【溫馨提示】壓縮包內(nèi)含CAD圖有下方大圖片預(yù)覽,下拉即可直觀呈現(xiàn)眼前查看、盡收眼底縱觀。打包內(nèi)容里dwg后綴的文件為CAD圖,可編輯,無水印,高清圖,壓縮包內(nèi)文檔可直接點開預(yù)覽,需要原稿請自助充值下載,所見才能所得,請見壓縮包內(nèi)的文件及下方預(yù)覽,請細(xì)心查看有疑問可以咨詢QQ:11970985或197216396
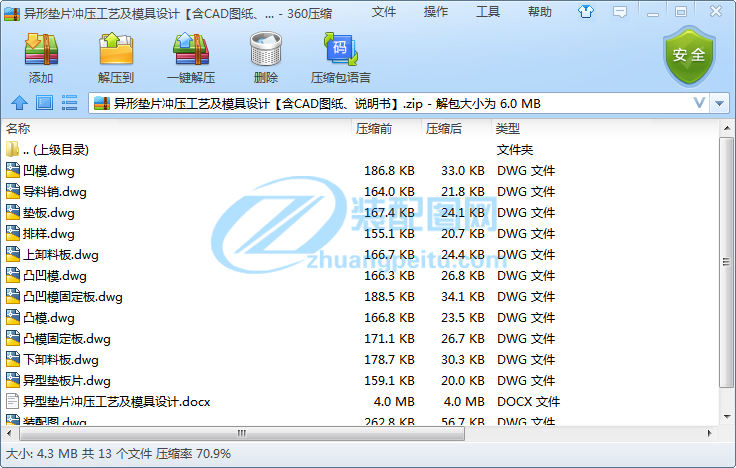
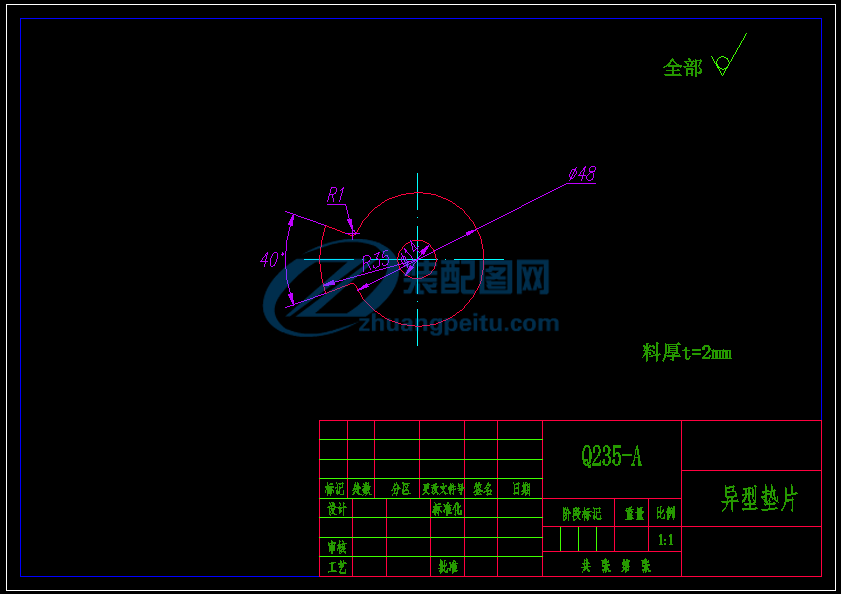
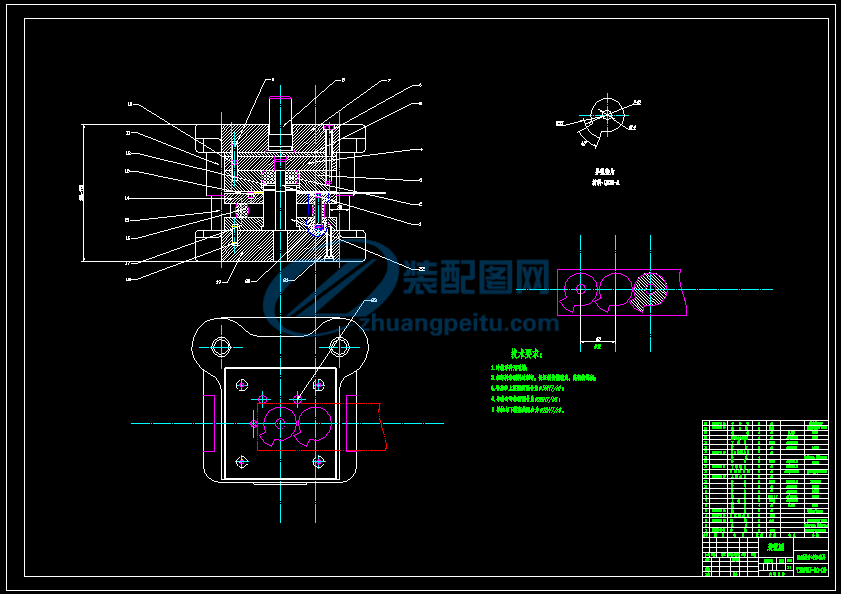
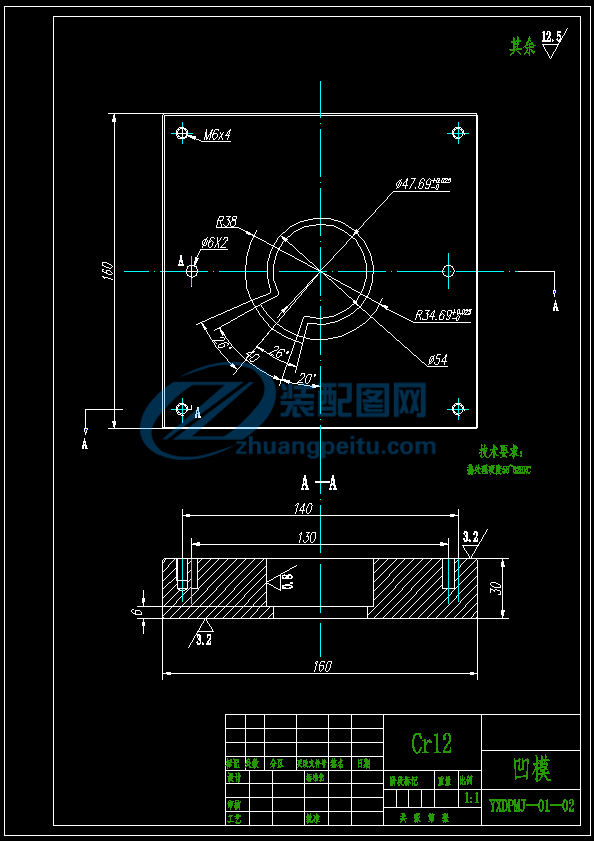
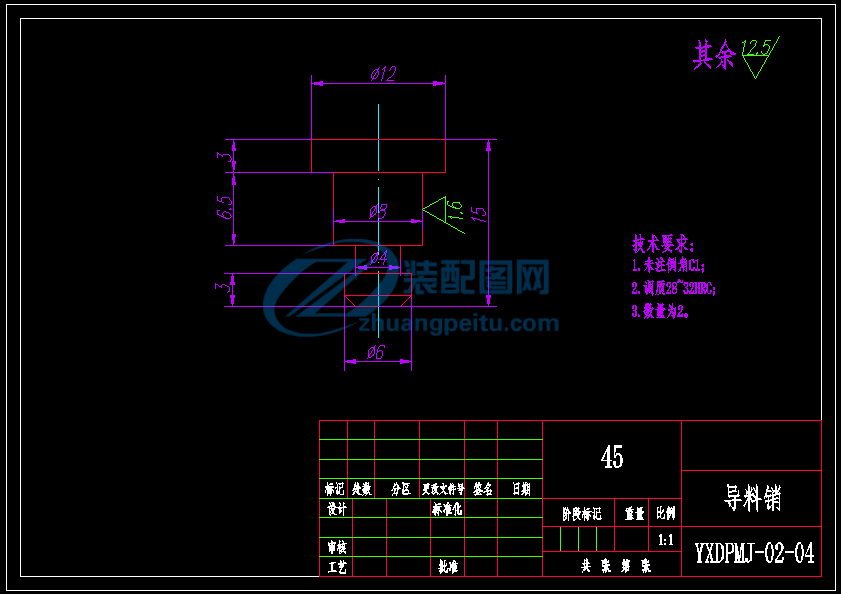
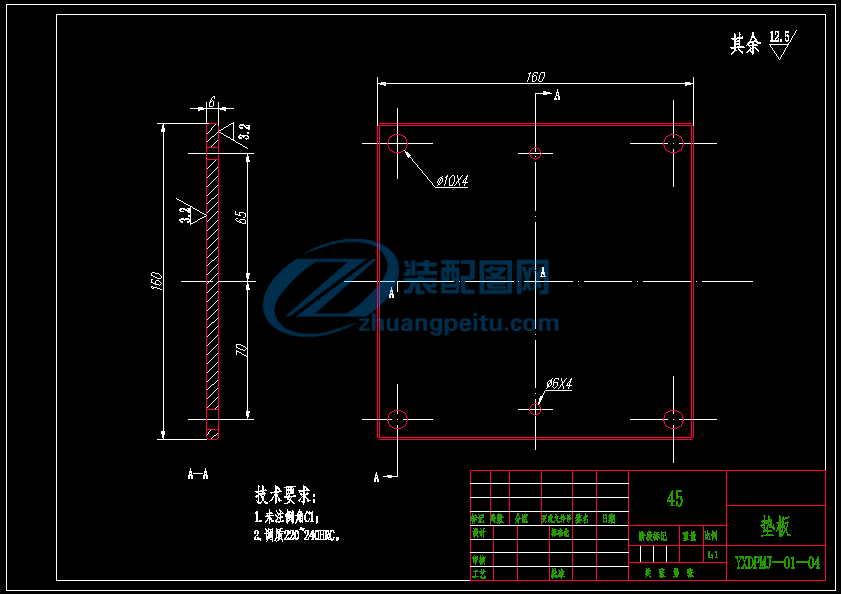


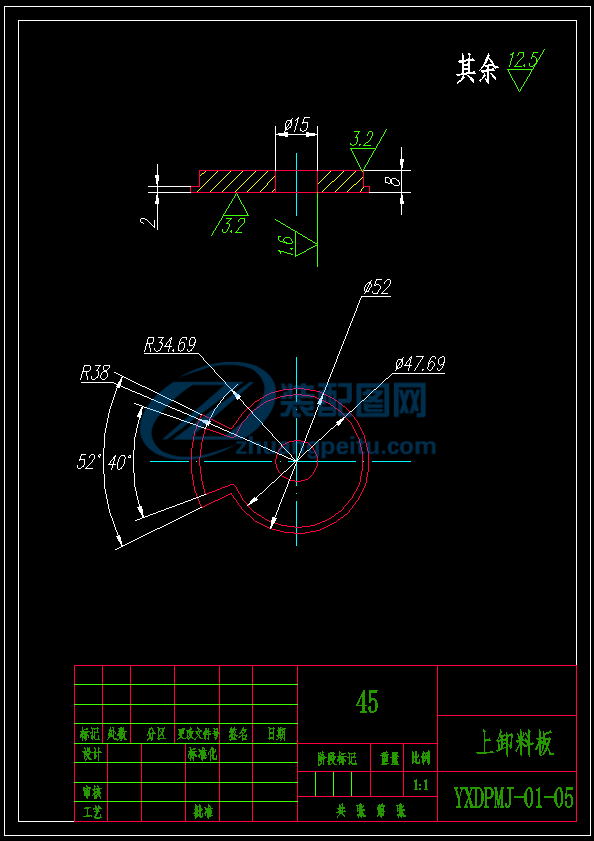
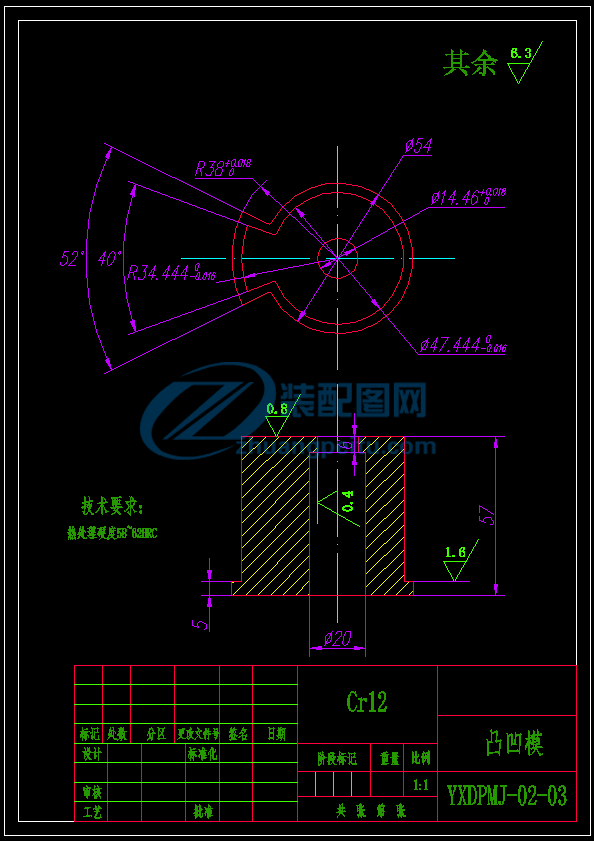

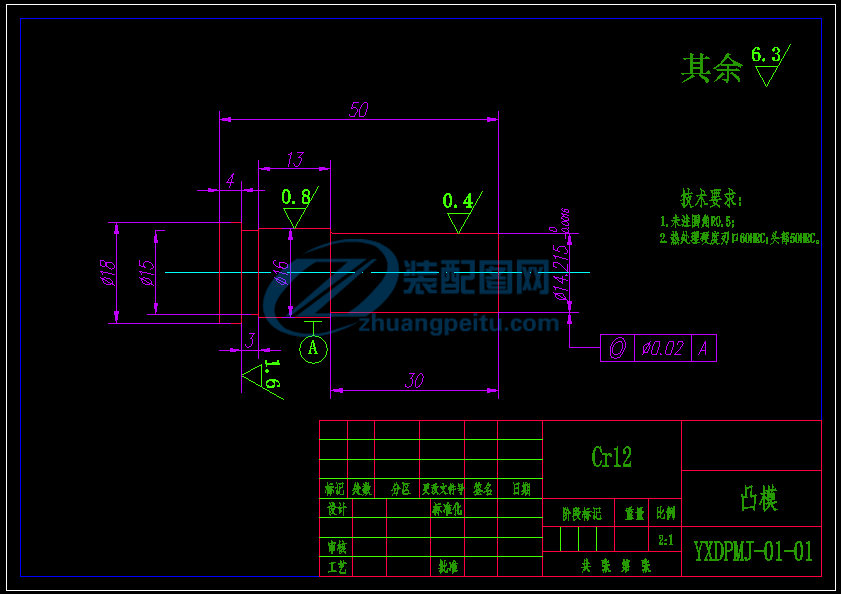
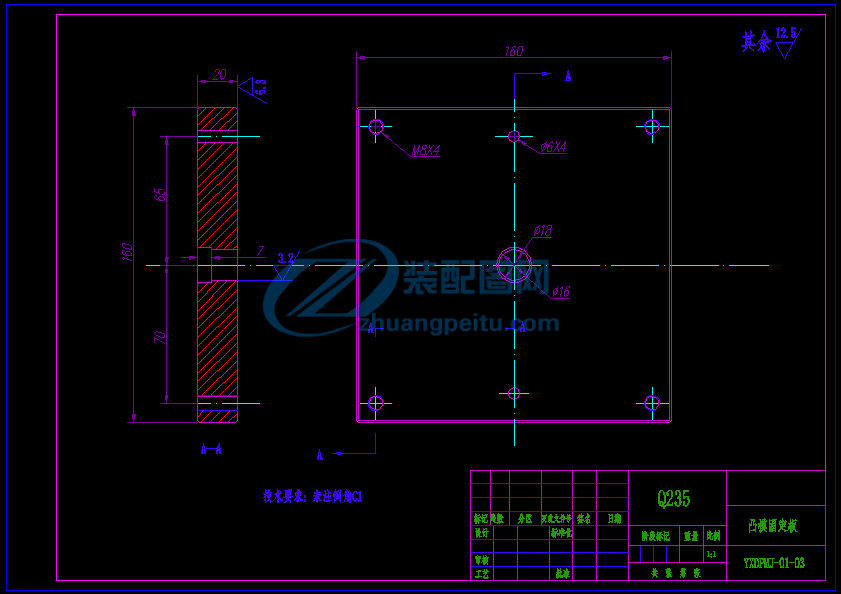
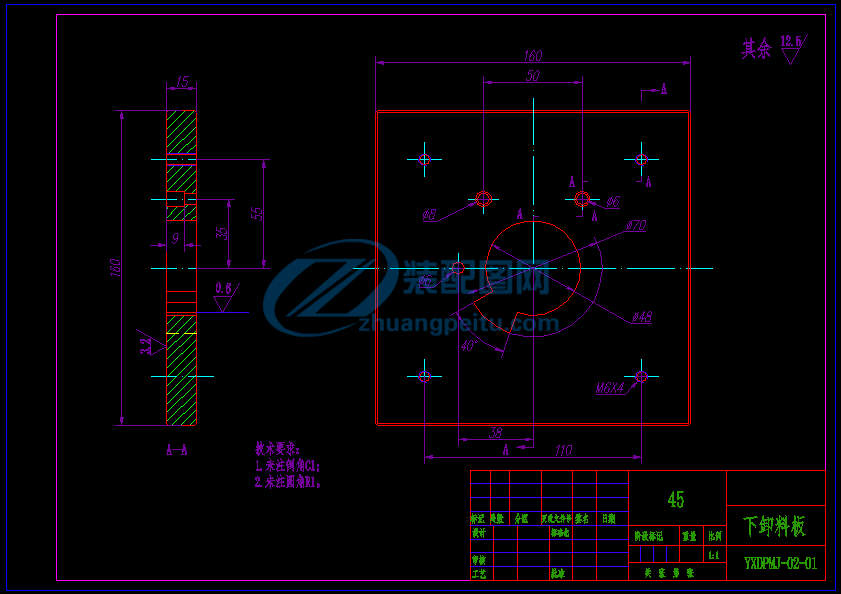
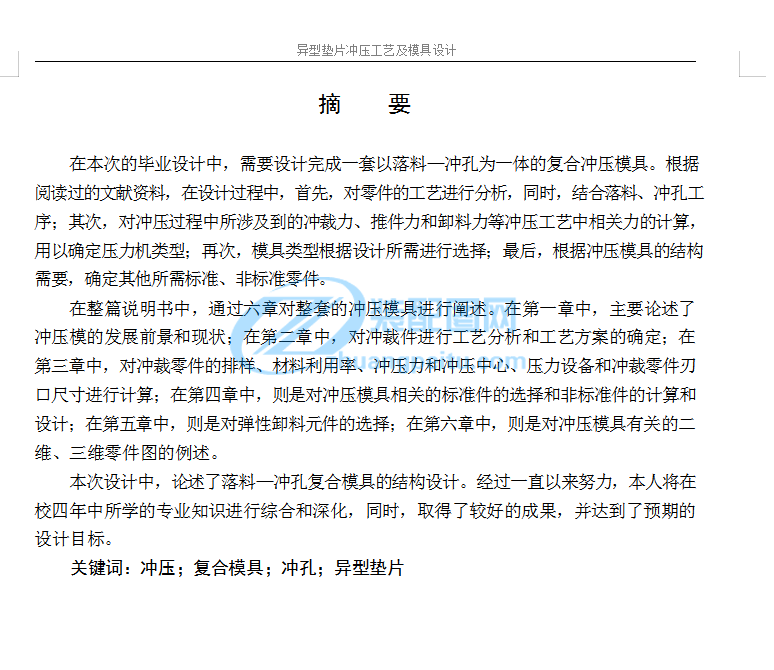
壓縮包內(nèi)含有CAD圖紙和說明書,咨詢Q 197216396 或 11970985
摘 要
在本次的畢業(yè)設(shè)計中,需要設(shè)計完成一套以落料—沖孔為一體的復(fù)合沖壓模具。根據(jù)閱讀過的文獻資料,在設(shè)計過程中,首先,對零件的工藝進行分析,同時,結(jié)合落料、沖孔工序;其次,對沖壓過程中所涉及到的沖裁力、推件力和卸料力等沖壓工藝中相關(guān)力的計算,用以確定壓力機類型;再次,模具類型根據(jù)設(shè)計所需進行選擇;最后,根據(jù)沖壓模具的結(jié)構(gòu)需要,確定其他所需標(biāo)準(zhǔn)、非標(biāo)準(zhǔn)零件。
在整篇說明書中,通過六章對整套的沖壓模具進行闡述。在第一章中,主要論述了沖壓模的發(fā)展前景和現(xiàn)狀;在第二章中,對沖裁件進行工藝分析和工藝方案的確定;在第三章中,對沖裁零件的排樣、材料利用率、沖壓力和沖壓中心、壓力設(shè)備和沖裁零件刃口尺寸進行計算;在第四章中,則是對沖壓模具相關(guān)的標(biāo)準(zhǔn)件的選擇和非標(biāo)準(zhǔn)件的計算和設(shè)計;在第五章中,則是對彈性卸料元件的選擇;在第六章中,則是對沖壓模具有關(guān)的二維、三維零件圖的例述。
本次設(shè)計中,論述了落料—沖孔復(fù)合模具的結(jié)構(gòu)設(shè)計。經(jīng)過一直以來努力,本人將在校四年中所學(xué)的專業(yè)知識進行綜合和深化,同時,取得了較好的成果,并達到了預(yù)期的設(shè)計目標(biāo)。
關(guān)鍵詞:沖壓;復(fù)合模具;沖孔;異型墊片
II
ABSTRACT
In this graduation design,the purpose of is to design a set of blanking, punching as one
of the compound stamping die. According to read the literature, the design process, first of all, analyze the parts of process,at the same time,combined with blanking and punching process; Second,involved in the process of punching blanking force and unloading force such as stamping process related force calculation,to determent the type of press;Once again,choose type of press according to the design;Eventually,according to the requirements of the
stamping die structure,determine other required standard and non-standard parts.
In the whole instruction,through six chapters of a complete set of stamping die.In the first chapter,mainly discusses the prospects of the development of stamping die and the status;In the second chapter,hedge cutting process analysis and determination of process scheme; In the third chapter,hedge cutting parts layout,material utilization,burst pressure and stamping center,pressure equipment and blanking parts edge size calculation;In the fourth chapter,it is for stamping die related tagging and labeling parts size calculation and selection;In the fifth chapter,is the choice of elastic discharging device;In the sixth chapter,it is for stamping die about 2 d and 3 d part drawing.
In this design ,this paper discusses the blanking punching compound die structure design.
After long efforts ,make oneself will be learned in the school four years professional knowledge comprehensively and deepen,at the same time, good results have been achieved,and achieve the expected design goal.
Key Words:Stamping;Composite mould;Punching ;Aline gasket
目錄
摘 要 I
ABSTRACT II
1 緒論 1
1.1 沖壓的概念、基本工序和特點 1
1.2 沖壓技術(shù)研究的意義和應(yīng)用價值 2
1.3 沖壓工藝目前研究的概況和發(fā)展趨勢 2
1.4 設(shè)計任務(wù)書 4
2 沖壓件異型墊片的工藝性分析 5
2.1 異型墊片材料分析 5
2.2 異型墊片的結(jié)構(gòu)分析 6
2.3 異型墊片工藝方案的確定 6
3 沖壓模具中的工藝計算 9
3.1 排樣設(shè)計 9
3.2 材料利用率 12
3.3 沖壓力和沖壓中心的計算 13
3.4 壓力設(shè)備的選擇 16
3.5 刃口尺寸計算 17
4 模具主要零部件的設(shè)計和選擇 23
4.1 標(biāo)準(zhǔn)模架的選取 23
4.2 上模 25
4.3 下模 32
4.4 緊固連接件 36
5 彈性卸料元件的選擇 38
5.1 彈性卸料元件的類型 39
5.2 彈性卸料元件的確定與選擇 41
6 相關(guān)零件圖、裝配圖 45
6.1 三維裝配圖 45
6.2 二維主要零件圖 47
7 結(jié)論 49
參考文獻 50
附錄 1:外文翻譯 51
附錄 2:外文原文 57
致 謝 64
1 緒論
1.1 沖壓的概念、基本工序和特點
1.1.1 沖壓的概念
沖壓是指在室溫下,利用安裝在壓力機上的模具對板料施加壓力,從而使其發(fā)生分離或塑形變形,以獲得所需零件的一種壓力加工方法,也稱為沖壓或沖壓件。沖壓是一種冷變形加工工藝,即在常溫下對材料進行加工,材料的種類主要為板料,也被稱為冷沖壓(或板料沖壓)。
將材料批量加工成為所需沖件的專用工具被稱為沖模,其中,材料既包括金屬也包括非金屬。沖壓所使用的模具被稱為沖壓模具,簡稱為沖模。在整個沖壓過程中,最為重要的就是沖模,要得到能夠批量加工生產(chǎn)的沖件,就必須有符合要求的沖模。因此, 在沖壓中追求更為先進的沖模以實現(xiàn)沖壓工藝的完美實現(xiàn)。沖壓加工的三要素有沖壓工藝與模具、沖壓設(shè)備和沖壓材料,上述三要素的完美結(jié)合才得出最優(yōu)秀的沖壓件。
1.1.2 沖壓的基本工序
沖壓的基本工序分為分離工序和變形工序。分離工序為沖裁(落料、沖孔、切斷、切邊、剖切);變形工序分為彎曲(切舌、彎曲、卷邊),拉伸,成形(翻遍、縮口、脹形、起伏成型、整型、旋壓),立體壓制(冷擠壓、頂墩)。
在上述工序中,較為常用的有沖裁、彎曲、拉伸、成形。
1.1.3 沖壓的優(yōu)點
本次設(shè)計零件的加工方式為板料沖壓,所以,板料沖壓加工工藝的優(yōu)點如下:
(1) 生產(chǎn)效率高,操作簡便,易于實現(xiàn)自動化和機械化;
(2) 沖壓加工零件的尺寸精度是由模具保證的,一般不需要再進行機械切削加工, 所以質(zhì)量穩(wěn)定,具有較高的尺寸精度;
(3) 沖壓工藝能制造出其他金屬加工方法所不能或難以加工出的、形狀復(fù)雜的零件;
(4) 沖壓加工一般不需要加熱毛坯,也不想切削加工那樣需要切除大量金屬,所以它不但節(jié)能,而且材料利用率高;
(5) 沖壓所用原材料多為軋制板料或帶料,在沖壓過程中材料表面一般不會被破壞,所以表面質(zhì)量較好,為后續(xù)表面處理工序提供了方便條件。
(6) 沖壓件有較好的互換性。
1.2 沖壓技術(shù)研究的意義和應(yīng)用價值
本次論文設(shè)計的主要內(nèi)容是設(shè)計出一套完整的模具,以得到材料為 Q235-A,厚度t=2mm 的異形墊片,用于大批量生產(chǎn)。所以,在本次的論文設(shè)計及沖壓模具設(shè)計過程
9
中,我們需要涉及到多門學(xué)科的相關(guān)知識。其中,沖壓工藝和沖壓模具的相關(guān)知識、模具設(shè)計的過程與步驟、材料力學(xué)的計、機械原理及設(shè)計和互換性與公差的相關(guān)知識、以及 CAD/CAE/CAM 和 Proe 等計算機繪圖軟件應(yīng)用技術(shù)。
因此,在本次設(shè)計中我們除了要學(xué)會本次設(shè)計的相關(guān)知識,還要熟練的對各個相關(guān)知識之間的串聯(lián)應(yīng)用融會貫通。在整個設(shè)計過程中,我們就會了解到模具設(shè)計的研究意義就是其在國民經(jīng)濟中的地位。
由于我國模具行業(yè)的整體水平依舊偏低,所以我國模具行業(yè)的發(fā)展前景同樣也是非??捎^的。同時,我國模具行業(yè)的發(fā)展空間也是十分廣闊、前景光明的。我們必須堅信在未來不久的時間內(nèi),我國模具行業(yè)必能迎來新生,成為世界模具行業(yè)發(fā)展強國位列前茅。
1.3 沖壓工藝目前研究的概況和發(fā)展趨勢
1.3.1 沖壓技術(shù)以及沖壓模具目前的發(fā)展概況
沖壓是在室溫下,利用安裝在壓力機上的模具對板材、帶材、管材及型材等材料施加壓力,使其產(chǎn)生分離或塑性變形,從而獲得到所需形狀和尺寸的加工方法。沖壓按工藝分類主要可以分為分離(沖裁)工序和成形工序。從廣義來說,沖裁是分離工序的總稱,它包括切斷、落料、沖孔、修邊、切口等多種工序;成形則是使材料在不被破壞的條件下發(fā)生塑性變形,從而達到所需形狀和尺寸的工件的工序。
沖壓是現(xiàn)代工藝中較為常見和常用的一種加工方法,主要是用來生產(chǎn)各種板料零 件,具有很大的競爭優(yōu)勢,它的生產(chǎn)產(chǎn)品具有自重輕、剛度大、互換性好、強度高、成本低、生產(chǎn)過程便于實現(xiàn)機械自動化及生產(chǎn)效率高等特點,因此擁有了其它的加工方法所不能代替的顯著優(yōu)勢。所以在近幾年來,被廣泛的運用于各種生產(chǎn)制造前線,例如, 汽車、能源、機械、信息、航空航天、國防工業(yè)和日常生活的生產(chǎn)制造之中。
模具工業(yè),在美國工業(yè)界,被譽為“美國工業(yè)的基石”;日本則稱其為“進入富裕社會的原動力”;德國則為其冠以“金屬加工工業(yè)中的帝王”的稱號;“模具就是黃金” 是歐盟一些國家對模具工業(yè)的贊譽;而我國模具權(quán)威則稱“模具是印鈔機”。由此則不難看出模具工業(yè)在世界各國經(jīng)濟發(fā)展所占有的重要地位,模具技術(shù)也亦然成為衡量一個國家產(chǎn)品制造水平的重要指標(biāo)之一。
旋壓成形、軟模具成形、高能率成形等是近幾十年來沖壓技術(shù)飛速發(fā)展的應(yīng)用,由此可以看出,人們對沖壓技術(shù)的認(rèn)知與掌握的程度有了質(zhì)的飛躍。
傳統(tǒng)模具生產(chǎn)方式由于模具 CAD/CAE/CAM 的廣泛使用而改變,成為模具生產(chǎn)方式的關(guān)鍵技術(shù)手段,作為一項高科技、高效益的系統(tǒng)工程被應(yīng)用于生產(chǎn)前線。它以計算
機軟件的形式,為企業(yè)提供一種有效的輔助工具,使工程技術(shù)人員借助于計算機對產(chǎn)品性能、模具結(jié)構(gòu)、成形工藝、數(shù)控加工及生產(chǎn)管理進行設(shè)計和優(yōu)化。在實際生產(chǎn)中,模具 CAD/CAE/CAM 技術(shù)能顯著縮短模具設(shè)計與制造周期,降低生產(chǎn)成本和提高產(chǎn)品質(zhì)量已成為模具界的共識。
我國從上世紀(jì) 90 年代開始,華中科技大學(xué)、上海交通大學(xué)、西安交通大學(xué)和北京機電研究院等相繼開展了級進模 CAD/CAM 系統(tǒng)的研究和開發(fā)。如華中科技大學(xué)模具技術(shù)國家重點實驗室在Auto CAD 軟件平臺上開發(fā)出基于特征的級進模CAD/CAM 系統(tǒng)HMJC,包括板金零件特征造型、基于特征的沖壓工藝設(shè)計、模具結(jié)構(gòu)設(shè)計、標(biāo)準(zhǔn)件及典型結(jié)構(gòu)建庫工具和線切割自動編程 5 個模塊。
1.3.2 沖壓技術(shù)以及沖壓模具未來的發(fā)展趨勢
在 21 世紀(jì)經(jīng)濟發(fā)展的大背景下,由于我國擁有豐厚廉價的人力資源、龐大的市場需求力以及其他優(yōu)異條件,漸漸成為發(fā)達國家轉(zhuǎn)移模具生產(chǎn)基地的選擇。模具產(chǎn)品具有“交貨期短”、“精度高”、“質(zhì)量好”、“價格低”的特點,所以為了適應(yīng)模具技術(shù)的發(fā)展在未來十年我國沖壓模具技術(shù)發(fā)展趨勢應(yīng)如下:
(1) 要全面推廣 CAD/CAM/CAE 技術(shù);
(2) 模具掃描及數(shù)字化系統(tǒng);
(3) 提高模具標(biāo)準(zhǔn)化程度;
(4) 開發(fā)優(yōu)質(zhì)模具材料;
(5) 自主創(chuàng)新能力模具工程師的培養(yǎng);
(6) 加強表面處理技術(shù)的應(yīng)用;
(7) 模具結(jié)構(gòu)日趨大型、精密、復(fù)雜及壽命日益提高。
1.4 設(shè)計任務(wù)書
1.4.1 異型墊片的主要參數(shù)
零件名稱為異型墊片,材料為 Q235-A,材料料厚為 2mm,生產(chǎn)方式為大批量生產(chǎn)。零件二維圖如圖 1.1 所示,零件三維圖如圖 1.2 所示。
圖 1.1 異型墊片(二維) 圖 1.2 異型墊片(三維)
1.4.2 設(shè)計任務(wù)與要求
(1) 原材料性能工藝分析,確定總體工藝方案。
(2) 對必要的數(shù)據(jù)進行計算:搭邊計算;材料利用率的計算;力的計算(沖裁工藝中力的計算、確定壓力中心);各模具部件的設(shè)計計算(凸模的設(shè)計、凹模的設(shè)計和凸凹模的設(shè)計等);彈性元件的選擇和計算。
(3) 壓力機類型的選取。
(4) 模架類型的選取。
(5) 模具中各種標(biāo)準(zhǔn)、非標(biāo)準(zhǔn)件的選取與部分零件的繪制。
(6) 凸模、凹模和凸凹模的繪制。
(7) 撰寫完整的設(shè)計說明書。
2 沖壓件異型墊片的工藝性分析
2.1 異型墊片材料分析
在整個沖壓過程中,沖壓件的材料費用就占整個沖壓成本的 60%~80%,材料的選擇直接影響著整個沖裁工藝設(shè)計、沖壓件質(zhì)量、使用壽命和成本等三個方面。要生產(chǎn)出優(yōu)秀的沖壓件,則必須完善和擇優(yōu)選擇上述三方面的因素。這也對沖壓材料提出了如下的基本要求[2]:
(1) 滿足產(chǎn)品應(yīng)用要求
由于產(chǎn)品的使用用途不同,則對材料的力學(xué)和物理性能的要求也不同。
(2) 沖壓性能良好
材料對各種沖壓加工方法的適應(yīng)能力被稱為沖壓性能。影響沖壓性能的因素包括三個方面,即材料塑形、材料抗壓失穩(wěn)起皺能力和材料表面質(zhì)量等。
塑性 任何材料都存在成形極限,在沖壓過程中當(dāng)變形超過材料成形極限時,就會引起沖壓件破裂。
抗壓失穩(wěn)起皺能力 在沖壓過程中,如直壁零件的拉深、縮口及外凸曲線翻邊等是材料主要受壓應(yīng)力作用的情況,這時材料壓縮變形且厚度增加,易引起失穩(wěn)起皺。
表面質(zhì)量 材料表面光潔、平整和無銹等是材料良好表面質(zhì)量的要求。
本次沖裁件的材料設(shè)定為 Q235-A,普通碳素鋼,是 Q235 根據(jù)不同的沖擊溫度劃分的等級,該材料具有較好的沖裁成形性能,詳細(xì)參數(shù)如表 2.1 所示。
表 2.1 沖壓常見鋼材的力學(xué)性能
2.2 異型墊片的結(jié)構(gòu)分析
沖裁件的形狀結(jié)構(gòu)、尺寸大小、尺寸偏差、形位公差與尺寸、基準(zhǔn)等是否符合沖裁加工的工藝要求即為沖裁件的工藝性,也是沖裁件對沖壓工藝的適應(yīng)性。產(chǎn)品零件結(jié)構(gòu)簡單對稱并且無尖角才對沖裁加工更為有利。
2.3 異型墊片工藝方案的確定
2.3.1 模具種類和特點
(1) 簡單模
定義:壓力機一次沖壓只能完成一個沖裁工序的模具,稱為單工序?;蚝唵文11]。種類:無導(dǎo)向簡單沖裁模、導(dǎo)板式簡單沖裁模、導(dǎo)柱式簡單沖裁模。
特點:無導(dǎo)向簡單沖裁模的特點有結(jié)構(gòu)簡單,重量較輕,尺寸較小,模具制造簡單, 成本低廉;模具依靠壓機滑塊導(dǎo)向,使用時安裝調(diào)整麻煩,模具壽命低,沖裁件精度差; 操作也不安全。無導(dǎo)向簡單模適用于精度要求不高、形狀簡單、批量小或試制的沖裁件。
導(dǎo)板式簡單沖裁模的特點:具有精度高、壽命長、使用安裝容易、操作安全,但制造比較復(fù)雜。一般適用于形狀較簡單尺寸不大的沖裁件。
導(dǎo)柱式簡單沖裁模的特點:雖然導(dǎo)柱會加大模具輪廓尺寸,使模具笨重、制造工藝復(fù)雜、增加模具成本,但是用導(dǎo)柱導(dǎo)向比導(dǎo)板可靠、精度高壽命長,使用安裝方便,所以在大量和成批生產(chǎn)中廣泛采用導(dǎo)柱式?jīng)_裁模。
(2) 連續(xù)模(或級進模)
定義:壓力機一次行程中,在模具的不同部位上同時完成數(shù)道工序的模具稱為連續(xù)模。連續(xù)模所完成的沖壓工序均布在坯料的送進方向上[11]。
特點:連續(xù)??梢园褍傻拦ば蚝喜?,用一套模具完成。所以使用連續(xù)??梢詼p少模具和設(shè)備的數(shù)量,提高生產(chǎn)效率,而且容易實現(xiàn)生產(chǎn)自動化。但是,比簡單模制造麻煩而且成本更高。用連續(xù)模沖制零件,必須解決條料的準(zhǔn)確定位問題,才有可能保證制件的質(zhì)量。根據(jù)定位零件的特征,常見的典型連續(xù)模結(jié)構(gòu)有這幾種形式,如有固定擋料銷及導(dǎo)正銷的連續(xù)模、有側(cè)刀的連續(xù)模、有自動擋料銷的連續(xù)模。
(3) 復(fù)合模
定義:壓力機一次行程中,在模具的同一部位上同時完成數(shù)道沖壓工序的模具稱為復(fù)合模。連續(xù)模和復(fù)合模都是多工序模[11]。
特點:
內(nèi)外形相對位置及零件尺寸的一致性非常好,生產(chǎn)零件表面平整,并且精度高; 模具結(jié)構(gòu)緊湊,對壓力機的平臺要求不高;
可以充分利用短料和余料;
適合沖裁簿料和脆性或軟性材料。
復(fù)合模結(jié)構(gòu)上的特點是具有即是落料凸模又是沖孔凹模的所謂凸凹模。
2.3.2 沖壓工藝方案的確定
該零件包括落料、沖孔兩道加工工序,因此根據(jù)模具的種類設(shè)定如下幾種方案: 方案一:先落料,后沖孔。采用兩套簡單(單工序)模具生產(chǎn)加工。
方案二:沖孔—落料連續(xù)(級進)沖壓。采用連續(xù)(級進)模具生產(chǎn)。方案三:沖孔—落料復(fù)合沖壓。采用復(fù)合(多工序)模具生產(chǎn)。
方案一,模具結(jié)構(gòu)雖然簡單,但是必須經(jīng)過兩道工序、兩副簡單模具才能得到所需零件,成本高而且生產(chǎn)率低,同時生產(chǎn)出來的沖裁件形位精度低,很難達到圖紙要求。方案二,模具應(yīng)用為連續(xù)(級進)模具,生產(chǎn)效率有所提高,但是產(chǎn)品的形位精度則得不到保證,連續(xù)模同樣也使得生產(chǎn)的成本提高。方案三,只需一副模具即復(fù)合模(多工序模),復(fù)合模的應(yīng)用使生產(chǎn)效率提高、工件形位精度得以保證,僅一套模具的使用使生產(chǎn)成本大大提高。該零件形狀簡單、對稱,零件精度要求不高,采用沖裁加工能得到保證。綜上所述分析,確定零件的工藝方案為方案三,采用沖孔—落料復(fù)合沖壓。
3 沖壓模具中的工藝計算
3.1 排樣設(shè)計
3.1.1 排樣方法
排樣方法可以分為有廢料排樣、少廢料排樣和無廢料排樣三種[2]。
(1) 有廢料排樣 該排樣形式如圖 3.1(a)所示,沖裁件尺寸完全是由沖模決定的。優(yōu)點為沖件質(zhì)量良好,模具使用壽命高;缺點為材料利用率較高。用于沖裁件形狀結(jié)構(gòu)較復(fù)雜并且尺寸精度要求也較高的情況。
(2) 少廢料排樣 該排樣形式如圖 3.1(b)所示,沖裁件質(zhì)量稍差,沖模壽命因為邊緣毛刺易被凸模帶入到間隙而縮減。優(yōu)點為沖模的結(jié)構(gòu)簡單,材料利用率也叫高。常用于形狀較規(guī)則、某些尺寸的尺寸精度要求不高的沖件。
(3) 無廢料排樣 該排樣形式如圖 3.1(c)、(d)所示,此類排樣的沖模,沖裁件質(zhì)量和壽命更差一些。優(yōu)點為材料的利用率最高,進距則是沖裁件寬度的兩倍,一次切斷就能獲得兩個沖件,提高了生產(chǎn)效率。用于形狀規(guī)則對稱、尺寸精度不高,沖裁件材料為較貴重金屬材料。
圖 3.1 排樣方法
除了上述的 3 種排樣方法除外,還可以根據(jù)沖裁件在條料上的不同的排列方式,分為直排、斜排、直對排、斜對排、混合排、多排及沖裁搭邊等。
綜上所述,根據(jù)零件形狀和考慮材料利用率確定排樣方法為斜排,傾斜角度為 40°。
3.1.2 搭邊和條料寬度的確定
排樣時沖件之間以及沖件與條料邊緣之間留下的工藝廢料被稱為搭邊。搭邊的作用如下:補償定位和送料的誤差,能保證沖出合格的零件;條料剛度增加,便于條料的送進和提高生產(chǎn)效率;沖裁時條料邊緣的毛刺也不易被拉入模具間隙,提高了模具的使用壽命。
在設(shè)計搭邊的過程中,搭邊值的大小選擇要合理,否則,過大的搭邊值會使材料利用率偏低,過小的搭邊值會使沖裁工藝達不到要求。材料的機械性能、沖件的形狀與尺寸、材料的厚度、送料及擋料和卸料方式。搭邊值一般根據(jù)經(jīng)驗來確定,具體數(shù)值如表
3.1 所示。
表 3.1 常見搭邊值的選用
卸 料 板形式
條料厚度
t(mm)
搭邊值(mm)
用于圖(a)、(b),
R > 2t
用于圖(c)、(d),L £ 50
用于圖(c)、(d), L > 50
a
a1
a
a1
a
a1
彈性卸料板
≤0.25
1.2
1.0
1.5
1.2
1.8~2.6
1.5~2.5
>0.25~0.5
1.0
0.8
1.2
1.0
1.5~2.5
1.2~2.2
>0.5~1.0
—
—
—
—
1.8~2.6
1.5~2.2
>1.0~1.5
1.3
1.0
1.5
1.2
2.2~3.2
1.8~2.8
>1.5~2.0
1.5
1.2
1.8
1.5
2.4~3.4
2.0~3.2
>2.0~2.5
1.9
1.5
2.2
1.8
2.7~3.7
2.2~3.2
>2.5~3.0
2.2
1.8
2.4
2.0
3.0~4.0
2.5~3.5
>3.0~3.5
2.5
2.0
2.7
2.2
3.3~4.3
2.8~3.8
>3.5~4.0
2.7
2.2
3.0
2.5
3.5~4.5
3.0~4.0
>4.0~4.5
3.0
2.5
3.5
3.0
4.0~5.0
3.5~4.5
>4.5~12
0.6t
0.5t
0.7t
0.6t
(0.8~1)t
(0.7~0.9)t
根據(jù)零件的排樣方式和上述表格所述,采用直邊沖件,其長度 L 在 50~100mm 內(nèi),
1
用于圖(c)、(d),沖裁件的料厚t = 2mm ,取a = 2.5mm , a = 2mm 。為節(jié)省
加工成本,確定排樣為斜排,排樣圖如圖 3.2 所示。
圖 3.2 排樣圖
在確定條料寬度和導(dǎo)板間距時,應(yīng)該考慮沖模的送料定位方式,同時也要根據(jù)不同的結(jié)構(gòu)分別進行計算。本次設(shè)計中,選擇有側(cè)壓裝置,即在送進時條料在測壓裝置作用下緊靠導(dǎo)料板,如圖 3.3 所示。
圖 3.3 條料寬度計算
19
可按如下公式進行計算:
B
-D
-D
條料寬度 0
= (D
max
+ 2a)0
(3.1)
導(dǎo)料板間距離
B = B + Z = D
+ 2a + Z
(3.2)
max
0
式中 Dmax ——條料寬度方向沖件的最大尺寸, mm ;
a ——側(cè)搭邊值, mm ,可以參考表 3.1;
D ——條料寬度的單向(負(fù)向)偏差, mm ,見表 3.2;
Z ——導(dǎo)料板與最寬條料之間的間隙, mm ,其數(shù)值參考表 3.3。
表 3.2 條料寬度偏差值D(mm)
條料寬度 B
材料厚度 t
~0.5
0.5~1
1~2
2~3
3~5
約 20
0.05
0.08
0.10
—
—
20~30
0.08
0.10
0.15
—
—
30~50
0.10
0.15
0.20
—
—
約 50
—
0.4
0.5
0.7
0.9
50~100
—
0.5
0.6
0.8
1.0
100~150
—
0.6
0.7
0.9
1.1
150~200
—
0.7
0.8
1.0
1.2
200~300
—
0.8
0.9
1.1
1.3
-D
根據(jù)圖 3.2 可知, B = 61.82mm ? 62mm 。根據(jù)表 3.2 可知, D = 0.6mm 。
-D
綜上所述,條料寬度 B0
= (D
max
+ 2a)0
0
= 62
-0.6
mm 。
表 3.3 導(dǎo)料板與條料之間的最小間隙 Zmin (mm)
材料厚度 t
無側(cè)壓裝置
有側(cè)壓裝置
條料寬度 B
條料寬度 B
≤100
100~200
200~300
≤100
>100
約 1
0.5
0.5
1
5
8
1~5
0.5
1
1
5
8
min
根據(jù)表 3.3 可知, Z = 5mm 。
綜上所述,導(dǎo)板間距離 B0
= B + Z = D
+ 2a + Z = 62 + 5mm = 67mm 。
max
3.2 材料利用率
一個進距內(nèi)的材料利用率h為(如圖 3.4 所示)
h= A Bs
′100%
(3.3)
圖 3.4 材料利用率計算
式中 A ——1 個沖裁件的面積(包括沖出的小孔在內(nèi)), mm ; B ——條料寬度, mm ;
s ——進距, mm 。
根據(jù)軟件計算得出廢料面積 A0 ,如圖 3.5 所示。
圖 3.5 材料利用率
根據(jù)零件排樣和材料利用率公式可知,
0
A = Bs - A = 62 ′ 50 -1467.43mm2
= 1632.57mm2
綜上所述,得出材料利用率h如下,
h= A Bs
′100% = 1632.57 ′100%
62 ′ 50
= 52.7%
3.3 沖壓力和沖壓中心的計算
3.3.1 沖壓力的計算
采用彈性卸料和下出料方式 。
沖壓力包括沖裁力、卸料力、推件力和頂件力。沖壓力是選擇壓力機、設(shè)計沖裁模具和校核模具強度的重要依據(jù)。
(1)沖裁力
選擇沖壓設(shè)備噸位和檢驗?zāi)>邚姸戎饕怯袥_裁力來決定。平刃沖模的沖裁力為
b
F = kLtt
式中 F ——沖裁力(N ) ;
L ——為沖裁周邊長度(mm);
t ——材料厚度(mm);
b
t ——材料抗剪強度(MPa) ;
k ——系數(shù)(一般取k = 1.3)。
(3.4)
上式中抗剪強度t ,為便于計算可取t = 0.8s ,故沖裁力又可以用下列公式表
b b b
達
b
F = Lts
(3.5)
b
式中 s ——被沖材料的抗拉強度(MPa) 。
材料Q235 - A的抗拉強度為380MPa 。
沖孔力
l = pf = 14p? 43.98(mm)
1
1
F = l ts = 43.98 ′ 2 ′ 380 = 33424.8(N )
1 1 b
L = 320 ′p′f + 40 ′p′ 2R + 2? R -f3 ?
2 360
è
?
320
2 360
40
? ÷
2
è ?
? 48 ?
落料力
= 360 ′p′ 48 + 360 ′p′ 2 ′ 35 + 2?35 - 2 ÷
= 180.48(mm)
F = L ts = 180.48′ 2 ′ 380 = 137161.681(N )
2 2 b
(2)推件力、頂件力和卸料力
卸料力
F = K F
(3.6)
x
x
推件力
F = nK F
(3.7)
t t
頂件力
F = K F
(3.8)
d d
式中, Fx 、Ft 、Fd 分別是卸料力、推件力和頂件力( kN ); Kx 、Kt 、Kd 分別是卸料力、推件力和頂件力的系數(shù),其值可查; F 為沖裁力( kN );n 為同時卡在凹
模內(nèi)的工件數(shù)。n = h ,h 為凹模直壁洞口的高度( mm ),t 為板材厚度( mm )。
t
沖孔時的推件力
1
t
t
F = n ′ K ′ F
6
查相關(guān)資料得 Kt
n = = 3(個)。2
= 0.055 ,凹模刃口深度取6mm ,則卡在凹模洞口的工件數(shù)目為
代入 Ft
落料部分的卸料力
= 3′ 0.055′ 33424.8 = 5515.092(N )
2
x
x
查相關(guān)資料得 Kx
= 0.05 。
F = K ′ F
代入 Fx = 0.05′137161.681 = 6858.08(N )
選擇沖床時的總壓力為:
1 2 t x
F? = F + F + F + F
= 182959.653(N ) = 183(kN )
3.3.2 壓力中心的計算
選定坐標(biāo)系 xOy 如圖 3.6 所示,因沖件對稱于 x 軸,所以 yc
圖 3.6 壓力中心計算
= 0 。
L = 320
′p′ 48 = 134.04(mm) ; x
= 24sin(320o / 2)
= 2.9(mm) ;
1 360
2
L = 40
360
1
2
′p′ 70 = 24.43(mm) ; x = -
320 ′
2
40 ′
p
180
p
= -34.29(mm) ;
2 180
L = 2 ′(35 - 24) = 22(mm) ; x = -? 24 + 35 ?cos 20° = -27.72(mm);
3 3 ? ÷
è 2 ?
4
4
L =p′14 = 43.98(mm); x = 0
L x + L x + L x + L x
2
3
4
1
x = 1 1 2 2 3 3 4 4
= -4.65
L
3.4 壓力設(shè)備的選擇
L + L
+ L + L
3.4.1 壓力機公稱壓力的確定
在沖裁工序中,壓力機的公稱壓力是大于或等于沖裁時總壓力的 1.1~1.3 倍,即
?
P 3 (1.1 ~ 1.3)F
式中 P ——壓力機的公稱壓力, N ;
F? ——沖裁時的總沖壓力, N 。根據(jù)上述公式,計算得出201255 .6( N ) £
3.4.2 壓力機類型的確認(rèn)
P £ 237847 .5( N ) 。
(3.9)
根據(jù)201255 .6( N ) £
P £ 237847 .5( N ) ,即201(kN ) £
P £ 238 (kN ) ,
選定壓力機類型為開式雙柱可傾式壓力機 J 23 - 25 ,具體參數(shù)如表 3.4 所示。
表 3.4 開式雙柱可傾式壓力機 J 23 - 25
標(biāo)稱壓力
250 kN
滑塊行程
65 mm
行程次數(shù)
55 次/mm
最大閉合高度
270 mm
閉合高度調(diào)節(jié)量
55 mm
滑塊中心線到床身距離
200 mm
工作臺尺寸
左右 560mm
前后 370mm
工作臺孔尺寸
左右 290 mm
前后 200mm
直徑 260mm
模柄孔尺寸
φ40 mm×60 mm
床身最大可傾角(°)
30
3.5 刃口尺寸計算
3.5.1 刃口尺寸相關(guān)概念
在沖壓模具設(shè)計中,零件的精度主要依賴于凸、凹模刃口的尺寸。其中,凸模、凹模的刃口尺寸也決定著沖裁件的尺寸和沖模間隙。所以,沖裁模刃口尺寸及公差的正確與否是沖模設(shè)計中的一項重要指標(biāo)。
沖裁件的斷面具有明顯的區(qū)域性特征。斷面上可以分為四個區(qū),即光亮帶、剪裂帶、塌角和毛刺,光亮帶的尺寸決定著沖孔直徑和落料件外形尺寸。其中,落料件的尺寸接近于凹模刃口的尺寸,凸模刃口的尺寸則接近于沖孔的尺寸。在設(shè)計過程中,沖孔時應(yīng)取凸模為基準(zhǔn)件,落料時取凹模作為設(shè)計基準(zhǔn)件。首先,確定基準(zhǔn)件的刃口尺寸;然后, 根據(jù)間隙確定另一件的刃口尺寸。也就是說,沖孔時先按選定的間隙用以確定凸模的刃口尺寸,再按選定的間隙確定凹模的刃口尺寸;落料時則是先按落料件確定凹模刃口尺寸,再按選定的間隙確定凸模的刃口尺寸。落料與沖孔時沖模刃口與零件尺寸及其公差的關(guān)系如圖 3.7 所示。
圖 3.7 沖模刃口尺寸的確定
在沖裁過程中,沖模在使用過程中都會有磨損,所以沖孔的尺寸在加工過程中隨著凸模的磨損而減少,落料件的尺寸則會在加工過程中隨著凹模刃口的磨損而增大。沖孔時凸模刃口尺寸取靠近孔的公差范圍內(nèi)的最大尺寸,落料時凹模刃口的尺寸取接近落料件公差范圍內(nèi)的最小尺寸。在落料和沖孔的過程中,沖模間隙都要采用合理間隙范圍內(nèi)的最小值。
3.5.2 落料刃口尺寸計算
根據(jù)異型墊片的尺寸要求,可以得出落料件的尺寸為f48 、 R35;根據(jù)異型墊片的加工要求,可以得出公差等級為IT14 級,查詢相關(guān)書籍,得出公差均為D = 0.62mm ,
-0.62
根據(jù)入體原則可知落料尺寸分別為f480
0
R35、
-0.62
。所以,采用普通沖裁,凸、凹
= (D
0
模則分別按著 IT6、IT7 級加工制造。落料尺寸計算公式如下:
落料凹模
Dd max
- xD)+dd
(3.10)
落料凸模
D = (D
- Z
min
0
)
-dp
(3.11)
d
p
式中 Dd ——落料凹模刃口的名義尺寸(mm); Dp ——落料凸模刃口的名義尺寸(mm);
D ——沖裁件公差(mm);
Zmin ——最小雙邊合理間隙(mm),查表 3.5;
x ——磨損系數(shù),為了避免多數(shù)沖裁件尺寸都偏向極限尺寸(落料偏向
最小尺寸,沖孔偏向最大尺寸),可取系數(shù)值 x = 0.75 ~ 0.5;或者按制件公差在 IT10 以上時,取 x = 1;當(dāng)制件公差在 IT11~IT13 時,取 x = 0.75 ;當(dāng)制件公差在 IT14 下時,取 x = 0.5;
d 、d ——分別為凸模和凹模的制造公差,一般情況下取零件公差D 的
d p
1 4 ~ 1 6 ,也可以根據(jù)凸模按 IT6 級、凹模按 IT7 級查詢。上述計算完成后,用下列公式進行校核:
d
p
d
+ d £ Z
max
- Z
min
(3.12)
若滿足則按計算所得數(shù)值為刃口尺寸。
若不滿足,則取
d £ 0.4(Z
d
p
d £ 0.6(Z
max
max
min
- Z
- Z
)
)
min
(3.13)
(3.14)
根據(jù)校核所得數(shù)值,得出刃口尺寸。
表 3.5 沖裁模初始雙面間隙 Z (mm)
材料厚度 t
08、10、35、09Mn2、Q235
16Mn
40、50
65Mn
Zmin
Zmax
Zmin
Zmax
Zmin
Zmax
Zmin
Zmax
0.7
0.064
0.092
0.064
0.092
0.064
0.092
0.064
0.092
0.8
0.072
0.104
0.072
0.104
0.072
0.104
0.064
0.092
0.9
0.090
0.126
0.090
0.126
0.090
0.126
0.090
0.126
1.0
0.100
0.140
0.100
0.140
0.100
0.140
0.090
0.126
1.2
0.126
0.180
0.132
0.180
0.132
0.180
—
—
1.5
0.132
0.240
0.170
0.240
0.170
0.240
—
—
1.75
0.220
0.320
0.220
0.320
0.220
0.320
—
—
2.0
0.0246
0.360
0.260
0.380
0.260
0.380
—
—
-0.62
(1)f480
落料尺寸計算
Zmax
根據(jù)計算需要可知,D = 0.62mm ;Z 根據(jù)表 3.4 可知,取Z = 0.246mm ,
d
min min
= 0.360mm ;x = 0.5;查得 IT 6 = 0.016 、IT 7 = 0.025 ,得出d = 0.025,
d
p
= 0.016 。
(= D
綜上所述,根據(jù)公式 3.10、3.11 進行刃口尺寸計算:
落料凹模
Dd max
- xD)+dd
= (48 - 0.5′ 0.62)+0.025
0
0
0
d
p
= 47.69+0.025
落料凸模
D = (D
- Z
min
0
)
-dp
= (47.69 - 0.246)0
-0.016
-0.016
= 47.4440
根據(jù)公式 3.12 進行尺寸校核:
d
p
d
+ d = 0.025 + 0.016 = 0.041
Z - Z
max min
= 0.360 - 0.246 = 0.114
d
p
滿足 d + d
£ Z
max
- Z
min
所以,落料凹模 Dd
= 47.69+0.025 mm ;落料凸模 D
= 47.4440
mm 。
0
-0.016
-0.62
p
(2) R350
落料尺寸計算
Zmax
根據(jù)計算需要可知,D = 0.62mm ;Z 根據(jù)表 3.5 可知,取Z = 0.246mm ,
d
min min
= 0.360mm ;x = 0.5;查得 IT 6 = 0.016 、IT 7 = 0.025 ,得出d = 0.025,
d
p
= 0.016 。
(= D
綜上所述,根據(jù)公式 3.10、3.11 進行刃口尺寸計算:
落料凹模
Dd max
- xD)+dd
= (35 - 0.5′ 0.62)+0.025
0
0
0
d
p
= 34.69+0.025
落料凸模
D = (D
- Z
min
0
)
-dp
= (34.69 - 0.246)0
-0.016
-0.016
= 34.4440
根據(jù)公式 3.12 進行尺寸校核:
d
p
d
+ d = 0.025 + 0.016 = 0.041
29
Z - Z
max min
= 0.360 - 0.246 = 0.114
d
p
滿足 d + d
£ Z
max
- Z
min
所以,落料凹模 Dd
= 34.69+0.025 mm ;落料凸模 D
= 34.4440
mm 。
0
-0.016
p
3.3.3 沖孔刃口尺寸計算
0
根據(jù)異型墊片的尺寸要求,可以得出沖孔件的尺寸為f14 ;根據(jù)異型墊片的加工要求,可以得出公差等級為 IT14 級,查詢相關(guān)書籍,得出公差均為D = 0.43mm ,根據(jù)入體原則可知沖孔尺寸為f14+0.43 。所以,采用普通沖裁,凸、凹模則分別按著 IT6、
IT7 級加工制造。
沖孔尺寸計算公式如下:
沖孔凸模
d = (d
min
+ xD)0
(3.15)
-dp
p
沖孔凹模
d = (d
+ Z
min
+dd
)
0
(3.16)
d
p
式中 dp ——沖孔凸模刃口的名義尺寸(mm);
dd ——沖孔凹模刃口的名義尺寸(mm);
D ——沖裁件公差(mm);
Zmin ——最小雙邊合理間隙(mm),查表 3.5;
x ——磨損系數(shù),為了避免多數(shù)沖裁件尺寸都偏向極限尺寸(落料偏
向最小尺寸,沖孔偏向最大尺寸),可取系數(shù)值 x = 0.75 ~ 0.5 ;或者按制件公差在IT10 以上時,取 x = 1;當(dāng)制件公差在 IT11~IT13 時,取 x = 0.75 ;當(dāng)制件公差在 IT14 下時,取 x = 0.5;
d 、d ——分別為凸模和凹模的制造公差,一般情況下取零件公差D 的
d p
1 4 ~ 1 6 ,也可以根據(jù)凸模按 IT6 級、凹模按 IT7 級查詢。上述計算完成后,校核方式和落料校核方式相同。
0
f14+0.43 沖孔尺寸計算
min min
根據(jù)計算需要可知,D = 0.62mm ;Z 根據(jù)表 3.5 可知,取Z = 0.246mm ,
Zmax
= 0.360mm ;x = 0.5;查得 IT 6 = 0.011、IT 7 = 0.018 ,得出d = 0.018,
d
d
p
= 0.011 。
綜上所述,根據(jù)公式進行公式 3.15、3.16 進行刃口尺寸計算:
-dp
p
沖孔凸模
d = (d
min
+ xD)0
= (14 + 0.5′ 0.43)0
-0.011
-0.011
= 14.2150
d
p
沖孔凹模
d = (d
+ Z
min
+dd
)
0
= (14.215 + 0.246)+0.018
0
0
= 14.461+0.018
根據(jù)公式 3.12 進行尺寸校核:
d
p
d
+ d = 0.011 + 0.018 = 0.039
Z - Z
max min
= 0.360 - 0.246 = 0.114
d
p
滿足 d + d
£ Z
max
-0.011
0
- Z
min
所以,沖孔凸模dp
= 14.2150
mm ,沖孔凹模dd
= 14.461+0.018 mm 。
4 模具主要零部件的設(shè)計和選擇
一套完整的沖模零部件包括工藝結(jié)構(gòu)零件和輔助結(jié)構(gòu)零件。
直接參與完成工藝過程、坯料直接發(fā)生作用的零件被稱為是工藝結(jié)構(gòu)零件。它又包括工作零件(直接對毛坯進行加工的零件:凸模、凹模、凸凹模),定位零件(確定加工毛坯正確位置的零件:擋料銷和導(dǎo)正銷、導(dǎo)尺、定位銷/板、側(cè)壓板、側(cè)刀),壓料、卸料及出件零件(下料板、壓邊圈、頂件器、推件器)。
不直接參與完成工藝過程、也不和坯料直接發(fā)生作用的零件被稱為是輔助結(jié)構(gòu)零件,它只對模具完成工藝過程起保證作用或?qū)δ>叩墓δ芷鹜晟谱饔?。其中,它包括?dǎo)向零件(用以保證模具上、下部分正確的相對位置:導(dǎo)柱、導(dǎo)套、導(dǎo)板、導(dǎo)筒),固定零件(用以承裝模具零件或?qū)⒛>甙惭b固定到壓機上:上/下模板、模柄、凸/凹模固定板、墊板、限制器),緊固及其他零件(用以聯(lián)接緊固工藝零件與輔助零件:螺釘、釘、鍵、其他)。模具整體結(jié)構(gòu)可以分為上模和下模。
4.1 標(biāo)準(zhǔn)模架的選取
對于整套模架而言,包括四部分,即上模座、下模座、導(dǎo)柱和導(dǎo)套。在沖壓過程中, 為了降低成本和縮短模架的制造周期,我國制定了一套標(biāo)準(zhǔn)的模架。模架的導(dǎo)向是根據(jù)導(dǎo)柱和導(dǎo)套間的配合得來的,模架分為滑動導(dǎo)向模架和滾動導(dǎo)向模架兩大類。模架類型主要有后側(cè)導(dǎo)柱式、中間導(dǎo)柱式、對角導(dǎo)柱式和四角導(dǎo)柱式。
根據(jù)凹模的輪廓尺寸和模具的閉合高度選擇模架。在本次設(shè)計中,根據(jù)零件的需求, 設(shè)計凹模形狀為矩形結(jié)構(gòu),它的主要尺寸為f48mm 和 R35mm 。根據(jù)公式計算出凹
模的尺寸,如圖 4.1 所示。
圖 4.1 凹模尺寸的確定
凹模高度
H = Kl (3 15mm)
(4.1)
凹模壁厚(或刃口到外邊緣的距離)
c = (1.5 ~ 2)H (3 30 ~ 40mm)
式中 l ——沖裁件最大外形尺寸, mm ;
K ——系數(shù),考慮毛坯厚度的影響,其值可查表 4.1。
表 4.1 系數(shù) K 值
(4.2)
b t
0.5
1
2
3
>3
<50
0.3
0.35
0.42
0.5
0.6
50~100
0.2
0.22
0.28
0.35
0.42
100~200
0.15
0.18
0.2
0.24
0.3
>200
0.1
0.12
0.15
0.18
0.22
根據(jù)零件的具體尺寸可知, b = 59mm , K = 0.28。計算可知,凹模高度
H = Kb = 0.28′ 59 = 16.52 ? 17
本次設(shè)計中,彈性元件的選擇設(shè)定為卸料橡膠,同時考慮到凹模型腔中需要安放卸
料橡膠,所以凹模厚度即凹模高度應(yīng)適當(dāng)?shù)脑黾?,實際取 H 凹模壁厚
= 30mm 。
c = (1.5 ~ 2)H
確定凹模壁厚c = 50mm 。
= 42 ~ 56
根據(jù) H 、c 、圖 4.1 和排樣設(shè)計,確定 L 和 B 的尺寸即凹模的外形尺寸: 長度、寬度和高度為160 ′160 ′ 30 。
min
模具的閉合高度 H 應(yīng)介于壓力機的最大裝模高度之間,一般取
H max
與最小裝模高度
H min
max
H - 5 3 H
3 H +10
(4.3)
即 270 - 50 - 5 3 H 3 270 - 50 - 55 +10
得出 175 £ H £ 215
根據(jù)凹模的外形尺寸和模具的閉合高度,選定模架的類型為后側(cè)導(dǎo)柱模具,規(guī)格為
Ⅰ級精度的后側(cè)導(dǎo)柱模架:模架160 ′160 ′180 ~ 220I ,GB / T 2851.3。模架各部分的主要參數(shù)如下表 4.2 所示。
表 4.2 模架各部件主要參數(shù)
名稱
規(guī)格(mm)
材料
標(biāo)準(zhǔn)代號
上模座
160×160×40
HT200
GB/T2855.5
下模座
160×160×45
HT200
GB/T2855.6
導(dǎo)柱
28×170
HT200
GB/T2861.1
導(dǎo)套
28×100×38
HT200
GB/T2861.8
工作臺:160×160
4.2 上模
4.2.1 凹模
根據(jù)常見的凹??卓谛问?,選擇凹??卓谛褪饺鐖D 4.1 所示,即直筒型刃口;根據(jù)常見的凹模固定方式,選擇凹模固定方式選擇為整體式或組合式,用螺釘、銷釘直接緊固凹模。凹模的常用材料有T10 A 、9Mn2V 、Cr12 、Cr6WV ,本次設(shè)計凹模材料選用為Cr12 。
圖 4.2 凹??卓谛褪?圖 4.3 凹模尺寸的確定
根據(jù)模架選擇要求可知,凹模的外形尺寸為長度、寬度和高度為160 ′160 ′ 30 。
4.2.2 凸模固定板
凸模固定板的作用是將凸模聯(lián)接固定在模板上的正確位置,還要保證定位銷釘和緊固螺釘?shù)恼?/div>
收藏