紡機(jī)凸輪輪廓曲線等線速CNC磨削技術(shù)研究論文
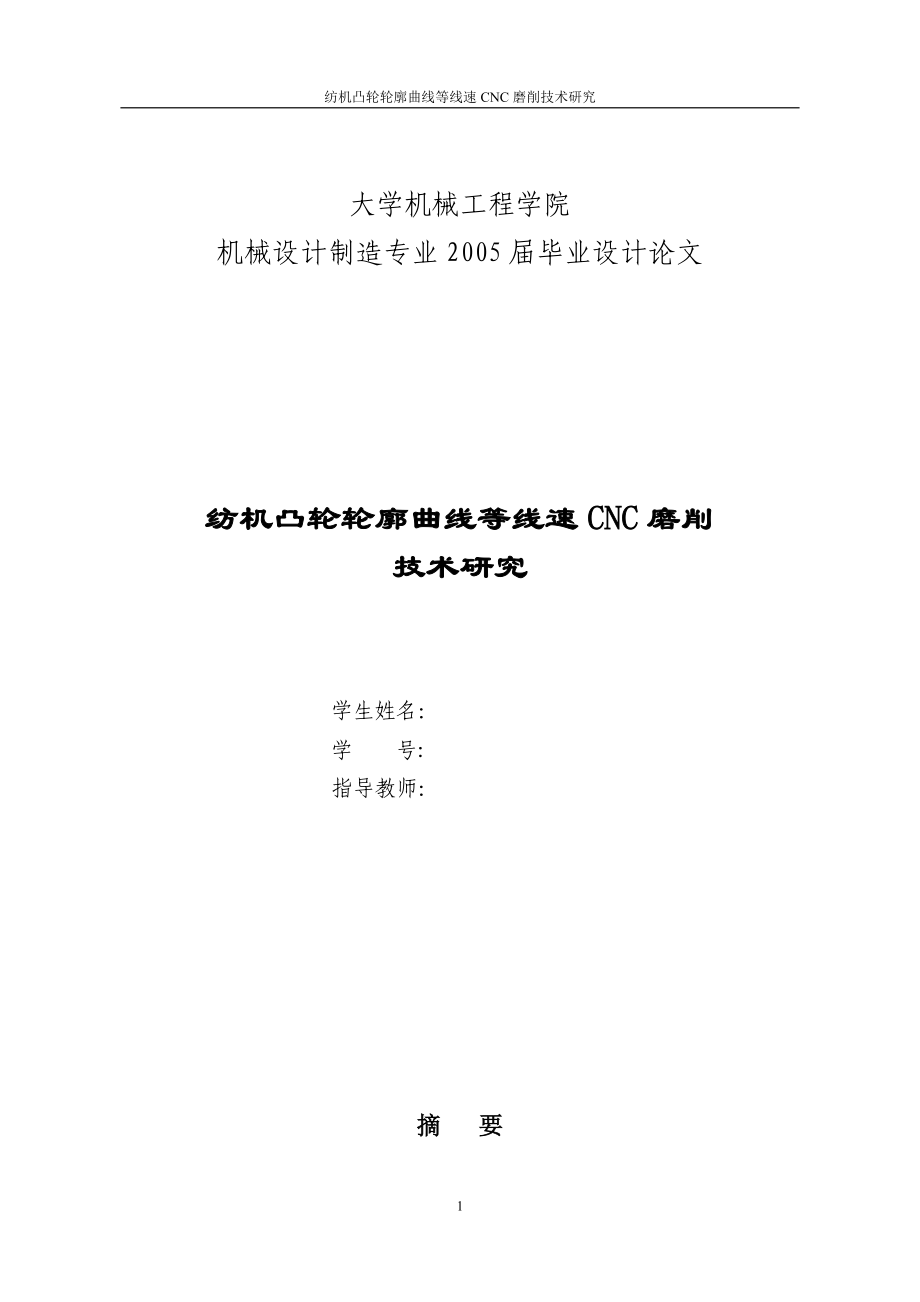


《紡機(jī)凸輪輪廓曲線等線速CNC磨削技術(shù)研究論文》由會員分享,可在線閱讀,更多相關(guān)《紡機(jī)凸輪輪廓曲線等線速CNC磨削技術(shù)研究論文(55頁珍藏版)》請?jiān)谘b配圖網(wǎng)上搜索。
1、紡機(jī)凸輪輪廓曲線等線速CNC磨削技術(shù)研究 大學(xué)機(jī)械工程學(xué)院 機(jī)械設(shè)計(jì)制造專業(yè)2005屆畢業(yè)設(shè)計(jì)論文 紡機(jī)凸輪輪廓曲線等線速CNC磨削 技術(shù)研究 學(xué)生姓名: 學(xué) 號: 指導(dǎo)教師: 摘 要 凸輪機(jī)構(gòu)是最常用的傳動(dòng)機(jī)構(gòu)之一,越來越廣泛地應(yīng)用于各種機(jī)械設(shè)備中。本課題所研究對象是某紡織機(jī)械開口機(jī)構(gòu)共扼凸輪副上下兩個(gè)凸輪,該凸輪是由非圓函數(shù)曲線組成,現(xiàn)有磨削加工工藝是在自行改造的三軸數(shù)控外圓磨床上,采用凸輪繞自身軸線等角速度磨削加工工藝,所磨削的凸輪表面存在著“棱邊”現(xiàn)象,有時(shí)
2、甚至伴隨磨削燒傷,磨削加工還需要增加一道拋光工序,表面質(zhì)量差,加工周期長。本文對凸輪等線速磨削進(jìn)行了研究,首先通過給定的導(dǎo)輪運(yùn)動(dòng)軌跡,求解了上凸輪的輪廓曲線,并根據(jù)開口機(jī)構(gòu)共扼原理求解了下凸輪的輪廓曲線;以等弦長磨削方法近似等線速磨削,通過給定的等弦長求解相應(yīng)的凸輪轉(zhuǎn)角,獲取凸輪曲線上一個(gè)個(gè)磨削分割點(diǎn);利用等距線原理,對凸輪曲線上的分割點(diǎn)求解砂輪中心運(yùn)動(dòng)軌跡;依據(jù)砂輪中心運(yùn)動(dòng)軌跡編寫凸輪磨削NC程序;在改造的數(shù)控外圓磨床上對共扼凸輪進(jìn)行等線速磨削試驗(yàn)。經(jīng)磨削試驗(yàn)結(jié)果說明,共扼凸輪等線速磨削單位金屬磨除率均勻,減小了磨削力的波動(dòng),消除了磨削“棱邊”現(xiàn)象,避免了磨削燒傷,取得較好的磨削避免質(zhì)量。通
3、過本課題的研究,不僅解決了紡機(jī)開口機(jī)構(gòu)共扼磨削工藝難題,還為凸輪數(shù)控磨床設(shè)計(jì)開發(fā)和傳統(tǒng)機(jī)床的改造提供了理論依據(jù)和經(jīng)驗(yàn)借鑒。 關(guān)鍵字:共扼凸輪;等線速磨削;CNC磨床 Abstract Content: The cam organization is one of the most frequently used transmission organizations, and it is more and more widely applied to various kinds of machinery. As the object of this researc
4、h , the cam 1 and cam 2 of the spinning machine cams are both have non- round curves as their components besides circle. Previously, the numerical control programs are automatically produced with Master CAM. However it is unfavourable that the grinded surfaces are unsatisfactory in quality. In this
5、subject, we change the angular speed when cams rotating for the sake of the permanent linear velocity. We approach the curves with a series of little straight lines , calculate the coordinates of the ends, and then those points on the on the track of the sharpener center, which have the equal distan
6、ce with the ends of those lines. We write the CNC programs and carry it on the cams. What we have to say is that the expressions of the curves ,the calculation of the coordinates and the generation of the programs are all achieved bu computer . It is practiced that the scheme is feasible, not only i
7、t has improved quality of processing, but also the whole course is uncomplicated. This scheme can be used when the curve’s expression is known and the curve is C1 continuous. The research to the equal linear velocity grinding about the the outline curve of the spinning machine cams has offered a key
8、 technological theory for the design of the modelling cam grinder and the reform to the existing grinder constantly. Key words: Spinning machine cam, outline curve, equal linear velocity, CNC grinding 紡機(jī)凸輪輪廓曲線等線速CNC磨削技術(shù)研究 目 錄 摘要 ………………………………………………………………………1
9、 Abstract………………………………………………………………… 2 第一章 緒論 ………………………………………………………………3 1.1 本課題研究的目的意義及其背景 ………………………………3 1.2 本課題研究的具體任務(wù)要求…………………………………… 3 1.3 本課題研究的思路和技術(shù)路線………………………………… 4
10、 第二章 紡機(jī)凸輪的運(yùn)動(dòng)分析及曲線求解 2.1 紡機(jī)凸輪的運(yùn)動(dòng)分析……………………………………………5 2.1.1 已知條件說明………………………………………………5 2.1.2 凸輪運(yùn)動(dòng)副分析……………………………………………5 2.2 凸輪曲線計(jì)算 ……………………………………………………6 2.2.1 凸輪1曲線方程計(jì)算………………………………………7 2.2.2 導(dǎo)輪4中心運(yùn)動(dòng)軌跡計(jì)算………………………………… 9 2.2.3 凸輪2曲線方程計(jì)算………………………………………10 第三章 凸輪等線速磨削分析計(jì)算 3.1等線速磨削原理 ………
11、……………………………………… 14 3.2 等線速磨削的相關(guān)計(jì)算……………………………………… 14 3.2.2 工件坐標(biāo)系的確立…………………………………………15 3.2.3 步長的確定…………………………………………………15 3.2.4 凸輪輪廓基點(diǎn)和節(jié)點(diǎn)坐標(biāo)的計(jì)算…………………………15 3.3凸輪磨削刀位點(diǎn)的計(jì)算 …………………………………………18 第四章 等線速磨削CNC程序的編制 4.1 數(shù)控系統(tǒng)簡介……………………………………………………22 4.2 凸輪磨削加工工藝分析…………………………………………23 4.2.1起始點(diǎn)的選擇………………………………
12、………………25 4.2.2工件裝夾 ……………………………………………………25 4.3 數(shù)控程序編制……………………………………………………23 4.3.1數(shù)控編程方法的選擇………………………………………23 4.3.2凸輪等線速CNC磨削中的參數(shù)設(shè)定 ………………………24 4.3.3凸輪等線速磨削CNC程序的自動(dòng)生成……………………25 第五章 凸輪等線速磨削試驗(yàn)與分析 5.1 凸輪磨削試驗(yàn)前的準(zhǔn)備…………………………………………29 5.1.1 砂輪修整 ………………………………………………… 29 5.1.2 數(shù)控程序的傳輸與校驗(yàn) ………………………………… 29
13、 5.1.3 初始位置調(diào)整 ………………………………………………30 5.2 磨削結(jié)果與分析…………………………………………………31 5.2.1 磨削試驗(yàn)過程 ………………………………………………31 5.2.2 磨削試驗(yàn)結(jié)果分析 …………………………………………31 第六章 總結(jié)與展望………………………………………………………33 致 謝……………………………………………………………………34 參考文獻(xiàn) …………………………………………………………………35 第一章 緒論 1.1 課題研究的目的意義及其背景 凸輪是一種常見的機(jī)械傳動(dòng)零件,凸輪輪廓的加工
14、一直是機(jī)械制造工藝中的難點(diǎn)之一。最原始的凸輪加工是通過劃線手銼法完成,這種低效率低精度的加工方法早已被淘汰。目前,廣泛采用數(shù)控加工技術(shù)來完成凸輪輪廓的加工,對表面輪廓精度要求高的凸輪,常常還需要通過磨削加工來完成?,F(xiàn)在生產(chǎn)企業(yè)所使用的凸輪磨床有兩大類:一類是機(jī)械靠模擺架式,這類凸輪磨床磨削砂輪不動(dòng),通過凸輪旋轉(zhuǎn)和靠模架的擺動(dòng)實(shí)現(xiàn)凸輪輪廓的磨削;另一類為數(shù)控凸輪磨床,它通過凸輪的旋轉(zhuǎn)和砂輪沿徑向的直線運(yùn)動(dòng)實(shí)現(xiàn)凸輪輪廓的磨削。數(shù)控凸輪磨床不需要凸輪靠模,對任意復(fù)雜的凸輪輪廓曲線,可通過數(shù)控程序的改變來實(shí)現(xiàn)不同凸輪的磨削,具有較大優(yōu)越性,既能保證凸輪表面磨削質(zhì)量,又方便于機(jī)床參數(shù)的調(diào)整。 目前,凸
15、輪的數(shù)控磨削常采用等角速度磨削工藝,即凸輪繞自身軸線作等角速度旋轉(zhuǎn),砂輪作跟隨的直線運(yùn)動(dòng)。由于凸輪輪廓表面各點(diǎn)曲率半徑不同,往往以較小的轉(zhuǎn)角變化產(chǎn)生較大的磨削線速度變化,引起單位時(shí)間內(nèi)金屬切除率不均勻,從而總存在著所磨削的凸輪表面“棱邊”現(xiàn)象,有時(shí)甚至還伴隨著磨削表面燒傷。 例如:揚(yáng)州大學(xué)機(jī)械電子實(shí)習(xí)工廠所磨削加工的某紡織機(jī)械開口機(jī)構(gòu)的一對共扼凸輪采用了等角速度磨削工藝,存在著較嚴(yán)重的“棱邊”現(xiàn)象,為此不得不在磨削工藝之后增加一道手工拋光工藝。 因而,近年來提出了凸輪等線速磨削工藝,國內(nèi)外也有不少關(guān)于凸輪等線速磨削工藝研究的報(bào)道[123]。所謂凸輪等線速磨削即通過控制凸輪在一周內(nèi)的轉(zhuǎn)速變化
16、,實(shí)現(xiàn)恒定凸輪表面磨削線速度,以此提高凸輪表面磨削精度。 本課題研究的對象就是針對揚(yáng)州大學(xué)機(jī)械電子實(shí)習(xí)工廠所加工紡機(jī)開口機(jī)構(gòu)共扼凸輪,進(jìn)行凸輪等線速磨削工藝研究,解決企業(yè)生產(chǎn)中的實(shí)際問題。利用本人四年來已學(xué)習(xí)掌握的專業(yè)知識,查閱學(xué)習(xí)現(xiàn)有的技術(shù)文獻(xiàn),分析一般凸輪磨削存在的現(xiàn)象和原因,提出自己關(guān)于凸輪等線磨削的解決辦法,以此提高自己的科學(xué)研究能力、動(dòng)手能力和分析解決實(shí)際問題的能力。 1.2 本課題研究的具體任務(wù)要求 以紡機(jī)開口共扼凸輪為研究對象,對所給凸輪曲線形狀進(jìn)行分析,針對凸輪磨削中存在的共性問題,擬定課題研究方案,進(jìn)行凸輪輪廓曲線和磨削運(yùn)動(dòng)軌跡的計(jì)算、編寫計(jì)算和NC磨削自動(dòng)生成程序,
17、進(jìn)行數(shù)控磨削試驗(yàn),驗(yàn)證磨削效果,獲取較為完全的等線速磨削工藝。具體任務(wù)如下: 1、學(xué)習(xí)與本課題有關(guān)的理論知識,學(xué)習(xí)計(jì)算機(jī)編程語言,學(xué)習(xí)西門子802D數(shù)控系統(tǒng)的操作方法和系統(tǒng)參數(shù)設(shè)置,為本課題研究順利進(jìn)行打好基礎(chǔ)。 2、分析開口機(jī)構(gòu)共扼凸輪輪廓形狀,根據(jù)已知的導(dǎo)輪運(yùn)動(dòng)軌跡,推導(dǎo)上、下凸輪的輪廓曲線方程,編寫計(jì)算分析計(jì)算機(jī)模塊軟件,自動(dòng)凸輪磨削NC數(shù)控程序。 3、進(jìn)行凸輪磨削試驗(yàn),對凸輪等線速磨削工藝方法磨削試驗(yàn)結(jié)果進(jìn)行分析,總結(jié)研究結(jié)果,提出進(jìn)一步研究展望。 1.3 本課題研究的思路和技術(shù)路線 本課題研究對象為紡機(jī)開口機(jī)構(gòu)的一對共扼凸輪。所采用的凸輪數(shù)控磨床為揚(yáng)州大學(xué)機(jī)電研究所改造的
18、數(shù)控外圓磨床,該磨床有三根伺服控制軸,分別工作臺縱向運(yùn)動(dòng)的Z軸,磨頭徑向運(yùn)動(dòng)的X軸,以及帶動(dòng)工件旋轉(zhuǎn)的C軸。 本課題研究的技術(shù)路線為:根據(jù)已知的上導(dǎo)輪中心運(yùn)動(dòng)軌跡,利用等距線求解上凸輪的輪廓曲線方程→利用共軛關(guān)系求解下導(dǎo)輪中心運(yùn)動(dòng)軌跡→根據(jù)下導(dǎo)輪中心軌跡,同樣利用等距線求解下凸輪輪廓曲線方程→根據(jù)加工精度要求確定離散點(diǎn)步長→分別計(jì)算上下兩凸輪的離散節(jié)點(diǎn);利用等距平行直線求解砂輪中心軌跡,即刀位點(diǎn)→自動(dòng)生成凸輪NC磨削程序→凸輪磨削試驗(yàn),分析結(jié)果。 第二章 紡機(jī)凸輪的運(yùn)動(dòng)分析及曲線求解 2.1 紡機(jī)凸輪的運(yùn)動(dòng)分析 2.1.1 已知條件 圖2-1為某紡機(jī)開口機(jī)構(gòu)的共額凸輪副
19、,上下兩凸輪同軸。凸輪1輪廓曲線圓弧部分半徑為R=90.5mm,長徑O2B1=109.5mm,升程角=降程角=73.405o,凸輪1始終與導(dǎo)輪3保持接觸。凸輪2始終與導(dǎo)輪4保持接觸。導(dǎo)輪3和4半徑均為r=44mm,固定臂O1O2=180mm,擺動(dòng)臂O1O3= O1O4=108mm,兩導(dǎo)輪臂夾角∠O3O1O4=106.26o,O1O5為輸出臂。 圖2-1開口機(jī)構(gòu)共額凸輪副運(yùn)動(dòng)分析 已知導(dǎo)輪3在凸輪1上升沿和下降沿的中心運(yùn)動(dòng)軌跡曲線方程為: (2-1) 2.1.2 共額凸輪副運(yùn)動(dòng)分析 下面由圖2-1所示的4個(gè)位置來分析共額凸輪副的運(yùn)動(dòng)
20、關(guān)系。 1)位置1:凸輪1開始進(jìn)入升程曲線部分,由于A1點(diǎn)為凸輪1輪廓曲線圓弧部分與升程曲線的連接點(diǎn),則切點(diǎn)A1位于O2O3連線上;同樣切點(diǎn)A2位于O2O4連線上。此時(shí)有: O2O3=90.5+44=134.5mm O2O4=109.5+44=153.5mm 計(jì)算可得: ∠A1O2A2=73.405o 2)位置2:將凸輪副逆時(shí)針旋轉(zhuǎn),凸輪1的接觸點(diǎn)從A1移動(dòng)到B1點(diǎn)。在凸輪副旋轉(zhuǎn)過程中導(dǎo)輪3與凸輪1的接觸點(diǎn)不在O2O3連線上,當(dāng)接觸點(diǎn)到達(dá)B1時(shí)正好落在O2O3上。旋轉(zhuǎn)過程中O2O3距離不斷增大,導(dǎo)致輸出臂O1O5連線繞O1逆時(shí)針旋轉(zhuǎn)。由于O2A1= O2B2,A1和B2也處于同一圓
21、上。此時(shí)有: O2O3=109.5+44=153.5mm O2O4=90.5+44=134.5mm 此時(shí)∠B1O2B2=73.405o,與位置1相同,但O1O5旋轉(zhuǎn)了一個(gè)角度。 3)位置3:同樣此時(shí)∠C1O2C2 =73.405o,而輸出臂O1O5方位與位置1相同。 4)位置4:凸輪副與導(dǎo)輪接觸于圓弧部分,擺動(dòng)臂O1O5靜止不動(dòng),直到旋轉(zhuǎn)到A1后重復(fù)上述運(yùn)動(dòng)過程。 由上述共額凸輪副運(yùn)動(dòng)分析可知: 1) 凸輪與導(dǎo)輪切點(diǎn)中心角∠B1O2B2在起始點(diǎn)和終點(diǎn)角度均為73.405o; 2) 在旋轉(zhuǎn)過程中,兩導(dǎo)輪與凸輪中心距不斷變化,但兩導(dǎo)輪臂夾角∠O3O1O4=106.26o保持不變;
22、 3) 不論哪個(gè)凸輪為主動(dòng),也不管旋轉(zhuǎn)方向如何,上下兩凸輪始終與導(dǎo)輪保持接觸。 2.2 凸輪曲線計(jì)算 根據(jù)已知的導(dǎo)輪3中心運(yùn)動(dòng)軌跡方程,通過凸輪副的運(yùn)動(dòng)規(guī)律和已知的機(jī)構(gòu)參數(shù),可求出凸輪1廓線曲線方程,并能精確地計(jì)算出凸輪廓線上各點(diǎn)的坐標(biāo)值。根據(jù)凸輪共軛關(guān)系,也可求解凸輪2的曲線方程。具體求解過程如下: ① 根據(jù)凸輪1中心與導(dǎo)輪3中心距離的變化,求解凸輪1輪廓曲線; ② 根據(jù)共額關(guān)系求取導(dǎo)輪4中心運(yùn)動(dòng)軌跡; ③ 由導(dǎo)論4中心運(yùn)動(dòng)軌跡求取凸輪2輪廓曲線。 其中第①③步是利用等距線關(guān)系進(jìn)行求解,第②步是凸輪副共額關(guān)系進(jìn)行計(jì)算。 2.2.1 凸輪1曲線方程計(jì)算 凸輪1輪廓曲線可以看成是
23、導(dǎo)輪3中心運(yùn)動(dòng)軌跡的等距線,而且是以凸輪長軸為對稱軸的對稱圖形?,F(xiàn)只需求解凸輪1下降沿輪廓曲線,上升沿曲線可通過對稱圖形獲得。 圖2-2 凸輪1輪廓曲線的求解 如圖2-2所示,假定凸輪1靜止,導(dǎo)輪3繞凸輪1中心O2從桃尖部分開始滾動(dòng)了角度θ,則在平面坐標(biāo)系下有: x=ρ1cosθ (2-3) y=ρ1sinθ 故
24、 (2-4) 由于切點(diǎn)A并不總在O2O3上,因此O2A與O2O3相差一角度α,也就是 = (2-5) 其中 (2-6) (2-
25、7) 需要注意的是由于dl相對于ρ1來說是一個(gè)微小的量,因此也是一個(gè)微小量,這樣,就可以近似地認(rèn)為每一個(gè)微小的非圓曲線段都是圓弧,再用弦長近似代替弧長,這樣的計(jì)算方法比較簡單,在dl相對于ρ1足夠小的情況下,誤差也很小。 根據(jù)內(nèi)等距線公式 (2-8) 其中,導(dǎo)輪半徑=44,凸輪1上下降曲線的極坐標(biāo)式為 (2-9) 最終表達(dá)式中含有變量θ,計(jì)算比較復(fù)雜,可以用計(jì)算機(jī)編程求解。 2.2
26、.2 導(dǎo)輪4中心運(yùn)動(dòng)軌跡計(jì)算 由于凸輪1與凸輪2是一對共額凸輪,其共額關(guān)系如圖2-3所示,A為凸輪機(jī)構(gòu)的固定點(diǎn),B為凸輪1和凸輪2的中心點(diǎn),C點(diǎn)和D點(diǎn)分別為凸輪3和導(dǎo)輪4的中心。已知∠CAD=106.26o,|AC|=|AD|=108mm,|AB|=180mm,可求解|BD|距離,即確定了導(dǎo)輪4的中心運(yùn)動(dòng)D點(diǎn)的軌跡。具體求解步驟如下: 圖2-3 中心距離相對關(guān)系 1)從⊿ACB可求解:γ1,γ2 (2-10) (2-11) 2)從⊿ADB,求解γ4, BD
27、 (2-12) = (2-13) 55 由 可以得到 (2-14) 這樣,導(dǎo)輪4對應(yīng)點(diǎn)的中心距為 |BD|(也就是上文所提到的ρ2),其相位角度與導(dǎo)輪3相差 (+),其數(shù)值為73.405o,這樣就可以求出導(dǎo)輪4中心的運(yùn)動(dòng)軌跡,再利用等距線方法可以計(jì)算出凸輪2的曲線。 2.2.3 凸輪2曲線方程計(jì)算 求解導(dǎo)輪4中心運(yùn)動(dòng)軌跡的等距線,便可得到凸輪2輪廓曲線,如圖2-4所示。計(jì)算方法與凸輪1曲線類似。 圖2-4 凸輪2輪廓曲線 1)
28、 BC段曲線求解 圖2-5 凸輪2的轉(zhuǎn)角落后于凸輪1角度,如圖2-5,有 則有 (2-15) (2-16) 令 (2-17) 對m求導(dǎo)得: (2-18) 令
29、 (2-19) 對k求導(dǎo)得: (2-20) 由式(2-13)知: (2-21) 則對ρ2求導(dǎo)得: (2-22) 由(2-1)得: 又令 (2-23) (2-24) 令 (2-25) 則對n求導(dǎo)得
30、: (2-26) 對式(2-15)兩邊求θ的導(dǎo)數(shù)得: (2-27) 又 (2-28)將(2-22)、(2-27)、(2-28)代入下式: (2-29)則 (2-30) 將以上各式按需代入 ,即可
31、求得凸輪2的曲線方程的平面坐標(biāo)下的表達(dá)式,代入式(2-9)就能得到凸輪2的實(shí)際輪廓的BC段的極坐標(biāo)方程。 2) AB段曲線求解 圖2-6 如圖2-6所示,有 則 (2-31) 兩邊求θ的導(dǎo)數(shù)得: (2-32) 由式(2-22)、(2-27)、(2-32)代入(2-29),再將所需表達(dá)式代入(2-30),即可求得凸輪2的曲線方程的平面坐標(biāo)下的表達(dá)式,代入式(2-9)就能得到凸輪2的實(shí)際輪廓的AB段的極坐標(biāo)方程。
32、 第三章 凸輪等線速磨削分析計(jì)算 3.1 等線速磨削原理 對于凸輪輪廓曲線的磨削,由于凸輪輪廓表面各點(diǎn)的線速度不一定相同,若采用等角速度磨削工藝,其單位時(shí)間內(nèi)金屬磨除率不同,引起磨削力的波動(dòng)較大,往往會造成凸輪磨削表面的“棱邊”現(xiàn)象,甚至?xí)霈F(xiàn)表面燒傷,嚴(yán)重影響凸輪表面加工質(zhì)量。 本文采用等線速凸輪磨削工藝,即根據(jù)凸輪輪廓曲線各點(diǎn)曲率的不同,采用不同的角速度,以保證凸輪磨削表面的線速度不變,使單位時(shí)間內(nèi)金屬磨除率相等。對于凸輪輪廓曲線而言,可用等弦長的小直線段來分割凸輪輪廓曲線,這樣通過改變各分割點(diǎn)對應(yīng)的角速度來可保證各磨削點(diǎn)的線速度不發(fā)生變化,從而達(dá)到等線速磨削
33、的目的。 3.2 等線速磨削的相關(guān)計(jì)算 3.2.1 工件坐標(biāo)系的確立 由于凸輪1與凸輪2同心并固連在一起,因此在數(shù)值計(jì)算時(shí)以兩凸輪的中心為工件坐標(biāo)系的原點(diǎn),以凸輪1的長徑為x軸,建立平面坐標(biāo)系(圖2-2),下面的數(shù)值計(jì)算就是以該坐標(biāo)系進(jìn)行計(jì)算的。 3.2.2 弦長的確定 凸輪的輪廓曲線是由不同的幾何元素(圓弧、非圓曲線)組成,各幾何元素間的交點(diǎn)稱為基點(diǎn)。當(dāng)利用具有直線插補(bǔ)功能的數(shù)控機(jī)床加工零件的曲線輪廓時(shí),任一輪廓的曲線均用連續(xù)的小直線段來逼近,其相鄰兩小直線段的交點(diǎn)稱為節(jié)點(diǎn)。 凸輪的等線速磨削需要將凸輪的輪廓曲線分割成的等弦長的直線段,其弦長的大小應(yīng)根據(jù)加工精度以及NC編程所允許
34、的誤差來確定。 如圖3-1所示,設(shè)A、B為被分割直線段的兩節(jié)點(diǎn),砂輪半徑為R,弦長為dl,若凸輪輪廓表面磨削粗糙度要求為0.8μm,所允許的微觀不平度為1.6μm,則由圖示可知: dl=AB==2 (3-1) 若取砂輪半徑為R=300mm時(shí),則: dl=1.960 mm 考慮到其它因素的影響,分別?。? 凸輪1:dl1=0.5mm 凸輪2:dl2=0.25mm 當(dāng)然,其弦長數(shù)值可實(shí)際磨削中進(jìn)行調(diào)整。 圖3-1 弦長的確定 3.2.4 凸輪輪廓基點(diǎn)和節(jié)點(diǎn)坐標(biāo)的計(jì)算 凸輪輪廓的基點(diǎn)是凸輪輪廓曲線上不同幾何
35、元素的交點(diǎn),比較容易求取,可根據(jù)共扼凸輪副的已知條件直接求取。而凸輪輪廓節(jié)點(diǎn),即一條條小直線段的分割點(diǎn),其求解卻比較困難。由于凸輪輪廓曲線是一個(gè)超越方程,很難通過解析法求得節(jié)點(diǎn)的精確解,只能用數(shù)值解法求得近似解。二分法是求解超越方程的最常用方法,下面將具體介紹應(yīng)用二分法求解凸輪輪廓曲線節(jié)點(diǎn)的方法和過程。 1、二分法定義 設(shè)函數(shù)y=f(x)在區(qū)間[a,b]上連續(xù),且有f(a)·f(b)<0,將函數(shù)f(x)=0所在的區(qū)間一分為二,再進(jìn)行計(jì)算比較,保留其中接近零點(diǎn)的小區(qū)間,如此迭代,減小區(qū)間范圍,直至區(qū)間端點(diǎn)函數(shù)值小于給定誤差,從而求得函數(shù)零點(diǎn)近似值。 2、二分法求解步驟 設(shè)定求解精確度為ε
36、,二分法求解函數(shù)零點(diǎn)(x0)步驟如下: ①確定初始區(qū)間[a,b],并驗(yàn)證f(a)f(b)<0; ②求區(qū)間[a,b]中點(diǎn)x1; (3-2) ③計(jì)算f(x1),判斷: a)如果f(x1)=0,則x1就是f(x)的零點(diǎn),計(jì)算終止; b)如果f(a)f(x1)<0,則令b= x1 (此時(shí)零點(diǎn)x0∈[a,x1]中); c)如果f(a)f(x1)>0,則令a= x1 (此時(shí)零點(diǎn)x0∈[x1 ,b]中) ④判斷是否滿足ε要求,若|a-b|<ε,則得到零點(diǎn)近似值是[a,b]區(qū) 間內(nèi)任一點(diǎn);否則重復(fù)2
37、~4步驟。 3、 計(jì)算流程圖 二分法求解的計(jì)算機(jī)求解流程圖如圖3-2所示。 圖3-2 二分法求解流程圖 說明:此處的a=0,b=db只是象征了每一個(gè)小區(qū)間的兩個(gè)端點(diǎn),也就是說在dl所分成的若干個(gè)區(qū)間內(nèi),在每一個(gè)區(qū)間試圖找到一個(gè)等距點(diǎn)(人為地使區(qū)間足夠小以保證區(qū)間內(nèi)最多只有一個(gè)符合要求的點(diǎn)),輸出等距點(diǎn)。然后改變a、b的值,在新的區(qū)間內(nèi)求取新的等距點(diǎn),循環(huán)往復(fù),直到將整個(gè)曲線處理完畢。 4、偽語句描述 5、C++程序?qū)崿F(xiàn) float f(float th,float th0) { float fun,dth; dth=th-th0; fun=rr(th)*
38、dth-dl; return fun; } int Bisection(float a,float b,float s0,float *th) { float fa,fb,fc,c; *th=0; fa=f(a,s0); fb=f(b,s0); if(fa*fb>0) return 0; while(fabs(a-b)>EPS) { c=(a+b)/2; fc=f(c,s0); if(fc*fa>0) { a=c; fa=f(a,s0); } else { b=c; fb=f(b,s0); } } *th=(a
39、+b)/2; return 1; } 6、凸輪輪廓曲線基點(diǎn)和節(jié)點(diǎn)坐標(biāo)的計(jì)算 如圖2-2所示的坐標(biāo)系下,凸輪1各基點(diǎn)的坐標(biāo)按順時(shí)針依次為:(109.5,0),B(90.5,-)、C (90.5,);凸輪2各基點(diǎn)的坐標(biāo)按順時(shí)針依次為:(109.5,(π+))、(90.5,0)、(109.5,(π-))。 凸輪輪廓曲線節(jié)點(diǎn)坐標(biāo)的計(jì)算,是應(yīng)用上述二分法,通過計(jì)算機(jī)編程求解獲得,其程序段參見附錄。 3.3 凸輪磨削刀位點(diǎn)的計(jì)算 由于本研究是在自行改造的三軸數(shù)控外圓磨床上進(jìn)行,對凸輪輪廓曲線的磨削實(shí)際上僅需C軸和X軸的聯(lián)動(dòng),即凸輪的回轉(zhuǎn)和砂輪的徑向進(jìn)給運(yùn)動(dòng)聯(lián)動(dòng)。各節(jié)點(diǎn)C軸轉(zhuǎn)角坐標(biāo)可根據(jù)給定
40、的弦長和磨削點(diǎn)的矢徑很容易求出,而砂輪的徑向進(jìn)給X軸坐標(biāo)較難計(jì)算。由于凸輪輪廓曲線各點(diǎn)的曲率不同,砂輪的磨削點(diǎn)往往不在凸輪中心和砂輪中心的連線上,從而造成求解的困難。 1. 砂輪中心運(yùn)動(dòng)軌跡的計(jì)算 由于砂輪的磨削點(diǎn)往往不在凸輪中心和砂輪中心的連線上,因而砂輪中心運(yùn)動(dòng)軌跡的計(jì)算可等距線方法求解。如圖3-3所示,A(x1,y1)、B(x2,y2)、C(x3,y3)是凸輪廓型曲線上等弦長的三個(gè)連續(xù)分布點(diǎn),分別作直線L1、L2相距為砂輪半徑d=R的等距線L1′、L2′,這兩等距線的交點(diǎn)就是與凸輪輪廓曲線節(jié)點(diǎn)B相對應(yīng)的砂輪中心軌跡點(diǎn)B′(xp2,yp2)。依次可求出砂輪中心軌跡點(diǎn)(xp3,yp3)、
41、(xp4,yp4)、……、(xpn,yn)。 L1′ B′ d A L1 B L2′ L2 d 圖3-3 對于凸輪1,可以先求出下降曲線上各節(jié)點(diǎn)的砂輪中心運(yùn)動(dòng)軌跡,再根據(jù)對稱原理求出上升曲線的砂輪中心運(yùn)動(dòng)軌跡。對于凸輪2由于上升曲線與下降曲線的表達(dá)式不同,需要分開求解。 已知凸輪輪廓曲線相鄰三各節(jié)點(diǎn)求砂輪中心軌跡刀位點(diǎn)的C語言程序如下: int offsetInt (float x1,float y1,float x2,float y2,float x3,float y3, int nFlag,float d,float *x,float *y
42、)
{
float A1,B1,C1,A2,B2,C2;
Callinepara(x1,y1,x2,y2,nFlag,d,&A1,&B1,&C1);
Callinepara(x2,y2,x3,y3,nFlag,d,&A2,&B2,&C2);
if(fabs(A1*B2-A2*B1) 43、e
{
*x=(C2*B1-C1*B2)/(A1*B2-A2*B1);
*y=(C2*A1-C1*A2)/(A2*B1-A1*B2);
}
return 1;
}
void Callinepara(float x1,float y1,float x2,float y2,int nFlag,
float rad,float *A1,float *B1,float *C1)
{
float A,B,C,k,b,db;
A=y1-y2;
B=x2-x1;
C=x1*y2-x2*y1;
if(fabs(B) 44、 *A1=A;*B1=B;
rad=R;
db=rad*A;
if(y2>y1) db*=-1;
if(nFlag==1) *C1=C+db;
else *C1=C-db;
}
else
{
k=(y2-y1)/(x2-x1);
b=y1-k*x1;
db=sqrt(k*k+1)*rad;
if(x1 45、
凸輪的數(shù)控磨削實(shí)際上是凸輪繞自身軸心旋轉(zhuǎn)(C軸),砂輪軸心沿水平方向移動(dòng)(X軸)。在此X-C極坐標(biāo)系統(tǒng)下,增量坐標(biāo)NC插補(bǔ)程序所要計(jì)算的量是(ΔX,ΔC),其中,ΔCi=θi+1-θi。
將上節(jié)所計(jì)算的砂輪中心運(yùn)動(dòng)軌跡,通過計(jì)算機(jī)程序進(jìn)行轉(zhuǎn)換,轉(zhuǎn)換為一系列(ΔXi,ΔCi)極坐標(biāo)形式,便于后續(xù)的NC程序后置處理。
所注意的是:上述極坐標(biāo)系統(tǒng)中的角度是用弧度表示的,在寫入砂輪中心運(yùn)動(dòng)軌跡文件時(shí)需將輸出的Δ轉(zhuǎn)化成弧度。
第四章 等線速磨削CNC程序自動(dòng)生成
4.1 數(shù)控系統(tǒng)簡介
數(shù)控技術(shù)(Numerical Cont 46、rol)是利用數(shù)字化信息對機(jī)床運(yùn)動(dòng)及加工過程進(jìn)行控制的一種方法。用數(shù)控技術(shù)實(shí)施加工控制的機(jī)床,或者說裝備了數(shù)控系統(tǒng)的機(jī)床稱為數(shù)控(NC)機(jī)床。本研究所用的數(shù)控凸輪磨床是由萬能外圓磨床改造而成的。
一般CNC機(jī)床主要由機(jī)床本體和數(shù)控系統(tǒng)兩大部分組成。數(shù)控系統(tǒng)又包括數(shù)控裝置、可編程序控制器、主軸驅(qū)動(dòng)及進(jìn)給驅(qū)動(dòng)等組成部分。各數(shù)控系統(tǒng)所采用的數(shù)控代碼雖然是標(biāo)準(zhǔn)代碼,但都帶有自身一些特殊的內(nèi)置代碼。
按數(shù)控系統(tǒng)控制功能分類,數(shù)控系統(tǒng)可分為點(diǎn)位(point-to-point)控制和連續(xù)(continuous-path)控制兩大類。點(diǎn)位控制的數(shù)控系統(tǒng)只能進(jìn)行準(zhǔn)確的坐標(biāo)點(diǎn)的控制,限于鉆孔、鉸孔、鏜孔等以及 47、與機(jī)床坐標(biāo)軸平行或成45度的直線銑削加工,不能加工圓弧等輪廓曲線。連續(xù)控制也成為輪廓(contouring)控制,可以完成圓弧及任意角度斜線的加工。由于電控部分易于實(shí)現(xiàn),點(diǎn)位控制機(jī)床曾經(jīng)流行一時(shí),隨著技術(shù)的進(jìn)步,連續(xù)控制系統(tǒng)已成為流行的控制系統(tǒng)。
數(shù)控系統(tǒng)的主要功能包括數(shù)控軸基本控制、程序暫停、平面選擇、坐標(biāo)設(shè)定、刀具補(bǔ)償、基準(zhǔn)點(diǎn)返回、固定循環(huán)、公英制轉(zhuǎn)換等準(zhǔn)備功能(G代碼),刀具功能(T代碼),主軸速度功能(S代碼),進(jìn)給速度功能(F代碼)和一系列輔助功能(M代碼)。
數(shù)控系統(tǒng)是數(shù)控機(jī)床的核心,根據(jù)數(shù)控機(jī)床的功能要求,可配置不同的數(shù)控系統(tǒng)。典型的數(shù)控系統(tǒng)有FANUC(日本)、SIEMEN 48、S(德國)、FAGOR(西班牙)、HEIDENHAIN(德國)、MITSUBISHI(日本)等公司的數(shù)控系統(tǒng)及其相關(guān)產(chǎn)品,在數(shù)控機(jī)床行業(yè)占據(jù)主導(dǎo)地位。我國數(shù)控產(chǎn)品以華中數(shù)控、航天數(shù)控為代表,也已將高性能數(shù)控系統(tǒng)產(chǎn)業(yè)化。
本次凸輪磨削試驗(yàn)所用的數(shù)控系統(tǒng)是西門子公司的SINUMERIK 802D系統(tǒng),它能控制4個(gè)數(shù)字進(jìn)給軸和1個(gè)主軸,內(nèi)置PLC,具有圖形式編程,有較好的工作界面。
4.2 數(shù)控加工工藝分析
4.2.1 共額凸輪輪廓曲線磨削起始點(diǎn)的選擇
為了保證磨削加工的安全,避免因計(jì)算錯(cuò)誤或其他故障導(dǎo)致砂輪與磨削工件碰撞引起事故的發(fā)生,取凸輪最大外處作為磨削的起始點(diǎn)。對于所磨削紡機(jī)共額凸輪 49、副,選擇凸輪1上A點(diǎn)(圖3-1)作磨削起始點(diǎn),選擇凸輪2圓弧段的中點(diǎn)作為磨削起始點(diǎn)。這樣,凸輪1磨削的順序依次為下降沿曲線AB→圓弧段BC→上升曲線CA,凸輪2磨削順序依次為圓弧段DE→上升曲線EF→下降曲線FG→圓弧段GD,周而復(fù)始直至凸輪磨削達(dá)到尺寸要求為止。由于共額凸輪副的兩凸輪為同心凸輪,因而兩只凸輪可一次裝夾磨削完成,僅是起始磨削相位點(diǎn)不同。
4.2.2 共額凸輪的裝夾方法
共額凸輪副一次裝夾,可完成兩個(gè)凸輪的磨削加工,可避免兩次裝夾引起的裝夾誤差。共額凸輪副裝夾時(shí),是用一個(gè)定位銷將凸輪副在主軸上定位。當(dāng)一個(gè)凸輪磨削完成后,將砂輪沿Z軸移動(dòng)一個(gè)適當(dāng)?shù)木嚯x就可以磨削第二個(gè)凸輪。
50、4.3 數(shù)控程序編制
4.3.1數(shù)控編程方法分析
數(shù)控加工編程可以手工編程,也通過計(jì)算機(jī)實(shí)現(xiàn)自動(dòng)編程。
⑴手工編程
手工編程的一般步驟為:首先分析所加工的零件圖樣,確定數(shù)控加工工藝過程,計(jì)算所需的加工輪廓基點(diǎn)和節(jié)點(diǎn),然后應(yīng)用數(shù)控代碼編寫零件加工程序清單,最后將NC程序制備成控制介質(zhì),提供給數(shù)控機(jī)床加工。手工編程從圖紙閱讀到數(shù)控程序的校驗(yàn)都是由人工完成,這對于形狀簡單、計(jì)算量小、程序不多的零件,采用手工編程比較容易實(shí)現(xiàn)。但對于形狀復(fù)雜的零件,特別是具有非圓直線、列表曲線以及復(fù)雜曲面組成的零件,用手工編程就無能為力了,必須借助于計(jì)算機(jī)根據(jù)實(shí)現(xiàn)NC程序的自動(dòng)編程。
⑵計(jì)算機(jī)自動(dòng)編程
計(jì)算 51、機(jī)自動(dòng)編程是利用計(jì)算機(jī)專用軟件模塊實(shí)現(xiàn)數(shù)控加工程序自動(dòng)編制的過程。在計(jì)算機(jī)自動(dòng)編程中,編程人員只需根據(jù)零件圖樣的要求,使用數(shù)控語言,由計(jì)算機(jī)自動(dòng)地進(jìn)行數(shù)值計(jì)算和后置處理,編寫出零件加工程序單,加工程序通過直接通訊的方式送入數(shù)控機(jī)床,控制機(jī)床進(jìn)行自動(dòng)作業(yè)。計(jì)算機(jī)自動(dòng)編程使計(jì)算繁瑣、手工編程無法實(shí)現(xiàn)的工作能夠自動(dòng)順利完成。
在本課題中,已經(jīng)根據(jù)磨削加工精度要求求解了砂輪中心運(yùn)動(dòng)軌跡各個(gè)刀位控制點(diǎn),因而僅需用C語言編寫一個(gè)后置處理模塊,按照數(shù)控系統(tǒng)的指令要求將砂輪中心運(yùn)動(dòng)軌跡各個(gè)刀位控制點(diǎn)轉(zhuǎn)換成實(shí)際NC程序文件即可。
4.3.2 凸輪等線速磨削的數(shù)控系統(tǒng)參數(shù)設(shè)定
凸輪數(shù)控磨削NC程序要涉及 52、許多相關(guān)參數(shù),如磨削量、磨削速度值,應(yīng)認(rèn)真加以選擇,以便保證磨削精度和磨削效率。
①工件參數(shù) 包括凸輪1-8位置參數(shù)和角度參數(shù)、凸輪基圓半徑、凸輪測量方法。
②砂輪參數(shù) 指砂輪直徑、砂輪寬度。
③整砂輪參數(shù) 金剛筆進(jìn)給位置、速度、修磨量、修磨次數(shù)等。
④磨削參數(shù) 砂輪進(jìn)給位置、速度、粗磨量、半精磨量、精磨量、C軸轉(zhuǎn)速、凸輪補(bǔ)償量等。這些參數(shù)有些是固定的,有些是根據(jù)磨削效果進(jìn)行調(diào)整的。根據(jù)實(shí)際磨削試驗(yàn)對這些參數(shù)進(jìn)行選擇和調(diào)整。
數(shù)控系統(tǒng)參數(shù)的定義:
R1:磨削循環(huán)數(shù) R26=d:磨削余量
R18=d1:砂輪直徑 53、 R20=L:X原點(diǎn)位置
R14=fz:每轉(zhuǎn)進(jìn)給量 R24=c:磨削起始相位
X0=109.5:X軸極限坐標(biāo) z=-709.438:Z軸極限坐標(biāo)
R26=R7:當(dāng)前加工余量
4.3.3 凸輪等線速磨削NC程序自動(dòng)生成
在本課題中,為了自動(dòng)生成凸輪數(shù)控磨削程序,我們用C++語言編寫了一個(gè)后置處理程序,按照數(shù)控系統(tǒng)的指令要求將砂輪中心運(yùn)動(dòng)軌跡文件,轉(zhuǎn)換成滿足本凸輪數(shù)控磨削要求的NC程序文件。
設(shè)定總磨削余量和每次循環(huán)磨削量后,計(jì)算循環(huán)次數(shù),計(jì)算確定每次循環(huán)中X軸坐標(biāo)零點(diǎn),在一次循環(huán)中其它各點(diǎn)都是相對應(yīng)于該零點(diǎn)進(jìn)行控制的 54、。
所轉(zhuǎn)換的NC程序如下所示:
%_N_TL1NEW_MPF
;R1:磨削圈數(shù)
;R26=d;加工余量
;R18=d1;砂輪直徑
;R20=L;X原點(diǎn)位置
;X=109.5;凸輪最大半徑
;R14=fz;每轉(zhuǎn)進(jìn)給量
;R24=c;磨削起始相位
;z=-709.438;Z方向進(jìn)給位置
G94 G64
R26=R7;當(dāng)前加工余量
R1=0;圈數(shù)
STOPRE
M8;開冷卻
M10;開砂輪
R26=R26-R14
G90G01X0F1000;機(jī)床定位
Z=-709.438C=R24
CUTSTART:;開始磨削
R37=109.5+R26+R18/2-R2 55、0+ ;計(jì)算X當(dāng)前進(jìn)給位置
TRANS X=R37C=R1*36.000+R24+3.319;設(shè)置偏值
G90G01C0F300
X0
X-0.016C0.123F500;曲線
***********
***********
***********
X0C36.000
TRANS ;取消偏值
IF(R26==0) GOTOF CUTEND
R26=R26-R14
R1=R1+1 ;圈數(shù)計(jì)數(shù)
IF(R26<0)
R26=0
GOTOB CUTSTART
ENDIF
IF(R26>0) GOTOB CUTSTART ;繼續(xù)加工條件
CUTEND:
56、G90G01X0 ;退回安全位置
M9 ;關(guān)冷卻
M11 ;關(guān)砂輪
M02
第五章 凸輪等線速磨削試驗(yàn)與分析
5.1 凸輪磨削試驗(yàn)前的準(zhǔn)備
5.1.1 砂輪修整
砂輪修整就是對砂輪表面進(jìn)行整理已達(dá)到期望的磨削功能。砂輪修整的目的是使銳利的新磨粒暴露于砂輪表面。為了更好觀察凸輪等線速方法的磨削效果,盡量減小其它因素對試驗(yàn)結(jié)果的影響,在磨削前最好先對砂輪進(jìn)行修整,以免因砂輪的鈍化影響凸輪磨削表面粗糙度,而不能正確反映試驗(yàn)結(jié)果。砂輪修整工具和修整方法的不同,均會影響磨削性能,因而磨削試驗(yàn)所采用的砂輪修整方法必須與實(shí)際生產(chǎn)時(shí)砂輪修整 57、方法相一致。
本試驗(yàn)所使用的機(jī)床是經(jīng)普通外圓磨床改造的數(shù)控凸輪磨床,有三根數(shù)控伺服控制軸。砂輪修整采用金剛筆修整方法,金剛筆安裝在尾座上。砂輪修整時(shí),砂輪作旋轉(zhuǎn)運(yùn)動(dòng),金剛筆依靠伺服電機(jī)驅(qū)動(dòng)工作臺作縱向往復(fù)運(yùn)動(dòng),以及伺服電機(jī)驅(qū)動(dòng)磨頭作砂輪的徑向進(jìn)給運(yùn)動(dòng),按照事先所設(shè)定的修整量自動(dòng)完成砂輪的修整,并且數(shù)控系統(tǒng)能夠記憶修整后的砂輪的直徑。
5.1.2 數(shù)控程序的傳輸與校驗(yàn)
按規(guī)定的程序代碼和格式要求所自動(dòng)生成的磨削加工數(shù)控程序,可通過DNC通信方法由RS232C接口傳送給機(jī)床數(shù)控系統(tǒng)。
當(dāng)凸輪磨削數(shù)控程序傳送到數(shù)控系統(tǒng)之后,須進(jìn)行數(shù)控程序的語法和詞法校驗(yàn),檢查是否符合所要求的語法規(guī)則,檢查出 58、錯(cuò)后及時(shí)對NC程序進(jìn)行修改,沒有問題后,再經(jīng)試切才能正式進(jìn)行磨削加工。試切的方法是:不安裝零件,運(yùn)行所要執(zhí)行的數(shù)控程序,讓機(jī)床空運(yùn)轉(zhuǎn),以檢查機(jī)床的運(yùn)動(dòng)軌跡是否正確。并通過數(shù)控系統(tǒng)CRT所顯示的運(yùn)動(dòng)軌跡,檢驗(yàn)砂輪與工件磨削過程。但這種試磨方法只能檢驗(yàn)?zāi)ハ鬟\(yùn)動(dòng)是否正確,不能檢驗(yàn)被加工零件的加工精度。因此,還需要對零件進(jìn)行首件試磨。當(dāng)發(fā)現(xiàn)磨削對象有加工誤差時(shí),分析誤差產(chǎn)生的原因,找出問題所在,再加以修正。
本課題對凸輪磨削數(shù)控程序的檢查是分兩步進(jìn)行:
首先,檢驗(yàn)砂輪刀位點(diǎn)計(jì)算的正確性,這是通過AutoCAD作圖法進(jìn)行檢驗(yàn)的。利用AutoCAD繪制凸輪曲線的等距線,并繪制所生成的砂輪中心運(yùn)動(dòng)軌跡, 59、比較這兩條曲線的一致性,檢測兩者之間的誤差。
然后,在機(jī)床上通過運(yùn)動(dòng)磨削數(shù)控程序進(jìn)行檢驗(yàn)。運(yùn)行已傳輸?shù)臄?shù)控程序,為安全起見,砂輪并不運(yùn)轉(zhuǎn),使之靠近凸輪,讓凸輪旋轉(zhuǎn),通過視覺檢查凸輪與砂輪的運(yùn)動(dòng)關(guān)系是否符合要求。
5.1.3 初始位置調(diào)整
機(jī)床主軸有一個(gè)相位零點(diǎn),凸輪磨削時(shí)必須使機(jī)床主軸的相位零點(diǎn)與凸輪的磨削起始點(diǎn)相一致,這便涉及凸輪磨削初始相位調(diào)整問題。
1、凸輪相位調(diào)整
為了使凸輪在磨削加工過程中受力平衡,保證凸輪輪廓的對稱性,在凸輪實(shí)際磨削之前必須調(diào)整相位,使砂輪在凸輪時(shí)從前面提及的起始點(diǎn)開始磨削。這是一個(gè)細(xì)心的工作,必須認(rèn)真調(diào)整,盡可能使凸輪毛坯對稱軸兩邊余量磨削均勻,避免出現(xiàn) 60、一邊磨不到,另一邊卻過量磨削,造成磨削燒傷現(xiàn)象。
在調(diào)整相位時(shí),可使砂輪不轉(zhuǎn)動(dòng),并逐漸接近凸輪最大半徑處,使凸輪(C軸)以很慢的轉(zhuǎn)速旋轉(zhuǎn),以視覺判斷凸輪對稱軸兩邊余量均衡,完成凸輪相位的調(diào)整。
2. 砂輪X軸位置的調(diào)整
由于砂輪直徑的變化,在第一件凸輪磨削時(shí),需要進(jìn)行砂輪X軸位置的調(diào)整,以減少空運(yùn)轉(zhuǎn)行程,提高磨削效率。砂輪X軸調(diào)整時(shí),可使凸輪緩慢轉(zhuǎn)動(dòng),砂輪啟動(dòng),使砂輪緩慢向凸輪靠近,可用塞尺或其它檢驗(yàn)工具檢驗(yàn)砂輪與凸輪之間的間隙,以此X軸坐標(biāo)位置計(jì)算砂輪的直徑,并將之保存在數(shù)控系統(tǒng)內(nèi),作為后面凸輪磨削的基本參數(shù)。
3. 砂輪Z向位置調(diào)整
砂輪Z向位置調(diào)整比較容易,僅需保 61、證砂輪外圓表面覆蓋凸輪寬度即可。為提高砂輪使用壽命,可在砂輪寬度方向進(jìn)行一定的串動(dòng)量。
5.2 磨削試驗(yàn)結(jié)果與分析
5.2.1 磨削試驗(yàn)過程
一旦凸輪磨削數(shù)控程序校驗(yàn)正確,并將機(jī)床數(shù)控系統(tǒng)參數(shù)設(shè)定以及機(jī)床相關(guān)調(diào)整完成后,便可進(jìn)行凸輪首件試磨。
1. 凸輪磨削操作順序
調(diào)用凸輪1的磨削NC程序→調(diào)整機(jī)床參數(shù)R37→磨削凸輪1→調(diào)用凸輪2的磨削NC程序→重新調(diào)整機(jī)床參數(shù)R37→磨削凸輪2→磨削過程結(jié)束。
2. 注意事項(xiàng)
磨削時(shí)要先打開冷卻液,以避免磨削工件磨削燒傷。磨削完成后,待砂輪退回原位后再去拆卸工件,以免被回轉(zhuǎn)砂輪擦傷。
5.2.2 磨削試驗(yàn)結(jié)果分析
1. 形狀尺寸
62、應(yīng)用等線速磨削的凸輪副,通過專用的檢測機(jī)構(gòu)進(jìn)行檢測得知,上下兩凸輪再旋轉(zhuǎn)過程中,其導(dǎo)輪3始終與凸輪1緊密嚙合,導(dǎo)輪4始終與凸輪2緊密嚙合,這就說明被磨削的凸輪副的尺寸形狀符合運(yùn)動(dòng)關(guān)系要求。用游標(biāo)卡尺測量凸輪1和凸輪2的長徑和短徑,其尺寸在所要求的公差范圍內(nèi)。
2. 表面質(zhì)量
磨削表面質(zhì)量包括表面粗糙度、表面燒傷、棱邊現(xiàn)象等。
對于機(jī)械零件加工,由于刀具進(jìn)給量、機(jī)械振動(dòng)等原因,總會在零件的加工表面留下凸凹不平的細(xì)微刀痕,出現(xiàn)交錯(cuò)起伏的峰谷現(xiàn)象,這就是表面粗糙度。表面粗糙度對零件使用性能和使用壽命有很大影響。一般說來,表面粗糙度值越小,表面配合精度越高,摩擦力減小,會延長使用壽命,但加工難 63、度和費(fèi)用也會增加。因此,應(yīng)根據(jù)零件實(shí)際應(yīng)用要求合理地選用表面粗糙度。
對用等線速磨削的凸輪副與常規(guī)等角速度磨削的凸輪副進(jìn)行比較,用視覺和觸覺直接觀察方法可以發(fā)現(xiàn),等線速磨削方法的凸輪副表面光潔度明顯比等角速度磨削方法的凸輪表面光潔度要好,沒有表面燒傷,完全消除了“棱邊”現(xiàn)象。這樣,可省除等角速度磨削后的拋光工序,大大節(jié)省了成本,縮短了生產(chǎn)周期。
所謂的“棱邊”現(xiàn)象,是在磨削加工后,凸輪表面曲線與圓弧的過渡處存在一條小棱,嚴(yán)重影響凸輪的表面加工質(zhì)量。在本課題中,運(yùn)用一系列微小的等弦長直線段來擬合曲線與圓弧,將曲線與圓弧的過渡轉(zhuǎn)化成無數(shù)微小直線段的首尾相接,達(dá)到了恒線速磨削的目的。實(shí)踐證明,運(yùn) 64、用此方法能夠有效地避免了“棱邊”現(xiàn)象,達(dá)到所要求的凸輪加工表面質(zhì)量。
3. 無磨削燒傷
等線速NC磨削在每個(gè)直線段上采用了相等的磨削速度,單位時(shí)間內(nèi)金屬磨除率相等,不會產(chǎn)生局部的磨削熱,因此不會出現(xiàn)磨削燒傷現(xiàn)象。
4. 加工效率與成本
等線速磨削工藝所磨削凸輪輪廓表面粗糙度小,表面質(zhì)量高,省去了原有的手工拋光工序,提高了加工效率,縮短了生產(chǎn)周期,降低了生產(chǎn)成本。
第六章 總結(jié)與展望
本次畢業(yè)設(shè)計(jì)針對紡機(jī)凸輪磨削過程中所存在的生產(chǎn)實(shí)際問題,進(jìn)行了等線速凸輪磨削方法的研究,完成了凸輪曲線的求解、磨削砂輪軌跡的計(jì) 65、算、數(shù)控程序的生成、實(shí)際磨削試驗(yàn)等研究工作,實(shí)現(xiàn)了對紡機(jī)凸輪等線速CNC磨削工藝方法,在保證尺寸和形狀精度的同時(shí),消除了常見的棱邊和燒傷現(xiàn)象,獲得了較好的表面質(zhì)量。
通過這次畢業(yè)設(shè)計(jì),我們學(xué)習(xí)掌握了VC++編程語言、二分法數(shù)值計(jì)算、等距線計(jì)算、CNC磨床的參數(shù)設(shè)置和機(jī)床調(diào)整等工程應(yīng)用中所需的理論和實(shí)踐知識,大大提高了自己分析和解決工程實(shí)際問題的能力,得到了一次很好的工程實(shí)際訓(xùn)練,受益匪淺。
遺憾的是,由于畢業(yè)設(shè)計(jì)的時(shí)間有限,尚未來得及對磨削凸輪粗糙度做比較分析,因而關(guān)于磨削結(jié)果的分析還不夠有說服力。若能有機(jī)會的話,可進(jìn)一步細(xì)化所做的工作,將凸輪等線速CNC磨削的機(jī)理、數(shù)控磨床的結(jié)構(gòu)、機(jī)床精 66、度對磨削質(zhì)量的影響做進(jìn)一步的研究,為凸輪恒線速磨床的改造和設(shè)計(jì)提供理論依據(jù)。
致 謝
兩個(gè)多月的畢業(yè)設(shè)計(jì)中,教授對我們進(jìn)行了悉心的指導(dǎo),不管工作多忙,基本上每天都抽空到設(shè)計(jì)地點(diǎn)為我們解決疑難問題,對畢業(yè)設(shè)計(jì)遇到的難題進(jìn)行點(diǎn)撥,保證了畢業(yè)設(shè)計(jì)順利進(jìn)行。老師的敬業(yè)精神和敏捷的思維,給我們留下了深刻的印象,樹立了良好的榜樣,對我們今后的學(xué)習(xí)和工作都是一種鞭策和啟示。機(jī)電研究所的李吉中老師為我們指正了畢業(yè)設(shè)計(jì)中編程和計(jì)算方面的錯(cuò)誤,為課題的順利解決提供了較大的幫助,在此一并表示衷心的感謝。此外,還要感謝同組的趙建飛同學(xué)在設(shè)計(jì)中的積極配合。
參考文獻(xiàn)
[ 1] 金建新 來傳遠(yuǎn),平面凸輪曲線的等線速度數(shù)控磨削方法研究,中國機(jī)械工程,2002年,第13卷第10期:838~841
[ 2] 王政帥 唐浙東,凸輪磨削動(dòng)態(tài)特性對磨削質(zhì)量影響的探討,內(nèi)燃機(jī),2004年,第2期:10~13
[ 3] 賈振元 傅南紅,凸輪軸變轉(zhuǎn)速數(shù)控磨削方法的數(shù)學(xué)解析,大連理工大學(xué)學(xué)
- 溫馨提示:
1: 本站所有資源如無特殊說明,都需要本地電腦安裝OFFICE2007和PDF閱讀器。圖紙軟件為CAD,CAXA,PROE,UG,SolidWorks等.壓縮文件請下載最新的WinRAR軟件解壓。
2: 本站的文檔不包含任何第三方提供的附件圖紙等,如果需要附件,請聯(lián)系上傳者。文件的所有權(quán)益歸上傳用戶所有。
3.本站RAR壓縮包中若帶圖紙,網(wǎng)頁內(nèi)容里面會有圖紙預(yù)覽,若沒有圖紙預(yù)覽就沒有圖紙。
4. 未經(jīng)權(quán)益所有人同意不得將文件中的內(nèi)容挪作商業(yè)或盈利用途。
5. 裝配圖網(wǎng)僅提供信息存儲空間,僅對用戶上傳內(nèi)容的表現(xiàn)方式做保護(hù)處理,對用戶上傳分享的文檔內(nèi)容本身不做任何修改或編輯,并不能對任何下載內(nèi)容負(fù)責(zé)。
6. 下載文件中如有侵權(quán)或不適當(dāng)內(nèi)容,請與我們聯(lián)系,我們立即糾正。
7. 本站不保證下載資源的準(zhǔn)確性、安全性和完整性, 同時(shí)也不承擔(dān)用戶因使用這些下載資源對自己和他人造成任何形式的傷害或損失。
最新文檔
- 市教育局冬季運(yùn)動(dòng)會安全工作預(yù)案
- 2024年秋季《思想道德與法治》大作業(yè)及答案3套試卷
- 2024年教師年度考核表個(gè)人工作總結(jié)(可編輯)
- 2024年xx村兩委涉案資金退還保證書
- 2024年憲法宣傳周活動(dòng)總結(jié)+在機(jī)關(guān)“弘揚(yáng)憲法精神推動(dòng)發(fā)改工作高質(zhì)量發(fā)展”專題宣講報(bào)告會上的講話
- 2024年XX村合作社年報(bào)總結(jié)
- 2024-2025年秋季第一學(xué)期初中歷史上冊教研組工作總結(jié)
- 2024年小學(xué)高級教師年終工作總結(jié)匯報(bào)
- 2024-2025年秋季第一學(xué)期初中物理上冊教研組工作總結(jié)
- 2024年xx鎮(zhèn)交通年度總結(jié)
- 2024-2025年秋季第一學(xué)期小學(xué)語文教師工作總結(jié)
- 2024年XX村陳規(guī)陋習(xí)整治報(bào)告
- 2025年學(xué)校元旦迎新盛典活動(dòng)策劃方案
- 2024年學(xué)校周邊安全隱患自查報(bào)告
- 2024年XX鎮(zhèn)農(nóng)村規(guī)劃管控述職報(bào)告