畢業(yè)設(shè)計論文 外文文獻翻譯 電子商務(wù)專業(yè) 引入第三方物流企業(yè)的以代理人為基礎(chǔ)的電子商務(wù)系統(tǒng)模型 中英文對照
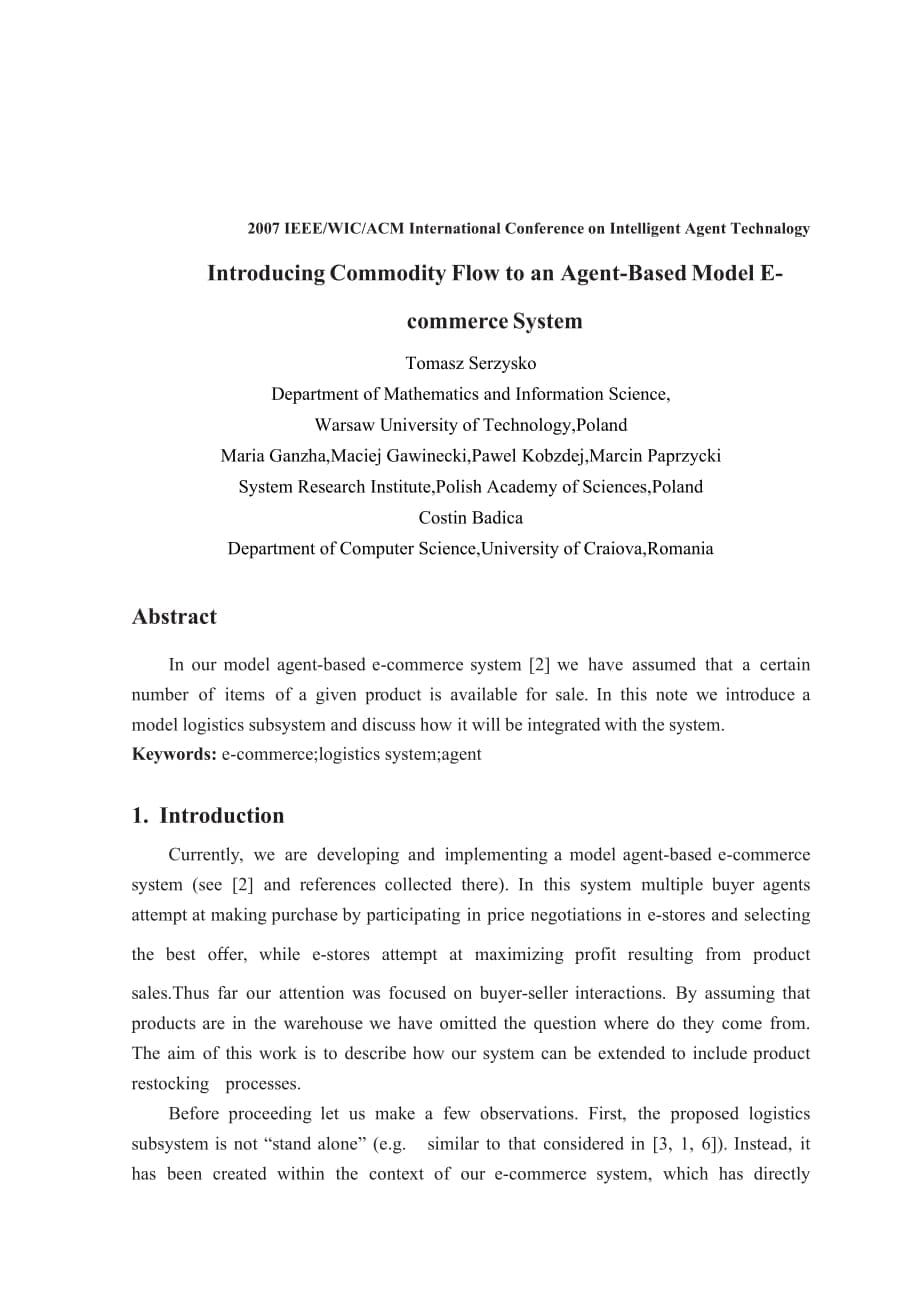


《畢業(yè)設(shè)計論文 外文文獻翻譯 電子商務(wù)專業(yè) 引入第三方物流企業(yè)的以代理人為基礎(chǔ)的電子商務(wù)系統(tǒng)模型 中英文對照》由會員分享,可在線閱讀,更多相關(guān)《畢業(yè)設(shè)計論文 外文文獻翻譯 電子商務(wù)專業(yè) 引入第三方物流企業(yè)的以代理人為基礎(chǔ)的電子商務(wù)系統(tǒng)模型 中英文對照(17頁珍藏版)》請在裝配圖網(wǎng)上搜索。
1、濟南大學(xué)畢業(yè)設(shè)計外文資料翻譯- 16 -2007 IEEE/WIC/ACM International Conference on Intelligent Agent TechnalogyIntroducing Commodity Flow to an Agent-Based Model E-commerce SystemTomasz SerzyskoDepartment of Mathematics and Information Science,Warsaw University of Technology,PolandMaria Ganzha,Maciej Gawinecki,Pawel
2、 Kobzdej,Marcin PaprzyckiSystem Research Institute,Polish Academy of Sciences,PolandCostin BadicaDepartment of Computer Science,University of Craiova,RomaniaAbstractIn our model agent-based e-commerce system 2 we have assumed that a certain number of items of a given product is available for sale. I
3、n this note we introduce a model logistics subsystem and discuss how it will be integrated with the system.Keywords: e-commerce;logistics system;agent1. IntroductionCurrently, we are developing and implementing a model agent-based e-commerce system (see 2 and references collected there). In this sys
4、tem multiple buyer agents attempt at making purchase by participating in price negotiations in e-stores and selecting the best oer, while e-stores attempt at maximizing profit resulting from product sales.Thus far our attention was focused on buyer-seller interactions. By assuming that products are
5、in the warehouse we have omitted the question where do they come from. The aim of this work is to describe how our system can be extended to include product restocking processes.Before proceeding let us make a few observations. First, the proposed logistics subsystem is not “stand alone” (e.g. simil
6、ar to that considered in 3, 1, 6). Instead, it has been created within the context of our e-commerce system, which has directly influenced its design. Second, while somewhat similar, processes involved in e-store restocking a warehouse differ from client making a purchase in an e-store (e.g. in prod
7、uct demand prediction, interactions with wholesalers, methods of price negotiations that involve more “conditions,” offer selection criteria, etc.) Therefore we have created a separate logistics subsystem (instead of reusing already modeled functions; e.g. price negotiations). Third, this note is de
8、voted to the agent structure and agent interactions and, due to the space limitations, we omit important topics like:forecasts derivation, oer evaluation etc.However, these functions can be encapsulated into modules that can become a part of an appropriate agent. Therefore readers should envision th
9、at, for instance, when we write that “received oers are evaluated,”then their favorite method of oer evaluation has been utilized.To proceed, first, we briefly describe our e-commerce system.We follow with assumptions that underline the logistics subsystem and description of new agents that were int
10、roduced. Finally, we present the sequence diagram of restocking and use it to discuss in detail how this process will take place in our system.2. System DescriptionOur system is a distributed marketplace in which software agents perform e-commerce functions (see 2 for details, the Use Case diagram i
11、n particular). User-Client is represented by the Client Agent (CA). The CA is autonomous and when a purchase order is communicated by the User-Client, it works until either it is completed, or purchase is abandoned. The CA communicates with the Client Information Center (CIC), which facilitates info
12、rmation which e-stores sell which products (yellow-page matchmaking).For each store that sells the requested product, the CA delegates a Buyer Agent (BA) to participate in price negotiations and if successful, possibly attempt at making a pur- chase (successful price negotiations result in a product
13、 reservation for a specific time; after which products that have not been purchased are available for sale again).Since multiple BAs representing the same CA can win price negotiations the CA makes the decision if either of available oers is good enough to make a purchase. Buyer Agents can participa
14、te in negotiations only if the Gatekeeper Agent (GA) admits them (if they are trusted; e.g. BAs that win price negotiations but do not make a purchase may be barred from subsequent negotiations). The GA represents a given e-store and is created by the Shop Agent (SA). The SA is the central manager a
15、nd facilitating the selling process it utilizes the GA, and a set of Seller Agents (SeA) that negotiate price with incoming BAs, as well as a Warehouse Agent (WA) that is responsible for inventory and reservation management. Thus far, the WA was responsible for managing product reservations and the
16、inventory. Specifically, (1) before a new price negotiation the WA “reserved” a given productso that if negotiation ended successfully there was an item that could be sold; (2) when a reservation ended in purchase, it adjusted product counters; and (3) when a reservation expired it also adjusted pro
17、ducts counters. However, the WA was always envisioned as the “gateway” between the store and suppliers, which is one of the foci of this note.3. Assumptions behind the logistics systemLet us now specify assumptions that underline design of the logistics subsystem: 1.Nowadays, except of largest store
18、-chains (e.g. TESCO, WalMart), companies outsource transportation activities (considered non-core business activities) to specialists (e.g. UPS, Mayflower). However, we assume here that suppliers are still responsible for facilitating transportation. Therefore, we omit transportation related process
19、es and focus only in interactions between e-stores and suppliers2. As a result of (1), transportation costs are assumed to be paid by the supplier and included directly in product price (e.g. discount on delivery costs, will manifest itself in the total price).3. While in the original system auction
20、-based price negotiations were used, here we opted for the simplicity of the FIPA Contract Net Protocol 4. Therefore, in the logistics subsystem, a single round of negotiations consisting of a call for proposals and evaluation of responses, is used.4. New functions and agentsIn order to perform logi
21、stics-related tasks, several new roles were introduced; some of them have been delegated to agents existing in the system, while others warranted adding new agents. Specifically: demand estimationto draw information from sales data and/or external premises to predict future sales of products, wareho
22、use monitoringto observe supply levels and react in case of a risk of dropping below values considered sucient to satisfy estimated demand, order managementto coordinate issuing orders for goods, to assist in evaluating received oers, ordering goodsto contact suppliers for their of- fers and to sele
23、ct the best oer, selling goodsin the system suppliers were also modeled; while goods are acquired without extensive price negotiations, “someone” has to deliver proposals to ordering components, logistics yellow pagesthe role of the “l(fā)ogistics CIC” is very similar to the original CIC (2); it has to
24、provide lists of potential suppliers of products; obviously, it is possible for a shop to become a sup- plier for another shop and to suggest that the two CICs could be joined, but we decided to clearly separate the client-side from the shop and from the supply-side. Another reason for this separati
25、on was that while some shops may not be interested in becoming wholesaler, we would have to make changes to the original CIC data structure (e.g. wholesaleryes/no). Finally, since the logistics subsystem does not involve auctions, the separation is even more warranted.Let us now see how these tasks/
26、roles could be placed in our system. The demand estimation role was attributed to the existing Shop Decision Agent (SDA), responsible for the “knowledge management” functions (e.g. trust management, sales trend data mining, etc.) in the shop.The warehouse monitoring role is already a part of the exi
27、sting WA. The dierence is that now WA becomes a proactive manager of supplies; acting on predictions supplied by the SDA.Fulfillment of the order management role required introduction of the Logistics Agent (LA), which became the “central manager” of the logistics subsystem. It is responsible for co
28、ntacting the logistics CIC for the list of potential suppliers and managing a pool of agents responsible for ordering goods from “wholesalers.” Finally, it collects and manages data related to supplier reliability. This data, in turn, will be one of factors in selecting the supplier.The ordering goo
29、ds process is facilitated by the Ordering Agent (OA), which is also a new agent. Its task is to issue a call for proposals, collect responses and select the best oer taking into account factors such as: price, delivery time, reliability etc. Let us recall that due to the modularity of agent design (
30、2), our system is flexible enough so that any method of selecting an oer can be applied (it can be encapsulated in a module and plugged into the OA).The selling goods role is realized by a very simple Wholesale Agent (WhA). Its role is to respond to CFPs incoming from OAs.Currently we assume that Wh
31、As receive instructions in what way to generate a stream of responses to the CFPs.Finally, logistics yellow pages are facilitated by the logistics CIC Agent. Its role is to store a complete list of suppliers and products that they sell. Obviously, the logistics CIC uses the original product ontology
32、 (2), extended by the logistics ontology. When the system is initialized, each WhA registers with the logistics CIC and provides it with a list of products for sale.What was described thus far is summarized in an UML use case diagram presented in Figure 1.Figure 1. Use Case of the logistics subsyste
33、m5. Typical Product Restocking ProcessLet us now describe the processes involved in restocking the warehouse. Here, we skip the description of system initialization, and start with the Shop Decision Agent sending a forecast to the Warehouse Agent. The sequence of actions resulting form such a foreca
34、st is depicted, as a UML sequence diagram in Figure 2.The SDA communicates the forecast to the WA by sending a FIPA Inform message containing the PredictionDescription (which contains all necessary data such as: product ID, amount of predicted sales, standard deviation of sales, expected purchase pr
35、ice, period for which this forecast is valid, etc.). We assume that the SDA forecasts are of the type: until a new fore- cast, weekly sales are expected to be 45 items of a given product. Forecasts can be issued at specific times (e.g. once a week or once a month) and their frequency de- pends on th
36、e information found in data analyzed by the SDA to derive forecast(s).The WA starts by examining current stock of a given product, and if current supplies are sucient, it sets up to check their levels at the end of the time unit specified in the forecast (i.e. forecasts specified on weekly basis are
37、 checked once a week). If stocks are insucient, the WA utilizes the FIPA Request Protocol (FIPA specification SC00026) and FIPA SL language 4 (used in all agent interactions), to com- municate with the Logistics Agent. The initial message from the WA is the FIPA Request message sent to the LA and it
38、 contains OrderRequest action with the Or- derRequestDescription. The OrderRequestDescription contains the necessary information specifying the order to be made: product ID, preferred delivery time, amount and maximum price. Delivery time and amount are computed based on the current product level, p
39、redicted delivery time and an overall inventory strategy.Upon receiving the request, the LA dispatches a query to the logistics CIC to obtain a list of suppliers of a given product. Ensuing conversation conforms to the FIPA Query Protocol, starting with the FIPA Query-Ref message containing the CICQ
40、uery action with the Product ID. The logistics CIC responds with the FIPA Inform-Ref message containing the CICResponse with a list (possibly empty) of suppliers. Empty list results in a FIPA Failure message (with OrderRequestResult set to failure) send by the LA to the WA. Similar response is sent
41、when the logistics CIC cannot be contacted.When the non-empty list was received, the LA removes these suppliers that have their reliability value below a certain threshold. Then the LAAgentDescriptions list is formed by supplementing each CICAgentDescription received from the logistics CIC with the
42、reliability information. If a given WhAs is not known a default trust value is used.After preparing the list, the LA utilizes the FIPA Request Protocol to find a free OA. Busy agents will re- spond with FIPA Refuse messages. If all agents respond in such a way, this process may need to be repeated u
43、n- til a free OA is found and responds with the FIPA Agree message. The LA then sends the ordering request to the selected OA and awaits for the result of the ordering pro- cess. LAs message contains the IssueOrder action with the OrderDescription and the LAAgentDescriptions.After obtaining the requ
44、est from the LA, the OA engages in the FIPA ContractNet Protocol interactions with WhAs from the list. It sends the FIPA CallForProposal message, containing CFPRequest with OrderDescription to the WhAs. WhAs evaluate the CFP and submit their oers by sending FIPA Propose messages containing the CFP R
45、esponse action with OerDescription or, if terms contained in the CFP are unacceptable/not interesting, respond using the FIPA Refuse message.Responses must arrive within a timeframe speci- fied by the OA, after which the OA proceeds to evalu- ate them. First, it filters unacceptable oers. Note that
46、it is possible that some WhAs may respond knowingly with proposals that violate some of the conditions and in special circumstances when no better oers were found the OA may need to accept such oers. In the next step, oers are ranked and the winner is determined. Winner is sent a FIPA AcceptProposal
47、 message containing the ConfirmationRequest action with its offer quoted. The winning WhA must in turn reply with the FIPA Inform message containing Confirmation Response action with the OrderConfirmation which has unique orderID generated by the supplier. This successfully completes the ordering pr
48、ocess. The winner can also withdraw the oer by sending a FIPA Failure message. In this case, runner-ups are contacted in an iterative manner. In case when there are no more oers left or there were no oers to begin with, the OA sends a FIPA Failure message to the LA, which, in turn, forwards it to th
49、e WA. When the winner confirms the order, the OA sends to the LA a FIPA Inform message containing the InformResult action with the WhA-received Order Confirmation, thus completing the protocol. At this time the LA sends information to the WA, inside a message of the FIPA Agree type. This performativ
50、e is used in compliance with the protocol to indicate that the LA is performing the desired task (ordering), but its eorts do not guarantee success (ordering success order success), and thus sending the final response (FIPA Inform) is inappropriate at this stage. Meanwhile the OA returns to the pool
51、 of available Ordering Agents.Now the purchase enters the delivery monitoring stage. Here, the LA waits for the delivery from the WhA to be registered with the WA. When a delivery arrives the WA sends (to the LA) a plain FIPA Inform message containing the WADelivery action with the DeliveryDescripti
52、on, which has suppliers AgentID and the already mentioned orderId. The LA does not need to respond to this message, but it checks the messages to see if it is currently awaiting a delivery with the given orderId coming from a supplier AgentID. If it finds a match, the ordering process is completed.
53、As a result, the reliability value of supplied AgentID is increased. If a delivery notification does not come within time agreed in the OrderConfirm, actions must be undertaken (recall, that receiving supplies is vital to the e-Shop as its warehouse is likely to run out of stock Those actions are: (
54、1) retry the ordering (sending reminder to the WhA / choosing new WhA), if there is still time, and (2) marking that a retry has been made.If there is still time before the deadline (established by the WA), then order can be retried. If it is the first time an attempt to retry the order is made, a r
55、eminder is sent to the WhA. To this end, LA contacts a free OA with a FIPA Request Protocol message with a Reminder action containing AgentID of the WhA and the orderId. The OA accepts the job (the FIPA Agree) and contacts the WhA (also using FIPA Request Protocol), sending it the exact same action.
56、The WhA is expected to reply within a timeframe using either a FIPA Failure (oer is withdrawn) or a FIPA Inform providing new Order Confirmation with a new delivery time, which is forwarded to the LA unchanged. In the case of an agreement, the LA returns to awaiting delivery, in the case of failure,
57、 the LA removes this WhA from the LA Agent Description list and locates an OA to perform entirely new search for a supplier. New search is also ordered if a reminder to the supplier whose delivery we were waiting resulted in a failure. The monitoring stage ends when: (1) delivery is received, or (2)
58、 reminder to the supplier was made, but it was refused, while deadline has already passed. Note that we assume that the actual order failure occurs only when the delivery deadline has passed and the reminder failed.This is because it is possible that there is an order delay and goods may arrive late
59、. This information can be obtained from the WhA, and thus the need for the reminder.Figure 2. Restocking process: sequence diagramWhen the monitoring stage ends, the WA is notified about the result by the FIPA Inform or the FIPA Failure message to complete the FIPA Request protocol. The message will
60、 contain the OrderRequest action with the OrderRequestResult set appropriately. Furthermore, at this stage the reliability bonuses and/or penalties are calculated and applied. Finally, in the case of a successful order, the WA sends to the SDA a FIPA In- form message containing status information ab
61、out the re-stocking of the warehouse.6. Concluding remarksIn this note we have discussed the way in which the logistics subsystem is being introduced into our model agent-based e-commerce system. We have presented used UMLs use case and sequence diagrams to formally depict and discuss the most impor
62、tant features of our approach. Due to the lack of space, we have focused our attention on agents and their interactions. The proposed system has been implemented and is in the final testing phase.References1AgentisSoftware,2007.2 C. Bdic, A. Bdit, M. Ganzha, M. Paprzycki, Developing a Model Agent-ba
63、sed E-commerce System. In: Jie Lu et. al. (eds.) E-Service IntelligenceMethodologies, Technologies and Applications, Springer, Berlin, 2007,5555783 C. A. Butler and J. T. Eanes. Software agent technology for large scale, real-time logistics decision support. US Army Research Report ADA392670, 2001.
64、23 pages.4 FIPA: Foundation for Physical Agents.http:/www.fipa.org5 JADE: Java Agent Development Framework.http:/jade.cselt.it 6W.Ying and S.Dayong. Multi-agent framework for third party logistics in e-commercestar. Expert Systems with Applications, 29(2):431436, August 2005.International Conference
65、 on Intelligent Agent Technalogy,2007, 78(7): 294-298引入第三方物流企業(yè)的以代理人為基礎(chǔ)的電子商務(wù)系統(tǒng)模型 Tomasz Serzysko數(shù)學(xué)信息科學(xué)部門,波蘭華沙工業(yè)大學(xué)Maria Ganzha,Maciej Gawinecki,Pawel Kobzdej,Marcin Paprzycki波蘭研究院Costin Badica羅馬尼亞大學(xué)計算機科學(xué)部門摘要在我們的模型以代理人為基礎(chǔ)的電子商務(wù)系統(tǒng)2的基礎(chǔ)上,我們假定一定數(shù)量的物品的某一特定的產(chǎn)品是適合出售的。摘要本文我們介紹了模型的物流系統(tǒng)并且討論了如何將它與系統(tǒng)結(jié)合。關(guān)鍵詞:電子商務(wù);物流系統(tǒng);代理1. 簡要目前,我們正在開發(fā)和實施模式以代理人為基礎(chǔ)的電子商務(wù)系統(tǒng)(參見2的基礎(chǔ)上,參考文獻收藏)。在該系統(tǒng)中當(dāng)網(wǎng)上商店試圖獲得產(chǎn)品銷售利潤最大化的時候,多買方代理試圖通過在電子商店參與價格談判做出購買
- 溫馨提示:
1: 本站所有資源如無特殊說明,都需要本地電腦安裝OFFICE2007和PDF閱讀器。圖紙軟件為CAD,CAXA,PROE,UG,SolidWorks等.壓縮文件請下載最新的WinRAR軟件解壓。
2: 本站的文檔不包含任何第三方提供的附件圖紙等,如果需要附件,請聯(lián)系上傳者。文件的所有權(quán)益歸上傳用戶所有。
3.本站RAR壓縮包中若帶圖紙,網(wǎng)頁內(nèi)容里面會有圖紙預(yù)覽,若沒有圖紙預(yù)覽就沒有圖紙。
4. 未經(jīng)權(quán)益所有人同意不得將文件中的內(nèi)容挪作商業(yè)或盈利用途。
5. 裝配圖網(wǎng)僅提供信息存儲空間,僅對用戶上傳內(nèi)容的表現(xiàn)方式做保護處理,對用戶上傳分享的文檔內(nèi)容本身不做任何修改或編輯,并不能對任何下載內(nèi)容負責(zé)。
6. 下載文件中如有侵權(quán)或不適當(dāng)內(nèi)容,請與我們聯(lián)系,我們立即糾正。
7. 本站不保證下載資源的準(zhǔn)確性、安全性和完整性, 同時也不承擔(dān)用戶因使用這些下載資源對自己和他人造成任何形式的傷害或損失。