.2/8.5π=493r/mi
11、n b)鉆孔9 1Φ11.9,盲孔,l=25mm 由d>6~12,硬度大于170~241HBS,選擇v=10~18m/min, f>0.1~0.18mm/r,又d=11.9mm,取定v=13.2m/min , f=0.17mm/r, 則n=100013.2/11.9π=352r/min B. 對右面上8個孔的切削用量的選擇 a)鉆孔1、2、4、5、6、8 6Φ8.5,盲孔,l=24mm 由d>6~12,硬度大于170~241HBS,選擇v=10~18m/min, f>0.1~0.18mm/r,又d=8.5mm,取定v=12.8m/min, f=0.135mm/r, 則n
12、=100012.8/8.5π=480r/min b)鉆孔3、7 2Φ9.8,盲孔,l=18.5mm 由于精鏜,加工材料為鑄鐵,硬度大于170~241HBS,選擇v=10~18m/min, f≤0.1~0.18mm/r,又d=9.8mm,取定v=13m/min, f=0.15mm/r, 則n=100013/9.8π=422r/min (孔的編號見被加工零件工序圖) 2.2.2計算切削力、切削扭矩及切削功率 鉆孔:根據(jù) 表6-20中公式 式中, F—切削力(N);T—切削轉(zhuǎn)矩(N?㎜);P—切削功率(Kw); v—切削速度(m
13、/min);f—進給量(mm/r);D—加工(或鉆頭)直徑(mm); HB—布氏硬度,,在本設計中,, ,得HB=217.3。 由以上公式可得: 左面 單根 1~8軸 F=1036.9N T=2736.65N?mm P=0.139Kw 9軸 F=1892.85N T=6762.9N?mm P=0.2453Kw 右面 單根 1、2、4、5、6、8軸 F=1124.3N T=2967.56N?mm P=0.1461Kw 單根 3、7軸 F=1410N T=4230.95N?mm P=0.1835Kw
14、 (軸編號與孔編號相對應) 總的切削功率:即求各面上所有軸的切削功率之和 左面 Pw=80.139+0.2453=1.3573Kw 右面 Pw=60.1461+20.1835=1.2436Kw 實際切削功率 根據(jù)[1],P=(1.5~2.5)Pw,因為是多軸加工,故取定P=2Pw 則 P左=21.3573=2.7146Kw P右=21.2436=2.4872Kw 2.2.3 刀具結(jié)構(gòu)的選擇 根據(jù)工藝要求及加工精度的要求, 17個加工孔的刀具采用標準錐柄麻花鉆. 2.3 總體設計——“三圖一卡” 2.3.1被加工零
15、件工序圖 被加工零件工序圖是根據(jù)制定的工藝方案,表示所設計的組合機床(或自動線)上完成的工藝內(nèi)容,加工部位的尺寸、精度、表面粗糙度及技術要求,加工用的定位基準、夾壓部位以及被加工零件的材料、硬度和在本機床加工前加工余量、毛坯或半成品情況的圖樣。除了設計研制合同外,它是組合機床設計的具體依據(jù),也是制造、使用、調(diào)整和檢驗機床精度的重要文件。 2.3.2 加工示意圖 零件加工的工藝方案要通過加工示意圖反映出來。加工示意圖表示被加工零件在機床上的加工過程,刀具、輔具的布置狀況以及工件、夾具、刀具等機床各部件間的相對位置關系,機床的工作行程及工作循環(huán)等。 A. 刀具的選擇 刀具直徑的選
16、擇應與加工部位尺寸、精度相適應??爪?.5選擇刀具Φ8.5G7;孔Φ11.9選擇刀具Φ11.9G7;孔Φ9.8選擇刀具Φ9.8G7。 B. 導向結(jié)構(gòu)的選擇 組合機床鉆孔時,零件上孔的位置精度主要是靠刀具、接桿的導向裝置來保證的。導向裝置的作用是:保證刀具相對工件的正確位置;保證刀具相互間的正確位置;提高刀具系統(tǒng)的支承剛性。 本課題中加工9個孔時導向表面旋轉(zhuǎn)線速度均小于20m/min,所以導向裝置選用固定導套。 對于加工Φ8.5孔,選擇的導套尺寸為:D=15mm,D1=22mm,D2=26mm,L=25mm,l=8mm,l1=3㎜,e=18.5mm,配用的螺釘M6。 對于加工Φ
17、11.9孔,選擇的導套尺寸為:D=18mm,D1=26mm,D2=30m,L=25mm,l=8mm,l1=3㎜,e=22mm,配用的螺釘M8。 對于加工Φ9.8孔,選擇的導套尺寸為:D=15mm,D1=22mm,D2=26mm,L=25mm,l=8mm,l1=3㎜,e=18.5mm,配用的螺釘M6。 C. 確定主軸、尺寸、外伸尺寸 在該課題中,主軸用于鉆孔、鏜孔,選用滾珠軸承主軸。又因為浮動卡頭與刀具剛性連接,所以該主軸屬于長主軸。故本課題中的主軸均為滾珠軸承長主軸。 根據(jù)由選定的切削用量計算得到的切削轉(zhuǎn)矩T,由公式
18、 (2-5) 式中,d—軸的直徑(㎜); T—軸所傳遞的轉(zhuǎn)矩(Nm); B—系數(shù),本課題中主軸為非剛性主軸,取B=6.2。 由公式可得: 左面 1~8軸 d=14.2㎜ 9軸 d=17.78㎜ 右面 1、2、4、5、6、8軸 d=14.47㎜ 3、7軸 d=15.8㎜ 考慮到安裝過程中軸的互換性、安裝方便等因素,除右面2、6軸徑取為15㎜外,其余15根主軸軸徑均取為20㎜。 根據(jù)主軸類型及初定的主軸軸徑,查[9]P44表3-6可得到主軸外伸尺寸及接桿莫氏圓錐號。主軸軸徑
19、d=15㎜時,主軸外伸尺寸為:,L=85㎜;接桿莫氏圓錐號為1。主軸軸徑d=20㎜時,主軸外伸尺寸為:,L=115㎜;接桿莫氏圓錐號為1。 D. 動力部件工作循環(huán)及行程的確定 a) 工作進給長度的確定 工作進給長度,應等于加工部位長度L(多軸加工時按最長孔計算)與刀具切入長度和切出長度之和。切入長度一般為5~10㎜,根據(jù)工件端面的誤差情況確定。鉆孔時切出長度按表3-7 (2-6) 計算式中,d為鉆頭直徑。兩個面上鉆孔時的工作進給長度見下表: 表2-1 兩個面上鉆孔的工作進給長度 L d
20、左主軸箱 47 8 8.5 10 65 右主軸箱 10.2 5 11.5 8 23.2 b) 快速進給長度的確定 快速進給是指動力部件把刀具送到工作進給位置。初步選定兩個主軸箱上刀具的快速進給長度為115㎜。 c) 快速退回長度的確定 快速退回長度等于快速進給和工作進給長度之和。由已確定的快速進給和工作進給長度可知,兩面快速退回長度為150㎜。 d) 動力部件總行程的確定 動力部件的總行程為快退行程與前后備量之和。兩面的前備量取30㎜,后備量取190㎜,則總行程為400㎜。 2.3.3 機床尺寸聯(lián)系總圖 A. 選擇動力部件 a) 動力滑臺
21、型號的選擇 根據(jù)選定的切削用量計算得到的單根主軸的進給力,按式 (2-7) 式中,—各主軸所需的 向切削力,單位為N。 則 左主軸箱 右主軸箱 實際上,為克服滑臺移動引起的摩擦阻力,動力滑臺的進給力應大于。又考慮到所需的最小進給速度、切削功率、行程、主軸箱輪廓尺寸等因素,為了保證工作的穩(wěn)定性,由表5-1,左、右兩面的液壓滑臺均選用1HY40A-I型。臺面寬400mm,臺面長800mm,行程長400mm,滑臺及滑座總高320mm,滑座長1240mm,允許最大進給力20000N,快速行程速度
22、8m/min,工進速度12.5~500mm/min。 b) 動力箱型號的選擇 由切削用量計算得到的各主軸的切削功率的總和,根據(jù)公式 (2-8) 式中, —消耗于各主軸的切削功率的總和(kW); —多軸箱的傳動效率,加工黑色金屬時取0.8~0.9,加工有色金屬時取0.7~0.8;主軸數(shù)多、傳動復雜時取小值,反之取大值。本課題中,被加工零件材料為灰鑄鐵,屬黑色金屬,又主軸數(shù)量較多、傳動復雜,故取。 左主軸箱: 則 右主軸箱: 則
23、 根據(jù)液壓滑臺的配套要求,滑臺額定功率應大于電機功率的原則,查表5-38得出動力箱及電動機的型號 表2-2 動力箱及電動機型號 動力箱型號 電動機型號 電動機功率(kW) 電動機轉(zhuǎn)速(r/min) 輸出軸轉(zhuǎn)速(r/min) 左主軸箱 1TD40I Y132S-4 5.5 1440 720 右主軸箱 1TD40I Y132S-4 5.5 1440 720 c) 配套通用部件的選擇 側(cè)底座CC401,其高度H=560㎜,寬度B=600㎜,長度L=1350㎜。 B. 確定機床裝料高度H 裝料高度是指機床上工件的定位基
24、準面到地面的垂直距離。本課題中,工件最低孔位置,主軸箱最低主軸高度,所選滑臺與滑座總高,側(cè)底座高度,夾具底座高度,中間底座高度,綜合以上因素,該組合機床裝料高度取H=880㎜。 a) 確定主軸箱輪廓尺寸 主要需確定的尺寸是主軸箱的寬度B和高度H及最低主軸高度。主軸箱寬度B、高度H的大小主要與被加工零件孔的分布位置有關,可按下式計算: (2-9) (2-10) 式中,b—工件在寬
25、度方向相距最遠的兩孔距離(㎜); —最邊緣主軸中心距箱外壁的距離(㎜); h—工件在高度方向相距最遠的兩孔距離(㎜); —最低主軸高度(㎜)。 其中,還與工件最低孔位置()、機床裝料高度(H=880㎜)、滑臺滑座總高()、側(cè)底座高度()、滑座與側(cè)底座之間的調(diào)整墊高度()等尺寸有關。對于臥式組合機床, h1要保證潤滑油不致從主軸襯套處泄漏箱外,通常推薦,本組合機床按式 (2-11) 計算,得: 。 b=180mm,h=242.78mm,取,則求出主軸箱輪廓尺寸: 根據(jù)上述計算
26、值,按主軸箱輪廓尺寸系列標準,最后確定主軸箱輪廓尺寸為BH=500㎜500㎜。 2.3.4 機床生產(chǎn)率計算卡 已知:工作行程為150㎜ 進刀量為8000㎜/min 輔助時間夾緊0.5min 機動時間0.582min 裝料時間0.5min 卸料時間0.5min 單件工時2.158min/件 A.理想生產(chǎn)率Q(件/h) 理想生產(chǎn)率是指完成年生產(chǎn)綱領(包括備品及廢品率)所要求的機床生產(chǎn)率。用公式 (2-12)
27、計算,式中, N—年生產(chǎn)綱領(件),本課題中N=55000件; —全年工時總數(shù),本課題以單班7小時計,則。 則 B.實際生產(chǎn)率Q1(件/h) 實際生產(chǎn)率是指所設計的機床每小時實際可生產(chǎn)的零件數(shù)量。即公式 (2-13) 式中,—生產(chǎn)一個零件所需時間(min)。 則 件/h C.機床負荷率 機床負荷率為理想生產(chǎn)率與實際生產(chǎn)率之比。即公式
28、 (2-14) 則 根據(jù)以上算得的數(shù)據(jù),填寫機床生產(chǎn)率計算卡,詳見表2-3。 表2-3 機床生產(chǎn)率計算卡 被加工零件 圖號 毛胚種類 鑄 件 名稱 變速箱殼體 毛胚重量 21kg 材料 HT150 硬 度 170~241HBS 工序名稱 鉆兩側(cè)面 工序號 序 號 工步名稱 被加 工零 件數(shù) 加工 直徑 mm 加工 長度 mm 工作 行程 mm 切削 速度 m/min 轉(zhuǎn)速 r/min 每轉(zhuǎn) 進
29、給量 mm/r 每分鐘 進給量 mm/min 工 時 min 機動 時間 輔助 時間 共計 1 裝入工件 1 0.5 2 工件定位夾緊 0.5 3 左動力部件 快進 115 5000 0.023 鉆8.5孔 8.5 24 35 13.2 493 0.122 60.164 0.582 鉆11.9孔 11.9 25 35 13.2 352 0.
30、17 59.84 0.585 死擋鐵停留 0.02 快退 150 5000 0.03 4 右動力部件 快進 115 5000 0.023 鉆8.5孔 8.5 24 35 12.8 480 0.135 64.8 0.540 鉆9.8孔 9.8 25 35 13 422 0.15 63.3 0.553 死擋鐵停留
31、 0.02 快退 150 5000 0.03 5 松開工件 0.2 6 卸下工件 0.3 備 注 單位工時 2.158min 機床實際生產(chǎn)率Q1 27.80件/h 機床理想生產(chǎn)率Q 23.4件/h 負荷率 84.2% 3 組合機床夾具設計 3.1夾具設計的基本要求和步驟 3.1.1夾具設計的基本要求 A.提高生產(chǎn)率、降低成本 夾具設計方案應與生產(chǎn)綱領相適
32、應。在大批量生產(chǎn)時,為了縮短輔助時間,提高生產(chǎn)率,盡量采用快速、高效的結(jié)構(gòu)和自動控制裝置;在批量生產(chǎn)和滿足夾具功能的前提下,盡量使夾具結(jié)構(gòu)簡單,容易制造,以降低夾具的制造成本。 B.保證工件的加工精度 夾具設計的最基本要求是保證工件的加工精度。關鍵是確定定位方案、夾緊方案,和合理地設計夾具的尺寸、公差和技術要求,必要時應進行誤差的分析和計算。 C.便于排屑 夾具的排屑是一個很重要的問題,切屑積集在夾具中,會破壞工件正確的定位;切屑帶來的大量熱量會引起夾具和工件的熱變形,影響加工質(zhì)量;切屑的的清掃又會增加輔助時間,降低生產(chǎn)率。切屑積集嚴重時,還會造成設備事故或工傷事故。因此,在
33、夾具設計時排屑問題必須給予充分的注意。 D.操作方便、省力和安全 夾具的操作要盡量做到方便、省力,盡可能采用氣動、液壓及其他機械化夾緊裝置、以減輕工人的勞動強度,控制好夾緊力。夾具操作位置應符合操作工人的習慣,應有安全保護裝置,確保使用安全。 E.有良好的結(jié)構(gòu)工藝性 夾具的結(jié)構(gòu)應簡單、合理,便于加工、裝配、檢驗和維修,盡可能多選用標準部件和標準元件。 夾具設計通??梢栽趨㈤営嘘P資料的情況下,按加工要求設計方案,繪制圖樣,經(jīng)修改確定夾具的結(jié)構(gòu)。 3.1.2 夾具設計的步驟 A.設計前的準備 分析產(chǎn)品零件圖及裝配圖,分析零件的作用、形狀、結(jié)構(gòu)特點、材料和技術要求;分
34、析零件的加工工藝規(guī)程,工藝裝備設計任務書,對任務書所提出的要求進行可行性研究;了解所用機床的規(guī)格、性能、精度以及與夾具選擇動力部件 B.方案設計 在分析各種原始資料的基礎上,確定夾具的類型、定位設計、夾緊方式、導向方案 、連接方式、總體布局和夾具的結(jié)構(gòu)形式。繪制方案設計圖,進行工序精度分析,對動力夾緊裝置進行夾緊力的計算。 C.審核 檢查夾具的各項功能是否符合設計要求。 D.總體設計 根據(jù)所定方案繪制夾具裝配圖,應將夾具的工作原理、結(jié)構(gòu)和各種元件的裝配關系表達清楚。用雙點劃線繪制工件外形輪廓。合理選擇材料,標注尺寸、公差和技術要求。 E.夾具零件設計 F.夾具的裝配、調(diào)試和驗證
35、 3.2 定位方案的確定 3.2.1 零件的工藝性分析 夾具是組合機床的重要組成部分,是根據(jù)機床的工藝和結(jié)構(gòu)方案的具體要求而專門設計的。它用于實現(xiàn)被加工零件的準確定位、夾壓、刀具的導向以及裝卸工件時的限位。 變速箱殼體材料為HT150,其硬度為170~241HBS,在本工序之前工件主要表面已加工完畢。本道工序一側(cè)鉆削8φ8.5深24的孔,φ11.9深25的孔;另一側(cè)6φ8.5深24的孔,2φ9.8深18.5的孔。 3.2.2 定位方案論證 箱體零件的定位方案一般有兩種,“一面兩銷”和“三平面”定位方法。 A.“一面兩銷”的定位方法 它的特點是:可以簡便地消除工件的六個
36、自由度,使工件獲得穩(wěn)定可靠定位。有同時加工零件五個表面的可能,既能高度集中工序,又有利于提高各面上孔的位置精度。“一面雙孔”可作為零件從粗加工到精加工全部工序的定位基準,使零件整個工藝過程基準統(tǒng)一,從而減少由基準轉(zhuǎn)換帶來的累積誤差,有利于保證零件的加工精度。同時,使機床各個工序(工位)的許多部件實現(xiàn)通用化,有利于縮短設計、制造周期,降低成本。易于實現(xiàn)自動化定位、夾緊,并有利于防止切削落于定位基面上。 B.“三平面”定位方法 它的特點是: 可以簡便地消除工件的六個自由度,使工件獲得穩(wěn)定可靠定位。有同時加工零件兩個表面的可能,能高度集中工序。 被加工零件為變速箱殼體屬箱體類零件,本工序加工
37、為雙面加工零件,加工工序集中、精度要求高,故選用“一面兩銷”定位方法,采用“一面兩銷”定位方法,能夠保證工件的位置精度要求,同時便于工件裝夾,又有利于夾具的設計與制造。 3.2.3 誤差分析 用夾具裝夾工件進行機械加工時,其工藝系統(tǒng)中影響工件加工精度的因素很多,與夾具有關的因素有: A. 定位誤差; B. 對刀誤差; C. 夾具的安裝誤差; D. 夾具誤差; E. 在機械加工工藝系統(tǒng)中,影響加工精度的其它因素綜合稱為加工方法誤差; F. 上述各項誤差均導致刀具相對工件的位置不精確而形成總的加工誤差∑Δ。 具體誤差分析如下: A. 定位誤差 a) 基準不重合誤差
38、 基準不重合誤差是由于定位基準和工序基準不重合而引起的工序基準相對于定位基準在加工尺寸上的最大位置變動范圍。在本設計中,由于定位誤差和工序基準是重合的,所以基準不重合誤差= 0。 b) 基準位移誤差 基準位移誤差是由于定位元件和定位基面本身的誤差而引起的定位基準在加工尺寸上的誤差。 當支承面即工件底面對夾具的安裝基準(底面)有平行度誤差,被加工孔的定位誤差?。簃m =+= 0.02mm B. 對刀誤差 因為刀具相對于對刀或?qū)蛟奈恢貌痪_而造成的加工誤差,稱為對刀誤差。 鉆套導向孔尺寸φ8.5G7(),鉆頭尺寸為φ8.5h9()對刀誤差為鉆頭于導向孔的最大的間隙:
39、 C. 夾具的安裝誤差 因夾具在機床上的安裝不精確而造成的加工誤差,稱為夾具的安裝誤差。 夾具的安裝基面為平面,因而沒有安裝誤差,=0 D. 夾具誤差 因夾具上定位元件、對刀或?qū)蛟鞍惭b基面三者之間(包括導向元件與導向元件之間)的位置不精確而造成的加工誤差,稱為夾具誤差,夾具誤差大小取決于夾具零件的加工精度的夾具裝配時的調(diào)整和修配精度。 夾具誤差主要包括定位元件相對于安裝基準的尺寸或位置誤差;定位元件相對于對刀或?qū)蛟ò▽蛟g)的尺寸或位置誤差;導向元件相對于安裝基準的尺寸或位置誤差。 =0.02mm 、與在公差上兼容,只需計算其中較大的一項即可
40、。 =0.02mm E. 加工方法誤差 加工方法誤差是指在切削加工過程中,因機床、刀具質(zhì)量、工件材質(zhì)以及由于切削力、切削熱的作用而引起的工藝系統(tǒng)彈性變形、熱變形等因素使加工表面位置發(fā)生變化,從而造成的加工尺寸誤差。因該項誤差影響因素很多,又不便于計算,所以常根據(jù)經(jīng)驗為它留出工件公差的。計算時可設 (3-1) 式中:——工件位置公差取0.30mm = 3.2.4 校核加工精度 工件在夾具中加工時,總加工誤差為上述各項誤差之和。由于上述誤差均為獨立隨機誤差,應用概
41、率法相加,根據(jù)文獻[7]工件加工精度的條件為: (3-2) = 0.118mm < = 0.30mm 即工件總加工誤差應不大于工件的加工尺寸公差,由以上得知,本夾具完全可以保證加工精度。 為保證夾具有一定的使用壽命,防止夾具因磨損而過早報廢,在分析計算工件加工精度時需留出一定精度儲備量,因此將上式改為: ≤- 或 =- ≥
42、0 (3-3) 當≥0時夾具能滿足加工要求,根據(jù)以上得: =-=0.30-0.118=0.182≥0 所以夾具完全可以滿足加工所要的要求。 3.3導向裝置 導向裝置的作用在于保證刀具對于工件的正確位置;保證各刀具相互間的正確位置和提高刀具系統(tǒng)的支承剛性。 變速箱殼體的兩面鉆組合機床的刀具導向裝置是設計在夾具支架上的,由于是大批生產(chǎn),所以采用可換式導套,是刀具在鉆套內(nèi)工作的。 鉆套的主要參數(shù)包括:鉆套的直徑和公差配合,鉆套的長度,鉆套至工件端面的距離。 鉆套的配合間隙對于孔的位置精度有較大的影響。為了提高加工的精度,應選擇較緊的配合。 變速箱殼
43、體兩面鉆孔是在精密的導套中進行的,因此要求較高的位置精度,達到0.05mm,而且導套應盡量接近被加工表面,力求選用較高的精度和較緊的配合。 導套結(jié)構(gòu)如圖3-1所示。 圖3-1 導套結(jié)構(gòu)圖 固定鉆套的尺寸可查文獻[2]的175頁的表8-4: 對于加工Φ8.5孔,選擇的導套尺寸為: ,,,。 配合尺寸為: , 配用的螺釘M6 對于加工Φ9.8孔,選擇的導套尺寸為: ,,,。 配合尺寸為: , 配用的螺釘M6 對于加工Φ11.9孔,選擇的導套尺寸為: ,,,。 配合
44、尺寸為: , 配用的螺釘M8 3.4 夾緊方案的確定 3.4.1 夾緊裝置的確定 A.夾緊裝置的組成 本設計中夾緊裝置采用氣壓夾緊裝置,由氣源裝置、中間傳力機構(gòu)、夾緊元件三部分組成。其組成部分的相互關系,如圖3-2的方框圖所示。 氣壓 夾緊裝置 氣源裝置 中間傳力機構(gòu)
45、 夾緊元件 工件 圖3-2夾緊裝置組成的方框圖 B.夾緊裝置設計的基本要求 a)夾緊過程中,不改變工件定位后占據(jù)的正確位置。 b)夾緊力的大小要可靠和適當,既要保證工件在整個加工過程中位置穩(wěn)定不變,振動小,又要使工件不產(chǎn)生于過大的夾緊變形。 c)夾緊裝置的自
46、動化和復雜程度應與生產(chǎn)綱領相適應,在保證生產(chǎn)率的前提下,其結(jié)構(gòu)要力求簡單,以便于制造和維修。 d)夾緊裝置的操作應當方便、安全、省力。 C.夾緊裝置的選擇 通常應用的夾緊裝置有氣壓裝置和液壓裝置兩種,各有其優(yōu)越性,要根據(jù)實際情況來選擇用哪種裝置。 a.液壓裝置 液壓裝置的特點是: a)液壓油油壓高、傳動力大,在產(chǎn)生同樣原始作用力的情況下,液壓缸的 結(jié)構(gòu)尺寸比氣壓小了許多。 b)液壓油的不可壓縮性可使夾具剛度高,工作平穩(wěn)、可靠。 c)液壓傳動噪聲小,勞動條件比氣壓的好。 但是,油壓高容易導致漏油,液壓元件的材質(zhì)和制造精度的要求高,故夾具成本高。
47、 b.氣壓裝置 氣壓裝置以壓縮空氣為力源,應用比較廣泛,與液壓相比有以下優(yōu)點: a)動作迅速,反應快。氣壓為0.5時,氣缸活塞速度為1~10,夾具每小時可連續(xù)松夾上千次。 b)工作壓力低(一般為0.4~0.6)。傳動結(jié)構(gòu)簡單,對裝置所用材料及制造精度要求不高,制造成本低。 c)空氣粘度小,在管路中的損失較少,便于集中供應和遠距離輸送,易于集中操縱或程序控制等。 d)空氣可就地取材,容易保持清潔,管路不易堵塞,也不會污染環(huán)境,具有維護簡單,使用安全、可靠、方便等特點。 主要缺點是空氣壓縮性大,夾具的剛度和穩(wěn)定性較差;在產(chǎn)生相同原始作用力的條件下,因工作壓力低,其動力裝置的結(jié)構(gòu)尺寸大
48、。此外,還有較大的排氣噪聲。 通過對以上兩種夾緊裝置優(yōu)缺點的比較,結(jié)合加工工件的精度要求、工人的勞動強度和環(huán)境要求、企業(yè)的實際情況,本設計中夾緊裝置采用氣壓夾緊裝置。 3.4.2 夾緊力的確定 A.夾緊力確定的基本原則 a.夾緊力的方向 夾緊力的方向應有助于定位穩(wěn)定,主夾緊力應朝向主要定位基面。夾緊力的方向應有利于減小夾緊力。夾緊力的方向應是工件剛度較高的方向。 b.夾緊力的作用點 夾緊力的作用點應落在定位元件的支承范圍內(nèi)。夾緊力的作用點應選在工件剛度較高的部位。夾緊力的作用點應盡量靠近加工表面。 B.夾緊方案 根據(jù)以上要求及原則,工件屬于箱體類零件,夾緊力的方向應垂直于最重
49、要的定位基面是底面,并將工件壓向該面,而不宜與其他方面進行夾緊。由于工件為薄壁件,易受力變形,故采用多點同時壓向工件,均勻分布壓緊力,起到減少受力變形的效果。夾緊力為氣壓缸驅(qū)動。用推桿將壓力傳遞至板,然后由壓板將壓力分散到工件壓緊表面,從而將工件壓緊。 C.夾緊力的預算: 根據(jù)工件所受切削力、夾緊力的作用情況,找出加工過程中對夾緊最不利的狀態(tài),來確定夾緊力。 根據(jù)文獻[2]P19頁查得夾緊力的計算公式如下 (3-4) 式中 ——安全系數(shù); ——切削力; ——壓板和工件表面間的摩擦系數(shù); ——工件和定位
50、支承塊間的摩擦系數(shù)。 根據(jù)文獻[2]的表2.2-1查得安全系數(shù)按下式計算 (3-5) 式中,~為各種因素的安全系數(shù), ——考慮工件材料及加工余量均勻性的基本安全系數(shù),取=1.5; ——加工性質(zhì),取; ——刀具鈍化程度,取=1.15; ——切削特點,取=1.2 ——夾緊力的穩(wěn)定性,?。? ——夾緊時的位置 ,??; ——僅有力矩使工件回轉(zhuǎn)時工件與支承面的接觸情況,取=1.0。 查文獻[2]表3-34摩擦系數(shù),均為0.16。 由于,右動力箱快進距離較左動力箱短,因此,先進入工進階
51、段。右動力箱的鉆削力方向指向夾具體左面的定位面,鉆削力不影響工件定位。當左動力箱也進入工進時,兩方向的鉆削力相互抵消一部分,左動力箱鉆削力稍大,因此,夾緊力只需要消除這部分力對工件定位的影響即可。 根據(jù)2.2.2節(jié)切削力的計算結(jié)果,取P=-=2714.6-2487.2=227.4N,由公式(3- 6)得: (3- 6) = =1776.5625N 3.4.3 氣缸的選擇 氣缸的工作壓力取決于工作氣壓和氣缸的工作面積。工廠采同一氣源,則其氣壓也就相對穩(wěn)定,其工作氣壓為1.0。根
52、據(jù)文獻[8]則氣缸直徑: D= (3-7) 式中:p——氣缸工作壓力(Pa) ——氣缸的機械效率(取0.80) ——氣缸輸出推力() ——氣缸直徑() 氣缸輸出推力應大于等于實際所需的加緊力 則取 P=1776.5625N 代入公式(3-7)得: D= = =0.053m 本設計所用氣缸采用通用件。根據(jù)文獻[3]的表3.4-18,選用氣缸直徑為100,其工作推力產(chǎn)生的夾緊力可達到3100;根據(jù)文獻[3] 查表3.4-18得另一輔助定位氣缸直徑為50。推力可達到1000。 3.5 夾具體的設計
53、 夾具體是用來將夾具的各個部分聯(lián)結(jié)成整體的元件,它是夾具上最大的和最復雜的元件。在它上面要安裝定位元件、夾緊裝置、刀具引導件以及其它各種裝置和元件。此外,在夾具體上還應有夾具在機床上安裝用的定位部分,以保證夾具在機床上獲得所需的相互位置,夾具體也是承受負荷最大的元件,承受著工作時的切削力、夾緊力等。 夾具體設計的基本要求有: a)有適當?shù)木群统叽绶€(wěn)定性。 b)有足夠的強度和剛度。 c)結(jié)構(gòu)工藝性好。 d)排屑方便。 e)保證裝卸工件方便。 f)在機床上安裝穩(wěn)定可靠。 本設計方案中的夾具體是由左右鉆模板與夾具頂板構(gòu)成的框架式夾具體,采用機械聯(lián)結(jié),具有良好的剛度,材料為HT150
54、,基本尺寸:702613370mm,各安裝面經(jīng)銑削達到相應精度要求,左右鉆模板的平行度不大于0.02。底部設計排屑裝置,具體見夾具裝配圖BSXCT-03-03。 3.6 夾具三維設計 3.6.1 三維建模及三維軟件介紹 三維建模從過程上講就是在空間建立立體模型的一種方法。從結(jié)果上來講,簡單的說就是建立的模型具有空間感的,能看到上下前后左右的?!熬S”是幾何學及空間理論的基本概念。構(gòu)成空間的每一個因素就叫做一維,普通的空間就是三維的。三維建?;诙S建??梢允箻?gòu)造的模型更具立體感和直觀感,便于設計和加工。 目前,應用比較廣泛的三維軟件有Pro/e、SolidEdge、UG等。設計中采用的三
55、維軟件是由美國PTC公司研發(fā)的Pro/e wildfire3.0軟件。該軟件包括了在工業(yè)設計和機械設計等方面的多項功能,還提供了目前所能達到的最全面、集成最緊密的產(chǎn)品開發(fā)環(huán)境。 3.6.2 基于三維的夾具設計過程 通過前面的計算和校核,可以得出夾具的尺寸大小,而且通過裝配圖及各零件圖的數(shù)據(jù),可以在Pro/e 軟件中畫出各零件的三維模型,最后經(jīng)組裝后,可得到夾具的三維造型圖。如圖3-3、3-4、3-5、3-6、3-7所示。 圖3-3夾具總裝配圖(1) 圖3-4夾具總裝配圖(2) 圖3-5夾具總
56、裝配圖(3) 圖3-6夾具體裝配圖 圖3-7夾具右支架裝配圖 4 結(jié)論 本次課題設計變速箱殼體鉆孔組合機床采用單工位臥式雙面鉆削的配置式,在加工生產(chǎn)線上同時完成了17個孔的加工,大大提高了生產(chǎn)效率,從而降低了零件的加工成本。本機床夾具根據(jù)被加工零件的結(jié)構(gòu)采用了手動伸縮式定位銷,滿足工件定位方便可靠的原則。夾緊裝置采用氣壓夾緊,自動化程度高、操作簡單、效率高、夾緊可靠,減輕了工人勞動強度,并且使用安全可靠、維護簡單;夾具體為框架式結(jié)構(gòu),有良好的剛性,有利于鉆孔精度的保持,刀具導向采用可換鉆套,則保證了鉆孔時的加工精度
57、不因鉆套的磨損而降低。 本組合機床設計合理,符合實際應用,滿足加工要求,且絕大部分采用了通用部件和標準件,制造成本低,機床操作簡單,設備調(diào)整、維修方便。同時,本機床設計也有一些不足之處需要加以改進如:機床占地面積大、機床結(jié)構(gòu)復雜;氣壓機構(gòu)工作壓力低,其動力裝置的結(jié)構(gòu)尺寸大等。 參 考 文 獻 [1] 謝家瀛主編.組合機床設計簡明手冊[M].北京:機械工業(yè)出版社,1999 [2] 徐鴻本. 機床夾具設計手冊[M].遼寧科學技術出版社,2004. [3] 徐發(fā)仁主編.氣壓液壓機床夾具設計M].上
58、海:上??茖W技術出版社,1982. [4] 楊黎明.機床夾具設計手冊[M].北京:國防工業(yè)出版社,1996. [5] 李 云.機械制造工藝及設備設計指導手冊[M].北京:機械工業(yè)出版社,1993. [6] 沈陽工業(yè)大學,大連鐵道學院.組合機床設計[M].上海:上??萍汲霭嫔?1985. [7] 李益民.機械制造工藝設計簡明手冊[M].北京:機械工業(yè)出版社,1994. [8] 朱耀祥主編.組合夾具[M].北京:機械工業(yè)出版社,1990. [9] 東北重型機械學院.機床夾具設計手冊[M].上海:上海科技出版社,1988. [10] 王啟平.機床夾具設計[M].哈爾濱:哈爾濱工業(yè)
59、大學出版社,1988. [11] 成大先.機械設計手冊(聯(lián)接與緊固)[M]. 北京:化學工業(yè)出版社,2004. [12] 肖繼德,陳寧平.機床夾具設計(第2版)[M]. 北京:機械工業(yè)出版社,2000. [13] 哈爾濱工業(yè)大學,上海工業(yè)大學.機床夾具設計(第二版[M]. 上海:上海科學技術出版社,1980. [14] 孫江宏. 精通Pro/ENGINEER Wildfire3.0-典型實例、專業(yè)精講[M].北京:電子工業(yè)出版社,2006. [15] 于志偉.Pro/ENGINEER零件設計完全手冊[M].北京:人民郵電出版社,2007.
60、 致 謝 本次畢業(yè)設計是變速箱殼體組合機床的設計,我主要負責的是機床總體設計及夾具部分的設計。機床的總體設計就是要確定機床各部件間的相互關系,選擇通用部件和刀具的導向,計算切削用量及機床生產(chǎn)率等;夾具的設計就是在滿足工件定位準確、可靠和夾緊裝置合理、經(jīng)濟,達到工藝精度所要求的條件下,提高工作效率,降低勞動成本。經(jīng)過多月的努力,我已經(jīng)較好地完成了本次畢業(yè)設計。 在設計工作開始之初,老師帶領我們?nèi)}城拖拉機廠、鹽城第一機床廠和鹽城江動集團進行了調(diào)研,讓我們首先對本課題有了感性認識。在調(diào)研的過程中,老師認真地給我們講解了各種零件的最新的與傳統(tǒng)的加工過程和生產(chǎn)方式,
61、避免我們在以后的畢業(yè)設計中走彎路。 在設計過程中,我得到邢青松老師的細心指導和周圍同學的熱心幫助,使我受益匪淺。在此對邢青松老師及同學們表示衷心的感謝! 此次設計與同組其他人員的通力合作也是分不開的,在此一并表示感謝! 限于本人水平有限和時間倉促,設計中缺點和錯誤在所難免,懇請各位老師不吝批評指正。 附 件 清 單 序號 圖名 圖號 圖幅 1. 2. 3. 4. 5. 6. 7. 8. 9. 10. 11. 12. 13. 被加工零件工序圖 BSXCT01
62、 A2 加工示意圖 BSXCT02 A2 機床聯(lián)系尺寸圖 BSXCT03 A3 生產(chǎn)率計算卡 BSXCT04 A4 夾具裝配圖 BSXCT03-03 A0 夾具體 BSXCT03-03-01 A1 定位塊 BSXCT0
63、3-03-02 A3 夾具左支架 BSXCT03-03-05 A1 蓋板 BSXCT03-03-06 A4 導向柱 BSXCT03-03-08 A3 球頭 BSXCT03-03-10 A4 襯塊 BSXCT03-03-11 A4 壓板 BSXCT03-03-12 A3
- 溫馨提示:
1: 本站所有資源如無特殊說明,都需要本地電腦安裝OFFICE2007和PDF閱讀器。圖紙軟件為CAD,CAXA,PROE,UG,SolidWorks等.壓縮文件請下載最新的WinRAR軟件解壓。
2: 本站的文檔不包含任何第三方提供的附件圖紙等,如果需要附件,請聯(lián)系上傳者。文件的所有權益歸上傳用戶所有。
3.本站RAR壓縮包中若帶圖紙,網(wǎng)頁內(nèi)容里面會有圖紙預覽,若沒有圖紙預覽就沒有圖紙。
4. 未經(jīng)權益所有人同意不得將文件中的內(nèi)容挪作商業(yè)或盈利用途。
5. 裝配圖網(wǎng)僅提供信息存儲空間,僅對用戶上傳內(nèi)容的表現(xiàn)方式做保護處理,對用戶上傳分享的文檔內(nèi)容本身不做任何修改或編輯,并不能對任何下載內(nèi)容負責。
6. 下載文件中如有侵權或不適當內(nèi)容,請與我們聯(lián)系,我們立即糾正。
7. 本站不保證下載資源的準確性、安全性和完整性, 同時也不承擔用戶因使用這些下載資源對自己和他人造成任何形式的傷害或損失。
最新文檔
- 建筑施工重大危險源安全管理制度
- 安全培訓資料:典型建筑火災的防治基本原則與救援技術
- 企業(yè)雙重預防體系應知應會知識問答
- 8 各種煤礦安全考試試題
- 9 危險化學品經(jīng)營單位安全生產(chǎn)管理人員模擬考試題庫試卷附答案
- 加壓過濾機司機技術操作規(guī)程
- 樹脂砂混砂工藝知識總結(jié)
- XXXXX現(xiàn)場安全應急處置預案
- 某公司消防安全檢查制度總結(jié)
- 1 煤礦安全檢查工(中級)職業(yè)技能理論知識考核試題含答案
- 4.燃氣安全生產(chǎn)企業(yè)主要負責人模擬考試題庫試卷含答案
- 工段(班組)級安全檢查表
- D 氯化工藝作業(yè)模擬考試題庫試卷含答案-4
- 建筑起重司索信號工安全操作要點
- 實驗室計量常見的30個問問答題含解析