畢業(yè)設計支架注塑模具
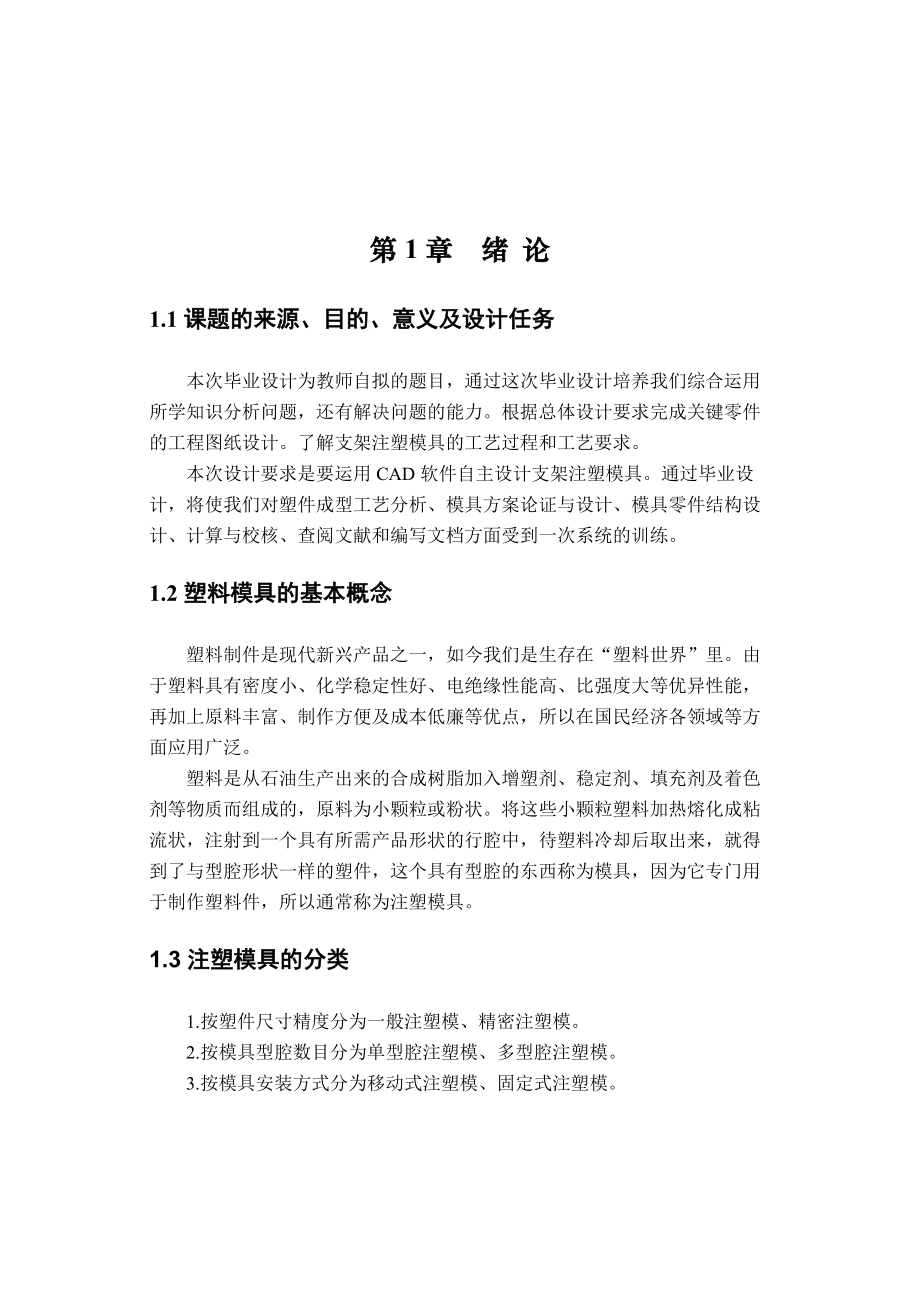


《畢業(yè)設計支架注塑模具》由會員分享,可在線閱讀,更多相關《畢業(yè)設計支架注塑模具(38頁珍藏版)》請在裝配圖網(wǎng)上搜索。
1、第1章 緒 論1.1課題的來源、目的、意義及設計任務本次畢業(yè)設計為教師自擬的題目,通過這次畢業(yè)設計培養(yǎng)我們綜合運用所學知識分析問題,還有解決問題的能力。根據(jù)總體設計要求完成關鍵零件的工程圖紙設計。了解支架注塑模具的工藝過程和工藝要求。本次設計要求是要運用CAD軟件自主設計支架注塑模具。通過畢業(yè)設計,將使我們對塑件成型工藝分析、模具方案論證與設計、模具零件結構設計、計算與校核、查閱文獻和編寫文檔方面受到一次系統(tǒng)的訓練。1.2塑料模具的基本概念塑料制件是現(xiàn)代新興產(chǎn)品之一,如今我們是生存在“塑料世界”里。由于塑料具有密度小、化學穩(wěn)定性好、電絕緣性能高、比強度大等優(yōu)異性能,再加上原料豐富、制作方便及成
2、本低廉等優(yōu)點,所以在國民經(jīng)濟各領域等方面應用廣泛。塑料是從石油生產(chǎn)出來的合成樹脂加入增塑劑、穩(wěn)定劑、填充劑及著色劑等物質而組成的,原料為小顆?;蚍蹱?。將這些小顆粒塑料加熱熔化成粘流狀,注射到一個具有所需產(chǎn)品形狀的行腔中,待塑料冷卻后取出來,就得到了與型腔形狀一樣的塑件,這個具有型腔的東西稱為模具,因為它專門用于制作塑料件,所以通常稱為注塑模具。1.3注塑模具的分類1.按塑件尺寸精度分為一般注塑模、精密注塑模。2.按模具型腔數(shù)目分為單型腔注塑模、多型腔注塑模。3.按模具安裝方式分為移動式注塑模、固定式注塑模。4.按塑料材料類別分為熱塑性注塑模、熱固性塑料注塑模。5.按注塑機類型分為臥式注塑模、立
3、式注塑模和直角式注塑模。6.按模具澆注系統(tǒng)分為冷流道模、絕熱流道模、熱流道模、溫流道模。7.按注塑模的總體結構特征分為單分型面注塑模、雙分型面注塑模、帶活動成型零件的注塑模、帶側向分型抽芯的注塑模、自動卸螺紋注塑模、無流道注塑模。1.4我國塑料模具發(fā)展趨勢分析我國注塑模具工業(yè)起步晚,底子薄,與工業(yè)發(fā)達的國家相比存在很大的差距。但在國家產(chǎn)業(yè)政策和與之配套的一系列國家經(jīng)濟政策的支持和改革及開放方針引導下,我國注塑模得到迅速發(fā)展,高效率、自動化、大型、微型、精密、無流道、氣體輔助、高壽命模具在整個塑料模具產(chǎn)量所占的比重越來越大。從模具設計和制造技術方面來看,注塑成型模具的發(fā)展趨勢可歸納為以下幾方面。
4、1.模具產(chǎn)品將向著更大型、更精密、更復雜及更經(jīng)濟快速方向發(fā)展;模具生產(chǎn)將朝著信息化、無圖化、精細化、自動化方向發(fā)展;模具企業(yè)將向著技術集成化、設備精良化、產(chǎn)品品牌化、管理信息化、經(jīng)營國際化方向發(fā)展。2.模具CADCAECAMPDM正向集成化、三維化、智能化、網(wǎng)絡化和信息化方向發(fā)展??旖莞咚俚男畔⒒瘯r代將帶領模具行業(yè)進入新時代。3.模具的質量、周期、價格、服務四要素中,已有越來越多的用戶將周期放在首位,要求模具盡快交貨,因此模具生產(chǎn)周期將繼續(xù)不斷縮短。4.大力提高開發(fā)能力,將開發(fā)工作盡量往前推,直至介入到模具用戶的產(chǎn)品開發(fā)中去,甚至在尚無明確的用戶對象之前進行開發(fā)(這需要在有較大把握和敢冒一定風
5、險的情況下進行),變被動為主動。以及“你給我一個概念,我還你一個產(chǎn)品”的一站式服務模式都已成為發(fā)展趨勢。5.隨著模具企業(yè)設計和加工水平的提高,過去以鉗工為核心,大量依靠技藝的現(xiàn)象已有了很大變化。在某種意義上說:“模具是一種工藝品”的概念正在被“模具是一種高新技術工業(yè)產(chǎn)品”所替代,模具“上下模單配成套”的概念正在被“只裝不配的概念所替代。模具正從長期以來主要依靠技藝而變?yōu)榻窈笾饕揽考夹g。這不但是一種生產(chǎn)手段的改變,也是一種生產(chǎn)方式的改變,更是一種觀念的改變。這一趨向使得模具標準化程度不斷提高,模具精度越來越高,生產(chǎn)周期越來越短,鉗工比例越來越低,最終促使整個模具工業(yè)水平不斷提高。6.高速加工、
6、復合加工、精益生產(chǎn)、敏捷制造及新材料、新工藝、新技術將不斷得到發(fā)展。據(jù)有關方面預測,模具市場的總體趨勢是平穩(wěn)向上的,在未來的模具市場中,塑料模具發(fā)展速度將高于其它模具,在模具行業(yè)中的比例將逐步提高。隨著塑料工業(yè)的不斷發(fā)展,對塑料模具提出越來越高的要求是正常的,因此,精密、大型、復雜、長壽命塑料模具的發(fā)展將高于總量發(fā)展速度。同時,由于近年來進口模具中,精密、大型、復雜、長壽命模具占多數(shù),所以,從減少進口、提高國產(chǎn)化率角度出發(fā),這類高檔模具在市場上的份額也將逐步增大。建筑業(yè)的快速發(fā)展,使各種異型材擠出模具、PVC塑料管材接頭模具成為模具市場新的經(jīng)濟增長點,高速公路的迅速發(fā)展,對汽車輪胎也提出了更高
7、要求,因此子午線橡膠輪胎模具,特別是活絡模的發(fā)展也將高于總平均水平;以塑代木,以塑代金屬使塑料模具在汽車、摩托車工業(yè)中的需求量巨大;家用電器行業(yè)在“十五”期間將有較大發(fā)展,特別是電冰箱、空調器和微波爐等的零配件的塑料模需求很大;而電子及通訊產(chǎn)品方面,除了彩電等音像產(chǎn)品外,筆記本電腦和網(wǎng)機頂盒將有較大發(fā)展,這些都是塑料模具市場的增長點。1.5注塑成型原理1.注塑成型:指將注射用的置于能加熱的料筒內,受熱、塑化,再施加壓力,使熔體塑料注入到所需形狀的模具中,經(jīng)過冷卻定型后脫模,得到所需形狀的制品。2.注塑成型三要素:注塑機、模具、原料。1.6注塑機的種類1.按合模裝置的特征分類按合模裝置的特征可分
8、為液壓式、液壓機械式和機械式注塑機。2.按注塑機的用途分類按用途可分為通用和專用注塑機。專用注塑機又可分為熱固性型、排氣型、轉盤式玻璃纖維增強塑料等注塑機。3.按注塑機加工能力分類注塑機加工能力主要由合模力和注塑量參數(shù)表示,國際上通用的表示法是同時采用注塑量和合模力來表示。按其加工能力可分為超小型、小型、中型、大型、和超大型注塑機。4.按設備外形特征分類(1)臥式注塑機臥式注塑機是最常見的形式。其合模裝置和注塑裝置的軸線呈水平一線排列。它具有機身低,易于操作和維修,自動化程度高,安裝較平穩(wěn)等特點,是目前應用最廣泛的一種。(2)立式注塑機注塑機的合模裝置和注塑裝置的軸線呈垂直一線排練。(3)角式
9、注塑機注塑機的合模裝置和注塑裝置的軸線互成垂直排列。第二章 支架的工藝分析支架的零件圖該支架所用的材料是ABS塑料,大(小)批量生產(chǎn)。2.1材料性能ABS塑料為淺黃色粒狀或珠狀不透明樹脂,無毒、無味,吸水率低。收縮率為0.30.8,密度為1.031.07g/cm3,抗彎強度41-76MPa,拉伸彈性模量1587-2277MPa,允許含水量0.10%。具有優(yōu)良的物理機械性能,極好的低溫抗沖擊性能,優(yōu)良的電性能、耐磨性、尺寸穩(wěn)定性、耐化學性、染色性。易于加工成型。ABS耐水、無機鹽、堿和酸類,不溶于大部分醇類和烴類溶劑,易溶于醛、酮、酯及某些氯化烴中。ABS的缺點是可燃,熱變形溫度較低,耐侯性較差
10、。燃燒特點:易燃;離火繼續(xù)燃燒;火焰黃色,濃黑煙;軟化,起泡;丙烯腈味。廣泛應用于制造汽車內飾件、電器外殼、手機、電話機殼、旋鈕、儀表盤等諸多方面。2.2成型特性1.吸收性能強,塑料在成型前必須充分預熱干燥,含水量應小于0.3%。對于要求表面光澤的零件,塑料在成型前更應進行長時間的預熱干燥。2.流動性中等,溢邊值0.04mm.。3.塑料的加熱溫度對塑料的質量影響較大,溫度過高易于分解(分解溫度是250度)。成型時采用較高的加熱溫度和較高的注射壓力。2.3結構工藝性零件壁厚基本均勻,所有壁厚均大于塑件的最小壁厚0.8mm,注射成型時應不會發(fā)生填充不足現(xiàn)象。2.4支架塑件體積、質量計算運用Pro/
11、E軟件分析可得:(1)單個塑件體積 V=5.34 cm3 ,質量m=5.341.05=5.61g。(2)兩個塑件和澆注系統(tǒng)凝料 總體積V總 =16.02 cm3 ,總質量m總 =16.82g2.5選擇注塑機塑件的材料為ABS,其密度為1.031.07g/cm3,取其平均密度為1.05g/cm3。使用Pro/E軟件畫出外殼的三維實體圖,應用軟件自動計算出圖形的體積為V塑=5.34cm3,,所以塑件的質量Mz =V塑=1.05g/cm35.34cm3=5.61g。注塑機的實際注射量通常為理論注射量的80%左右。其注射量應大于塑件體積與澆注系統(tǒng)體積之和,綜合意識所述,初步選定注塑機為XSZY60型。
12、其技術參數(shù)見表-1 機型編號XSZY60螺桿直徑mm38噴嘴球半徑mm12 孔半徑4最大注塑量cm3/g 60注射壓力MPa122鎖模力KN500最大注塑面積cm3/ 130模具最大厚度mm200模具最小厚度mm70 最大開模行程 mm 180 定位圈直徑mm55頂出中心孔徑Mm55模板尺寸mm330440機器外型尺寸(LWH)mm31608501550表-1注塑機XSZY60型注塑機相關參數(shù)的校核:1.最大注射量校核最大注射量和制品的質量或體積有直接關系。兩者必須相適應,不然會影響制品產(chǎn)量和質量.若最大注射量小于制品的質量,就會造成制品的形狀不完整或內部組織疏松,制品強度下降等缺陷;而注射量
13、過大,注射機利用率低,浪費電能,而且可能導致塑料分解。因此,為了保證正常的注塑成型,注射機的最大注射量應稍大于制品的質量或體積(包括流道及澆口凝料和飛邊)。通常注射機的實際注射量最好在注射機的最大注射量的80%以內。當注射機最大注射量以最大注射容積標定時,為保證正常的注射成型,注射機的最大注射容積應等于或大于所需塑料容積,既KVVK是注射機最大注射量的利用系數(shù),一般取 K=0.8V是注射機最大注射量,cmV是所需塑料的容積(包括流道及澆口凝料和飛邊),cm因塑料的體積與壓縮率有關,所以所需塑料體積為 : V=KVK是塑料收縮率,K=0.5V是塑料制品的體積(包括流道及澆口凝料和飛邊) cm零件
14、質量為5.61 g,(1.05g/ cm), V=5.61(1+0.005)/1.05 g/ cm=5.37cm本模具澆注系統(tǒng)采用熱流道技術+冷流道+側澆口,無飛邊冷流道澆口凝料體積為Va1 cm,取Va=1 cmV= 0此外,以上計算中的V表示制品的總體積(包括流道及澆口凝料和飛邊)。所以V= n V+ nVa+ V n 為型腔數(shù); n=2V為一個塑料制品的體積,cmV a為澆注系統(tǒng)的體積,cmV為飛邊的體積,cmV=5.37cm+1 cm= 6.37cm根據(jù)XSZY60型注射機機械參數(shù)表知:實際射膠量=理論射膠量0.9=60cmV=60 cmKV=48 cm 6.37cm=V2.注射壓力校
15、核注射壓力校核的目的是校驗注射機的最大注射壓力能否滿足塑料制品成型的需要。為此,注射機的最大注射壓力應稍大于塑料制品成型所需的注射壓力。p pp是注射機的最大注射壓力,Mpa查表得知其注射壓力為122Mpa.p是塑料制品成型時所需的注射壓力,MPa,它由注射機類型,噴嘴形式,塑料流動性,澆注系統(tǒng)及型腔的流動阻力等因素確定,一般p=40100MPa。根據(jù)經(jīng)驗得知:p p3.鎖摸力的校核鎖模力又稱合模力,是指注射機的合模裝置對模具所施加的最大夾緊力。當溶體充滿型腔時,注射壓力在型腔內所產(chǎn)生的作用力總是力圖使模具延分型面張開,為此,注射機的鎖模力必須大于型腔內熔體壓力與塑料制品及澆注系統(tǒng)在分型面上的
16、投影面積之和的乘積。而型腔內的塑料經(jīng)過注射機的噴嘴和模具的澆注系統(tǒng)后,其壓力損失很大。故p = K pp是型腔內熔體壓力,MPap是柱塞或螺桿施加于料筒熔體的壓力,MPaK是壓力損失系數(shù),一般取K=1/32/3。型腔內熔體壓力的大小及其分布與很多因素有關,如塑料流動性,注射機類型,噴嘴形式,模具流道阻力,注射壓力,注射速度,塑料制品壁厚與形狀等等。在工程實際中,可以用型腔平均壓力來校核。F p AF是注射機公稱鎖模力,N;A是塑料制品及澆注系統(tǒng)在分型面上的投影面積之和,m注射機允許的最大成型面積 A= A 4.模具與注射機合模部分相關尺寸的校核.設計模具時應校核的主要參數(shù)有噴嘴尺寸,定位圈尺寸
17、,模具最大厚度和最小厚度,模板上安裝螺孔尺寸等(1)注射機噴嘴與模具主流道襯套的關系注射機噴嘴前端徑孔d與模具主流道襯套的小端直徑D的關系為:D=d+(0.51)(2)注射機定位板與定位圈的關系兩者按H7/h6配合,以保證模具主流道的軸線重合,否則將產(chǎn)生溢料并造成流道凝料脫模難。定位環(huán)高度h=10mm (3)模具輪廓尺寸與注射機裝??臻g的關系各種規(guī)格的注射機,可安裝模具的最大厚度和最小厚度均有限制,所以,設計的模具閉合厚度必須在模具最大厚度和最小厚度自之間。HHH H= H+HH是模具閉合厚度,205mm;H是注射機允許模具最小厚度,70mm;H是注射機允許模具最大厚度,210mm;H是注射機
18、調節(jié)螺母長度,mm。第三章 支架塑料模具設計3.1塑料模具設計的一般流程一、接受任務書1.經(jīng)過審簽的正規(guī)制制件圖紙,并注明采用塑料的牌號、透明度等。2.塑料制件說明書或技術要求。3.生產(chǎn)產(chǎn)量。4.塑料制件樣品。二、收集、分析、消化原始資料收集整理有關制件設計、成型工藝、成型設備、機械加工及特殊加工資料,以備設計模具時使用。1.消化塑料制件圖,了解制件的用途,分析塑料制件的工藝性,尺寸精度等技術要求。2.消化工藝資料,分析工藝任務書所提出的成型方法、設備型號、材料規(guī)格、模具結構類型等要求是否恰當,能否落實。3.確定成型方法采用直壓法、鑄壓法還是注射法。4.選擇成型設備根據(jù)成型設備的種類來進行模具
19、,因此必須熟知各種成型設備的性能、規(guī)格、特點。5. 具體結構方案(1)確定模具類型(2)確定模具類型的主要結構三、影響模具結構及模具個別系統(tǒng)的因素很多,很復雜:1.型腔布置。根據(jù)塑件的幾何結構特點、尺寸精度要求、批量大小、模具制造難易、模具成本等確定型腔數(shù)量及其排列方式。2.確定分型面。分型面的位置要有利于模具加工,排氣、脫模及成型操作,塑料制件的表面質量等。3.確定澆注系統(tǒng)和排氣系統(tǒng)。4.選擇頂出方式,決定側凹處理方法、抽芯方式。5.決定冷卻、加熱方式及加熱冷卻溝槽的形狀、位置、加熱元件的安裝部位。6.根據(jù)模具材料、強度計算或者經(jīng)驗數(shù)據(jù),確定模具零件厚度及外形尺寸,外形結構及所有連接、定位、
20、導向件位置。7.確定主要成型零件,結構件的結構形式。8.考慮模具各部分的強度,計算成型零件工作尺寸。四、繪制模具圖在畫模具總裝圖之前,應繪制工序圖,并要符合制件圖和工藝資料的要求。由下道工序保證的尺寸,應在圖上標寫注明工藝尺寸字樣。如果成型后除了修理毛刺之外,再不進行其他機械加工,那么工序圖就與制件圖完全相同。在工序圖下面最好標出制件編號、名稱、材料、材料收縮率、繪圖比例等。通常就把工序圖畫在模具總裝圖上。五、模具總裝圖應包括以下內容:1.模具成型部分結構2.澆注系統(tǒng)、排氣系統(tǒng)的結構形式。3.分型面及分模取件方式。4.外形結構及所有連接件,定位、導向件的位置。5.標注型腔高度尺寸及模具總體尺寸
21、。6.輔助工具。7.按順序將全部零件序號編出,并且填寫明細表。8.標注技術要求和使用說明。六、模具總裝圖的技術要求內容:1.對于模具某些系統(tǒng)的性能要求。2.對模具裝配工藝的要求。3.模具使用,裝拆方法。4.防氧化處理、模具編號、刻字、標記、油封、保管等要求。5. 有關試模及檢驗方面的要求。七、繪制全部零件圖由模具總裝圖拆畫零件圖的順序應為:先內后外,先復雜后簡單,先成型零件,后結構零件。1.圖形要求:一定要按比例畫,允許放大或縮小。2.標注尺寸要求統(tǒng)一、集中、有序、完整。3.表面粗糙度。把應用最多的一種粗糙度標于圖紙右上角。4.其它內容,例如技術說明等都要正確填寫。八、.校對、審圖、描圖、送曬
22、A.自我校對的內容是:1.模具及其零件與塑件圖紙的關系2.塑料制件方面3.成型設備方面4.模具結構方面5.設計圖紙6.校核加工性能7.復算輔助工具的主要工作尺寸B.專業(yè)校對原則上按設計者自我校對項目進行。C.把描好的底圖交設計者校對簽字。D.編寫制造工藝卡片。九、試模及修模十、整理資料進行歸檔3.2塑料模具的結構塑料模具依總體功能結構可分為:成型系統(tǒng)、澆注系統(tǒng)、排氣系統(tǒng)、冷卻系統(tǒng)、頂出系統(tǒng)等。3.3模具結構設計3.3.1行腔數(shù)目的確定行腔的排列方式塑件的在注射時采用一模兩件,即模具需要兩個型腔,綜合考慮澆注系統(tǒng)、模具結構的復雜程度等因素,行腔的排列方式應具備以下優(yōu)點:1. 經(jīng)濟性好。2. 采用
23、平衡式排列,便于構成平衡式的澆注系統(tǒng),保證制品質量的均勻和穩(wěn)定。3. 型腔布置和澆口開設部位對稱,防止了模具受偏載面出現(xiàn)溢料現(xiàn)象。4. 型腔排列得緊湊,減小了模具的外形尺寸,合理利用了模具的各個結構。由塑件的體積選擇設備型號規(guī)格,確定行腔數(shù)。N=(0.8mg-mj)/mz n為型腔數(shù)mj澆注系統(tǒng)mz塑件重量mg注射機額定注射量V i澆注系統(tǒng)體積由塑件精度一般,塑件為大批量生產(chǎn),故選擇多型腔n=23.3.2分型面的選擇塑料在模具型腔凝固形成塑件,為了將塑件取出來,必須將模具型腔打開,也就是必須將模具分成兩部分,即定模和動模兩大部分。簡單的說,分型面就是動模和定模或瓣合模的接觸面。常見的分型面形狀
24、有平面、斜面、階梯面、曲面。由分型面開模方式有平行于開模方向、垂直與開模方向、與開模方向呈一斜角。分型面的選擇好壞對塑件質量、操作難易、模具結構及制造都有很大的影響。通常遵循以下原則:1.有利于脫模分型面應取在塑件尺寸最大處、分型面應使塑件留在動模部分和將分型面選在塑件的中間部分。2.有利于保證塑件的外觀質量和精度要求為了保證塑料制品的質量,對有同軸度要求的塑料制品,應將有同軸度要求的部分設在同一模板內。3.有利于成型零件的加工制造4.有利于側向抽芯當塑料制品有側孔或側凹時,應盡可能的將側型心設在動模部分,以便于抽芯。5.分型面應選在塑件外形最大輪廓處便于塑件脫模,盡量使塑件開模時留在動模一邊
25、。6.分型面的選擇有利于排氣為了便于排氣,一般分型面應盡可能與熔體流動的末端重合??紤]以上選擇原則,同時為使側型芯處于動模部分,選水平分型面。3.3.3澆注系統(tǒng)的設計澆注系統(tǒng)是指注塑模具中從注塑機噴嘴開始到型腔入口為止的塑料溶體的流動通道。它的作用是將塑料溶體順利地充滿型腔的各個部分,并在填充及保壓過程中,將注射壓力傳遞到型腔的各個部位,以獲得外形清晰、內在質量良好的塑件。正確設計澆注系統(tǒng)對獲得優(yōu)良的塑料制品極為重要。3.3.3.1澆注系統(tǒng)的設計原則1.排氣良好 能順利地引導熔融塑料填充到型腔的各個深度,不產(chǎn)生渦流和紊流,并能使型腔內的氣體順利排出。2.流程短 在滿足成型和排氣良好的前提下,要
26、選取短的流程來填充型腔,且應盡量減少彎折,以降低壓力損失,縮短填充時間。3.防止型芯和嵌件變形 應盡量避免熔融塑料正面沖擊直徑較小的型芯和金屬嵌件,防止型芯彎曲變形和嵌件移位。4.整修方便 澆口位置和形式應結合塑件形狀考慮,做到整修方便并無損塑件的外觀和使用。5.防止塑件翹曲變形 在流程較長或需開設兩個以上澆口是更應注意這一點。6.合理設計冷料穴或溢料槽 冷料穴或溢料槽設計是否合理,直接影響塑件質量。7.澆注系統(tǒng)的斷面面積和長度 除滿足以上各點外,澆注系統(tǒng)的斷面面積和長度應盡量取小值,以減少澆注系統(tǒng)占用的塑料量,從而減少回收料。3.3.3.2主流道的設計主流道是連接注塑機與分流道的異端通道,通
27、常和注塑機的噴嘴在同一軸線上,斷面為圓形,帶有一定的錐度。主流道的設計要點:1.為便于從主流道中拉出澆注系統(tǒng)的凝料,以及考慮塑料溶體的膨脹,主流道設計成圓錐形。錐角為2度到4度。內壁表面粗糙度Ra 為0.63微米。2.主流道大端呈圓角,其半徑常取 r=13mm,以減小料流轉向過渡時的阻力。3.在保證塑件成型良好的情況下,主流道的長度盡量短,否則將會使主流道的凝料增多,且增加壓力損失,是塑料溶體降溫過多而影響注塑成型。4.為了使熔融塑料從噴嘴完全進入主流道而不溢出,其半徑R=R1+(12)mm,其小端直徑D=d+(0.51)mm,凹坑深度常取34mm5.由于主流道要與高溫的塑料溶體和噴嘴反復接觸
28、和碰撞,所以主流道部分常設計成可拆卸的主流道澆口套,以便選用優(yōu)質鋼材單獨加工和熱處理。3.3.3.3澆口套的選擇1.根據(jù)塑料成型工藝與模具設計圖4-187可知:型號為XSZY60型注塑機的噴嘴直徑公式為:d=注射機噴嘴直徑+0.5mm=4.5mm根據(jù)塑料模具設計可知:下端直徑D=8 mm (D為澆口套進料口直徑)注塑機的噴嘴球頭半徑為:r=12mm 。根據(jù)塑料模具設計的公式球面凹坑半徑:R=r+(0.51)mm=12+(0.51)mm=12.5mm13mm2.澆口套與定模板、定位環(huán)的配合根據(jù)塑料模具設計的第四章“塑料注塑模結構設計”可知:澆口套與定模板的配合采用H7/m6,澆口套與定位環(huán)的配合
29、采用H6/h7。3.選定澆口套根據(jù)以上計算可知:澆口套進料口直徑D=8mm;球面凹坑半徑R=13mm;則查實用注塑成型及模具設計圖2選定澆口套形式。選a型澆口套圖2澆口套的類型3.3.3.4澆口設計原則及位置選擇澆口是連接流道與形腔之間的一段細短通道,是澆注系統(tǒng)的關鍵部分,起著調節(jié)控制料流速度、補料時間及防止倒流作用。澆口的形狀、尺寸和進料位置等對塑件成型質量影響很大,塑件上的一些缺陷,如缺料、白斑、熔接痕、翹曲等往往是由于澆口設計不合理產(chǎn)生的。正確設計澆口是提高塑件質量的重要環(huán)節(jié)。一、澆口設計的原則:(1)澆口尺寸及位置選擇應避免熔體破裂而產(chǎn)生噴射和蠕動。(2)澆口位置應有利于流動、排氣和補
30、料。(3)澆口位置應使流程最短,料流變向最少,并防止型心變形。(4)澆口位置及數(shù)量應有利于減少熔接痕和增加熔接強度。(5)澆口位置應盡量開設在不影響塑件外觀的部位。二、澆口的類型在注塑模設計中常用的澆口有以下幾種類型:1直接澆口直澆口又稱中心澆口,這種澆口的流動阻力小,進料速度快,在單型腔模具中常用來成型大而深的塑件,它適應各種塑料,特別是黏度高、流動性差的塑料2側澆口側澆口又稱邊緣澆口,其斷面一般為矩形,通常開在分型面上,從塑件側面進料,可按需要合理選擇澆口位置,尤其適用于一模多腔。側澆口的厚度決定著澆口的固定時間,在實踐中通常是在容許的范圍內首先將側澆口的厚度加工得薄一些,在試模時再進行修
31、正,以調節(jié)澆口的固化時間。側澆口廣泛應用于中小型制品的多型腔注射模,其優(yōu)點是截面形狀簡單、易于加工、便于試模后修正,缺點是在制品的外表面留有澆口痕跡。對于不同形狀的塑件,根據(jù)成型的需要,側澆口可設計成多種變異形式。3點澆口點澆口又稱針點式澆口,是一種尺寸很小的澆口,塑料融體通過它有很高的剪切速率。它廣泛地應用于各類殼型塑件。開模時,澆口可自行拉斷。但是點澆口截面積較小,冷凝快,不利于補縮,對壁厚較厚的塑件不宜使用。4潛伏式澆口又稱剪切澆口,是由點澆口演變而來,點澆口用于三板模,而潛伏式澆口用于兩板模,從而簡化了模具結構。潛伏式澆口設在塑件內側或外惻隱蔽部位,不影響塑件的外形美觀。在推出塑件時澆
32、口被切斷,但需要有較強的推力,對強韌的塑料不宜采用。三、確定澆口的參數(shù)綜上所述,澆口選擇側澆口。當塑件材料為ABS,壁厚為1.53mm時,側澆口直徑的推薦值為0.52mm,所以選擇側澆口直徑為1mm。由于塑件質量較小,為小型塑件,起流動比不用校核。所以其澆注系統(tǒng)可以確定。如圖5圖5澆注系統(tǒng)3.3.4成型零件結構設計成型零部件的結構設計主要是凸、凹模的結構設計,應在保證塑件質量的前提下,從便于加工、裝配、使用、維修等角度加以考慮。一、行腔及型芯的設計1. 凹模結構設計凹模是成型塑件外表面的零部件,按其結構可分為整體式和組合式兩大類。(1)整體式整體式型腔是由整塊鋼材直接加工而成,其特點是強度、剛
33、度都相對較高,因此,整體式型腔牢固且不易變形。此外,還有無鑲拼痕跡的優(yōu)點。適用于形狀簡單、機械加工沒有困難的模具。如圖6所示。圖6整體式型腔(2)組合式當塑件外形比較復雜時,采用整體式凹模加工,其加工過程困難,導致加工工藝性差,若采用組合式凹??梢愿纳萍庸すに囆裕瑴p少熱處理變形,節(jié)省優(yōu)質鋼材。組合式凹模類型多樣,包括整體鑲拼式和局部鑲拼式。如圖7所示。(a)整體鑲拼式在多型腔模具中,為了節(jié)約工時和優(yōu)質鋼材,便于加工,常引入整體鑲拼式型腔的設計。這種整體鑲拼式型腔,一般作成帶臺肩的鑲件,被鑲嵌或固定在模板上。(b)局部鑲拼式局部鑲拼式是為了解決型腔某部分加工和熱處理困難的問題;容易損壞的部分也經(jīng)
34、常設計成鑲件形式。(a) 整體嵌入式; (b)局部嵌入式圖7凹模類型根據(jù)外殼塑件的結構特征,同時考慮到加工的難易程度和模具的成本問題,選定凹模為嵌入式結構。2. 凸模的設計凸模是用于成型塑件內表面的零部件,有時也稱型芯和成型桿。與凹模相類似,凸模也可以分為整體式和組合式兩類。整體式凸模就是把凸模與模板作成整體,結構牢固,成型質量好,但鋼材消耗量大,適用于內表面形狀簡單的小型凸模。當塑件內表面形狀復雜而不便于機械加工,或形狀雖然不復雜,但為節(jié)省優(yōu)質鋼材,減少切削加工量時,可采用鑲拼式凸模,將凸模及固定板分別采用不同材料制造和熱處理,然后連接在一起,支架的型芯小鑲件9、25用臺階固定,型芯5用螺塞
35、鉚接,型腔和型芯均通過套板用臺階方式固定。二、工作尺寸計算 所謂工作尺寸是指成型零件上直接用以成型塑料制品部分的尺寸。任何塑料制品都要有一定的尺寸要求,在安裝和使用中有配合要求的塑料制品,其尺寸公差常要求較小。在設計模具時,必須根據(jù)塑料制品的尺寸和公差要求來確定相應的成型零件的尺寸公差。影響塑料制品尺寸公差的因素成型零件工作尺寸的制造公差它直接影響塑件的尺寸公差。通常凹、凸模的制造公差取塑件公差的1/31/6,表面粗糙度取Ra值為0.8m0.4m。成型零件使用過程中的磨損量及其他因素的影響生產(chǎn)過程中的磨損以及修復會使的凸模尺寸變小,凹模的尺寸變大塑件收縮率的影響由于塑料的熱脹冷縮的原因,成型冷
36、卻后的塑件尺寸小于模具型腔尺寸。因此,成型大型塑件時,收縮率對塑件的尺寸影響較大:而成型小型件時,制造公差與磨損量對塑件的尺寸影響較大。查表查得ABS的收縮率為0.5%。a.型腔尺寸計算其工作尺寸屬于包容尺寸,盡量取下限尺寸,尺寸公差取上偏差。徑向尺寸計算公式: L=深度尺寸計算公式: H=其中: L為塑件外形最大尺寸K為塑件的平均收縮率0.05為塑件的尺寸公差為模具制造公差,取塑件尺寸公差的1/3-1/6 H為塑件高度方向的最大尺寸b.型芯的工作尺寸計算 其工作尺寸屬于被包容尺寸,盡量取上限尺寸,尺寸公差取下偏差。徑向尺寸計算公式: =高度尺寸計算公式: =其中: 為塑件外形最大尺寸K為塑件
37、的平均收縮率0.055為塑件的尺寸公為模具制造公差,取塑件尺寸公差的1/3-1/6為塑件高度方向的最大尺寸型芯5的尺寸計算:a. 型腔尺寸計算 L =11.930.003 H =1.930.002b.型芯的工作尺寸計算 =4.13-0.023 = =0.09-0.003型芯9的尺寸計算a.型腔尺寸計算 L =21.950.037 H =1.930.002b.型芯的工作尺寸計算 =4.13-0.023 = =0.09-0.003型芯25的尺寸計算a、.型腔尺寸計算 L =21.950.037 H =1.930.002b、型芯的工作尺寸計算 =8.16-0.023 = =0.09-0.003三、型
38、腔側壁及底板厚度計算按強度計算側壁公式:式中系數(shù)取0.321查塑料注塑模結構與設計表4-14模腔壓力,取45 MP凹模行腔深度,為2mm材料許用應力,為180 MP(材料選為)代入公式進行計算得:mm,取=0.57mm。因為行腔壁上有抽芯機構,故取凹模尺寸為370650 (mmmm)底板計算公式:式中系數(shù)取0.3078查塑料注塑模結構與設計表4-15模腔壓力,取45 MP凹模行腔的內孔短邊尺寸,為2mm材料許用應力,為180 MP代入公式進行計算得: =0.56mm,取=0.56mm3.3.5合模導向機構的設計合模導向裝置是保證動模與定模或上模與下模和模時正確定位和導向裝置。合模導向裝置主要是
39、有導柱導向和錐面定位。導柱導向裝置的主要零件是導柱和導套。也可不用導套而在模板上鏜孔代替導套,該孔通稱導向孔。3.3.5.1模架的選取模架是注射模的骨架。標準模架一般由凹模板、凹模固定板、凸模板、凸模固定板、凸模墊板、墊腳、頂出固定板、頂出墊板、導柱、導套、復位桿等組成。(1)模具材料的選擇對一個具體的模具,為了保持其高精度及較長的使用壽命,就應該根據(jù)模具的結構和使用情況,合理的選用制模材料。塑料成型模的結構均比較復雜。零件由于工作時所處的地位不同,作用不同,環(huán)境不同,因此對材料的要求就完全不同。因此,根據(jù)要求模具用鋼材,應具備以下性能:良好的耐磨性良好的拋光性良好的耐蝕性和耐熱性。(2)模架
40、的尺寸由于模具采用的是直接澆口澆注,所以應該選擇A2型模架。其各個部分尺寸如圖8。圖8模架的確定3.3.5.2導向裝置的作用1.導向作用 2.定位作用 3.承載作用 4.承受一定側壓力3.3.5.3導向零件的設計原則1.導向零件應合理的均勻的分布在模具的周圍或靠近邊緣的部位,其中心距模具的邊緣應有足夠的距離,以保證模具的強度,防止壓入導柱和導套時發(fā)生變形。2.根據(jù)模具的大小,一副模具一般需要24個導柱。對于大型模具,為了簡化加工工藝,采用三個或四個直徑相同的導柱,導柱位置對稱。3.為了便于塑料制品脫模,導柱通常安裝于動?;蚨!?.為保證分型面很好的接觸,導柱和導套在分型面處應有承屑槽,一般都
41、是削去一個面,或在導套的孔口倒角。5.當上模板與下模板采用合模并加工時,導柱裝配處直徑應與導套外徑相等。6.各導柱和導套的軸線應保持平行,否則將影響合模的準確性。甚至損壞導向零件。3.3.5.4導柱的設計導柱設計在動模一側,因為作為成型零件的主型芯多裝在動模一側,導柱與主型芯安裝在同一側,在合模時可起到保護作用。1.有單節(jié)與臺階式之分。2.導柱的長度必須高出凸模端面68mm。3.導柱頭部應有圓錐或球形的引導部分。4.固定方式有鉚接固定和螺釘固定。5.其表面應熱處理,以保證耐磨。導套有套筒式、臺階式、凸臺式,為了導柱順利進入導套孔,在導套前端應倒有圓角r。根據(jù)以上要求和設計原則,選取導柱和導套如
42、圖9所示。圖9導套和導柱的尺寸3.3.5.5復位桿復位桿又稱反推桿或回程桿,它的作用是使已經(jīng)完成推出制品位置的推桿回到注射成型時需要的位置。復位桿在機構上與推桿,兩者不同之處在于它與模具配合間隙大于推桿與模具的配合間隙,其直徑也較粗同時復位桿頂面不應高出分型面。根據(jù)動模固定板的結構,采用四個復位桿。復位桿如圖10圖10復位桿3.3.6脫模、頂出機構的設計一、脫模力計算將制品從包緊的型芯上脫出時所需克服的阻力稱為脫模力。計算脫模力時應考慮以下方面。a.由收縮包緊力造成的制品與型芯的摩擦阻力,該值應由實驗確定。b.由大氣壓造成的阻力。c.由塑件的粘附力造成的脫模阻力。d.推出機構運動摩擦阻力。上述
43、各項脫模阻力中,a與b兩項起決定作用,c和d兩項可用修正系數(shù)的形式包括在脫模力計算公式中。此外,脫模力的大小還與制品的厚薄及幾何形狀有關,在注塑模設計時,可用公式對一般的制品作脫模力的粗略計算。注塑成型過程中,型腔內熔融塑料因固化收縮包在型芯上,為使塑件能自動脫落,在模具開啟后就需在塑件上施加一頂出力。頂出力的作用點應盡量靠近型芯并且頂出力應施于塑件剛性和強度最大的部位。作用面積也盡可能大些,頂出力是確定頂出機構結構和尺寸的依據(jù),它與塑料、種類、塑件包容在型芯上的面積以及塑件的熱收縮值等有關。計算公式為: K查塑料成形加工與模具表83得1.0035矩形制件的平均壁厚2 mmE塑料的彈性模量20
44、00 MPS塑料平均成型收縮率0.005L制件對型芯的包容長度10.5mm模具型芯的脫模斜度1制件與型芯的摩擦因數(shù)0.21塑料的泊松比0.4F=4F1=4398=1592N頂出力滿足要求。二、頂出力的計算注塑成型過程中,型腔內熔融塑料因固化收縮包在型芯上,為使塑件能自動脫落,在模具開啟后就需要在塑件上施加一頂出力。頂出力的作用點應盡量靠近型芯,并且頂出力應施于塑件剛性和強度的最大的部位,如凸緣或加強筋等處作用面積也盡可能大一些。頂出力是確定頂出機構結構和尺寸的依據(jù),它與塑料種類,塑件包容在型芯上的面積以及塑件的熱收縮率等有關,計算公式: F1頂出力 NE塑料彈性模量2000MPA塑料包容在型芯
45、的徑向面積1678.25mmf塑料與鋼之間的摩擦因素0.21d型芯直徑8mmt塑件平均壁厚2 mm塑件材料的泊松比0.4塑件在徑向的熱收縮 塑料熱膨脹系數(shù)710 注入型腔的熔融塑料溫度180 塑件出模溫度60代入得:0.4638NF=4F1=4638=2553N推桿直徑效核柔度定義: 因為=57.1229 所以屬于大柔度推桿計算公式: 脫模阻力1592NE推桿材料彈性模量;n推桿數(shù)量;12個 K安全系數(shù);1.41.8;取1.5 d推桿直徑8mm 故推桿滿足要求。3.3.7側向抽芯機構的設計(1)結構及工作原理塑件邊頂出邊抽芯,斜導柱個斜滑塊固定在動模上,是斜導柱和斜滑塊同步抽心機構。(2)抽芯
46、距其計算公式為:設計抽芯距,0.5mmS:抽芯距,mmS=0.5+3=3.5mm(3)斜導柱傾斜角斜導柱的傾斜角通常取1520,一般不大于25。考慮到抽芯距不大,則取20。(4)斜導柱的直徑考慮到抽拔力和傾斜角不大,這里工作部分直徑初步定12mm.(5)最小開模行程3.3.8排氣系統(tǒng)的設計塑料注射模具的型腔,在熔融塑料填充過程中,除了模具型腔內有空氣外,還有因塑料受熱而產(chǎn)生的氣體,尤其在高速注射成型產(chǎn)生的氣體更多,因此,在模具設計時必需設置排氣槽。選擇排氣槽的位置是很重要的,一般在塑料填充的同時,必須把氣體排出模外。否則,被壓縮的空氣會高溫燃燒,使熔融的塑料焦化或使熔接線處強度降低以及不成型,
47、影響塑料制品質量,尤其對于大型塑料注射模具,開設合理的排氣槽更顯得重要。1、排氣不良的危害性(1) 在塑件上形成氣泡,銀紋,云霧,接縫,使表面輪廓不清,甚至充模不滿。(2)嚴重時,在塑件表面產(chǎn)生焦痕。(3)降低充模速度,影響成型周期。(4)形成繼續(xù)注射,降低生產(chǎn)效率。2、開設排氣槽應該注意以下幾點(1)根據(jù)進料口位置,排氣槽應開設在型腔最后充滿的地方。(2)盡量把排氣槽開設在分型面上,如直接澆口排槽的位置。(3)對于流速較大的塑料制品,可利用模具的分型面及頂桿零件配合的間隙進行排氣。(4)排氣槽不要開設在工人操作的地方,以防止塑料在注射時溢出模外,發(fā)生燒傷事故。(5)對于大型塑料注射模具,為了
48、防止溢料,排氣槽應設在模具分型面上,并成為曲線形。(6)排氣槽的尺寸,應根據(jù)塑料的流動性來選擇。3、排氣機構的設置,一般有如下的方法。(1)利用分型面排氣。(2)利用推桿排氣。(3)利用鑲件排氣。(4)利用燒結合金排氣。(5)排氣槽排氣。(6)排氣井排氣。(7)強制性排氣。在本設計中采用的方式是:利用分型面排氣。3.3.9溫度調節(jié)系統(tǒng)的設計一、溫度調節(jié)的必要性溫度的調節(jié)對塑件的質量影響主要表現(xiàn)在以下幾個方面:1.變形模具溫度穩(wěn)定,冷卻速度均衡,可以減少塑件的變型。對于壁厚不均的和形狀復雜的塑件,經(jīng)常會出現(xiàn)因收縮不均勻而產(chǎn)生翹曲變形的情況。因此,必須采用合適的冷卻系統(tǒng),使模具凹模與型芯的各個溫度
49、基本上保持一致,以便型腔里的塑料熔體能同時凝固。2.尺寸精度利用溫度調節(jié)系統(tǒng)能保持模具溫度的恒定,能減少塑件成型收縮率的波動,提高塑件尺寸精度的穩(wěn)定性。在可能的情況下采用較低的模溫能有助于減少塑件的成型收縮率。例如,對于結晶材料,因為模溫較低,制件的結晶度可以降低收縮率。但是,結晶度低不利于制件尺寸的穩(wěn)定性,從尺寸的穩(wěn)定性出發(fā),又需要提高模具溫度,使塑件結晶均勻。3.力學性能對于結晶性材料,結晶度越高,塑件的應力開列傾向越大,故從減小應力開裂的角度出發(fā),降低模溫是有利的。但對于聚碳酸脂一類高粘度無定形塑料,其應力開裂傾向與塑件中的內應力的大小有關,提高模溫有利于減小制件3中的內應力,也就減小了
50、其應力開裂傾向。4.表面質量提高模具溫度能改善制件表面質量,過低的模溫會使制件輪廓不清晰并產(chǎn)生明顯的熔接痕,導致制件表面粗糙度提高。以上幾個方面對模具溫度的要求又相互矛盾的地方,在選擇模具溫度時,應根據(jù)使用情況著重滿足制件的主要性能要求。二、冷卻系統(tǒng)的設計原則為了提高冷卻系統(tǒng)的效率和使型腔表面溫度分布均勻,在冷卻系統(tǒng)的設計中應遵守如下原則:1.在設計時冷卻系統(tǒng)應先于推出機構,也就是說,不要在推出機構設計完成后才考慮冷卻回路的布置,而應盡早將冷卻方式和冷卻回路的位置確 定下來,以便能得到較好的冷卻效果。將該點作為首要設計原則提出來 的依據(jù)是,在傳統(tǒng)設計中,往往推出機構的設計先于冷卻系統(tǒng),冷卻系
51、統(tǒng)的重要性未能引起足夠的認識。2.注意凹模和型芯的熱平衡。有些塑件的形狀能使塑料散發(fā)的熱量等量的被凹模和型芯所吸收。但是極大多數(shù)塑件的模具都有一定的高度型芯以及包圍型芯的凹模,對于這類模具,凹模和型芯所吸收的熱量是不同的。這是因為塑件在固化時因收縮包緊在型芯上,塑件與凹模之間會形成空隙,這時絕大部分的熱量將依靠型芯的冷卻回路傳遞,加上型芯布置冷卻回路的空間小,還有推動的干擾,使型芯的傳熱變得更加困難,因此,在冷卻的設計中,要把主要注意力放在型芯的冷卻上。3.對于簡單的模具,可先設置冷卻水出入口的溫差,然后計算冷卻水的流量,冷卻管道的直徑,保證湍流的流速以及維持這一流速所需要的壓力降便以足夠。4
52、.生產(chǎn)批量大的普通模具和精密模具在冷卻方式上又差異,對于大批量生產(chǎn)的普通塑件可采用快冷以獲得較短的循環(huán)注射周期。所謂快冷就是使冷卻管道靠近型腔布置,采用較低的模具溫度。精密塑件需要有精密的尺寸公差和良好的力學性能,因此需采用緩冷,即模具溫度較高,冷卻管道的尺寸和位置也適應緩冷的要求。5.模具中冷卻水溫度升高會使熱傳遞減小,精密模具中出入口水溫相差應在5度。從壓力的損失觀點出發(fā),冷卻回路的長度應在1.2-1.5m以下,回路的彎頭數(shù)目不希望超過5個。6.由于凹模和型芯的冷卻情況不同,一般應采用兩條冷卻俄回路分別冷卻凹模和型芯。7.當模具僅設一個入水接口時,應將冷卻管道進行串聯(lián)連接,若采用并聯(lián)連接,
53、由于各個回路的留動阻力不同,很難形成相同的冷卻條件。當需要并聯(lián)連接時,則需要在每個回路中設置水量調節(jié)泵及流量計。8.采用多而細的冷卻水道,比采用獨大的冷卻管道好。因為多而細的冷卻管道擴大了模溫的調節(jié)的范圍,但管道不可以太細,以免堵塞,一般取管道的直徑為8-25mm。在收縮率大的塑料制件的模具中,應延其收縮方向設置為冷卻回路。9.通模具的冷卻俄水應采用常溫下的水,通常調節(jié)水流量來調節(jié)模具的溫度。對于小型塑件,由于其注塑時間和保壓時間都較短,成型周期主要有冷卻時間決定,為了提高成型效率,可以采用經(jīng)過冷卻的水進行冷卻,目前經(jīng)冷卻機冷卻的5-10度的水。用冷水進行冷卻時,大氣中的水分會凝聚在型腔的表面
54、以引起塑件的缺陷。對于流動距離長,成型面積大的塑件,為了防止填充不足或者變型,有時還得通熱水。總之,模溫最好同過冷卻系統(tǒng)或者專門的裝置能任意調節(jié)。 10.的確定冷卻管道的中心距以及冷卻管道與型腔壁的距離。冷卻管道與型腔壁的距離太大會使冷卻效率下降,而距離太小有會造成冷卻不均勻。根據(jù)經(jīng)驗,一般冷卻管道中心線與型腔壁的距離應為冷卻管道直徑的1-2倍。冷卻管道的中心距應為管道直徑的3-5倍。11.盡可能使所有冷卻管道孔分別到各處型腔表面的距離相等。當制件壁厚均勻時,應盡可能使所有的冷卻管道孔到各處的型腔表面的距離相等。12.應加強澆口處的冷卻。熔體充模時,澆口附近的溫度最高。一般來說,據(jù)澆口越遠溫度
55、越低。因此,在澆口附近應加強冷卻,一般可將冷卻回路的入口設在澆口處,這樣可使冷卻水道首先通過澆口附近。13.應盡量避免將冷卻水道開設在塑件熔合紋的部位。當采用多澆口的進料或者型腔形狀較復雜時,多股熔體在匯合處將產(chǎn)生熔合紋。在熔合紋的溫度一般較其它的溫度低,為了不致使溫度進一步下降,保證熔合質量,應盡可能不在熔合紋部位開設冷卻水道。14.水管的密封問題,以免漏水。一般,冷卻管道應避免穿過鑲塊,否則在接縫處漏水,若必須通過鑲塊時,應加設套管密封。15.進口,出口水管的接頭的位置應該盡可能設在模具的同一側。為了不影響操作,通常應將進口,出口水管接在設在注塑機背面的模具的一側。三、冷卻管道傳熱面積及管
56、道數(shù)目的計算a.冷卻介質的體積流量計算冷卻介質的體積流量,單位時間內注入模具中的塑料質量,單位重量的塑料在凝固時所放出的熱量,冷卻介質的密度,冷卻介質的比熱容,)冷卻介質的,20冷卻介質的,27b.求冷卻管道直徑d查塑料成型加工與模具表101,為使冷卻水處于湍流狀態(tài)取 d=10mm.c.求冷水在管道內的流速Vd.求冷卻管道孔壁與冷卻介質的傳熱膜系數(shù)h查表取7.22(水溫30)水的密度,0.99610d推桿直徑,8mme.求冷卻管道總傳熱面積Af.求模具上應開設的冷卻管道3.3.10有關參數(shù)的校核1.動模固定板效核 因為動模固定板需要效核部分與動模的厚度相同,并且他們所受的型腔壓力一樣,作用范圍
57、也一樣大,所以不用計算可知強度滿足要求。2. 推桿固定板效核 推桿固定板厚度為16mm,其所受壓力為板所受的力除以其受力面積為16/0.1256=127MP至此,注塑機已校核完畢,各項參數(shù)均符合要求,且比較合理,基本上滿足了設計的需要。第四章 總結通過這次畢業(yè)設計的實踐,我了解了支架注塑模的設計的步驟和模具在我國的最新發(fā)展趨勢。對設計模具有了一個系統(tǒng)的設計思路,注塑模具的設計包括模具結構設計、注塑機的選用、澆注系統(tǒng)的設計等方面。支架的材料是ABS,吸收性能強,塑料在成型前必須充分預熱干燥,選擇的注塑機是XS-ZY-60,選擇側澆口,2個型腔選用鑲拼式,模架選用寬度和長度為200mm250mm的標準模架,采用斜導柱和斜滑塊同步抽芯,塑件邊頂出邊抽芯。采用一模兩腔,冷卻管道選用1個。當我終于完成了所有打字、繪圖、排版、校對的任務后整個人都很累,但同時看著電腦熒屏上的畢業(yè)設計稿件我的心里是甜的,我覺得這一切都值了。這次畢業(yè)論文的制作過程是我的一次再學習,再提高的過程。在論文中我充分地運用了大學期間所學到的知識。 我不會忘記這難忘的幾周時間。畢業(yè)論文的制作給了我難忘的回憶。我從資料的收集中,掌握了很多關于注塑模具的知識,讓我對我所學過的知識有所鞏固和提高。在今后的日子里,我仍然要不斷地充實自己,爭取在所學領域有所作為。
- 溫馨提示:
1: 本站所有資源如無特殊說明,都需要本地電腦安裝OFFICE2007和PDF閱讀器。圖紙軟件為CAD,CAXA,PROE,UG,SolidWorks等.壓縮文件請下載最新的WinRAR軟件解壓。
2: 本站的文檔不包含任何第三方提供的附件圖紙等,如果需要附件,請聯(lián)系上傳者。文件的所有權益歸上傳用戶所有。
3.本站RAR壓縮包中若帶圖紙,網(wǎng)頁內容里面會有圖紙預覽,若沒有圖紙預覽就沒有圖紙。
4. 未經(jīng)權益所有人同意不得將文件中的內容挪作商業(yè)或盈利用途。
5. 裝配圖網(wǎng)僅提供信息存儲空間,僅對用戶上傳內容的表現(xiàn)方式做保護處理,對用戶上傳分享的文檔內容本身不做任何修改或編輯,并不能對任何下載內容負責。
6. 下載文件中如有侵權或不適當內容,請與我們聯(lián)系,我們立即糾正。
7. 本站不保證下載資源的準確性、安全性和完整性, 同時也不承擔用戶因使用這些下載資源對自己和他人造成任何形式的傷害或損失。